Содержание
- 2. Дәріс жоспары: 1.Шихта материалы. 2.Тотықсыздандыру кезеңіндегі дәстүрлі технология.
- 3. Шихта материалы Электр балқытудағы негізгі шихта материалы – болат сынықтары (75–100 %). Болат сынығында түсті металдар
- 4. Шойынға қойылатын негізгі талап-фосфордың ең аз мөлшері; шағын ( Негізгі пештерде қож түзуші ретінде әк, әктас,
- 5. Балқыту келесі кезеңдерден тұрады: 1) пешті толықтыру; 2) шихтаны тиеу; 3) балқыту; 4)тотықтыру кезеңі; 5)тотықсыздандыру кезеңі;
- 6. Толықтыру-балқыманы шығарғаннан кейін, пештің толтырылуының зақымдалған жерлеріне немесе оның бүкіл бетіне магнезит ұнтағы (кейде пек немесе
- 7. Балқыту. Завалкадан кейін электродты жіберіп шихтаға тоқты қосамыз. Толтыру аяқталғаннан кейін электродтар шихтаға тигенге дейін түсіріледі
- 8. Тотықтыру кезеңі. Балқытудың тотығу кезеңінің міндеттері: а) металдағы фосфор құрамын 0,01—0,015% - ға дейін азайту; б)
- 9. Кеннің жалпы шығыны металл массасының 3-6, 5% құрайды. Металдың қатты салқындауына жол бермеу үшін кеннің бір
- 10. СО көпіршіктерімен бірге қайнаған кезде сутегі мен азот металдан алынады. Бұл процесс электростальдың сапасын жақсарту үшін
- 11. Қалпына келтіру кезеңі. Кезеңнің міндеттері: а)металды қышқылсыздандыру; б)күкіртті жою; в) болаттың химиялық құрамын белгіленген деңгейге дейін
- 12. Бүкіл кезең ішінде жүретін диффузиялық қышқылсызданудың мәні келесідей. Қышқылсыздандырғыш заттарды ұнтақ түрінде қолданғандықтан олардың тығыздығы төмен
- 13. Тотықсыздандыру кезеңінің соңында, қож бен металл қышқылсызданған кезде, металды оттегіге айтарлықтай химиялық жақындығы бар элементтермен легирлеу
- 15. Скачать презентацию
Слайд 3Шихта материалы
Электр балқытудағы негізгі шихта материалы – болат сынықтары (75–100 %). Болат
Шихта материалы
Электр балқытудағы негізгі шихта материалы – болат сынықтары (75–100 %). Болат
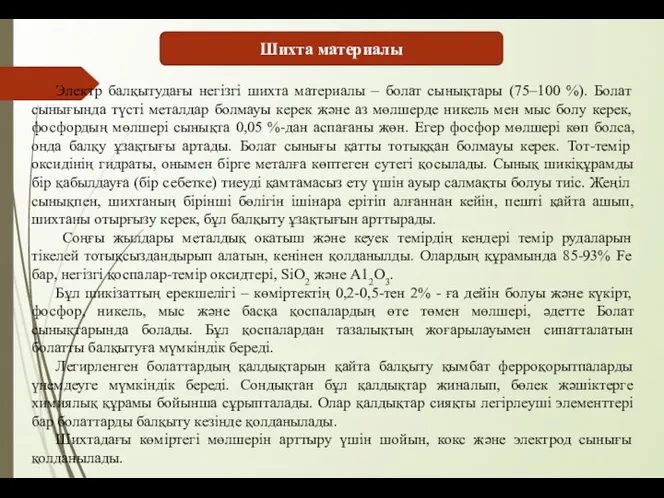
Соңғы жылдары металдық окатыш және кеуек темірдің кендері темір рудаларын тікелей тотықсыздандырып алатын, кенінен қолданылды. Олардың құрамында 85-93% Fe бар, негізгі қоспалар-темір оксидтері, SiО2 және А12О3.
Бұл шикізаттың ерекшелігі – көміртектің 0,2-0,5-тен 2% - ға дейін болуы және күкірт, фосфор, никель, мыс және басқа қоспалардың өте төмен мөлшері, әдетте Болат сынықтарында болады. Бұл қоспалардан тазалықтың жоғарылауымен сипатталатын болатты балқытуға мүмкіндік береді.
Легирленген болаттардың қалдықтарын қайта балқыту қымбат ферроқорытпаларды үнемдеуге мүмкіндік береді. Сондықтан бұл қалдықтар жиналып, бөлек жәшіктерге химиялық құрамы бойынша сұрыпталады. Олар қалдықтар сияқты легірлеуші элементтері бар болаттарды балқыту кезінде қолданылады.
Шихтадағы көміртегі мөлшерін арттыру үшін шойын, кокс және электрод сынығы қолданылады.
Слайд 4Шойынға қойылатын негізгі талап-фосфордың ең аз мөлшері; шағын (< 40 т) пештердің
Шойынға қойылатын негізгі талап-фосфордың ең аз мөлшері; шағын (< 40 т) пештердің
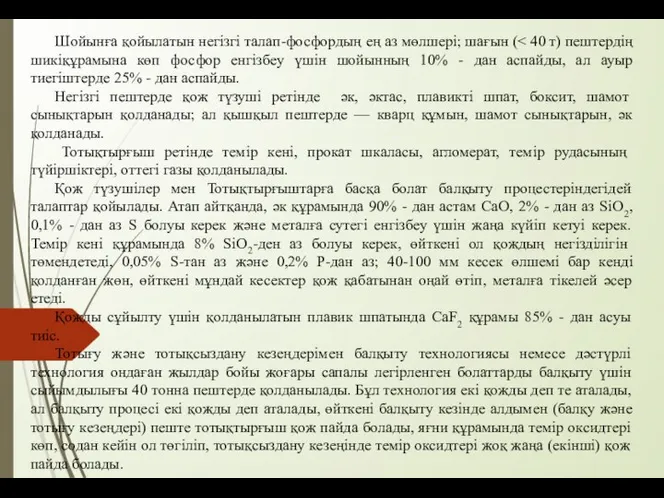
Негізгі пештерде қож түзуші ретінде әк, әктас, плавикті шпат, боксит, шамот сынықтарын қолданады; ал қышқыл пештерде — кварц құмын, шамот сынықтарын, әк қолданады.
Тотықтырғыш ретінде темір кені, прокат шкаласы, агломерат, темір рудасының түйіршіктері, оттегі газы қолданылады.
Қож түзушілер мен Тотықтырғыштарға басқа болат балқыту процестеріндегідей талаптар қойылады. Атап айтқанда, әк құрамында 90% - дан астам СаО, 2% - дан аз SiO2, 0,1% - дан аз S болуы керек және металға сутегі енгізбеу үшін жаңа күйіп кетуі керек. Темір кені құрамында 8% ЅіО2-ден аз болуы керек, өйткені ол қождың негізділігін төмендетеді, 0,05% S-тан аз және 0,2% Р-дан аз; 40-100 мм кесек өлшемі бар кенді қолданған жөн, өйткені мұндай кесектер қож қабатынан оңай өтіп, металға тікелей әсер етеді.
Қожды сұйылту үшін қолданылатын плавик шпатында CaF2 құрамы 85% - дан асуы тиіс.
Тотығу және тотықсыздану кезеңдерімен балқыту технологиясы немесе дәстүрлі технология ондаған жылдар бойы жоғары сапалы легірленген болаттарды балқыту үшін сыйымдылығы 40 тонна пештерде қолданылады. Бұл технология екі қожды деп те аталады, ал балқыту процесі екі қожды деп аталады, өйткені балқыту кезінде алдымен (балқу және тотығу кезеңдері) пеште тотықтырғыш қож пайда болады, яғни құрамында темір оксидтері көп, содан кейін ол төгіліп, тотықсыздану кезеңінде темір оксидтері жоқ жаңа (екінші) қож пайда болады.
Слайд 5Балқыту келесі кезеңдерден тұрады: 1) пешті толықтыру; 2) шихтаны тиеу; 3) балқыту;
Балқыту келесі кезеңдерден тұрады: 1) пешті толықтыру; 2) шихтаны тиеу; 3) балқыту;
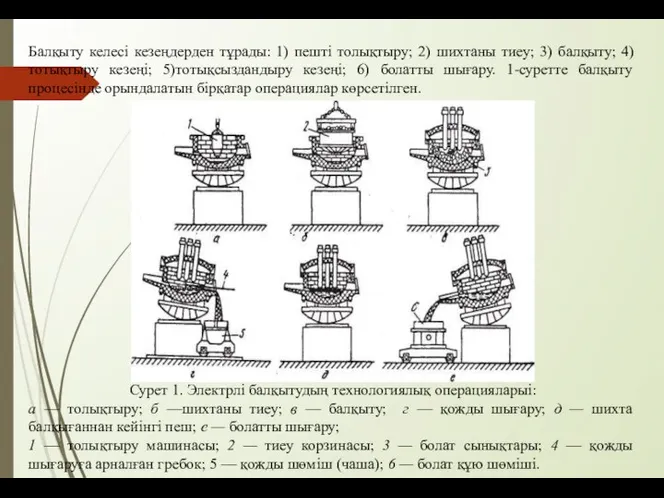
Сурет 1. Электрлі балқытудың технологиялық операцияларыі:
а — толықтыру; б —шихтаны тиеу; в — балқыту; г — қожды шығару; д — шихта балқығаннан кейінгі пеш; е — болатты шығару;
1 — толықтыру машинасы; 2 — тиеу корзинасы; 3 — болат сынықтары; 4 — қожды шығаруға арналған гребок; 5 — қожды шөміш (чаша); 6 — болат құю шөміші.
Слайд 6Толықтыру-балқыманы шығарғаннан кейін, пештің толтырылуының зақымдалған жерлеріне немесе оның бүкіл бетіне магнезит
Толықтыру-балқыманы шығарғаннан кейін, пештің толтырылуының зақымдалған жерлеріне немесе оның бүкіл бетіне магнезит
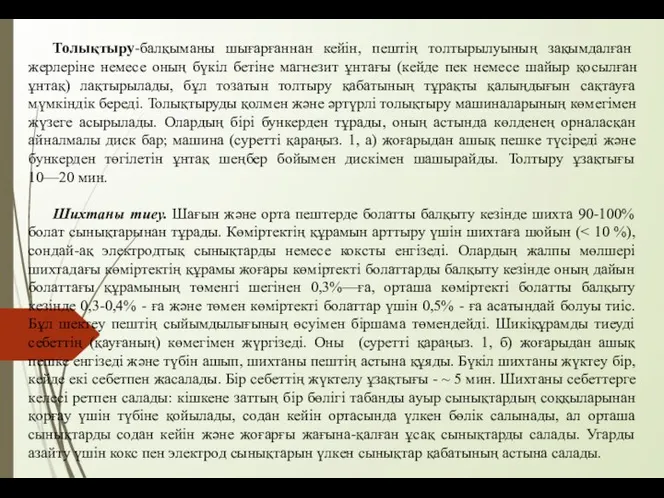
Шихтаны тиеу. Шағын және орта пештерде болатты балқыту кезінде шихта 90-100% болат сынықтарынан тұрады. Көміртектің құрамын арттыру үшін шихтаға шойын (< 10 %), сондай-ақ электродтық сынықтарды немесе коксты енгізеді. Олардың жалпы мөлшері шихтадағы көміртектің құрамы жоғары көміртекті болаттарды балқыту кезінде оның дайын болаттағы құрамының төменгі шегінен 0,3%—ға, орташа көміртекті болатты балқыту кезінде 0,3-0,4% - ға және төмен көміртекті болаттар үшін 0,5% - ға асатындай болуы тиіс. Бұл шектеу пештің сыйымдылығының өсуімен біршама төмендейді. Шикіқұрамды тиеуді себеттің (қауғаның) көмегімен жүргізеді. Оны (суретті қараңыз. 1, б) жоғарыдан ашық пешке енгізеді және түбін ашып, шихтаны пештің астына құяды. Бүкіл шихтаны жүктеу бір, кейде екі себетпен жасалады. Бір себеттің жүктелу ұзақтығы - ~ 5 мин. Шихтаны себеттерге келесі ретпен салады: кішкене заттың бір бөлігі табанды ауыр сынықтардың соққыларынан қорғау үшін түбіне қойылады, содан кейін ортасында үлкен бөлік салынады, ал орташа сынықтарды содан кейін және жоғарғы жағына-қалған ұсақ сынықтарды салады. Угарды азайту үшін кокс пен электрод сынықтарын үлкен сынықтар қабатының астына салады.
Слайд 7Балқыту. Завалкадан кейін электродты жіберіп шихтаға тоқты қосамыз.
Толтыру аяқталғаннан кейін электродтар
Балқыту. Завалкадан кейін электродты жіберіп шихтаға тоқты қосамыз.
Толтыру аяқталғаннан кейін электродтар
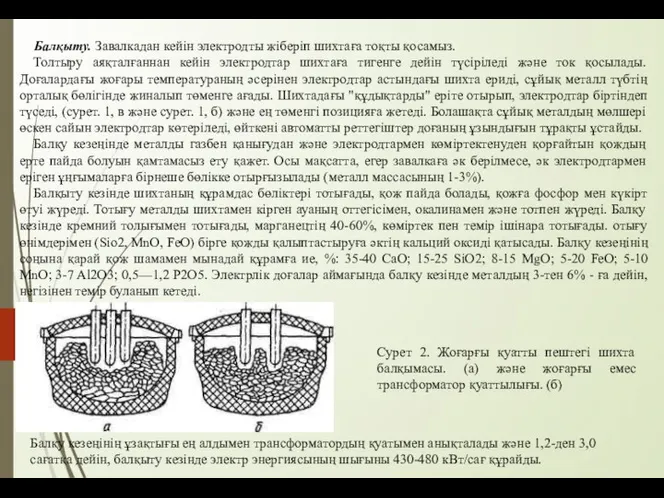
Балқу кезеңінде металды газбен қанығудан және электродтармен көміртектенуден қорғайтын қождың ерте пайда болуын қамтамасыз ету қажет. Осы мақсатта, егер завалкаға әк берілмесе, әк электродтармен еріген ұңғымаларға бірнеше бөлікке отырғызылады (металл массасының 1-3%).
Балқыту кезінде шихтаның құрамдас бөліктері тотығады, қож пайда болады, қожға фосфор мен күкірт өтуі жүреді. Тотығу металды шихтамен кірген ауаның оттегісімен, окалинамен және тотпен жүреді. Балқу кезінде кремний толығымен тотығады, марганецтің 40-60%, көміртек пен темір ішінара тотығады. отығу өнімдерімен (Sio2, MnO, FeO) бірге қожды қалыптастыруға әктің кальций оксиді қатысады. Балқу кезеңінің соңына қарай қож шамамен мынадай құрамға ие, %: 35-40 СаО; 15-25 ЅіО2; 8-15 MgO; 5-20 FeO; 5-10 MnO; 3-7 Al2О3; 0,5—1,2 P2O5. Электрлік доғалар аймағында балқу кезінде металдың 3-тен 6% - ға дейін, негізінен темір буланып кетеді.
Сурет 2. Жоғарғы қуатты пештегі шихта балқымасы. (а) және жоғарғы емес трансформатор қуаттылығы. (б)
Балқу кезеңінің ұзақтығы ең алдымен трансформатордың қуатымен анықталады және 1,2-ден 3,0 сағатқа дейін, балқыту кезінде электр энергиясының шығыны 430-480 кВт/сағ құрайды.
Слайд 8Тотықтыру кезеңі. Балқытудың тотығу кезеңінің міндеттері: а) металдағы фосфор құрамын 0,01—0,015% -
Тотықтыру кезеңі. Балқытудың тотығу кезеңінің міндеттері: а) металдағы фосфор құрамын 0,01—0,015% -
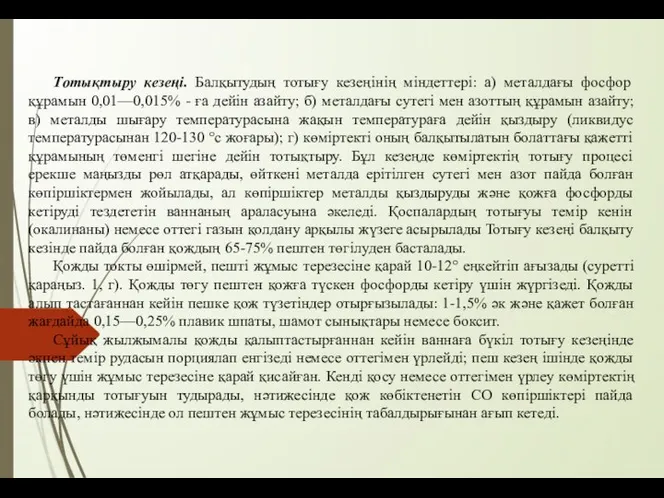
Қожды токты өшірмей, пешті жұмыс терезесіне қарай 10-12° еңкейтіп ағызады (суретті қараңыз. 1, г). Қожды төгу пештен қожға түскен фосфорды кетіру үшін жүргізеді. Қожды алып тастағаннан кейін пешке қож түзетіндер отырғызылады: 1-1,5% әк және қажет болған жағдайда 0,15—0,25% плавик шпаты, шамот сынықтары немесе боксит.
Сұйық жылжымалы қожды қалыптастырғаннан кейін ваннаға бүкіл тотығу кезеңінде әкпен темір рудасын порциялап енгізеді немесе оттегімен үрлейді; пеш кезең ішінде қожды төгу үшін жұмыс терезесіне қарай қисайған. Кенді қосу немесе оттегімен үрлеу көміртектің қарқынды тотығуын тудырады, нәтижесінде қож көбіктенетін СО көпіршіктері пайда болады, нәтижесінде ол пештен жұмыс терезесінің табалдырығынан ағып кетеді.
Слайд 9Кеннің жалпы шығыны металл массасының 3-6, 5% құрайды. Металдың қатты салқындауына жол
Кеннің жалпы шығыны металл массасының 3-6, 5% құрайды. Металдың қатты салқындауына жол
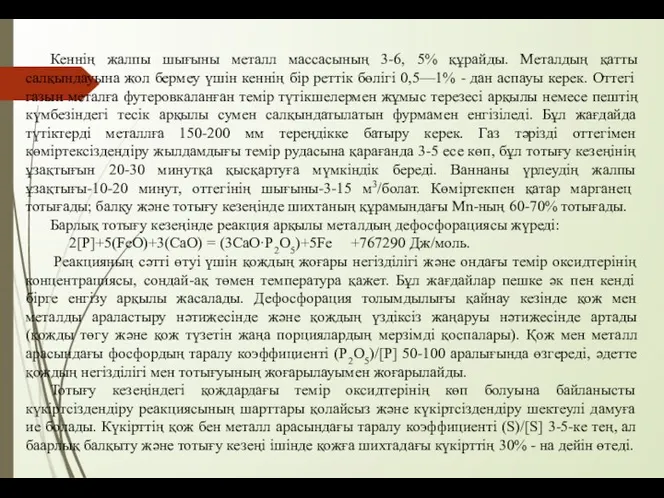
Барлық тотығу кезеңінде реакция арқылы металдың дефосфорациясы жүреді:
2[P]+5(FeO)+3(CaO) = (3СаО·P2O5)+5Fe +767290 Дж/моль.
Реакцияның сәтті өтуі үшін қождың жоғары негізділігі және ондағы темір оксидтерінің концентрациясы, сондай-ақ төмен температура қажет. Бұл жағдайлар пешке әк пен кенді бірге енгізу арқылы жасалады. Дефосфорация толымдылығы қайнау кезінде қож мен металды араластыру нәтижесінде және қождың үздіксіз жаңаруы нәтижесінде артады (қожды төгу және қож түзетін жаңа порциялардың мерзімді қоспалары). Қож мен металл арасындағы фосфордың таралу коэффициенті (P2O5)/[P] 50-100 аралығында өзгереді, әдетте қождың негізділігі мен тотығуының жоғарылауымен жоғарылайды.
Тотығу кезеңіндегі қождардағы темір оксидтерінің көп болуына байланысты күкіртсіздендіру реакциясының шарттары қолайсыз және күкіртсіздендіру шектеулі дамуға ие болады. Күкірттің қож бен металл арасындағы таралу коэффициенті (S)/[S] 3-5-ке тең, ал баарлық балқыту және тотығу кезеңі ішінде қожға шихтадағы күкірттің 30% - на дейін өтеді.
Слайд 10СО көпіршіктерімен бірге қайнаған кезде сутегі мен азот металдан алынады. Бұл процесс
СО көпіршіктерімен бірге қайнаған кезде сутегі мен азот металдан алынады. Бұл процесс
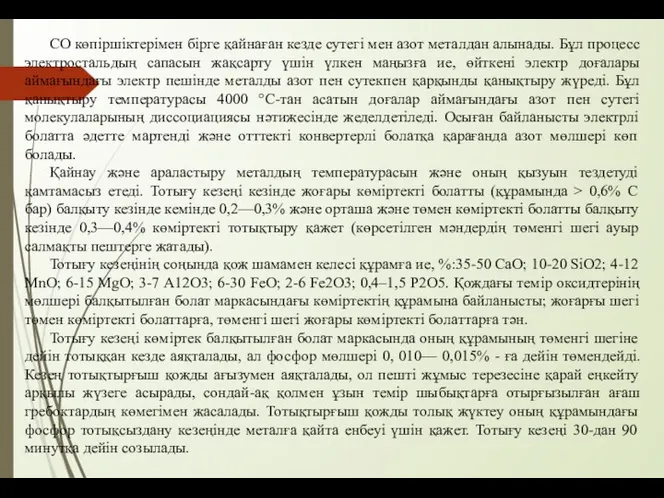
Қайнау және араластыру металдың температурасын және оның қызуын тездетуді қамтамасыз етеді. Тотығу кезеңі кезінде жоғары көміртекті болатты (құрамында > 0,6% С бар) балқыту кезінде кемінде 0,2—0,3% және орташа және төмен көміртекті болатты балқыту кезінде 0,3—0,4% көміртекті тотықтыру қажет (көрсетілген мәндердің төменгі шегі ауыр салмақты пештерге жатады).
Тотығу кезеңінің соңында қож шамамен келесі құрамға ие, %:35-50 СаО; 10-20 ЅіО2; 4-12 MnO; 6-15 MgO; 3-7 А12О3; 6-30 FeO; 2-6 Fe2О3; 0,4–1,5 Р2О5. Қождағы темір оксидтерінің мөлшері балқытылған болат маркасындағы көміртектің құрамына байланысты; жоғарғы шегі төмен көміртекті болаттарға, төменгі шегі жоғары көміртекті болаттарға тән.
Тотығу кезеңі көміртек балқытылған болат маркасында оның құрамының төменгі шегіне дейін тотыққан кезде аяқталады, ал фосфор мөлшері 0, 010— 0,015% - ға дейін төмендейді. Кезең тотықтырғыш қожды ағызумен аяқталады, ол пешті жұмыс терезесіне қарай еңкейту арқылы жүзеге асырады, сондай-ақ қолмен ұзын темір шыбықтарға отырғызылған ағаш гребоктардың көмегімен жасалады. Тотықтырғыш қожды толық жүктеу оның құрамындағы фосфор тотықсыздану кезеңінде металға қайта енбеуі үшін қажет. Тотығу кезеңі 30-дан 90 минутқа дейін созылады.
Слайд 11Қалпына келтіру кезеңі. Кезеңнің міндеттері:
а)металды қышқылсыздандыру; б)күкіртті жою; в) болаттың химиялық
Қалпына келтіру кезеңі. Кезеңнің міндеттері:
а)металды қышқылсыздандыру; б)күкіртті жою; в) болаттың химиялық
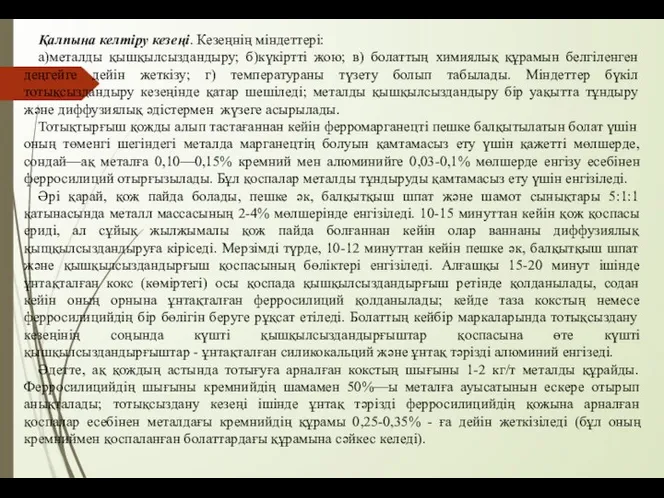
Тотықтырғыш қожды алып тастағаннан кейін ферромарганецті пешке балқытылатын болат үшін оның төменгі шегіндегі металда марганецтің болуын қамтамасыз ету үшін қажетті мөлшерде, сондай—ақ металға 0,10—0,15% кремний мен алюминийге 0,03-0,1% мөлшерде енгізу есебінен ферросилиций отырғызылады. Бұл қоспалар металды тұндыруды қамтамасыз ету үшін енгізіледі.
Әрі қарай, қож пайда болады, пешке әк, балқытқыш шпат және шамот сынықтары 5:1:1 қатынасында металл массасының 2-4% мөлшерінде енгізіледі. 10-15 минуттан кейін қож қоспасы ериді, ал сұйық жылжымалы қож пайда болғаннан кейін олар ваннаны диффузиялық қыщқылсыздандыруға кіріседі. Мерзімді түрде, 10-12 минуттан кейін пешке әк, балқытқыш шпат және қышқылсыздандырғыш қоспасының бөліктері енгізіледі. Алғашқы 15-20 минут ішінде ұнтақталған кокс (көміртегі) осы қоспада қышқылсыздандырғыш ретінде қолданылады, содан кейін оның орнына ұнтақталған ферросилиций қолданылады; кейде таза кокстың немесе ферросилицийдің бір бөлігін беруге рұқсат етіледі. Болаттың кейбір маркаларында тотықсыздану кезеңінің соңында күшті қышқылсыздандырғыштар қоспасына өте күшті қышқылсыздандырғыштар - ұнтақталған силикокальций және ұнтақ тәрізді алюминий енгізеді.
Әдетте, ақ қождың астында тотығуға арналған кокстың шығыны 1-2 кг/т металды құрайды. Ферросилицийдің шығыны кремнийдің шамамен 50%—ы металға ауысатынын ескере отырып анықталады; тотықсыздану кезеңі ішінде ұнтақ тәрізді ферросилицийдің қожына арналған қоспалар есебінен металдағы кремнийдің құрамы 0,25-0,35% - ға дейін жеткізіледі (бұл оның кремниймен қоспаланған болаттардағы құрамына сәйкес келеді).
Слайд 12Бүкіл кезең ішінде жүретін диффузиялық қышқылсызданудың мәні келесідей. Қышқылсыздандырғыш заттарды ұнтақ түрінде
Бүкіл кезең ішінде жүретін диффузиялық қышқылсызданудың мәні келесідей. Қышқылсыздандырғыш заттарды ұнтақ түрінде
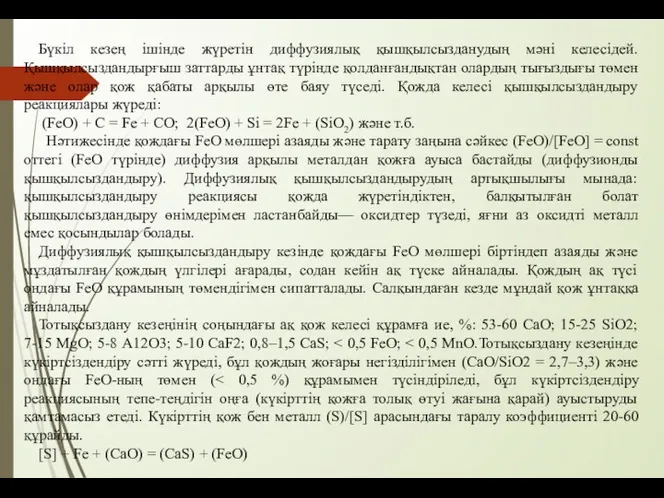
(FeO) + С = Fe + CO; 2(FeO) + Si = 2Fe + (SiО2) және т.б.
Нәтижесінде қождағы FeO мөлшері азаяды және тарату заңына сәйкес (FeO)/[FeO] = const оттегі (FeO түрінде) диффузия арқылы металдан қожға ауыса бастайды (диффузионды қышқылсыздандыру). Диффузиялық қышқылсыздандырудың артықшылығы мынада: қышқылсыздандыру реакциясы қожда жүретіндіктен, балқытылған болат қышқылсыздандыру өнімдерімен ластанбайды— оксидтер түзеді, яғни аз оксидті металл емес қосындылар болады.
Диффузиялық қышқылсыздандыру кезінде қождағы FeO мөлшері біртіндеп азаяды және мұздатылған қождың үлгілері ағарады, содан кейін ақ түске айналады. Қождың ақ түсі ондағы FeO құрамының төмендігімен сипатталады. Салқындаған кезде мұндай қож ұнтаққа айналады.
Тотықсыздану кезеңінің соңындағы ақ қож келесі құрамға ие, %: 53-60 СаО; 15-25 ЅіО2; 7-15 MgO; 5-8 А12О3; 5-10 CaF2; 0,8–1,5 CaS; < 0,5 FeO; < 0,5 MnO.Тотықсыздану кезеңінде күкіртсіздендіру сәтті жүреді, бұл қождың жоғары негізділігімен (CaO/ЅіО2 = 2,7–3,3) және ондағы FeO-ның төмен (< 0,5 %) құрамымен түсіндіріледі, бұл күкіртсіздендіру реакциясының тепе-теңдігін оңға (күкірттің қожға толық өтуі жағына қарай) ауыстыруды қамтамасыз етеді. Күкірттің қож бен металл (S)/[S] арасындағы таралу коэффициенті 20-60 құрайды.
[S] + Fe + (СаО) = (CaS) + (FeO)
Слайд 13Тотықсыздандыру кезеңінің соңында, қож бен металл қышқылсызданған кезде, металды оттегіге айтарлықтай химиялық
Тотықсыздандыру кезеңінің соңында, қож бен металл қышқылсызданған кезде, металды оттегіге айтарлықтай химиялық
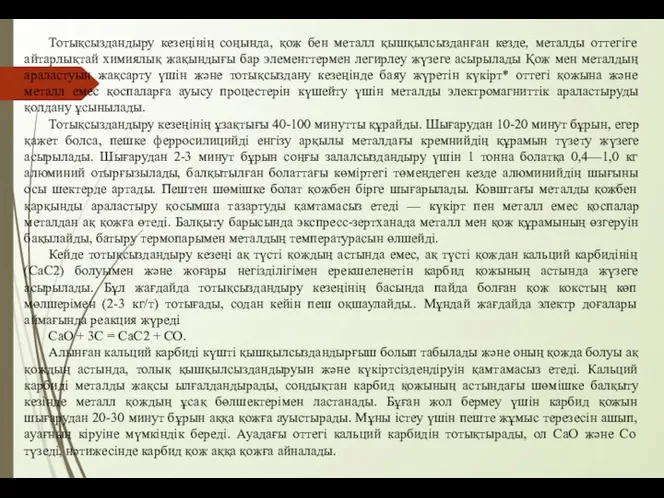
Тотықсыздандыру кезеңінің ұзақтығы 40-100 минутты құрайды. Шығарудан 10-20 минут бұрын, егер қажет болса, пешке ферросилицийді енгізу арқылы металдағы кремнийдің құрамын түзету жүзеге асырылады. Шығарудан 2-3 минут бұрын соңғы залалсыздандыру үшін 1 тонна болатқа 0,4—1,0 кг алюминий отырғызылады, балқытылған болаттағы көміртегі төмендеген кезде алюминийдің шығыны осы шектерде артады. Пештен шөмішке болат қожбен бірге шығарылады. Ковштағы металды қожбен қарқынды араластыру қосымша тазартуды қамтамасыз етеді — күкірт пен металл емес қоспалар металдан ақ қожға өтеді. Балқыту барысында экспресс-зертханада металл мен қож құрамының өзгеруін бақылайды, батыру термопарымен металдың температурасын өлшейді.
Кейде тотықсыздандыру кезеңі ақ түсті қождың астында емес, ақ түсті қождан кальций карбидінің (СаС2) болуымен және жоғары негізділігімен ерекшеленетін карбид қожының астында жүзеге асырылады. Бұл жағдайда тотықсыздандыру кезеңінің басында пайда болған қож кокстың көп мөлшерімен (2-3 кг/т) тотығады, содан кейін пеш оқшаулайды.. Мұндай жағдайда электр доғалары аймағында реакция жүреді
СаО + 3С = СаС2 + СО.
Алынған кальций карбиді күшті қышқылсыздандырғыш болып табылады және оның қожда болуы ақ қождың астында, толық қышқылсыздандыруын және күкіртсіздендіруін қамтамасыз етеді. Кальций карбиді металды жақсы ылғалдандырады, сондықтан карбид қожының астындағы шөмішке балқыту кезінде металл қождың ұсақ бөлшектерімен ластанады. Бұған жол бермеу үшін карбид қожын шығарудан 20-30 минут бұрын аққа қожға ауыстырады. Мұны істеу үшін пеште жұмыс терезесін ашып, ауағның кіруіне мүмкіндік береді. Ауадағы оттегі кальций карбидін тотықтырады, ол СaО және Co түзеді, нәтижесінде карбид қож аққа қожға айналады.