Содержание
- 2. Что такое каландрование Каландрование - это процесс непрерывного формования полимерного материала при пропускании его расплава через
- 3. Перерабатываемые материалы Каландрованием перерабатывают в основном поливинилхлорид (ПВХ) жесткий и пластифицированный, сополимеры винилхлорида и винилацетата, а
- 4. Краткая характеристика основных процессов переработки пластмасс на валковых машинах 2 1 3 4
- 5. Общая технологическая схема процесса каландрования При каландровании расплав полимера превращается в пленку или лист, проходя между
- 6. Схема каландровой линии для производства пленок из пластифицированного ПВХ вальцево-каландровым методом 1- смеситель непрерывного действия; 2
- 7. Получение пленки из пластифицированного ПВХ экструзионного – каландровым методом Предварительное смещение компонентов композиции осуществляется в червячном
- 8. Схема получения безосновного ПВХ линолеума Приготовление композиционной массы осуществляется в смесителе, куда при работающей мешалке последовательно
- 9. Подготовка композиций для каландрования Обработке материала на каландре предшествуют получение композиции полимера и пластикация. Поэтому свойства
- 10. Примерные рецептуры для каландрированных изделий общего назначения 100 масс. ч. П ВХ [ К= 65-70]; 40-60
- 11. Примерные рецептуры современных каландрированных пленок
- 12. Предварительная подготовка композиции ПВХ На первом этапе в начале линии каландрования ПВХ предусмотрено изготовление сухой смеси
- 13. Смешение компонентов композиции ПВХ Введение различных добавок в поливинилхлорид (ПВХ) необходимо из-за характера самого полимера и
- 14. Получение композиции ПВХ сухим смешением компонентов Схема двухстадийного смесителя 1- лопасть для регулирования вращательного движения смеси;
- 15. Смешение композиции на обогреваемых вальцах После пластикации формовочная полимерная масса по транспортерной ленте передается на смесительные
- 16. Подготовка композиции ПВХ на вальцах Вальцы состоят из двух литых станин 6, установленных на фундаментной плите
- 17. Технологические параметры вальцевания композиций ПВХ Режимы вальцевания композиций для производства линолеума Режимы вальцевания композиций непластифицированного ПВХ
- 18. Смешение композиции на пластикационном экструдере Для подготовки композиции, включая смешение, гомогенизацию и пластикацию, используют экструдеры различных
- 19. Технологическая схема процесса каландрования
- 20. Описание технологической схемы Из отделения подготовки композиции на основе ПВХ пластицированный материал в виде прутка или
- 21. Принцип получения пленки методом каландрования Пластифицированная термопластичная масса с помощью непрерывной транспортерной ленты подается к каландру,
- 22. Виды каландровых установок Конструкция универсальных каландров позволяет выполнять большинство технологических операций, производимых в процессе каландрования. Существуют
- 23. Основные типы каландров и их применение Основная операция — формование пленки — происходит на каландре. Каландры
- 24. Преимущества и недостатки разных схем расположения валков 4-валкового каландра Преимущество L-образного каландра (б) состоит в том,
- 25. Схема четырехвалкового каландра для ПВХ
- 26. Эпюра скоростей и давлений в зазоре валков каландра Схема работы каландра (а) и эпюры скоростей (б)
- 27. Процессы, происходящие в зазоре валков каландра На входе в валки обычно имеется избыток материала, в котором
- 28. Компенсация распорного усилия в валках каландра Высокое давление (7—70 МПа), развивающееся в зазоре между валками каландра,
- 29. Бомбировка валков заключается в придании им бочкообразной формы. Увеличение диаметра средней части валка по сравнению с
- 30. Система охлаждающих барабанов и ширительного устройства Принципиальная схема валка ширительно-расправочного устройства
- 31. Охлаждение полотна на охлаждающих барабанах Полученное полотно охлаждается при помощи валков, внутрь которых подается вода. В
- 32. Состав комплектной каландровой линии
- 33. Режимы каландрования при изготовлении листов и пленок из композиций на основе различных типов ПВХ
- 34. Параметры процесса каландрования Пленка, полученная каландровым способом, обладает продольной ориентацией. Так, при переработке пластифицированного ПВХ линейная
- 35. Влияние параметров процесса каландрования Влияние минимального зазора на потребляемую мощность N и производительность Q. Влияние скорости
- 36. Производительность четырехвалкового Г-образного каландра при изготовлении пленки разной толщины
- 37. Виды брака при каландровании
- 38. Использованная литература Переработка пластмасс под ред. Брагинского В.А. Л., Химия, 1985 г. 2. Основы технологии переработки
- 40. Скачать презентацию
Слайд 2Что такое каландрование
Каландрование - это процесс непрерывного формования полимерного материала при пропускании
Что такое каландрование
Каландрование - это процесс непрерывного формования полимерного материала при пропускании
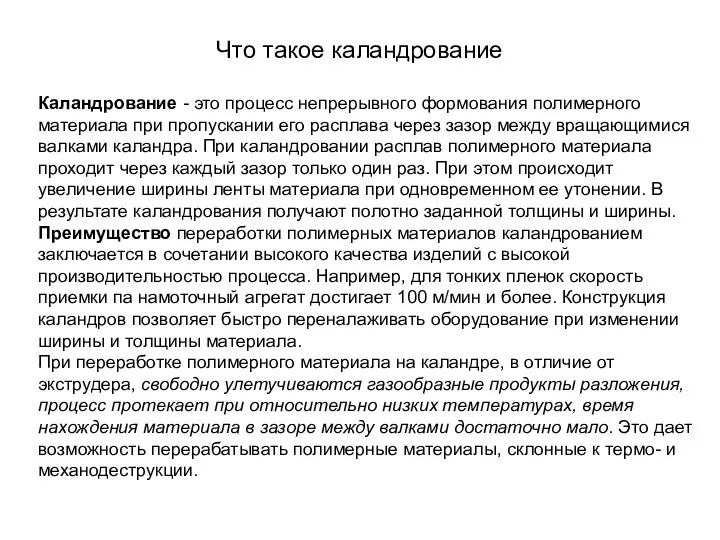
Преимущество переработки полимерных материалов каландрованием заключается в сочетании высокого качества изделий с высокой производительностью процесса. Например, для тонких пленок скорость приемки па намоточный агрегат достигает 100 м/мин и более. Конструкция каландров позволяет быстро переналаживать оборудование при изменении ширины и толщины материала.
При переработке полимерного материала на каландре, в отличие от экструдера, свободно улетучиваются газообразные продукты разложения, процесс протекает при относительно низких температурах, время нахождения материала в зазоре между валками достаточно мало. Это дает возможность перерабатывать полимерные материалы, склонные к термо- и механодеструкции.
Слайд 3Перерабатываемые материалы
Каландрованием перерабатывают в основном поливинилхлорид (ПВХ) жесткий и пластифицированный, сополимеры винилхлорида
Перерабатываемые материалы
Каландрованием перерабатывают в основном поливинилхлорид (ПВХ) жесткий и пластифицированный, сополимеры винилхлорида
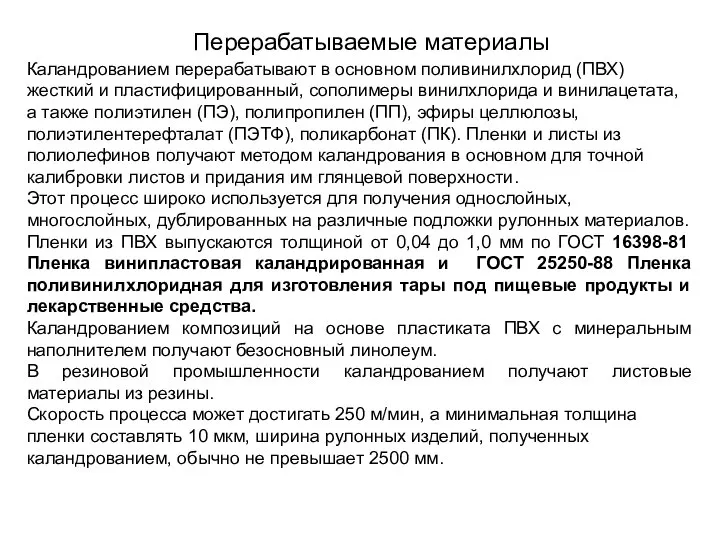
Этот процесс широко используется для получения однослойных, многослойных, дублированных на различные подложки рулонных материалов.
Пленки из ПВХ выпускаются толщиной от 0,04 до 1,0 мм по ГОСТ 16398-81 Пленка винипластовая каландрированная и ГОСТ 25250-88 Пленка поливинилхлоридная для изготовления тары под пищевые продукты и лекарственные средства.
Каландрованием композиций на основе пластиката ПВХ с минеральным наполнителем получают безосновный линолеум.
В резиновой промышленности каландрованием получают листовые материалы из резины.
Скорость процесса может достигать 250 м/мин, а минимальная толщина пленки составлять 10 мкм, ширина рулонных изделий, полученных каландрованием, обычно не превышает 2500 мм.
Слайд 4Краткая характеристика основных процессов переработки пластмасс на валковых машинах
2
1
3
4
Краткая характеристика основных процессов переработки пластмасс на валковых машинах
2
1
3
4
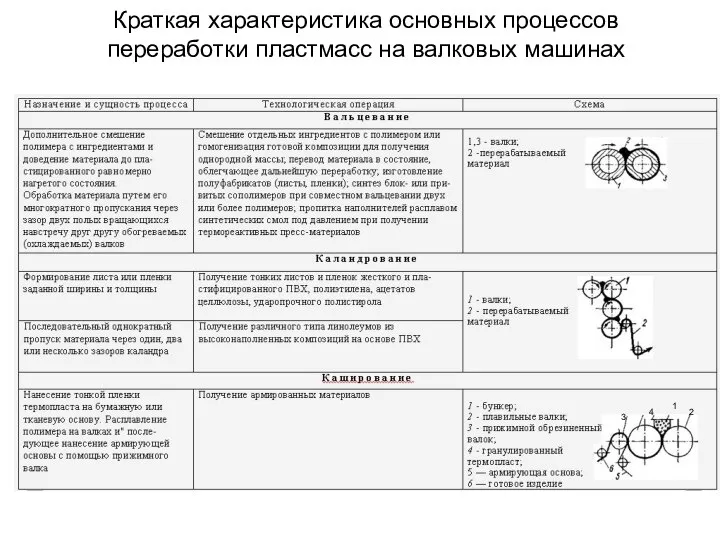
Слайд 5Общая технологическая схема процесса каландрования
При каландровании расплав полимера превращается в пленку или
Общая технологическая схема процесса каландрования
При каландровании расплав полимера превращается в пленку или
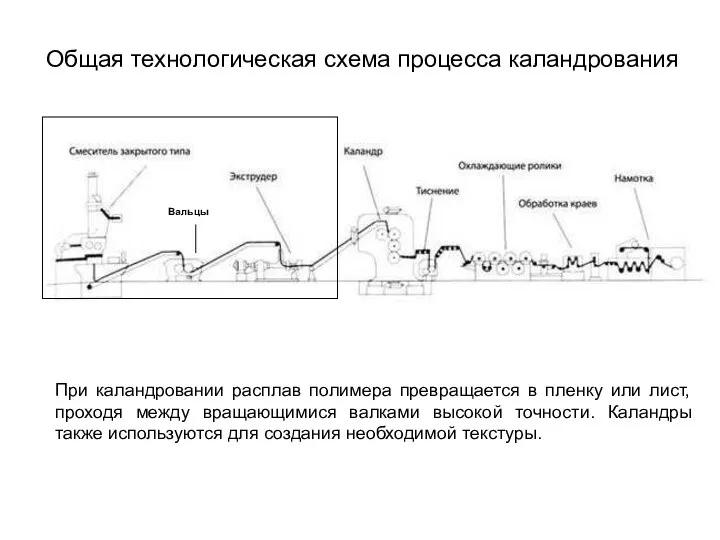
Вальцы
Слайд 6Схема каландровой линии для производства пленок из пластифицированного ПВХ вальцево-каландровым методом
1- смеситель
Схема каландровой линии для производства пленок из пластифицированного ПВХ вальцево-каландровым методом
1- смеситель
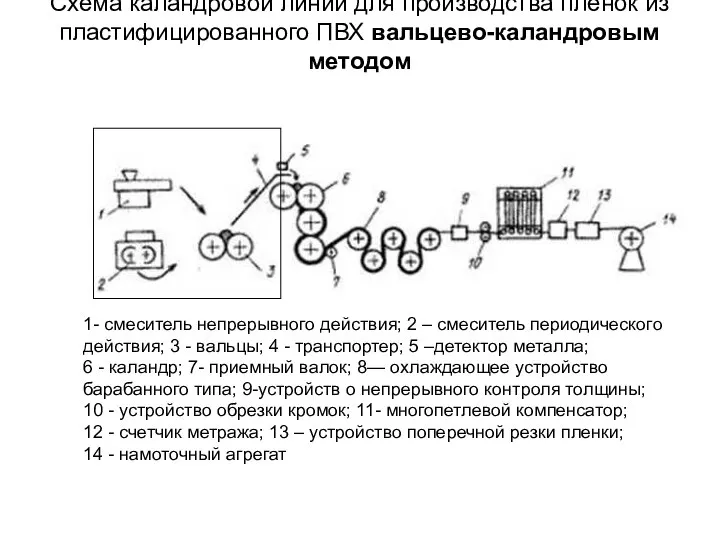
6 - каландр; 7- приемный валок; 8— охлаждающее устройство барабанного типа; 9-устройств о непрерывного контроля толщины;
10 - устройство обрезки кромок; 11- многопетлевой компенсатор;
12 - счетчик метража; 13 – устройство поперечной резки пленки;
14 - намоточный агрегат
Слайд 7Получение пленки из пластифицированного ПВХ экструзионного – каландровым методом
Предварительное смещение компонентов композиции
Получение пленки из пластифицированного ПВХ экструзионного – каландровым методом
Предварительное смещение компонентов композиции
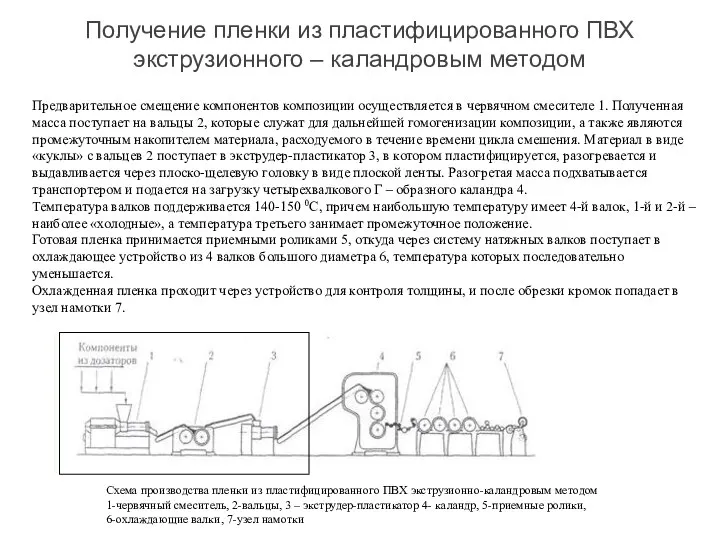
Температура валков поддерживается 140-150 0С, причем наибольшую температуру имеет 4-й валок, 1-й и 2-й – наиболее «холодные», а температура третьего занимает промежуточное положение.
Готовая пленка принимается приемными роликами 5, откуда через систему натяжных валков поступает в охлаждающее устройство из 4 валков большого диаметра 6, температура которых последовательно уменьшается.
Охлажденная пленка проходит через устройство для контроля толщины, и после обрезки кромок попадает в узел намотки 7.
Схема производства пленки из пластифицированного ПВХ экструзионно-каландровым методом
1-червячный смеситель, 2-вальцы, 3 – экструдер-пластикатор 4- каландр, 5-приемные ролики,
6-охлаждающие валки, 7-узел намотки
Слайд 8Схема получения безосновного ПВХ линолеума
Приготовление композиционной массы осуществляется в смесителе, куда при
Схема получения безосновного ПВХ линолеума
Приготовление композиционной массы осуществляется в смесителе, куда при
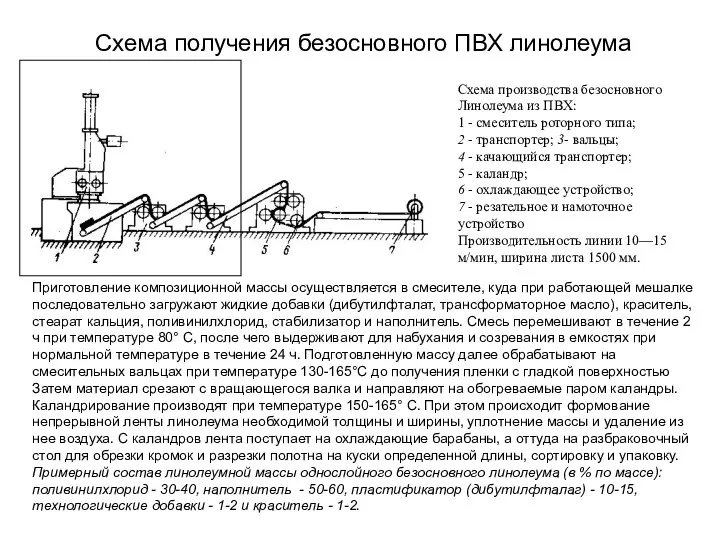
Слайд 9Подготовка композиций для каландрования
Обработке материала на каландре предшествуют получение композиции полимера и
Подготовка композиций для каландрования
Обработке материала на каландре предшествуют получение композиции полимера и
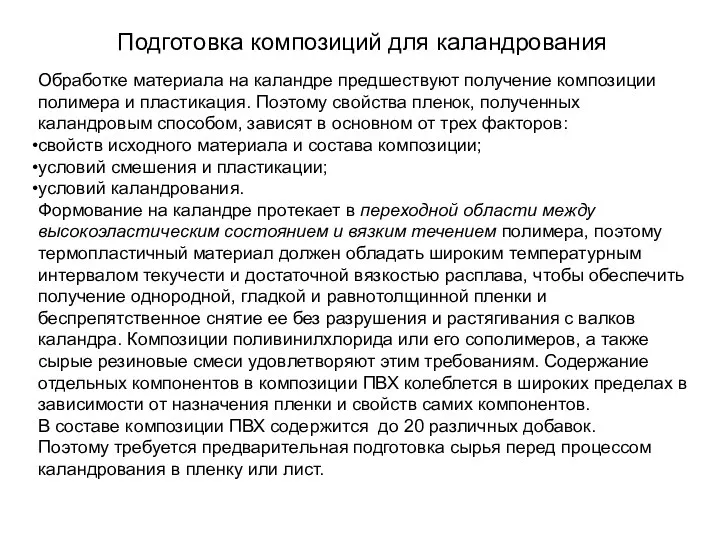
свойств исходного материала и состава композиции;
условий смешения и пластикации;
условий каландрования.
Формование на каландре протекает в переходной области между высокоэластическим состоянием и вязким течением полимера, поэтому термопластичный материал должен обладать широким температурным интервалом текучести и достаточной вязкостью расплава, чтобы обеспечить получение однородной, гладкой и равнотолщинной пленки и беспрепятственное снятие ее без разрушения и растягивания с валков каландра. Композиции поливинилхлорида или его сополимеров, а также сырые резиновые смеси удовлетворяют этим требованиям. Содержание отдельных компонентов в композиции ПВХ колеблется в широких пределах в зависимости от назначения пленки и свойств самих компонентов.
В составе композиции ПВХ содержится до 20 различных добавок.
Поэтому требуется предварительная подготовка сырья перед процессом каландрования в пленку или лист.
Слайд 10Примерные рецептуры для каландрированных
изделий общего назначения
100 масс. ч. П ВХ [
Примерные рецептуры для каландрированных
изделий общего назначения
100 масс. ч. П ВХ [
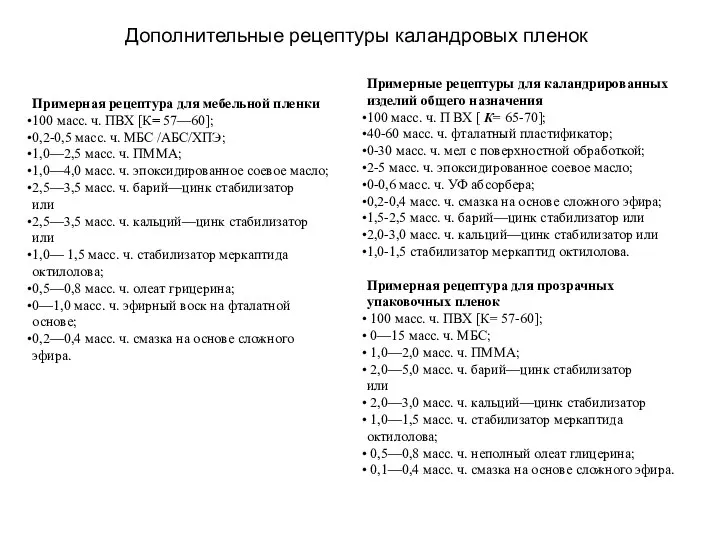
40-60 масс. ч. фталатный пластификатор;
0-30 масс. ч. мел с поверхностной обработкой;
2-5 масс. ч. эпоксидированное соевое масло;
0-0,6 масс. ч. УФ абсорбера;
0,2-0,4 масс. ч. смазка на основе сложного эфира;
1,5-2,5 масс. ч. барий—цинк стабилизатор или
2,0-3,0 масс. ч. кальций—цинк стабилизатор или
1,0-1,5 стабилизатор меркаптид октилолова.
Примерная рецептура для прозрачных упаковочных пленок
100 масс. ч. ПВХ [К= 57-60];
0—15 масс. ч. МБС;
1,0—2,0 масс. ч. ПММА;
2,0—5,0 масс. ч. барий—цинк стабилизатор
или
2,0—3,0 масс. ч. кальций—цинк стабилизатор
1,0—1,5 масс. ч. стабилизатор меркаптида октилолова;
0,5—0,8 масс. ч. неполный олеат глицерина;
0,1—0,4 масс. ч. смазка на основе сложного эфира.
Дополнительные рецептуры каландровых пленок
Слайд 11Примерные рецептуры современных каландрированных пленок
Примерные рецептуры современных каландрированных пленок
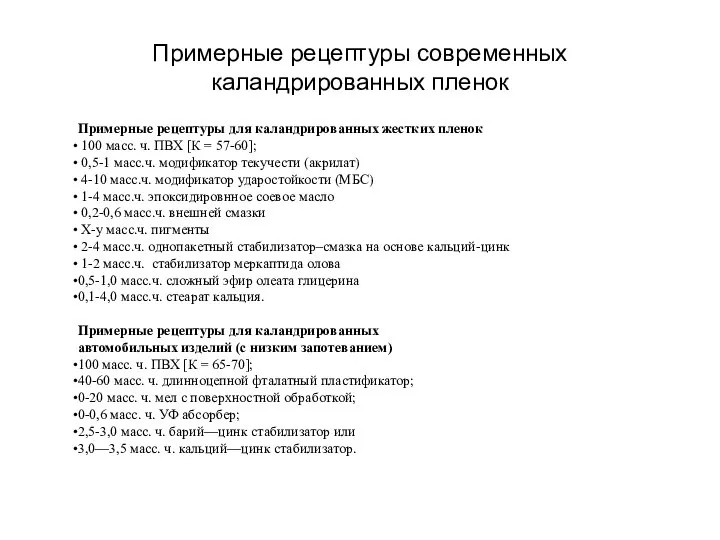
Слайд 12Предварительная подготовка композиции ПВХ
На первом этапе в начале линии каландрования ПВХ предусмотрено
Предварительная подготовка композиции ПВХ
На первом этапе в начале линии каландрования ПВХ предусмотрено
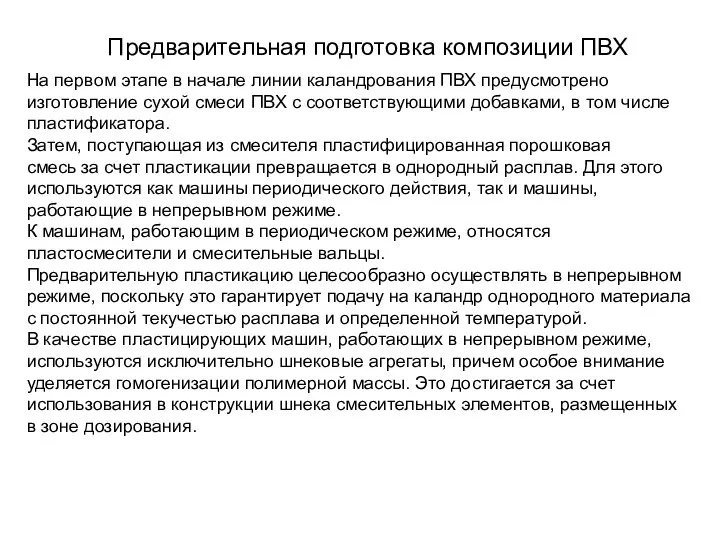
пластификатора.
Затем, поступающая из смесителя пластифицированная порошковая
смесь за счет пластикации превращается в однородный расплав. Для этого
используются как машины периодического действия, так и машины,
работающие в непрерывном режиме.
К машинам, работающим в периодическом режиме, относятся пластосмесители и смесительные вальцы.
Предварительную пластикацию целесообразно осуществлять в непрерывном
режиме, поскольку это гарантирует подачу на каландр однородного материала с постоянной текучестью расплава и определенной температурой.
В качестве пластицирующих машин, работающих в непрерывном режиме,
используются исключительно шнековые агрегаты, причем особое внимание
уделяется гомогенизации полимерной массы. Это достигается за счет
использования в конструкции шнека смесительных элементов, размещенных
в зоне дозирования.
Слайд 13Смешение компонентов композиции ПВХ
Введение различных добавок в поливинилхлорид (ПВХ) необходимо из-за характера
Смешение компонентов композиции ПВХ
Введение различных добавок в поливинилхлорид (ПВХ) необходимо из-за характера
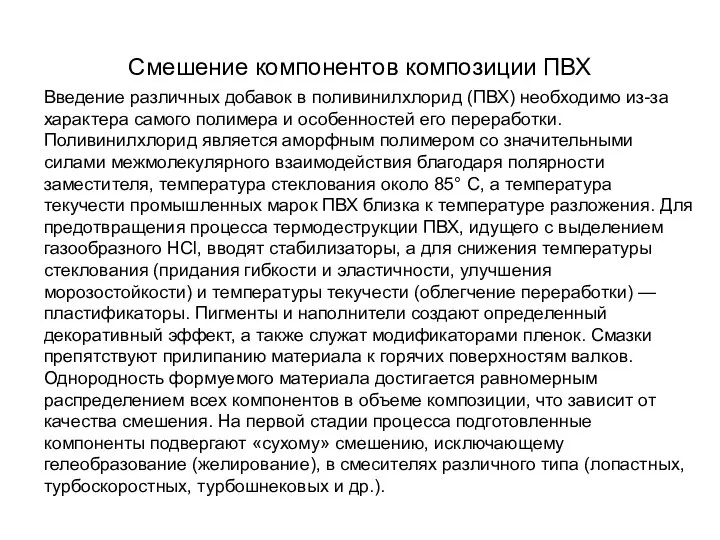
Однородность формуемого материала достигается равномерным распределением всех компонентов в объеме композиции, что зависит от качества смешения. На первой стадии процесса подготовленные компоненты подвергают «сухому» смешению, исключающему гелеобразование (желирование), в смесителях различного типа (лопастных, турбоскоростных, турбошнековых и др.).
Слайд 14Получение композиции ПВХ сухим смешением компонентов
Схема двухстадийного смесителя
1- лопасть для регулирования вращательного
Получение композиции ПВХ сухим смешением компонентов
Схема двухстадийного смесителя
1- лопасть для регулирования вращательного
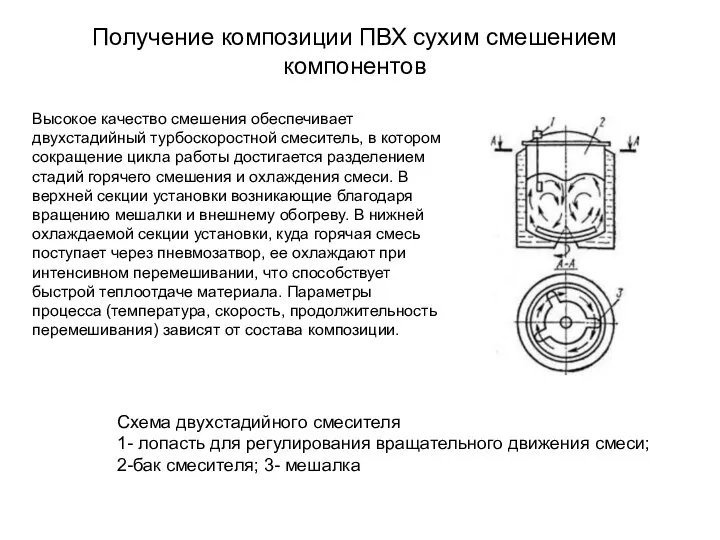
Высокое качество смешения обеспечивает двухстадийный турбоскоростной смеситель, в котором сокращение цикла работы достигается разделением стадий горячего смешения и охлаждения смеси. В верхней секции установки возникающие благодаря вращению мешалки и внешнему обогреву. В нижней охлаждаемой секции установки, куда горячая смесь поступает через пневмозатвор, ее охлаждают при интенсивном перемешивании, что способствует быстрой теплоотдаче материала. Параметры процесса (температура, скорость, продолжительность перемешивания) зависят от состава композиции.
Слайд 15Смешение композиции на обогреваемых вальцах
После пластикации формовочная полимерная масса по транспортерной ленте
Смешение композиции на обогреваемых вальцах
После пластикации формовочная полимерная масса по транспортерной ленте
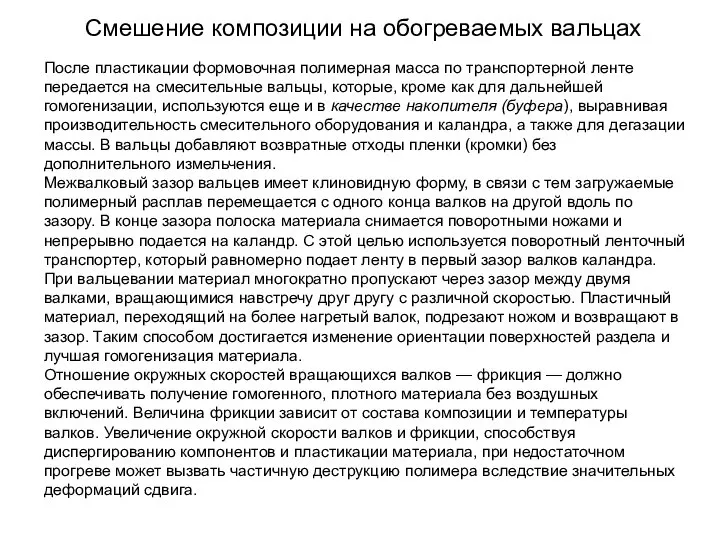
Межвалковый зазор вальцев имеет клиновидную форму, в связи с тем загружаемые полимерный расплав перемещается с одного конца валков на другой вдоль по зазору. В конце зазора полоска материала снимается поворотными ножами и непрерывно подается на каландр. С этой целью используется поворотный ленточный транспортер, который равномерно подает ленту в первый зазор валков каландра.
При вальцевании материал многократно пропускают через зазор между двумя валками, вращающимися навстречу друг другу с различной скоростью. Пластичный материал, переходящий на более нагретый валок, подрезают ножом и возвращают в зазор. Таким способом достигается изменение ориентации поверхностей раздела и лучшая гомогенизация материала.
Отношение окружных скоростей вращающихся валков — фрикция — должно обеспечивать получение гомогенного, плотного материала без воздушных включений. Величина фрикции зависит от состава композиции и температуры валков. Увеличение окружной скорости валков и фрикции, способствуя диспергированию компонентов и пластикации материала, при недостаточном прогреве может вызвать частичную деструкцию полимера вследствие значительных деформаций сдвига.
Слайд 16Подготовка композиции ПВХ на вальцах
Вальцы состоят из двух литых станин 6, установленных
Подготовка композиции ПВХ на вальцах
Вальцы состоят из двух литых станин 6, установленных
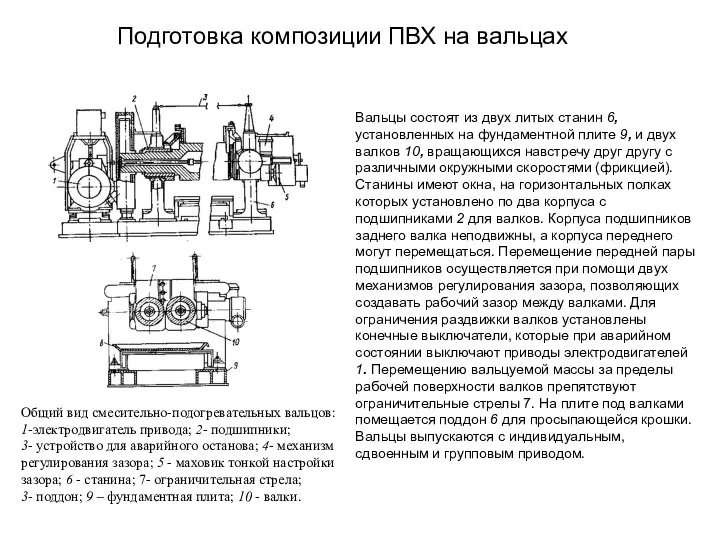
Слайд 17Технологические параметры вальцевания композиций ПВХ
Режимы вальцевания композиций для производства линолеума
Режимы вальцевания
Технологические параметры вальцевания композиций ПВХ
Режимы вальцевания композиций для производства линолеума
Режимы вальцевания
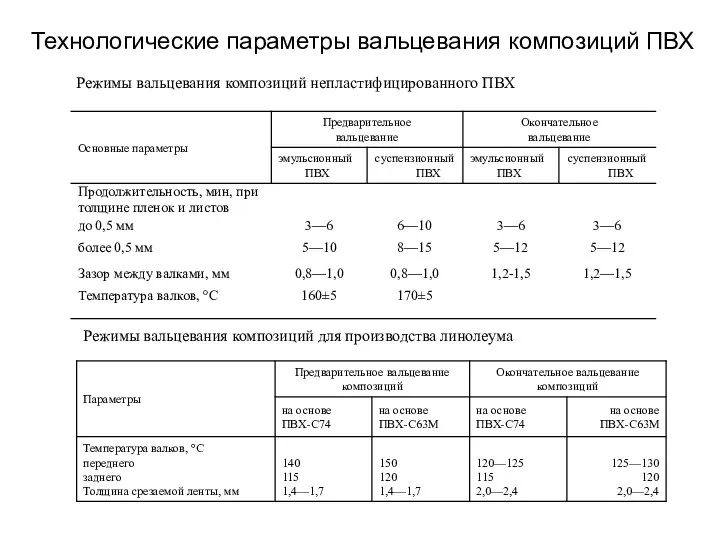
Продолжительность, мин, при
толщине пленок и листов
Слайд 18Смешение композиции на пластикационном экструдере
Для подготовки композиции, включая смешение, гомогенизацию и пластикацию,
Смешение композиции на пластикационном экструдере
Для подготовки композиции, включая смешение, гомогенизацию и пластикацию,
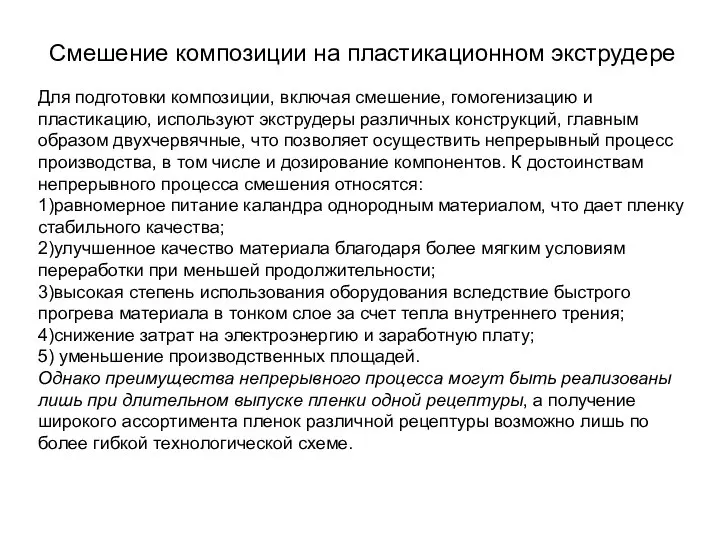
1)равномерное питание каландра однородным материалом, что дает пленку стабильного качества;
2)улучшенное качество материала благодаря более мягким условиям переработки при меньшей продолжительности;
3)высокая степень использования оборудования вследствие быстрого прогрева материала в тонком слое за счет тепла внутреннего трения;
4)снижение затрат на электроэнергию и заработную плату;
5) уменьшение производственных площадей.
Однако преимущества непрерывного процесса могут быть реализованы лишь при длительном выпуске пленки одной рецептуры, а получение широкого ассортимента пленок различной рецептуры возможно лишь по более гибкой технологической схеме.
Слайд 19Технологическая схема процесса каландрования
Технологическая схема процесса каландрования
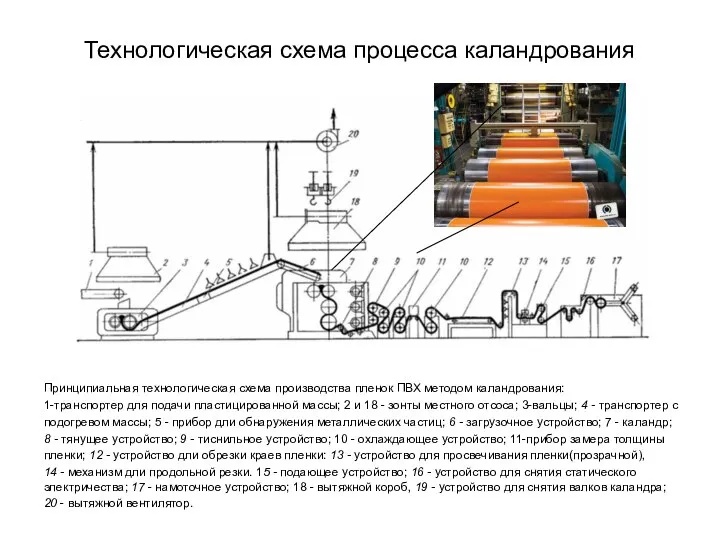
Слайд 20Описание технологической схемы
Из отделения подготовки композиции на основе ПВХ пластицированный материал в
Описание технологической схемы
Из отделения подготовки композиции на основе ПВХ пластицированный материал в
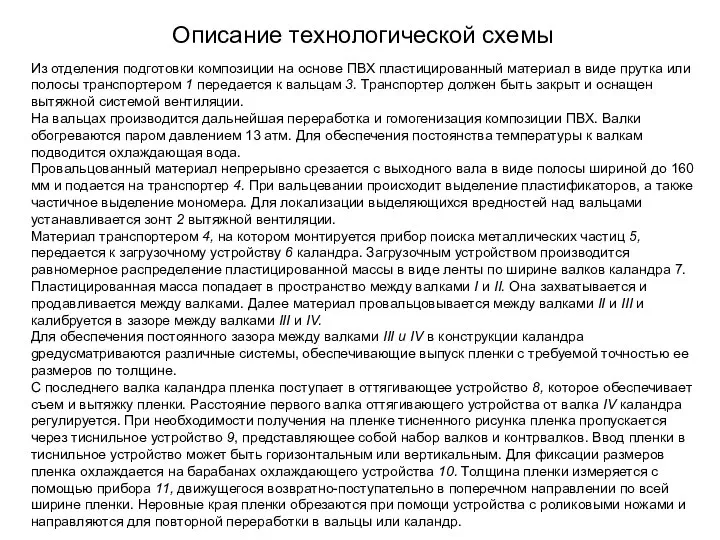
На вальцах производится дальнейшая переработка и гомогенизация композиции ПВХ. Валки обогреваются паром давлением 13 атм. Для обеспечения постоянства температуры к валкам подводится охлаждающая вода.
Провальцованный материал непрерывно срезается с выходного вала в виде полосы шириной до 160 мм и подается на транспортер 4. При вальцевании происходит выделение пластификаторов, а также частичное выделение мономера. Для локализации выделяющихся вредностей над вальцами устанавливается зонт 2 вытяжной вентиляции.
Материал транспортером 4, на котором монтируется прибор поиска металлических частиц 5, передается к загрузочному устройству 6 каландра. Загрузочным устройством производится равномерное распределение пластицированной массы в виде ленты по ширине валков каландра 7.
Пластицированная масса попадает в пространство между валками I и II. Она захватывается и продавливается между валками. Далее материал провальцовывается между валками II и III и калибруется в зазоре между валками III и IV.
Для обеспечения постоянного зазора между валками III и IV в конструкции каландра gредусматриваются различные системы, обеспечивающие выпуск пленки с требуемой точностью ее размеров по толщине.
С последнего валка каландра пленка поступает в оттягивающее устройство 8, которое обеспечивает съем и вытяжку пленки. Расстояние первого валка оттягивающего устройства от валка IV каландра регулируется. При необходимости получения на пленке тисненного рисунка пленка пропускается через тиснильное устройство 9, представляющее собой набор валков и контрвалков. Ввод пленки в тиснильное устройство может быть горизонтальным или вертикальным. Для фиксации размеров пленка охлаждается на барабанах охлаждающего устройства 10. Толщина пленки измеряется с помощью прибора 11, движущегося возвратно-поступательно в поперечном направлении по всей ширине пленки. Неровные края пленки обрезаются при помощи устройства с роликовыми ножами и направляются для повторной переработки в вальцы или каландр.
Слайд 21Принцип получения пленки методом каландрования
Пластифицированная термопластичная масса с помощью непрерывной транспортерной
Принцип получения пленки методом каландрования
Пластифицированная термопластичная масса с помощью непрерывной транспортерной
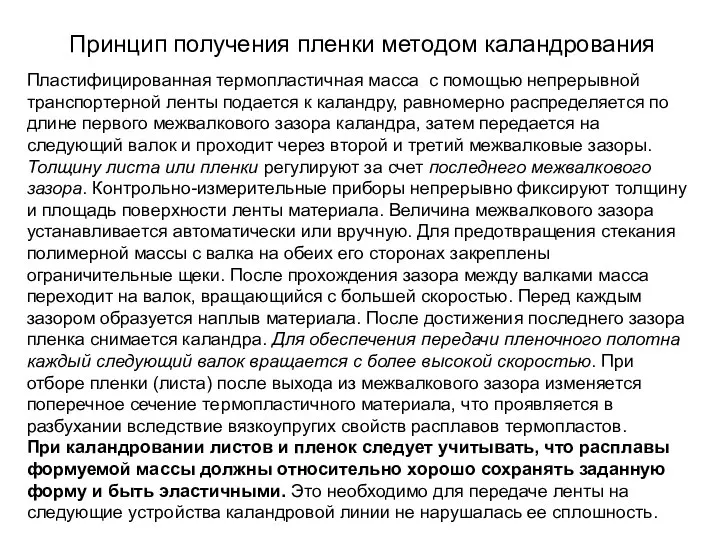
При каландровании листов и пленок следует учитывать, что расплавы формуемой массы должны относительно хорошо сохранять заданную форму и быть эластичными. Это необходимо для передаче ленты на следующие устройства каландровой линии не нарушалась ее сплошность.
Слайд 22Виды каландровых установок
Конструкция универсальных каландров позволяет выполнять большинство технологических операций, производимых в
Виды каландровых установок
Конструкция универсальных каландров позволяет выполнять большинство технологических операций, производимых в
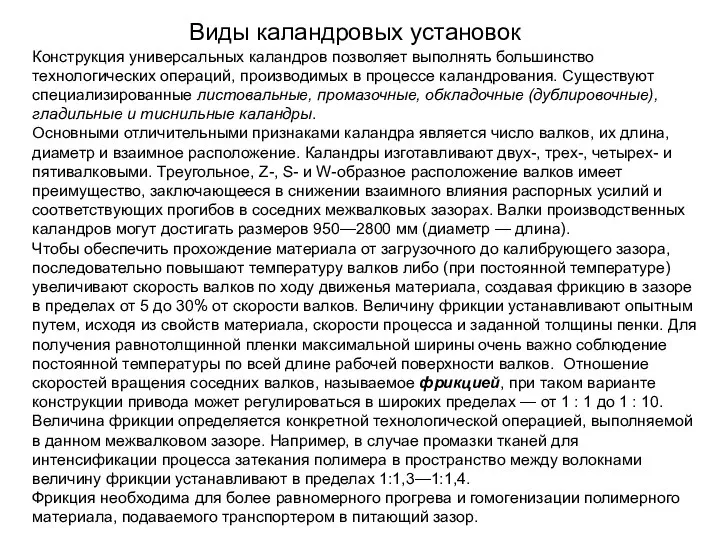
Основными отличительными признаками каландра является число валков, их длина, диаметр и взаимное расположение. Каландры изготавливают двух-, трех-, четырех- и пятивалковыми. Треугольное, Z-, S- и W-образное расположение валков имеет преимущество, заключающееся в снижении взаимного влияния распорных усилий и соответствующих прогибов в соседних межвалковых зазорах. Валки производственных каландров могут достигать размеров 950—2800 мм (диаметр — длина).
Чтобы обеспечить прохождение материала от загрузочного до калибрующего зазора, последовательно повышают температуру валков либо (при постоянной температуре) увеличивают скорость валков по ходу движенья материала, создавая фрикцию в зазоре в пределах от 5 до 30% от скорости валков. Величину фрикции устанавливают опытным путем, исходя из свойств материала, скорости процесса и заданной толщины пенки. Для получения равнотолщинной пленки максимальной ширины очень важно соблюдение постоянной температуры по всей длине рабочей поверхности валков. Отношение скоростей вращения соседних валков, называемое фрикцией, при таком варианте конструкции привода может регулироваться в широких пределах — от 1 : 1 до 1 : 10. Величина фрикции определяется конкретной технологической операцией, выполняемой в данном межвалковом зазоре. Например, в случае промазки тканей для интенсификации процесса затекания полимера в пространство между волокнами величину фрикции устанавливают в пределах 1:1,3—1:1,4.
Фрикция необходима для более равномерного прогрева и гомогенизации полимерного материала, подаваемого транспортером в питающий зазор.
Слайд 23Основные типы каландров и их применение
Основная операция — формование пленки — происходит
Основные типы каландров и их применение
Основная операция — формование пленки — происходит
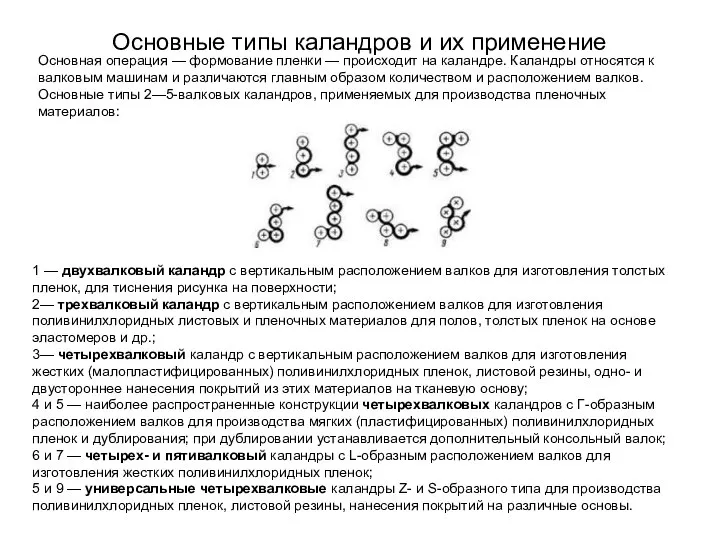
Основные типы 2—5-валковых каландров, применяемых для производства пленочных материалов:
1 — двухвалковый каландр с вертикальным расположением валков для изготовления толстых пленок, для тиснения рисунка на поверхности;
2— трехвалковый каландр с вертикальным расположением валков для изготовления поливинилхлоридных листовых и пленочных материалов для полов, толстых пленок на основе эластомеров и др.;
3— четырехвалковый каландр с вертикальным расположением валков для изготовления жестких (малопластифицированных) поливинилхлоридных пленок, листовой резины, одно- и двустороннее нанесения покрытий из этих материалов на тканевую основу;
4 и 5 — наиболее распространенные конструкции четырехвалковых каландров с Г-образным расположением валков для производства мягких (пластифицированных) поливинилхлоридных пленок и дублирования; при дублировании устанавливается дополнительный консольный валок;
6 и 7 — четырех- и пятивалковый каландры с L-образным расположением валков для изготовления жестких поливинилхлоридных пленок;
5 и 9 — универсальные четырехвалковые каландры Z- и S-образного типа для производства поливинилхлоридных пленок, листовой резины, нанесения покрытий на различные основы.
Слайд 24Преимущества и недостатки разных схем расположения валков 4-валкового каландра
Преимущество L-образного каландра (б)
Преимущества и недостатки разных схем расположения валков 4-валкового каландра
Преимущество L-образного каландра (б)
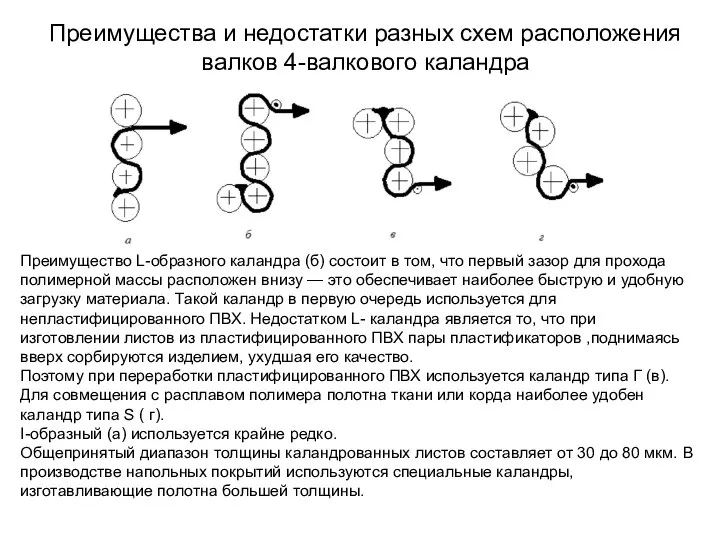
Поэтому при переработки пластифицированного ПВХ используется каландр типа Г (в). Для совмещения с расплавом полимера полотна ткани или корда наиболее удобен каландр типа S ( г).
I-образный (а) используется крайне редко.
Общепринятый диапазон толщины каландрованных листов составляет от 30 до 80 мкм. В производстве напольных покрытий используются специальные каландры,
изготавливающие полотна большей толщины.
Слайд 25Схема четырехвалкового каландра для ПВХ
Схема четырехвалкового каландра для ПВХ
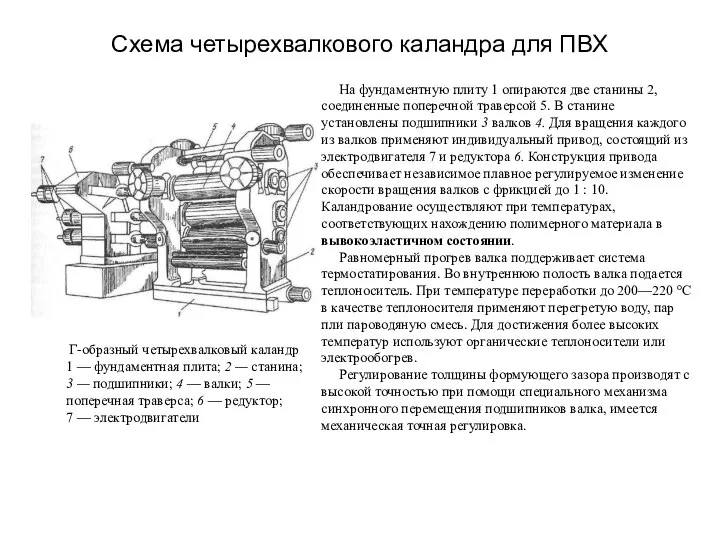
Слайд 26Эпюра скоростей и давлений в зазоре валков каландра
Схема работы каландра (а) и
Эпюра скоростей и давлений в зазоре валков каландра
Схема работы каландра (а) и
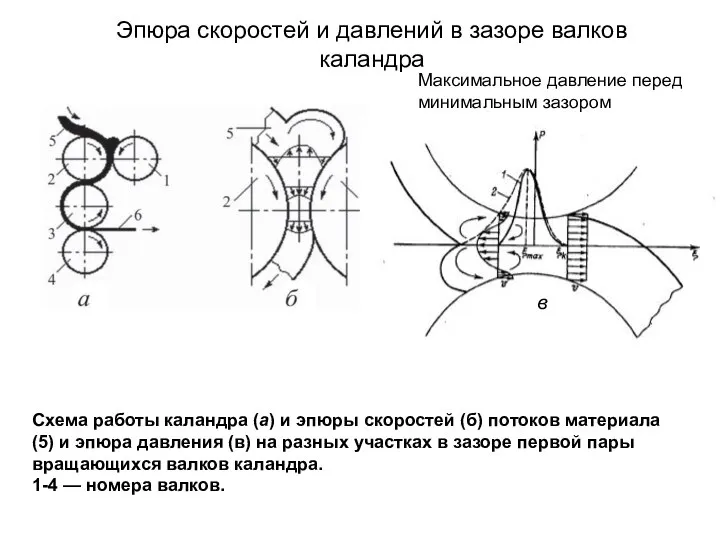
1-4 — номера валков.
в
Максимальное давление перед
минимальным зазором
Слайд 27Процессы, происходящие в зазоре валков каландра
На входе в валки обычно имеется избыток
Процессы, происходящие в зазоре валков каландра
На входе в валки обычно имеется избыток

Слайд 28Компенсация распорного усилия в валках каландра
Высокое давление (7—70 МПа), развивающееся в зазоре
Компенсация распорного усилия в валках каландра
Высокое давление (7—70 МПа), развивающееся в зазоре
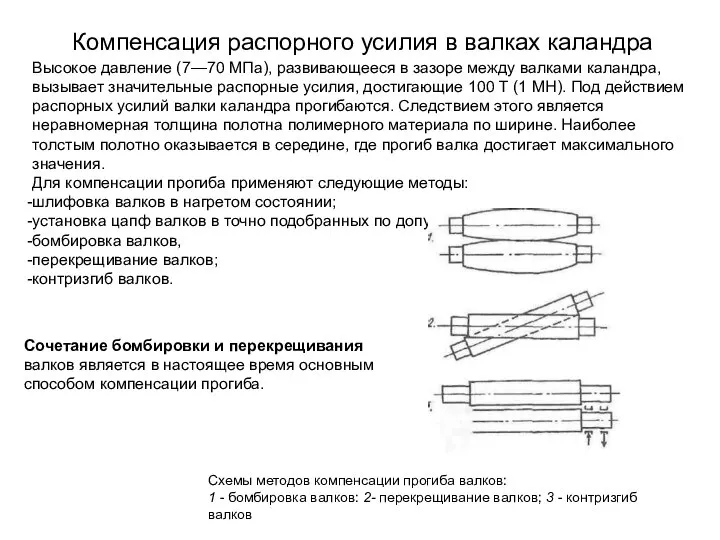
Для компенсации прогиба применяют следующие методы:
шлифовка валков в нагретом состоянии;
установка цапф валков в точно подобранных по допуску подшипниках качения;
бомбировка валков,
перекрещивание валков;
контризгиб валков.
Сочетание бомбировки и перекрещивания валков является в настоящее время основным способом компенсации прогиба.
Слайд 29Бомбировка валков заключается в придании им бочкообразной формы. Увеличение диаметра средней части
Бомбировка валков заключается в придании им бочкообразной формы. Увеличение диаметра средней части
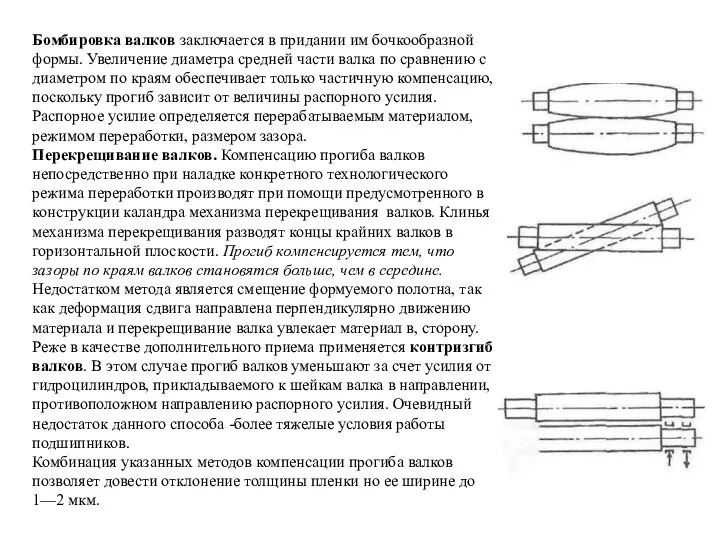
Перекрещивание валков. Компенсацию прогиба валков непосредственно при наладке конкретного технологического режима переработки производят при помощи предусмотренного в конструкции каландра механизма перекрещивания валков. Клинья механизма перекрещивания разводят концы крайних валков в горизонтальной плоскости. Прогиб компенсируется тем, что зазоры по краям валков становятся больше, чем в середине.
Недостатком метода является смещение формуемого полотна, так как деформация сдвига направлена перпендикулярно движению материала и перекрещивание валка увлекает материал в, сторону.
Реже в качестве дополнительного приема применяется контризгиб валков. В этом случае прогиб валков уменьшают за счет усилия от гидроцилиндров, прикладываемого к шейкам валка в направлении, противоположном направлению распорного усилия. Очевидный недостаток данного способа -более тяжелые условия работы подшипников.
Комбинация указанных методов компенсации прогиба валков позволяет довести отклонение толщины пленки но ее ширине до 1—2 мкм.
Слайд 30Система охлаждающих барабанов и ширительного устройства
Принципиальная схема валка ширительно-расправочного устройства
Система охлаждающих барабанов и ширительного устройства
Принципиальная схема валка ширительно-расправочного устройства
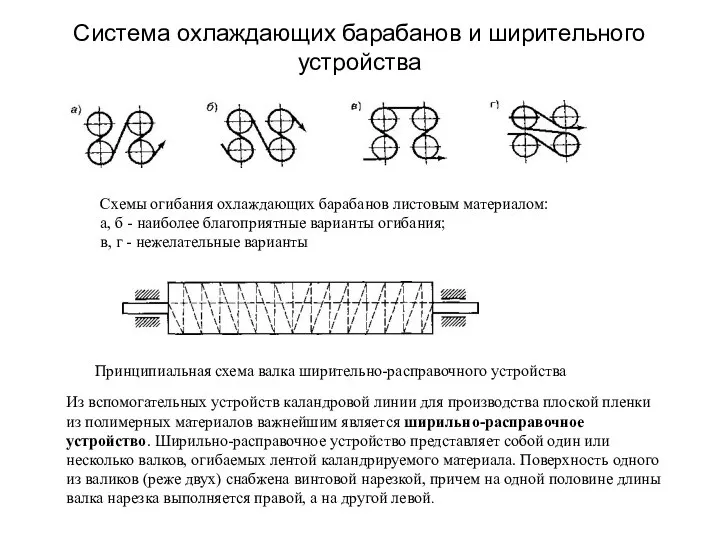
Слайд 31Охлаждение полотна на охлаждающих барабанах
Полученное полотно охлаждается при помощи валков, внутрь которых
Охлаждение полотна на охлаждающих барабанах
Полученное полотно охлаждается при помощи валков, внутрь которых
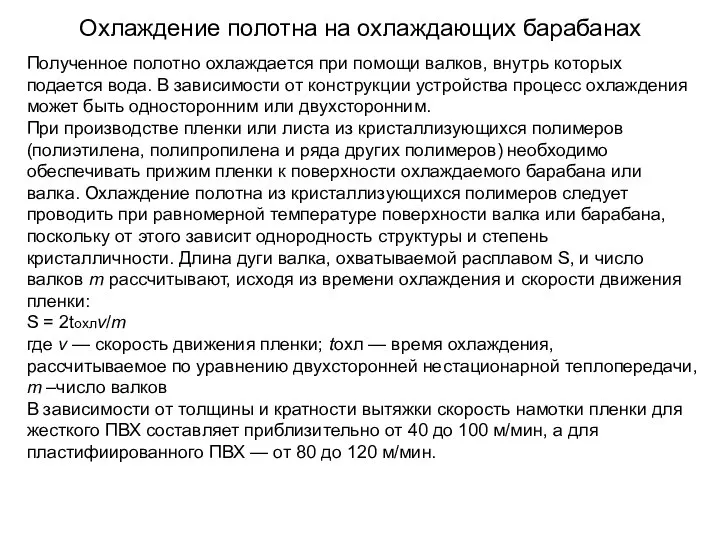
При производстве пленки или листа из кристаллизующихся полимеров (полиэтилена, полипропилена и ряда других полимеров) необходимо обеспечивать прижим пленки к поверхности охлаждаемого барабана или валка. Охлаждение полотна из кристаллизующихся полимеров следует проводить при равномерной температуре поверхности валка или барабана, поскольку от этого зависит однородность структуры и степень кристалличности. Длина дуги валка, охватываемой расплавом S, и число валков т рассчитывают, исходя из времени охлаждения и скорости движения пленки:
S = 2tохлv/m
где v — скорость движения пленки; tоxл — время охлаждения, рассчитываемое по уравнению двухсторонней нестационарной теплопередачи, т –число валков
В зависимости от толщины и кратности вытяжки скорость намотки пленки для жесткого ПВХ составляет приблизительно от 40 до 100 м/мин, а для
пластифиированного ПВХ — от 80 до 120 м/мин.
Слайд 32Состав комплектной каландровой линии
Состав комплектной каландровой линии
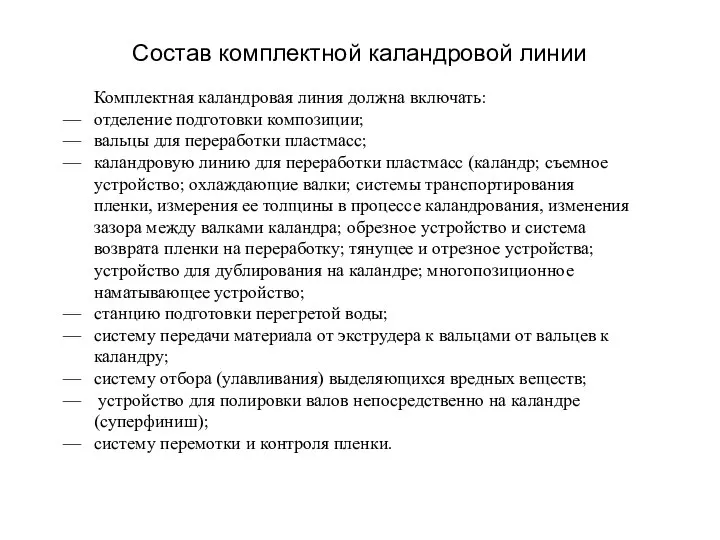
Слайд 33Режимы каландрования при изготовлении листов и пленок из композиций на основе различных
Режимы каландрования при изготовлении листов и пленок из композиций на основе различных
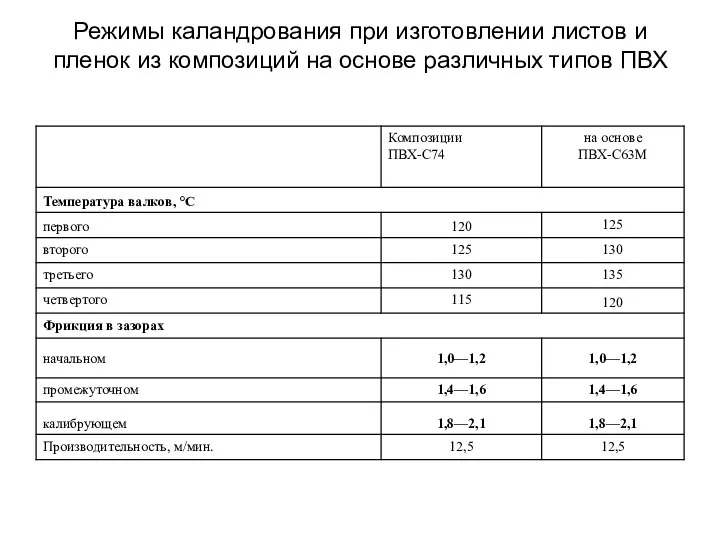
Слайд 34Параметры процесса каландрования
Пленка, полученная каландровым способом, обладает продольной ориентацией. Так, при переработке
Параметры процесса каландрования
Пленка, полученная каландровым способом, обладает продольной ориентацией. Так, при переработке
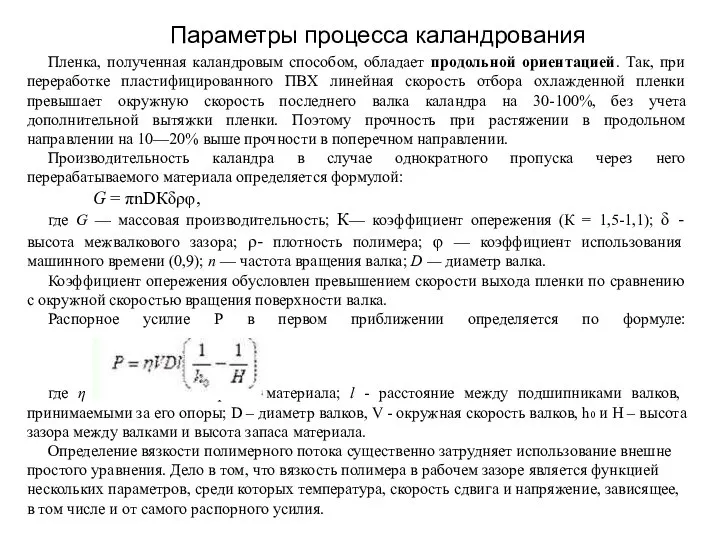
Производительность каландра в случае однократного пропуска через него перерабатываемого материала определяется формулой:
G = πnDКδρφ,
где G — массовая производительность; К— коэффициент опережения (К = 1,5-1,1); δ - высота межвалкового зазора; ρ- плотность полимера; φ — коэффициент использования машинного времени (0,9); п — частота вращения валка; D — диаметр валка.
Коэффициент опережения обусловлен превышением скорости выхода пленки по сравнению с окружной скоростью вращения поверхности валка.
Распорное усилие Р в первом приближении определяется по формуле:
где η -вязкость полимерного материала; l - расстояние между подшипниками валков, принимаемыми за его опоры; D – диаметр валков, V - окружная скорость валков, h0 и H – высота зазора между валками и высота запаса материала.
Определение вязкости полимерного потока существенно затрудняет использование внешне простого уравнения. Дело в том, что вязкость полимера в рабочем зазоре является функцией нескольких параметров, среди которых температура, скорость сдвига и напряжение, зависящее, в том числе и от самого распорного усилия.
Слайд 35Влияние параметров процесса каландрования
Влияние минимального зазора на потребляемую мощность N и производительность
Влияние параметров процесса каландрования
Влияние минимального зазора на потребляемую мощность N и производительность
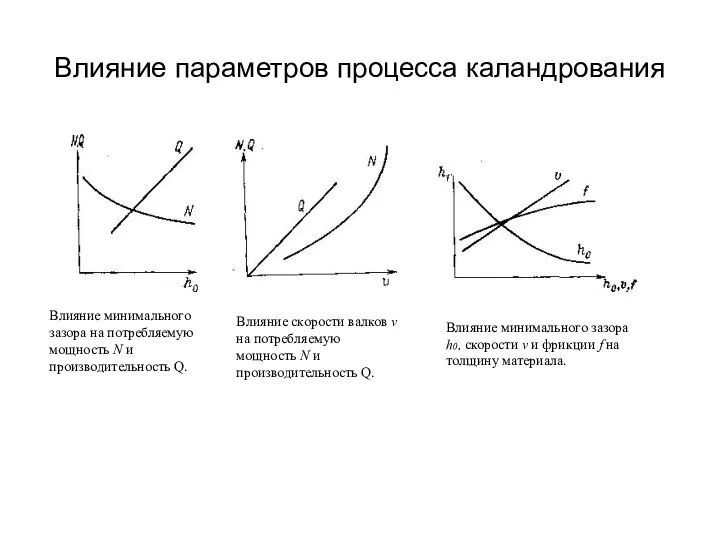
Влияние скорости валков v на потребляемую мощность N и производительность Q.
Влияние минимального зазора h0, скорости v и фрикции f на толщину материала.
Слайд 36Производительность четырехвалкового Г-образного
каландра при изготовлении пленки разной толщины
Производительность четырехвалкового Г-образного
каландра при изготовлении пленки разной толщины
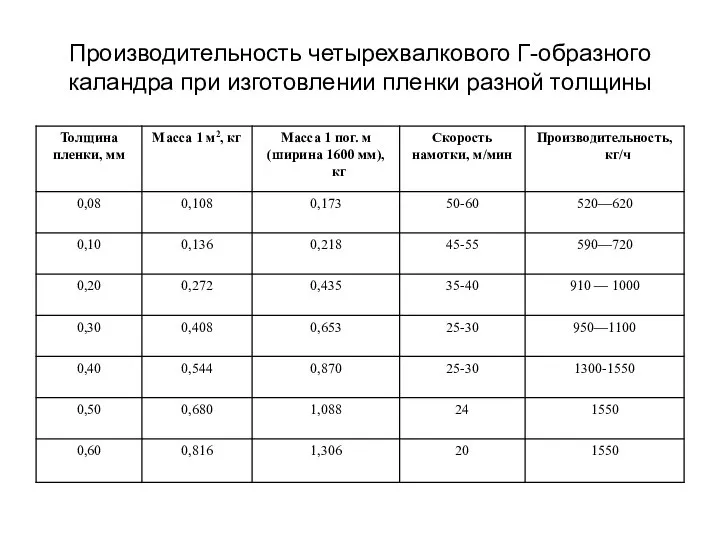
Слайд 37Виды брака при каландровании
Виды брака при каландровании
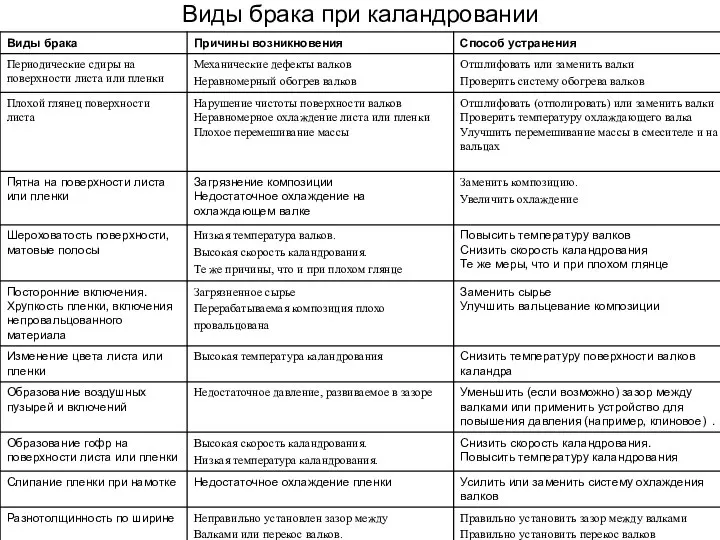
Слайд 38Использованная литература
Переработка пластмасс под ред. Брагинского В.А. Л., Химия, 1985 г.
2. Основы
Использованная литература
Переработка пластмасс под ред. Брагинского В.А. Л., Химия, 1985 г.
2. Основы
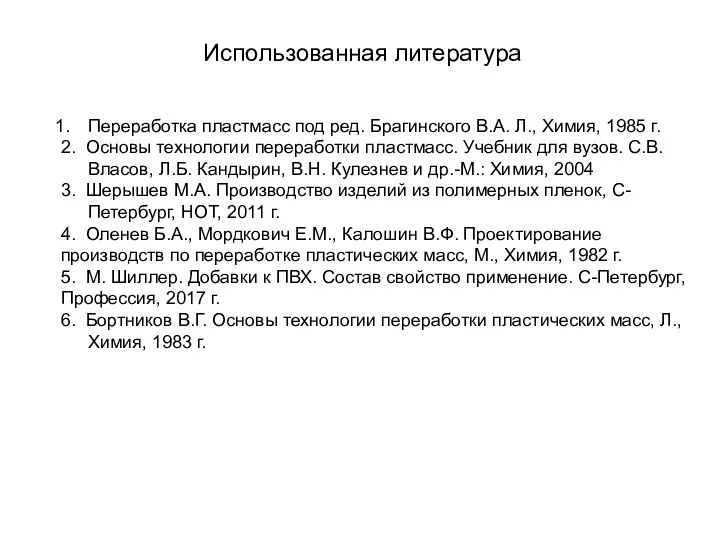
3. Шерышев М.А. Производство изделий из полимерных пленок, С-Петербург, НОТ, 2011 г.
4. Оленев Б.А., Мордкович Е.М., Калошин В.Ф. Проектирование
производств по переработке пластических масс, М., Химия, 1982 г.
5. М. Шиллер. Добавки к ПВХ. Состав свойство применение. С-Петербург,
Профессия, 2017 г.
6. Бортников В.Г. Основы технологии переработки пластических масс, Л., Химия, 1983 г.