Содержание
- 2. 1) Выбор расчетного режима определяется характером работы элемента конструкции. Расчет на прочность производится при наиболее невыгодном
- 3. 2) Выбор расчетной схемы проектируемого элемента конструкции: реальная конструкция представляется в виде некоторой идеализированной расчетной схемы
- 4. Второй метод: определяют «общие» максимальные напряжения σ в детали без учета концентраций напряжений и сравнивают их
- 5. Эквивалентные напряжения σэ в деталях при сложном напряженном состоянии (сочетание изгиба с кручением, кручения с растяжением-сжатием
- 6. Расчет на усталость Основными факторами, определяющими предел усталости, т. е. максимальную величину переменного напряжения, при котором
- 7. – Асимметричный цикл с неодинаковыми по величине наибольшими и наименьшими напряжениями, каждое из которых не равно
- 8. – коэффициенты концентрации напряжений полированного образца, выполненного из материала детали, имеющего форму детали, но отличный от
- 9. 5) Определяется величина предела усталости детали для тех же условий при асимметричном цикле нагружения (если имеет
- 10. Расчет на работоспособность по эквивалентной нагрузке: где Qo – постоянная (статическая) нагрузка детали; QΣ – максимальная
- 11. Свойства, способствующие быстрому внедрению пластмасс: малая удельная масса (1…2 г/см3), обеспечивающая значительное снижение веса конструкций; высокая
- 13. Скачать презентацию
Слайд 21) Выбор расчетного режима определяется характером работы элемента конструкции.
Расчет на прочность производится
1) Выбор расчетного режима определяется характером работы элемента конструкции.
Расчет на прочность производится
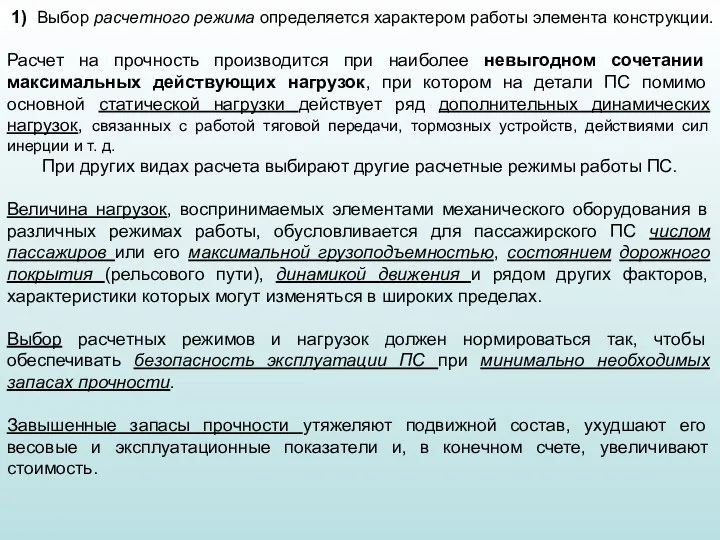
При других видах расчета выбирают другие расчетные режимы работы ПС.
Величина нагрузок, воспринимаемых элементами механического оборудования в различных режимах работы, обусловливается для пассажирского ПС числом пассажиров или его максимальной грузоподъемностью, состоянием дорожного покрытия (рельсового пути), динамикой движения и рядом других факторов, характеристики которых могут изменяться в широких пределах.
Выбор расчетных режимов и нагрузок должен нормироваться так, чтобы обеспечивать безопасность эксплуатации ПС при минимально необходимых запасах прочности.
Завышенные запасы прочности утяжеляют подвижной состав, ухудшают его весовые и эксплуатационные показатели и, в конечном счете, увеличивают стоимость.
Слайд 32) Выбор расчетной схемы проектируемого элемента конструкции:
реальная конструкция представляется в виде
2) Выбор расчетной схемы проектируемого элемента конструкции:
реальная конструкция представляется в виде
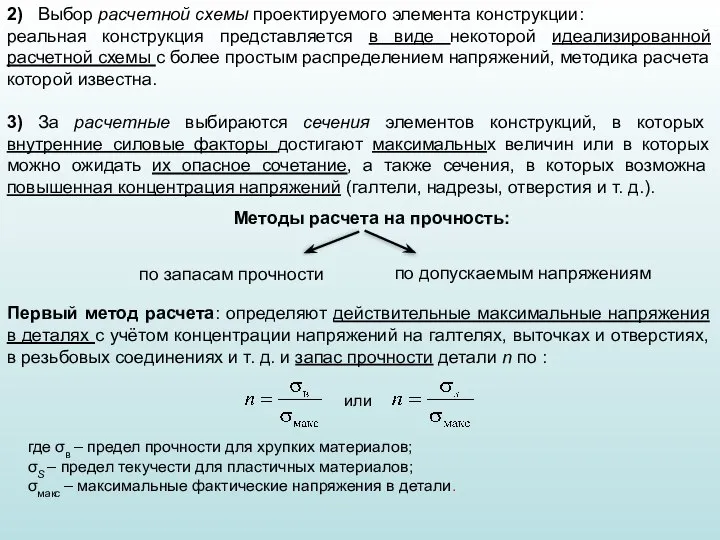
3) За расчетные выбираются сечения элементов конструкций, в которых внутренние силовые факторы достигают максимальных величин или в которых можно ожидать их опасное сочетание, а также сечения, в которых возможна повышенная концентрация напряжений (галтели, надрезы, отверстия и т. д.).
Методы расчета на прочность:
по запасам прочности
по допускаемым напряжениям
Первый метод расчета: определяют действительные максимальные напряжения в деталях с учётом концентрации напряжений на галтелях, выточках и отверстиях, в резьбовых соединениях и т. д. и запас прочности детали n по :
или
где σв – предел прочности для хрупких материалов;
σS – предел текучести для пластичных материалов;
σмакс – максимальные фактические напряжения в детали.
Слайд 4Второй метод: определяют «общие» максимальные напряжения σ в детали без учета концентраций
Второй метод: определяют «общие» максимальные напряжения σ в детали без учета концентраций
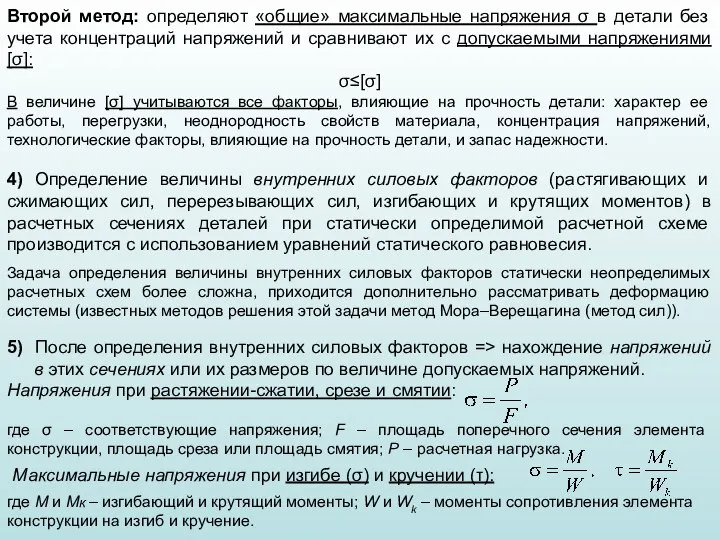
σ≤[σ]
В величине [σ] учитываются все факторы, влияющие на прочность детали: характер ее работы, перегрузки, неоднородность свойств материала, концентрация напряжений, технологические факторы, влияющие на прочность детали, и запас надежности.
4) Определение величины внутренних силовых факторов (растягивающих и сжимающих сил, перерезывающих сил, изгибающих и крутящих моментов) в расчетных сечениях деталей при статически определимой расчетной схеме производится с использованием уравнений статического равновесия.
Задача определения величины внутренних силовых факторов статически неопределимых расчетных схем более сложна, приходится дополнительно рассматривать деформацию системы (известных методов решения этой задачи метод Мора–Верещагина (метод сил)).
5) После определения внутренних силовых факторов => нахождение напряжений в этих сечениях или их размеров по величине допускаемых напряжений.
Напряжения при растяжении-сжатии, срезе и смятии:
где σ – соответствующие напряжения; F – площадь поперечного сечения элемента конструкции, площадь среза или площадь смятия; Р – расчетная нагрузка.
Максимальные напряжения при изгибе (σ) и кручении (τ):
где М и Мк – изгибающий и крутящий моменты; W и Wk – моменты сопротивления элемента конструкции на изгиб и кручение.
Слайд 5Эквивалентные напряжения σэ в деталях при сложном напряженном состоянии (сочетание изгиба с
Эквивалентные напряжения σэ в деталях при сложном напряженном состоянии (сочетание изгиба с
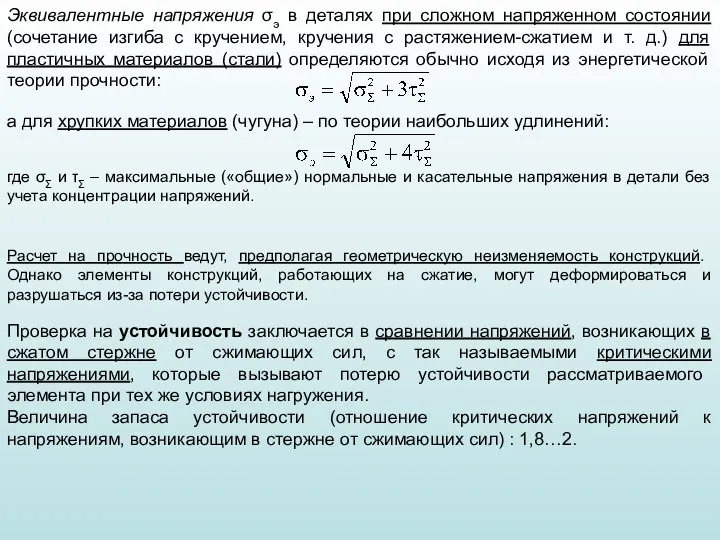
где σΣ и τΣ – максимальные («общие») нормальные и касательные напряжения в детали без учета концентрации напряжений.
а для хрупких материалов (чугуна) – по теории наибольших удлинений:
Расчет на прочность ведут, предполагая геометрическую неизменяемость конструкций. Однако элементы конструкций, работающих на сжатие, могут деформироваться и разрушаться из-за потери устойчивости.
Проверка на устойчивость заключается в сравнении напряжений, возникающих в сжатом стержне от сжимающих сил, с так называемыми критическими напряжениями, которые вызывают потерю устойчивости рассматриваемого элемента при тех же условиях нагружения.
Величина запаса устойчивости (отношение критических напряжений к напряжениям, возникающим в стержне от сжимающих сил) : 1,8…2.
Слайд 6Расчет на усталость
Основными факторами, определяющими предел усталости, т. е. максимальную величину переменного
Расчет на усталость
Основными факторами, определяющими предел усталости, т. е. максимальную величину переменного
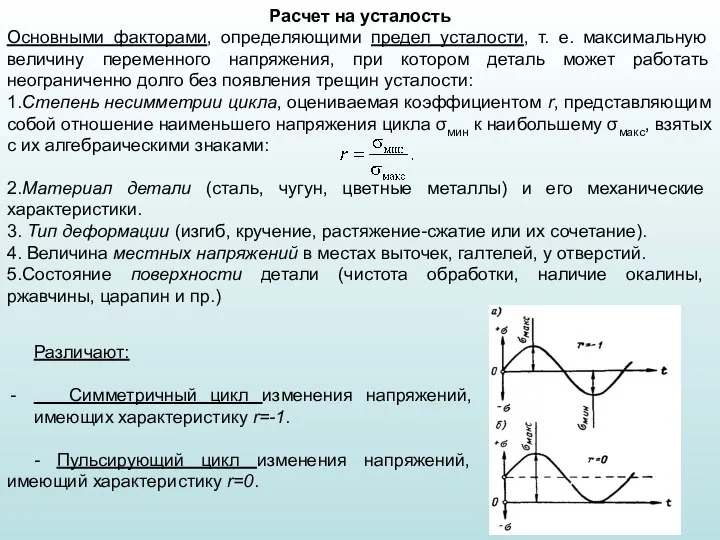
1.Степень несимметрии цикла, оцениваемая коэффициентом r, представляющим собой отношение наименьшего напряжения цикла σмин к наибольшему σмакс, взятых с их алгебраическими знаками:
2.Материал детали (сталь, чугун, цветные металлы) и его механические характеристики.
3. Тип деформации (изгиб, кручение, растяжение-сжатие или их сочетание).
4. Величина местных напряжений в местах выточек, галтелей, у отверстий.
5.Состояние поверхности детали (чистота обработки, наличие окалины, ржавчины, царапин и пр.)
Различают:
Симметричный цикл изменения напряжений, имеющих характеристику r=-1.
- Пульсирующий цикл изменения напряжений, имеющий характеристику r=0.
Слайд 7– Асимметричный цикл с неодинаковыми по величине наибольшими и наименьшими напряжениями, каждое из
– Асимметричный цикл с неодинаковыми по величине наибольшими и наименьшими напряжениями, каждое из
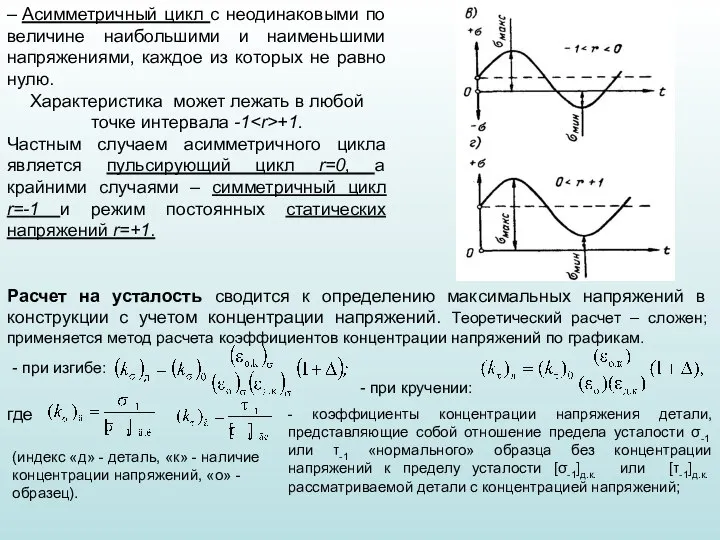
Характеристика может лежать в любой точке интервала -1
Частным случаем асимметричного цикла является пульсирующий цикл r=0, а крайними случаями – симметричный цикл r=-1 и режим постоянных статических напряжений r=+1.
Расчет на усталость сводится к определению максимальных напряжений в конструкции с учетом концентрации напряжений. Теоретический расчет – сложен; применяется метод расчета коэффициентов концентрации напряжений по графикам.
- при изгибе:
- при кручении:
- коэффициенты концентрации напряжения детали, представляющие собой отношение предела усталости σ-1 или τ-1 «нормального» образца без концентрации напряжений к пределу усталости [σ-1]д.к. или [τ-1]д.к. рассматриваемой детали с концентрацией напряжений;
где
(индекс «д» - деталь, «к» - наличие концентрации напряжений, «о» - образец).
Слайд 8
– коэффициенты концентрации напряжений полированного образца, выполненного из материала детали, имеющего
– коэффициенты концентрации напряжений полированного образца, выполненного из материала детали, имеющего
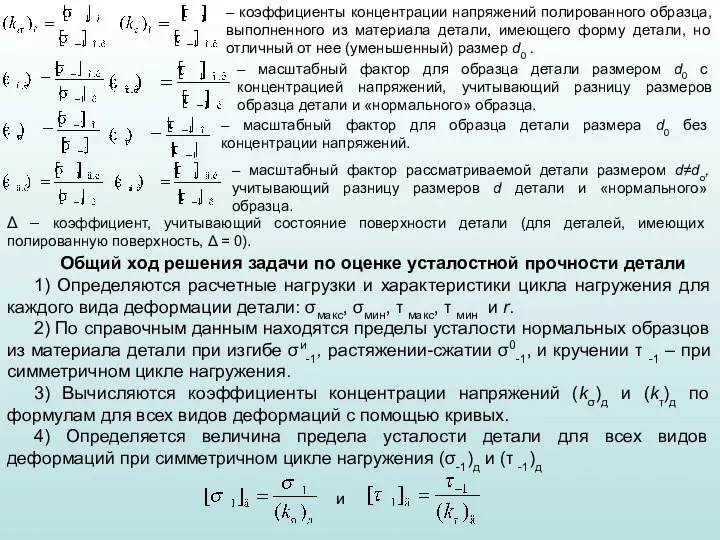
– масштабный фактор для образца детали размером d0 с концентрацией напряжений, учитывающий разницу размеров образца детали и «нормального» образца.
– масштабный фактор для образца детали размера d0 без концентрации напряжений.
– масштабный фактор рассматриваемой детали размером d≠dо, учитывающий разницу размеров d детали и «нормального» образца.
Δ – коэффициент, учитывающий состояние поверхности детали (для деталей, имеющих полированную поверхность, Δ = 0).
Общий ход решения задачи по оценке усталостной прочности детали
1) Определяются расчетные нагрузки и характеристики цикла нагружения для каждого вида деформации детали: σмакс, σмин, τ макс, τ мин и r.
2) По справочным данным находятся пределы усталости нормальных образцов из материала детали при изгибе σи-1, растяжении-сжатии σ0-1, и кручении τ -1 – при симметричном цикле нагружения.
3) Вычисляются коэффициенты концентрации напряжений (kσ)д и (kτ)д по формулам для всех видов деформаций с помощью кривых.
4) Определяется величина предела усталости детали для всех видов деформаций при симметричном цикле нагружения (σ-1)д и (τ -1)д
и
Слайд 95) Определяется величина предела усталости детали для тех же условий при асимметричном цикле
5) Определяется величина предела усталости детали для тех же условий при асимметричном цикле
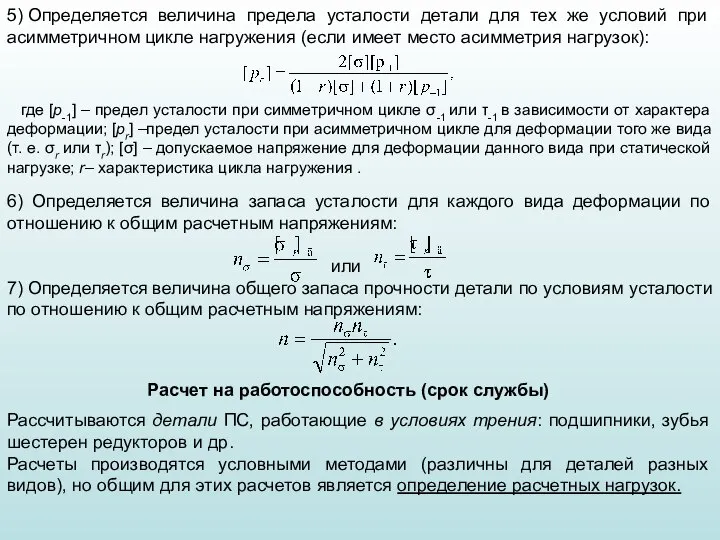
где [р-1] – предел усталости при симметричном цикле σ-1 или τ-1 в зависимости от характера деформации; [рr] –предел усталости при асимметричном цикле для деформации того же вида (т. е. σr или τr); [σ] – допускаемое напряжение для деформации данного вида при статической нагрузке; r– характеристика цикла нагружения .
6) Определяется величина запаса усталости для каждого вида деформации по отношению к общим расчетным напряжениям:
или
7) Определяется величина общего запаса прочности детали по условиям усталости по отношению к общим расчетным напряжениям:
.
Расчет на работоспособность (срок службы)
Рассчитываются детали ПС, работающие в условиях трения: подшипники, зубья шестерен редукторов и др.
Расчеты производятся условными методами (различны для деталей разных видов), но общим для этих расчетов является определение расчетных нагрузок.
Слайд 10Расчет на работоспособность по эквивалентной нагрузке:
где Qo – постоянная (статическая) нагрузка детали;
Расчет на работоспособность по эквивалентной нагрузке:
где Qo – постоянная (статическая) нагрузка детали;
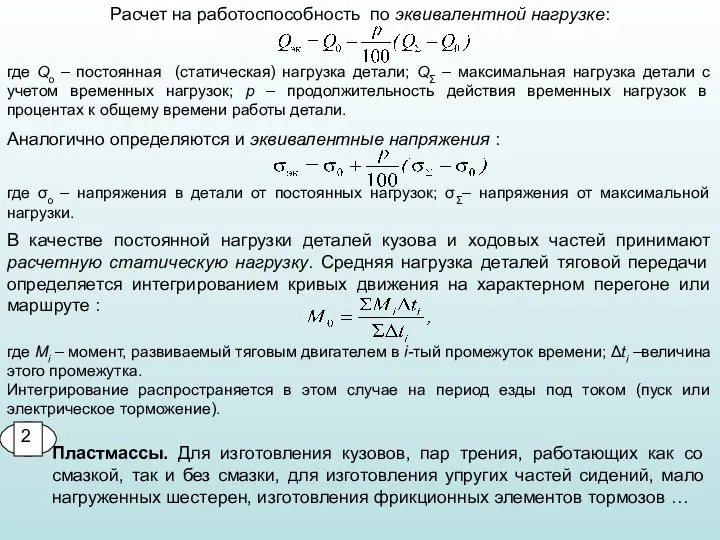
Аналогично определяются и эквивалентные напряжения :
где σо – напряжения в детали от постоянных нагрузок; σΣ– напряжения от максимальной нагрузки.
В качестве постоянной нагрузки деталей кузова и ходовых частей принимают расчетную статическую нагрузку. Средняя нагрузка деталей тяговой передачи определяется интегрированием кривых движения на характерном перегоне или маршруте :
где Mi – момент, развиваемый тяговым двигателем в i-тый промежуток времени; Δti –величина этого промежутка.
Интегрирование распространяется в этом случае на период езды под током (пуск или электрическое торможение).
Пластмассы. Для изготовления кузовов, пар трения, работающих как со смазкой, так и без смазки, для изготовления упругих частей сидений, мало нагруженных шестерен, изготовления фрикционных элементов тормозов …
Слайд 11Свойства, способствующие быстрому внедрению пластмасс:
малая удельная масса (1…2 г/см3), обеспечивающая значительное снижение
Свойства, способствующие быстрому внедрению пластмасс:
малая удельная масса (1…2 г/см3), обеспечивающая значительное снижение
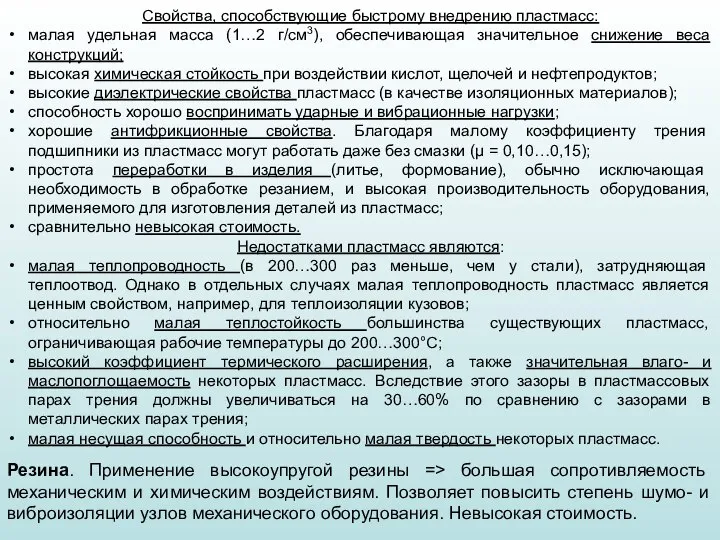
высокая химическая стойкость при воздействии кислот, щелочей и нефтепродуктов;
высокие диэлектрические свойства пластмасс (в качестве изоляционных материалов);
способность хорошо воспринимать ударные и вибрационные нагрузки;
хорошие антифрикционные свойства. Благодаря малому коэффициенту трения подшипники из пластмасс могут работать даже без смазки (μ = 0,10…0,15);
простота переработки в изделия (литье, формование), обычно исключающая необходимость в обработке резанием, и высокая производительность оборудования, применяемого для изготовления деталей из пластмасс;
сравнительно невысокая стоимость.
Недостатками пластмасс являются:
малая теплопроводность (в 200…300 раз меньше, чем у стали), затрудняющая теплоотвод. Однако в отдельных случаях малая теплопроводность пластмасс является ценным свойством, например, для теплоизоляции кузовов;
относительно малая теплостойкость большинства существующих пластмасс, ограничивающая рабочие температуры до 200…300°С;
высокий коэффициент термического расширения, а также значительная влаго- и маслопоглощаемость некоторых пластмасс. Вследствие этого зазоры в пластмассовых парах трения должны увеличиваться на 30…60% по сравнению с зазорами в металлических парах трения;
малая несущая способность и относительно малая твердость некоторых пластмасс.
Резина. Применение высокоупругой резины => большая сопротивляемость механическим и химическим воздействиям. Позволяет повысить степень шумо- и виброизоляции узлов механического оборудования. Невысокая стоимость.