Содержание
- 2. НАРЕЗАНИЕ И ОТДЕЛКА ЗУБЧАТЫХ КОЛЕС ОБЩИЕ СВЕДЕНИЯ Зубчатые колёса имеют весьма широкий спектр назначения и подразделяются
- 3. НАРЕЗАНИЕ ЗУБЧАТЫХ КОЛЕС МЕТОДОМ КОПИРОВАНИЯ Сущность метода копирования заключается в том, что профиль впадин между зубьями
- 4. Построение профилей фрез стандартных наборов по этой схеме закладывает погрешности нарезания колес, поэтому дисковыми модульными фрезами
- 5. НАРЕЗАНИЕ ЗУБЧАТЫХ КОЛЕС МНОГОРЕЗЦОВЫМИ ЗУБОДОЛБЕЖНЫМИ ГОЛОВКАМИ Одним из высокопроизводительных и точных методов нарезания зубчатых колес, базирующимся
- 6. НАРЕЗАНИЕ ЗУБЧАТЫХ КОЛЕС КРУГОВЫМИ ПРОТЯЖКАМИ По методу копирования работают также круговые протяжки, предназначенные для нарезания прямозубых
- 7. НАРЕЗАНИЕ ЗУБЧАТЫХ КОЛЕС МЕТОДОМ ОБКАТКИ При нарезании зубчатых колес методом обкатки воспроизводится имитация зацепления зубчатой передачи,
- 8. В процессе нарезании зубчатых колес фреза получает вращательное движение I вокруг своей оси, которое является главным,
- 9. Рис. 8. Нарезание зубчатого колеса на зубофрезерном обрабатывающем центре с ЧПУ HERA 350: а – установка
- 10. Скорость резания при зубофрезеровании зависит от стойкости режущего инструмента Т, модуля нарезаемого колеса m и вертикальной
- 11. Помимо цельных фрез в производстве используются также и сборные фрезы (рис. 10). Для изготовления червячных модульных
- 12. Рис. 11. Червячная модульная фреза: а – конструктивные элементы и геометрические параметры; б – профиль зуба
- 13. В то же время увеличение приводит к увеличению расхода инструментального материала, росту величины крутящего момента на
- 14. Поэтому с целью обеспечения заданной точности нарезаемых зубчатых колес теоретическую (расчетную) величину задают для сечения, отстоящего
- 15. а б Рис. 12. Процесс нарезания блока зубчатых колес (а) и вал-шестерни (б) на зубодолбежном станке
- 16. Главное движение или движения резания совершается при перемещении долбяка вниз, а холостой ход при движении его
- 17. а б в Рис. 14. Дисковые прямозубый (а) косозубый (б) и прямозубый чашечный (в) долбяки а
- 18. исключает возможность их контакта с упором, имеющего место, например, при изготовлении блока зубчатых колес. Хвостовые долбяки
- 19. У стандартных долбяков, предназначенных для нарезания зубчатых колес с углом профиля величины переднего и заднего углов
- 20. Период стойкости Т для долбяка выбирается в зависимости от значения модуля m. Для средних значений модуля
- 21. Рис. 2.9. Конструктивные параметры дискового шевера ЗУБООТДЕЛОЧНЫЕ ОПЕРАЦИИ ШЕВИНГОВАНИЕ Для повышения степени точности и снижения величины
- 22. Реечные шеверы (рис. 20, а) предназначены для обработки цилиндрических колес с прямыми и винтовыми зубьями. Они
- 23. а б Рис. 21. Общий вид (а) и конструктивные параметры дискового шевера (б) При шевинговании уменьшаются
- 24. Зубья шевера закалены до высокой твердости (63...66 HRCэ) и имеют на боковых поверхностях канавки, которые образуют
- 25. Рис. 23. Схема шевингования: а – с продольной подачей; б – с диагональной подачей; в –
- 26. Шевингование с диагональной подачей. Этот метод шевингования производится на станках, допускающих возможность поворота центровых бабок относительно
- 27. а б Рис. 24. Процессы шевингования: а – косозубого зубчатого колеса; б – много шестеренчатого вала
- 28. Рис. 25. Схема профильного зубошлифования [3] вдоль образующей зуба, а радиальная подача Sp производится периодически на
- 29. На рис. 26 приведены процессы профильного зубошлифования прямозубой и косозубой шестерен на станке с ЧПУ SMG
- 30. Развитию процесса профильного шлифования способствовало создание фирмой КАРР процесса зубошлифования на базе использования неправящихся шлифовальных кругов.
- 31. Станки для шлифования зубчатых колес профильными кругами выпускаются многими западными фирмами, такими, как КАРР, GLEASON-PFAUTER-HURTH, NILES
- 32. Рис. 30. Следы резов от шлифовальных кругов на боковых поверхностях зубьев [3]: а – при 15-градусном
- 33. Этому способствуют два обстоятельства. Во-первых, шлифование зубьев можно производить пористыми и сравнительно мягкими абразивными кругами, так
- 34. При шлифовании зубчатых колес коническим кругом существует два способа шлифования – раздельное и одновременное. При раздельном
- 35. Основным движением станка, определяющим точность обработки деталей, является согласованное движение (вращение) шлифовального круга и обрабатываемого колеса.
- 36. Получил распространение также станок TAG 400 CNC, являющийся совместной разработкой фирм GLEASON и OKAMOTO. По своим
- 37. КАЧЕСТВО ПОВЕРХНОСТНОГО СЛОЯ ПРИ ЗУБОШЛИФОВАНИИ ПОНЯТИЕ КАЧЕСТВА ПОВЕРХНОСТЕЙ ДЕТАЛЕЙ МАШИН Под качеством поверхности детали следует понимать
- 38. Отклонения формы а б в Рис. 37. Отклонение от круглости и ее частые виды: а –
- 39. Волнистость поверхности (РС 3951-73) Волнистость поверхности представляет собой совокупность периодически повторяющихся неровностей на поверхности детали Рис.
- 40. Механизм формирования шероховатости поверхности На формирование шероховатости поверхности в процессе обработки оказывают влияние геометрия режущего инструмента,
- 41. Физико-химические характеристики поверхностного слоя При резании поверхностный слой обрабатываемой детали деформируется и изменяются его физико-механические свойства:
- 42. а б Рисунок 46 – Зависимости степени наклепа и глубины наклепа от подачи (а) и скорости
- 43. Методы контроля микротвердости и остаточных напряжений Рис. 50. Автоматизированная установка для определения остаточных напряжений а б
- 44. Механизм формирования остаточных напряжений Рис. 52. Условная схема свободного резания малопластичных материалов Рис. 53. Условная схема
- 45. СТРУКТУРНЫЕ ИЗМЕНЕНИЯ В ПОВЕРХНОСТНОМ СЛОЕ ПРИ ШЛИФОВАНИИ Эффективно устраняя деформации и коробление, возникающее при химико-термической обработке
- 46. Прижоги закалки с отпуском (рис. 54, б) возникают при нагреве шлифуемой поверхности выше температуры фазовых превращений
- 47. ИЗМЕНЕНИЕ СВОЙСТВ ПОВЕРХНОСТНОГО СЛОЯ ЗУБЬЕВ ПРИ ШЛИФОВАНИИ С ПРИЖОГАМИ Появление шлифовочных прижогов сопровождается образованием неоднородной структуры
- 48. Рис. 58. Распределение остаточных напряжений по толщине l поверхностного слоя [3]: а – зубьев колес из
- 49. Влияние шлифовочных прижогов на выносливость зубьев при изгибе. Шлифовочные прижоги снижают сопротивление зубьев при изгибе. Из
- 50. Рис. 61. Кривые усталости зубчатых колес из стали 12Х2Н4А [3]: 1- с нешлифованной впадиной с выкружкой;
- 51. ПРОГРЕССИВНЫЕ АБРАЗИВНЫЕ ИНСТРУМЕНТЫ ДЛЯ ЗУБОШЛИФОВАНИЯ К прогрессивным абразивным инструментам, применяемым для процессов зубошлифования можно отнести высокоструктурные
- 52. Рис. 63. Прерывистые шлифовальные круги: а – цельный; б – составной (1 – корпус; 2 –
- 53. Рис. 65. Сборный композиционный круг для профильного зубошлифования Рис. 66. Схема работы абразивных зерен при прерывистом
- 54. А это приводит к перераспределению глубины резания между зернами, т.е. к коренному изменению схемы удаления припуска.
- 56. Скачать презентацию
Слайд 2НАРЕЗАНИЕ И ОТДЕЛКА ЗУБЧАТЫХ КОЛЕС
ОБЩИЕ СВЕДЕНИЯ
Зубчатые колёса имеют весьма широкий спектр
НАРЕЗАНИЕ И ОТДЕЛКА ЗУБЧАТЫХ КОЛЕС
ОБЩИЕ СВЕДЕНИЯ
Зубчатые колёса имеют весьма широкий спектр
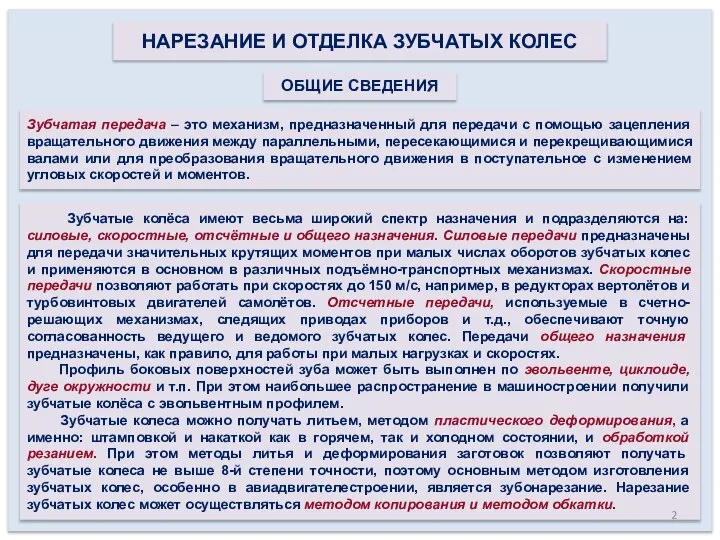
Профиль боковых поверхностей зуба может быть выполнен по эвольвенте, циклоиде, дуге окружности и т.п. При этом наибольшее распространение в машиностроении получили зубчатые колёса с эвольвентным профилем.
Зубчатые колеса можно получать литьем, методом пластического деформирования, а именно: штамповкой и накаткой как в горячем, так и холодном состоянии, и обработкой резанием. При этом методы литья и деформирования заготовок позволяют получать зубчатые колеса не выше 8-й степени точности, поэтому основным методом изготовления зубчатых колес, особенно в авиадвигателестроении, является зубонарезание. Нарезание зубчатых колес может осуществляться методом копирования и методом обкатки.
Зубчатая передача – это механизм, предназначенный для передачи с помощью зацепления вращательного движения между параллельными, пересекающимися и перекрещивающимися валами или для преобразования вращательного движения в поступательное с изменением угловых скоростей и моментов.
Слайд 3НАРЕЗАНИЕ ЗУБЧАТЫХ КОЛЕС МЕТОДОМ КОПИРОВАНИЯ
Сущность метода копирования заключается в том, что профиль
НАРЕЗАНИЕ ЗУБЧАТЫХ КОЛЕС МЕТОДОМ КОПИРОВАНИЯ
Сущность метода копирования заключается в том, что профиль
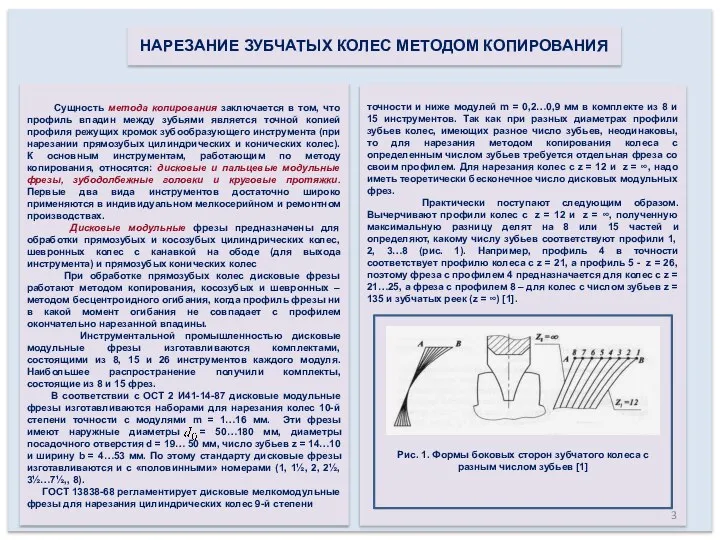
Дисковые модульные фрезы предназначены для обработки прямозубых и косозубых цилиндрических колес, шевронных колес с канавкой на ободе (для выхода инструмента) и прямозубых конических колес
При обработке прямозубых колес дисковые фрезы работают методом копирования, косозубых и шевронных – методом бесцентроидного огибания, когда профиль фрезы ни в какой момент огибания не совпадает с профилем окончательно нарезанной впадины.
Инструментальной промышленностью дисковые модульные фрезы изготавливаются комплектами, состоящими из 8, 15 и 26 инструментов каждого модуля. Наибольшее распространение получили комплекты, состоящие из 8 и 15 фрез.
В соответствии с ОСТ 2 И41-14-87 дисковые модульные фрезы изготавливаются наборами для нарезания колес 10-й степени точности с модулями m = 1…16 мм. Эти фрезы имеют наружные диаметры = 50…180 мм, диаметры посадочного отверстия d = 19… 50 мм, число зубьев z = 14…10 и ширину b = 4…53 мм. По этому стандарту дисковые фрезы изготавливаются и с «половинными» номерами (1, 1½, 2, 2½, 3½…7½,, 8).
ГОСТ 13838-68 регламентирует дисковые мелкомодульные фрезы для нарезания цилиндрических колес 9-й степени
точности и ниже модулей m = 0,2…0,9 мм в комплекте из 8 и 15 инструментов. Так как при разных диаметрах профили зубьев колес, имеющих разное число зубьев, неодинаковы, то для нарезания методом копирования колеса с определенным числом зубьев требуется отдельная фреза со своим профилем. Для нарезания колес с z = 12 и z = ∞, надо иметь теоретически бесконечное число дисковых модульных фрез.
Практически поступают следующим образом. Вычерчивают профили колес с z = 12 и z = ∞, полученную максимальную разницу делят на 8 или 15 частей и определяют, какому числу зубьев соответствуют профили 1, 2, 3…8 (рис. 1). Например, профиль 4 в точности соответствует профилю колеса с z = 21, а профиль 5 - z = 26, поэтому фреза с профилем 4 предназначается для колес с z = 21…25, а фреза с профилем 8 – для колес с числом зубьев z = 135 и зубчатых реек (z = ∞) [1].
Рис. 1. Формы боковых сторон зубчатого колеса с разным числом зубьев [1]
Слайд 4 Построение профилей фрез стандартных наборов по этой схеме закладывает погрешности нарезания
Построение профилей фрез стандартных наборов по этой схеме закладывает погрешности нарезания
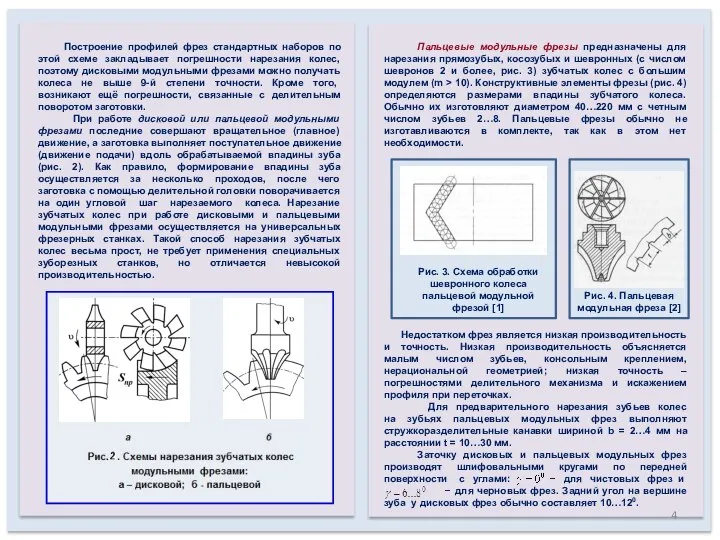
При работе дисковой или пальцевой модульными фрезами последние совершают вращательное (главное) движение, а заготовка выполняет поступательное движение (движение подачи) вдоль обрабатываемой впадины зуба (рис. 2). Как правило, формирование впадины зуба осуществляется за несколько проходов, после чего заготовка с помощью делительной головки поворачивается на один угловой шаг нарезаемого колеса. Нарезание зубчатых колес при работе дисковыми и пальцевыми модульными фрезами осуществляется на универсальных фрезерных станках. Такой способ нарезания зубчатых колес весьма прост, не требует применения специальных зуборезных станков, но отличается невысокой производительностью.
Пальцевые модульные фрезы предназначены для нарезания прямозубых, косозубых и шевронных (с числом шевронов 2 и более, рис. 3) зубчатых колес с большим модулем (m > 10). Конструктивные элементы фрезы (рис. 4) определяются размерами впадины зубчатого колеса. Обычно их изготовляют диаметром 40…220 мм с четным числом зубьев 2…8. Пальцевые фрезы обычно не изготавливаются в комплекте, так как в этом нет необходимости.
Недостатком фрез является низкая производительность и точность. Низкая производительность объясняется малым числом зубьев, консольным креплением, нерациональной геометрией; низкая точность – погрешностями делительного механизма и искажением профиля при переточках.
Для предварительного нарезания зубьев колес на зубьях пальцевых модульных фрез выполняют стружкоразделительные канавки шириной b = 2…4 мм на расстоянии t = 10…30 мм.
Заточку дисковых и пальцевых модульных фрез производят шлифовальными кругами по передней поверхности с углами: − для чистовых фрез и
− для черновых фрез. Задний угол на вершине зуба у дисковых фрез обычно составляет 10…120.
Рис. 3. Схема обработки шевронного колеса пальцевой модульной фрезой [1]
Рис. 4. Пальцевая модульная фреза [2]
Слайд 5
НАРЕЗАНИЕ ЗУБЧАТЫХ КОЛЕС МНОГОРЕЗЦОВЫМИ ЗУБОДОЛБЕЖНЫМИ ГОЛОВКАМИ
Одним из высокопроизводительных и точных
НАРЕЗАНИЕ ЗУБЧАТЫХ КОЛЕС МНОГОРЕЗЦОВЫМИ ЗУБОДОЛБЕЖНЫМИ ГОЛОВКАМИ
Одним из высокопроизводительных и точных
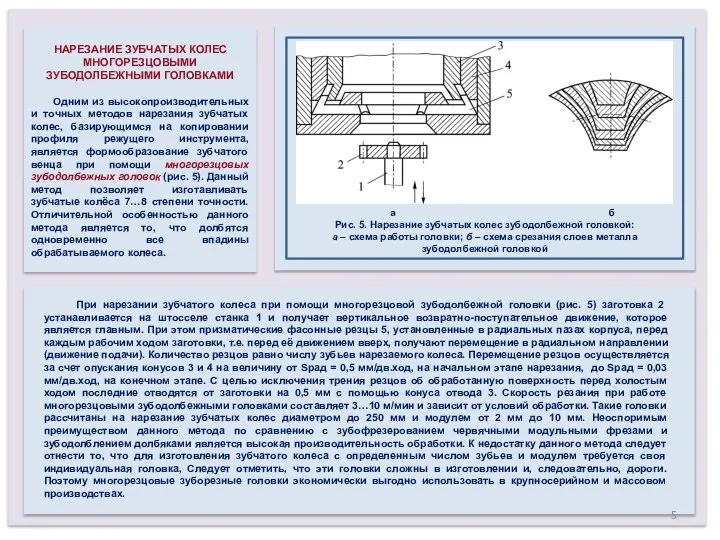
При нарезании зубчатого колеса при помощи многорезцовой зубодолбежной головки (рис. 5) заготовка 2 устанавливается на штосселе станка 1 и получает вертикальное возвратно-поступательное движение, которое является главным. При этом призматические фасонные резцы 5, установленные в радиальных пазах корпуса, перед каждым рабочим ходом заготовки, т.е. перед её движением вверх, получают перемещение в радиальном направлении (движение подачи). Количество резцов равно числу зубьев нарезаемого колеса. Перемещение резцов осуществляется за счет опускания конусов 3 и 4 на величину от Sрад = 0,5 мм/дв.ход, на начальном этапе нарезания, до Sрад = 0,03 мм/дв.ход, на конечном этапе. С целью исключения трения резцов об обработанную поверхность перед холостым ходом последние отводятся от заготовки на 0,5 мм с помощью конуса отвода 3. Скорость резания при работе многорезцовыми зубодолбежными головками составляет 3…10 м/мин и зависит от условий обработки. Такие головки рассчитаны на нарезание зубчатых колес диаметром до 250 мм и модулем от 2 мм до 10 мм. Неоспоримым преимуществом данного метода по сравнению с зубофрезерованием червячными модульными фрезами и зубодолблением долбяками является высокая производительность обработки. К недостатку данного метода следует отнести то, что для изготовления зубчатого колеса с определенным числом зубьев и модулем требуется своя индивидуальная головка, Следует отметить, что эти головки сложны в изготовлении и, следовательно, дороги. Поэтому многорезцовые зуборезные головки экономически выгодно использовать в крупносерийном и массовом производствах.
а б
Рис. 5. Нарезание зубчатых колес зубодолбежной головкой:
а – схема работы головки; б – схема срезания слоев металла зубодолбежной головкой
Слайд 6НАРЕЗАНИЕ ЗУБЧАТЫХ КОЛЕС КРУГОВЫМИ ПРОТЯЖКАМИ
По методу копирования работают также круговые протяжки,
НАРЕЗАНИЕ ЗУБЧАТЫХ КОЛЕС КРУГОВЫМИ ПРОТЯЖКАМИ
По методу копирования работают также круговые протяжки,
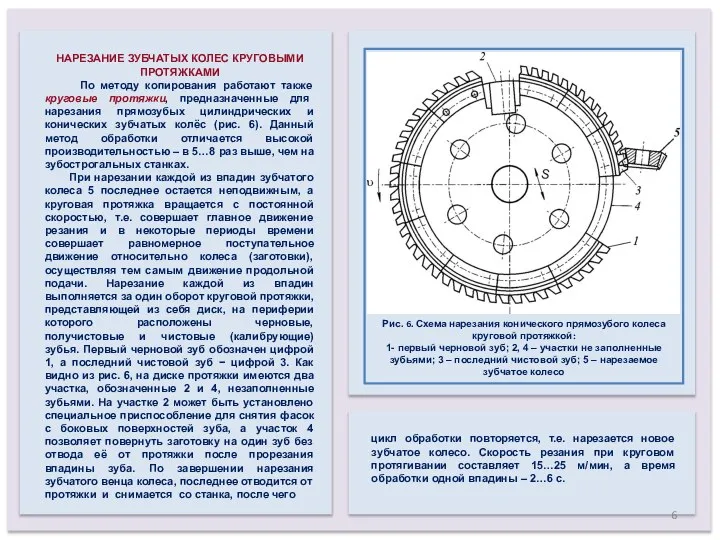
При нарезании каждой из впадин зубчатого колеса 5 последнее остается неподвижным, а круговая протяжка вращается с постоянной скоростью, т.е. совершает главное движение резания и в некоторые периоды времени совершает равномерное поступательное движение относительно колеса (заготовки), осуществляя тем самым движение продольной подачи. Нарезание каждой из впадин выполняется за один оборот круговой протяжки, представляющей из себя диск, на периферии которого расположены черновые, получистовые и чистовые (калибрующие) зубья. Первый черновой зуб обозначен цифрой 1, а последний чистовой зуб − цифрой 3. Как видно из рис. 6, на диске протяжки имеются два участка, обозначенные 2 и 4, незаполненные зубьями. На участке 2 может быть установлено специальное приспособление для снятия фасок с боковых поверхностей зуба, а участок 4 позволяет повернуть заготовку на один зуб без отвода её от протяжки после прорезания впадины зуба. По завершении нарезания зубчатого венца колеса, последнее отводится от протяжки и снимается со станка, после чего
цикл обработки повторяется, т.е. нарезается новое зубчатое колесо. Скорость резания при круговом протягивании составляет 15…25 м/мин, а время обработки одной впадины – 2…6 с.
Рис. 6. Схема нарезания конического прямозубого колеса
круговой протяжкой:
1- первый черновой зуб; 2, 4 – участки не заполненные зубьями; 3 – последний чистовой зуб; 5 – нарезаемое зубчатое колесо
Слайд 7НАРЕЗАНИЕ ЗУБЧАТЫХ КОЛЕС МЕТОДОМ ОБКАТКИ
При нарезании зубчатых колес методом обкатки воспроизводится
НАРЕЗАНИЕ ЗУБЧАТЫХ КОЛЕС МЕТОДОМ ОБКАТКИ
При нарезании зубчатых колес методом обкатки воспроизводится
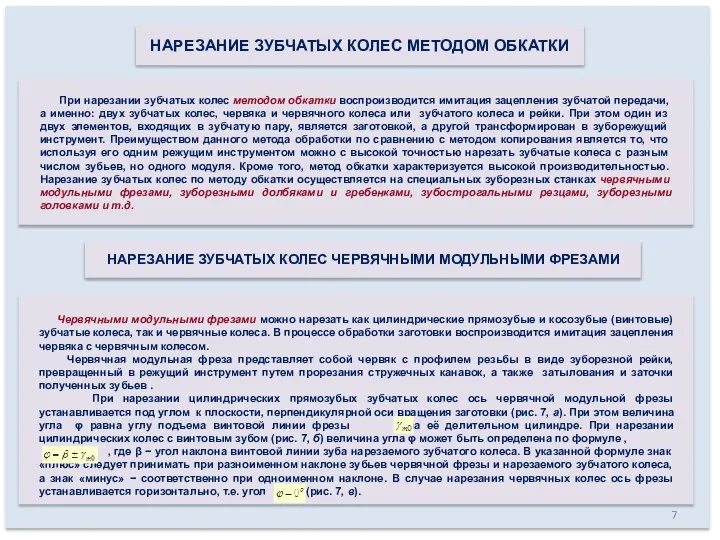
НАРЕЗАНИЕ ЗУБЧАТЫХ КОЛЕС ЧЕРВЯЧНЫМИ МОДУЛЬНЫМИ ФРЕЗАМИ
Червячными модульными фрезами можно нарезать как цилиндрические прямозубые и косозубые (винтовые) зубчатые колеса, так и червячные колеса. В процессе обработки заготовки воспроизводится имитация зацепления червяка с червячным колесом.
Червячная модульная фреза представляет собой червяк с профилем резьбы в виде зуборезной рейки, превращенный в режущий инструмент путем прорезания стружечных канавок, а также затылования и заточки полученных зубьев .
При нарезании цилиндрических прямозубых зубчатых колес ось червячной модульной фрезы устанавливается под углом к плоскости, перпендикулярной оси вращения заготовки (рис. 7, а). При этом величина угла φ равна углу подъема винтовой линии фрезы на её делительном цилиндре. При нарезании цилиндрических колес с винтовым зубом (рис. 7, б) величина угла φ может быть определена по формуле ,
, где β − угол наклона винтовой линии зуба нарезаемого зубчатого колеса. В указанной формуле знак «плюс» следует принимать при разноименном наклоне зубьев червячной фрезы и нарезаемого зубчатого колеса, а знак «минус» − соответственно при одноименном наклоне. В случае нарезания червячных колес ось фрезы устанавливается горизонтально, т.е. угол (рис. 7, в).
Слайд 8 В процессе нарезании зубчатых колес фреза получает вращательное движение I вокруг
В процессе нарезании зубчатых колес фреза получает вращательное движение I вокруг
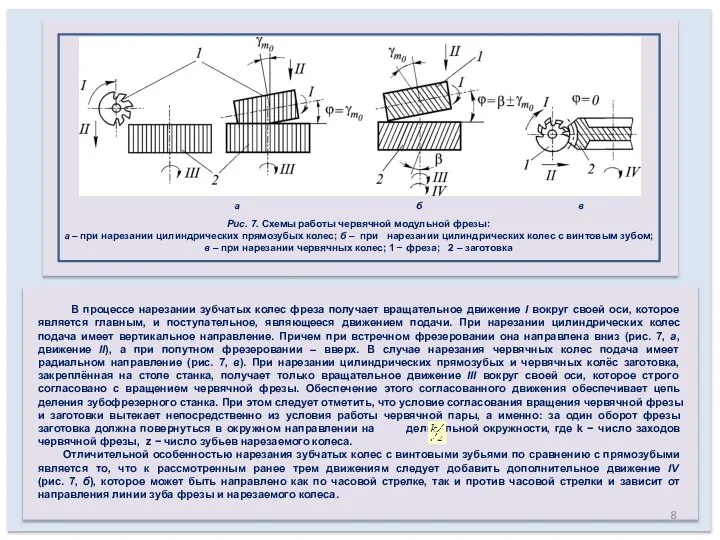
Отличительной особенностью нарезания зубчатых колес с винтовыми зубьями по сравнению с прямозубыми является то, что к рассмотренным ранее трем движениям следует добавить дополнительное движение IV (рис. 7, б), которое может быть направлено как по часовой стрелке, так и против часовой стрелки и зависит от направления линии зуба фрезы и нарезаемого колеса.
а б в
Рис. 7. Схемы работы червячной модульной фрезы:
а – при нарезании цилиндрических прямозубых колес; б – при нарезании цилиндрических колес с винтовым зубом; в – при нарезании червячных колес; 1 − фреза; 2 – заготовка
Слайд 9Рис. 8. Нарезание зубчатого колеса
на зубофрезерном обрабатывающем центре
с ЧПУ HERA
Рис. 8. Нарезание зубчатого колеса
на зубофрезерном обрабатывающем центре
с ЧПУ HERA

а – установка заготовки; б – процесс обработки
а
б
Слайд 10 Скорость резания при зубофрезеровании зависит от стойкости режущего инструмента Т, модуля
Скорость резания при зубофрезеровании зависит от стойкости режущего инструмента Т, модуля
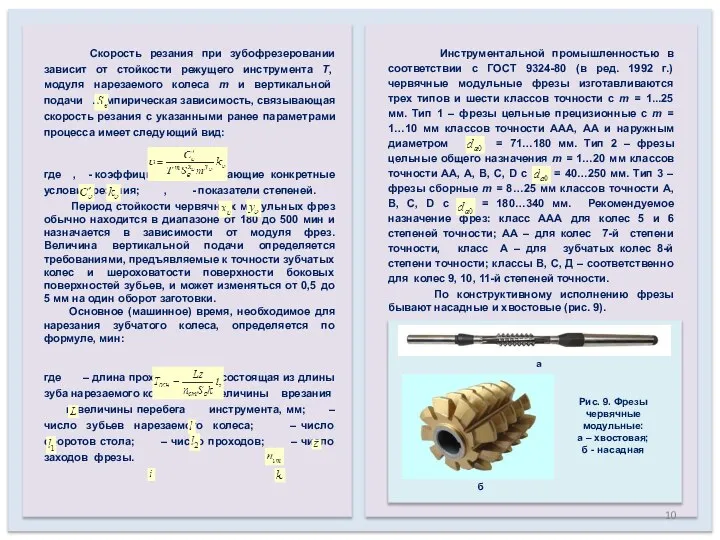
где , - коэффициенты, учитывающие конкретные условия резания; , - показатели степеней.
Период стойкости червячных модульных фрез обычно находится в диапазоне от 180 до 500 мин и назначается в зависимости от модуля фрез. Величина вертикальной подачи определяется требованиями, предъявляемые к точности зубчатых колес и шероховатости поверхности боковых поверхностей зубьев, и может изменяться от 0,5 до 5 мм на один оборот заготовки.
Основное (машинное) время, необходимое для нарезания зубчатого колеса, определяется по формуле, мин:
где – длина прохода фрезы, состоящая из длины зуба нарезаемого колеса , величины врезания
и величины перебега инструмента, мм; – число зубьев нарезаемого колеса; – число оборотов стола; – число проходов; – число заходов фрезы.
Инструментальной промышленностью в соответствии с ГОСТ 9324-80 (в ред. 1992 г.) червячные модульные фрезы изготавливаются трех типов и шести классов точности c m = 1...25 мм. Тип 1 – фрезы цельные прецизионные с m = 1…10 мм классов точности ААА, АА и наружным диаметром = 71…180 мм. Тип 2 – фрезы цельные общего назначения m = 1…20 мм классов точности АА, А, В, С, D с = 40…250 мм. Тип 3 – фрезы сборные m = 8…25 мм классов точности А, В, С, D с = 180…340 мм. Рекомендуемое назначение фрез: класс ААА для колес 5 и 6 степеней точности; АА – для колес 7-й степени точности, класс А – для зубчатых колес 8-й степени точности; классы В, С, Д – соответственно для колес 9, 10, 11-й степеней точности.
По конструктивному исполнению фрезы бывают насадные и хвостовые (рис. 9).
а
б
Рис. 9. Фрезы червячные модульные:
а – хвостовая;
б - насадная
Слайд 11 Помимо цельных фрез в производстве используются также и сборные фрезы (рис.
Помимо цельных фрез в производстве используются также и сборные фрезы (рис.
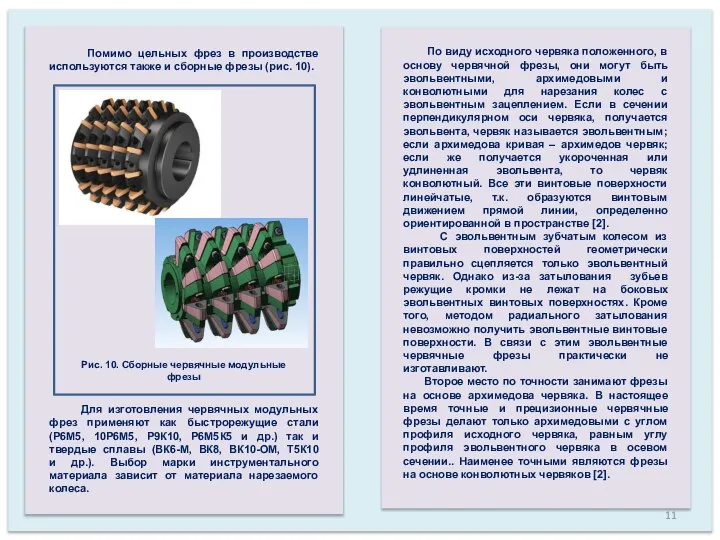
Для изготовления червячных модульных фрез применяют как быстрорежущие стали (Р6М5, 10Р6М5, Р9К10, Р6М5К5 и др.) так и твердые сплавы (ВК6-М, ВК8, ВК10-ОМ, Т5К10 и др.). Выбор марки инструментального материала зависит от материала нарезаемого колеса.
По виду исходного червяка положенного, в основу червячной фрезы, они могут быть эвольвентными, архимедовыми и конволютными для нарезания колес с эвольвентным зацеплением. Если в сечении перпендикулярном оси червяка, получается эвольвента, червяк называется эвольвентным; если архимедова кривая – архимедов червяк; если же получается укороченная или удлиненная эвольвента, то червяк конволютный. Все эти винтовые поверхности линейчатые, т.к. образуются винтовым движением прямой линии, определенно ориентированной в пространстве [2].
С эвольвентным зубчатым колесом из винтовых поверхностей геометрически правильно сцепляется только эвольвентный червяк. Однако из-за затылования зубьев режущие кромки не лежат на боковых эвольвентных винтовых поверхностях. Кроме того, методом радиального затылования невозможно получить эвольвентные винтовые поверхности. В связи с этим эвольвентные червячные фрезы практически не изготавливают.
Второе место по точности занимают фрезы на основе архимедова червяка. В настоящее время точные и прецизионные червячные фрезы делают только архимедовыми с углом профиля исходного червяка, равным углу профиля эвольвентного червяка в осевом сечении.. Наименее точными являются фрезы на основе конволютных червяков [2].
Рис. 10. Сборные червячные модульные фрезы
Слайд 12Рис. 11. Червячная модульная фреза:
а – конструктивные элементы и геометрические параметры; б
Рис. 11. Червячная модульная фреза:
а – конструктивные элементы и геометрические параметры; б
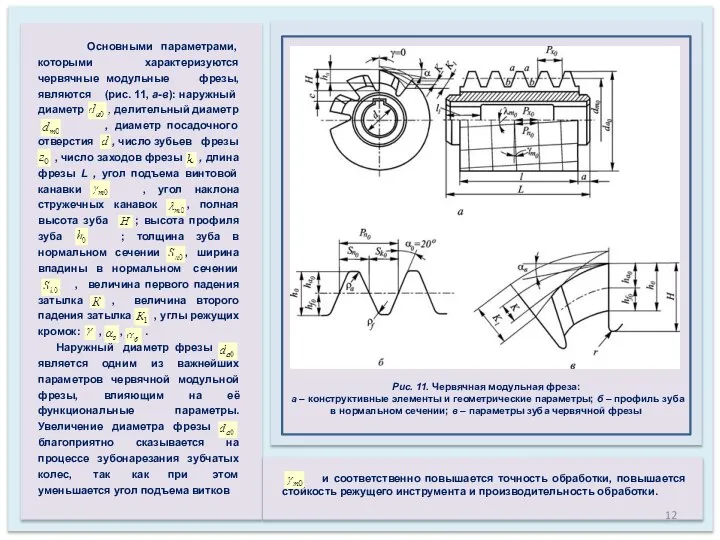
Основными параметрами, которыми характеризуются червячные модульные фрезы, являются (рис. 11, а-в): наружный диаметр , делительный диаметр
, диаметр посадочного отверстия , число зубьев фрезы
, число заходов фрезы , длина фрезы L , угол подъема винтовой канавки , угол наклона стружечных канавок , полная высота зуба ; высота профиля зуба ; толщина зуба в нормальном сечении , ширина впадины в нормальном сечении
, величина первого падения затылка , величина второго падения затылка , углы режущих кромок: , , .
Наружный диаметр фрезы
является одним из важнейших параметров червячной модульной фрезы, влияющим на её функциональные параметры. Увеличение диаметра фрезы
благоприятно сказывается на процессе зубонарезания зубчатых колес, так как при этом уменьшается угол подъема витков
и соответственно повышается точность обработки, повышается стойкость режущего инструмента и производительность обработки.
Слайд 13 В то же время увеличение приводит к увеличению расхода инструментального материала,
В то же время увеличение приводит к увеличению расхода инструментального материала,
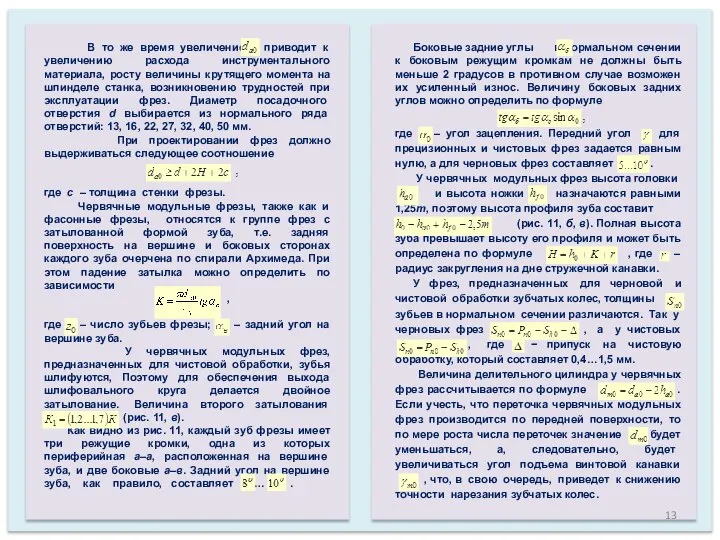
При проектировании фрез должно выдерживаться следующее соотношение
где с – толщина стенки фрезы.
Червячные модульные фрезы, также как и фасонные фрезы, относятся к группе фрез с затылованной формой зуба, т.е. задняя поверхность на вершине и боковых сторонах каждого зуба очерчена по спирали Архимеда. При этом падение затылка можно определить по зависимости
,
где – число зубьев фрезы; – задний угол на вершине зуба.
У червячных модульных фрез, предназначенных для чистовой обработки, зубья шлифуются, Поэтому для обеспечения выхода шлифовального круга делается двойное затылование. Величина второго затылования
(рис. 11, в).
Как видно из рис. 11, каждый зуб фрезы имеет три режущие кромки, одна из которых периферийная а–а, расположенная на вершине зуба, и две боковые а–в. Задний угол на вершине зуба, как правило, составляет … .
Боковые задние углы в нормальном сечении к боковым режущим кромкам не должны быть меньше 2 градусов в противном случае возможен их усиленный износ. Величину боковых задних углов можно определить по формуле
где – угол зацепления. Передний угол для прецизионных и чистовых фрез задается равным нулю, а для черновых фрез составляет .
У червячных модульных фрез высота головки
и высота ножки назначаются равными 1,25m, поэтому высота профиля зуба составит
(рис. 11, б, в). Полная высота зуба превышает высоту его профиля и может быть определена по формуле , где ‒ радиус закругления на дне стружечной канавки.
У фрез, предназначенных для черновой и чистовой обработки зубчатых колес, толщины зубьев в нормальном сечении различаются. Так у черновых фрез , а у чистовых
, где − припуск на чистовую
обработку, который составляет 0,4…1,5 мм.
Величина делительного цилиндра у червячных фрез рассчитывается по формуле . Если учесть, что переточка червячных модульных фрез производится по передней поверхности, то по мере роста числа переточек значение будет уменьшаться, а, следовательно, будет увеличиваться угол подъема винтовой канавки
, что, в свою очередь, приведет к снижению точности нарезания зубчатых колес.
Слайд 14
Поэтому с целью обеспечения заданной точности нарезаемых зубчатых колес теоретическую
Поэтому с целью обеспечения заданной точности нарезаемых зубчатых колес теоретическую
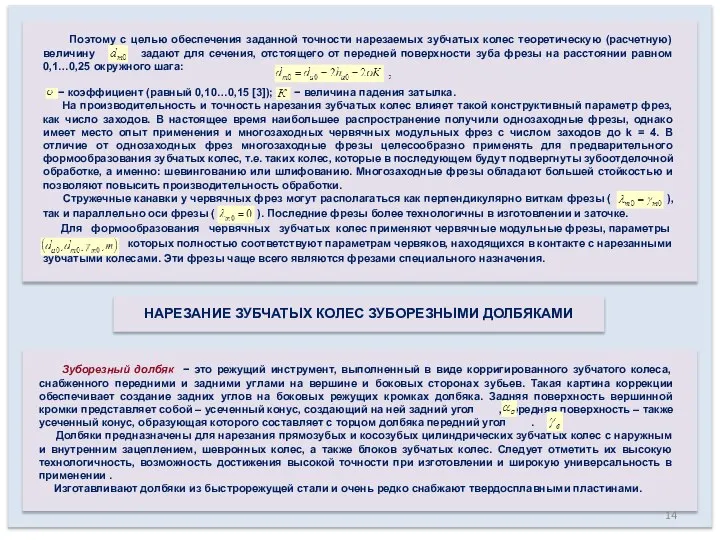
− коэффициент (равный 0,10…0,15 [3]); − величина падения затылка.
На производительность и точность нарезания зубчатых колес влияет такой конструктивный параметр фрез, как число заходов. В настоящее время наибольшее распространение получили однозаходные фрезы, однако имеет место опыт применения и многозаходных червячных модульных фрез с числом заходов до k = 4. В отличие от однозаходных фрез многозаходные фрезы целесообразно применять для предварительного формообразования зубчатых колес, т.е. таких колес, которые в последующем будут подвергнуты зубоотделочной обработке, а именно: шевингованию или шлифованию. Многозаходные фрезы обладают большей стойкостью и позволяют повысить производительность обработки.
Стружечные канавки у червячных фрез могут располагаться как перпендикулярно виткам фрезы ( ), так и параллельно оси фрезы ( ). Последние фрезы более технологичны в изготовлении и заточке.
Для формообразования червячных зубчатых колес применяют червячные модульные фрезы, параметры
которых полностью соответствуют параметрам червяков, находящихся в контакте с нарезанными зубчатыми колесами. Эти фрезы чаще всего являются фрезами специального назначения.
НАРЕЗАНИЕ ЗУБЧАТЫХ КОЛЕС ЗУБОРЕЗНЫМИ ДОЛБЯКАМИ
Зуборезный долбяк − это режущий инструмент, выполненный в виде корригированного зубчатого колеса, снабженного передними и задними углами на вершине и боковых сторонах зубьев. Такая картина коррекции обеспечивает создание задних углов на боковых режущих кромках долбяка. Задняя поверхность вершинной кромки представляет собой – усеченный конус, создающий на ней задний угол , передняя поверхность – также усеченный конус, образующая которого составляет с торцом долбяка передний угол .
Долбяки предназначены для нарезания прямозубых и косозубых цилиндрических зубчатых колес с наружным и внутренним зацеплением, шевронных колес, а также блоков зубчатых колес. Следует отметить их высокую технологичность, возможность достижения высокой точности при изготовлении и широкую универсальность в применении .
Изготавливают долбяки из быстрорежущей стали и очень редко снабжают твердосплавными пластинами.
Слайд 15а
б
Рис. 12. Процесс нарезания блока зубчатых колес (а) и вал-шестерни (б) на
а
б
Рис. 12. Процесс нарезания блока зубчатых колес (а) и вал-шестерни (б) на
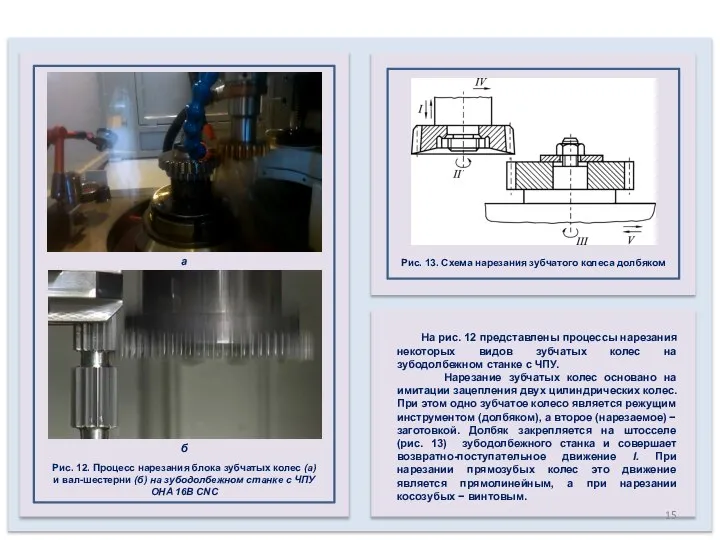
Рис. 13. Схема нарезания зубчатого колеса долбяком
На рис. 12 представлены процессы нарезания некоторых видов зубчатых колес на зубодолбежном станке с ЧПУ.
Нарезание зубчатых колес основано на имитации зацепления двух цилиндрических колес. При этом одно зубчатое колесо является режущим инструментом (долбяком), а второе (нарезаемое) − заготовкой. Долбяк закрепляется на штосселе (рис. 13) зубодолбежного станка и совершает возвратно-поступательное движение I. При нарезании прямозубых колес это движение является прямолинейным, а при нарезании косозубых − винтовым.
Слайд 16Главное движение или движения резания совершается при перемещении долбяка вниз, а холостой
Главное движение или движения резания совершается при перемещении долбяка вниз, а холостой
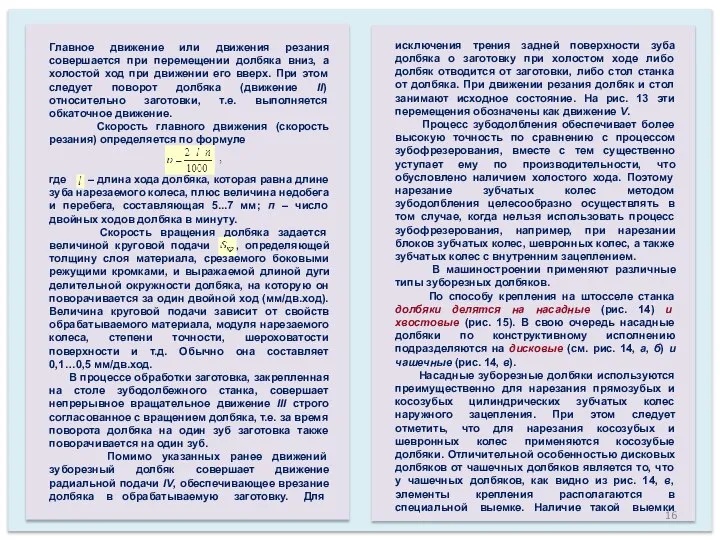
Скорость главного движения (скорость резания) определяется по формуле
где – длина хода долбяка, которая равна длине зуба нарезаемого колеса, плюс величина недобега и перебега, составляющая 5...7 мм; п – число двойных ходов долбяка в минуту.
Скорость вращения долбяка задается величиной круговой подачи , определяющей толщину слоя материала, срезаемого боковыми режущими кромками, и выражаемой длиной дуги делительной окружности долбяка, на которую он поворачивается за один двойной ход (мм/дв.ход). Величина круговой подачи зависит от свойств обрабатываемого материала, модуля нарезаемого колеса, степени точности, шероховатости поверхности и т.д. Обычно она составляет 0,1…0,5 мм/дв.ход.
В процессе обработки заготовка, закрепленная на столе зубодолбежного станка, совершает непрерывное вращательное движение III строго согласованное с вращением долбяка, т.е. за время поворота долбяка на один зуб заготовка также поворачивается на один зуб.
Помимо указанных ранее движений зуборезный долбяк совершает движение радиальной подачи IV, обеспечивающее врезание долбяка в обрабатываемую заготовку. Для
исключения трения задней поверхности зуба долбяка о заготовку при холостом ходе либо долбяк отводится от заготовки, либо стол станка от долбяка. При движении резания долбяк и стол занимают исходное состояние. На рис. 13 эти перемещения обозначены как движение V.
Процесс зубодолбления обеспечивает более высокую точность по сравнению с процессом зубофрезерования, вместе с тем существенно уступает ему по производительности, что обусловлено наличием холостого хода. Поэтому нарезание зубчатых колес методом зубодолбления целесообразно осуществлять в том случае, когда нельзя использовать процесс зубофрезерования, например, при нарезании блоков зубчатых колес, шевронных колес, а также зубчатых колес с внутренним зацеплением.
В машиностроении применяют различные типы зуборезных долбяков.
По способу крепления на штосселе станка долбяки делятся на насадные (рис. 14) и хвостовые (рис. 15). В свою очередь насадные долбяки по конструктивному исполнению подразделяются на дисковые (см. рис. 14, а, б) и чашечные (рис. 14, в).
Насадные зуборезные долбяки используются преимущественно для нарезания прямозубых и косозубых цилиндрических зубчатых колес наружного зацепления. При этом следует отметить, что для нарезания косозубых и шевронных колес применяются косозубые долбяки. Отличительной особенностью дисковых долбяков от чашечных долбяков является то, что у чашечных долбяков, как видно из рис. 14, в, элементы крепления располагаются в специальной выемке. Наличие такой выемки
Слайд 17
а
б
в
Рис. 14. Дисковые прямозубый (а) косозубый (б)
и прямозубый чашечный (в)
а
б
в
Рис. 14. Дисковые прямозубый (а) косозубый (б)
и прямозубый чашечный (в)
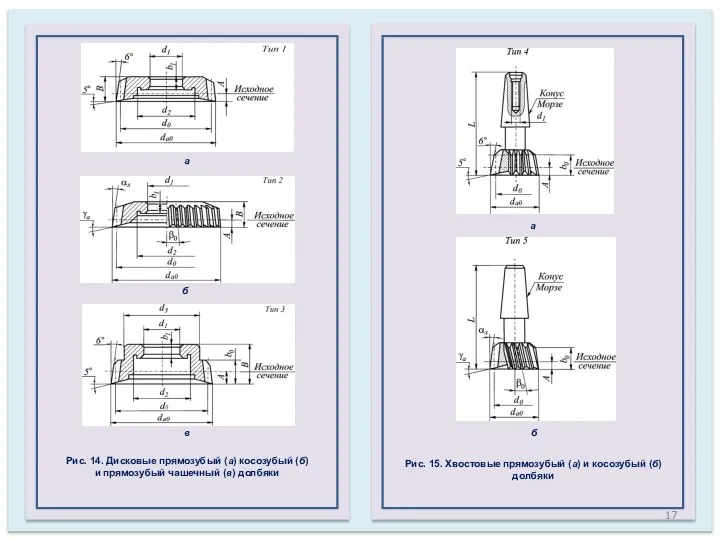
а
б
Рис. 15. Хвостовые прямозубый (а) и косозубый (б) долбяки
Слайд 18исключает возможность их контакта с упором, имеющего место, например, при изготовлении блока
исключает возможность их контакта с упором, имеющего место, например, при изготовлении блока
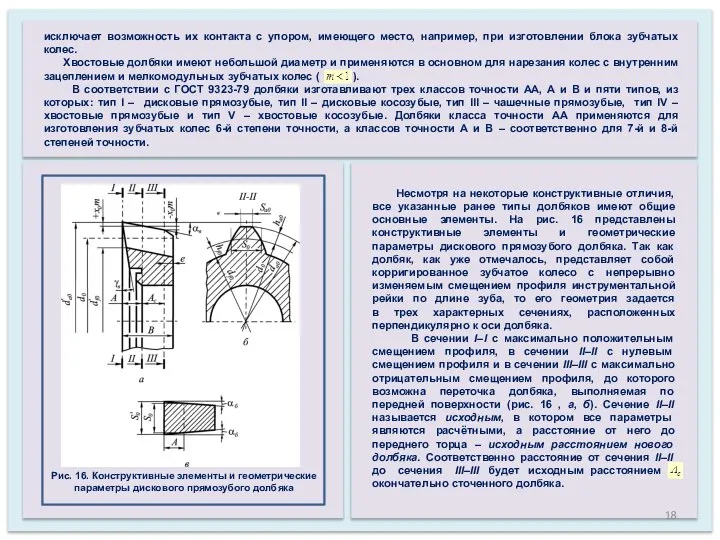
Хвостовые долбяки имеют небольшой диаметр и применяются в основном для нарезания колес с внутренним зацеплением и мелкомодульных зубчатых колес ( ).
В соответствии с ГОСТ 9323-79 долбяки изготавливают трех классов точности АА, А и В и пяти типов, из которых: тип I – дисковые прямозубые, тип II – дисковые косозубые, тип III – чашечные прямозубые, тип IV – хвостовые прямозубые и тип V – хвостовые косозубые. Долбяки класса точности АА применяются для изготовления зубчатых колес 6-й степени точности, а классов точности А и В – соответственно для 7-й и 8-й степеней точности.
Несмотря на некоторые конструктивные отличия, все указанные ранее типы долбяков имеют общие основные элементы. На рис. 16 представлены конструктивные элементы и геометрические параметры дискового прямозубого долбяка. Так как долбяк, как уже отмечалось, представляет собой корригированное зубчатое колесо с непрерывно изменяемым смещением профиля инструментальной рейки по длине зуба, то его геометрия задается в трех характерных сечениях, расположенных перпендикулярно к оси долбяка.
В сечении I‒I с максимально положительным смещением профиля, в сечении II‒II c нулевым смещением профиля и в сечении III‒III с максимально отрицательным смещением профиля, до которого возможна переточка долбяка, выполняемая по передней поверхности (рис. 16 , а, б). Сечение II‒II называется исходным, в котором все параметры являются расчётными, а расстояние от него до переднего торца – исходным расстоянием нового долбяка. Соответственно расстояние от сечения II‒II до сечения III‒III будет исходным расстоянием
окончательно сточенного долбяка.
Рис. 16. Конструктивные элементы и геометрические параметры дискового прямозубого долбяка
Слайд 19
У стандартных долбяков, предназначенных для нарезания зубчатых колес с углом
У стандартных долбяков, предназначенных для нарезания зубчатых колес с углом
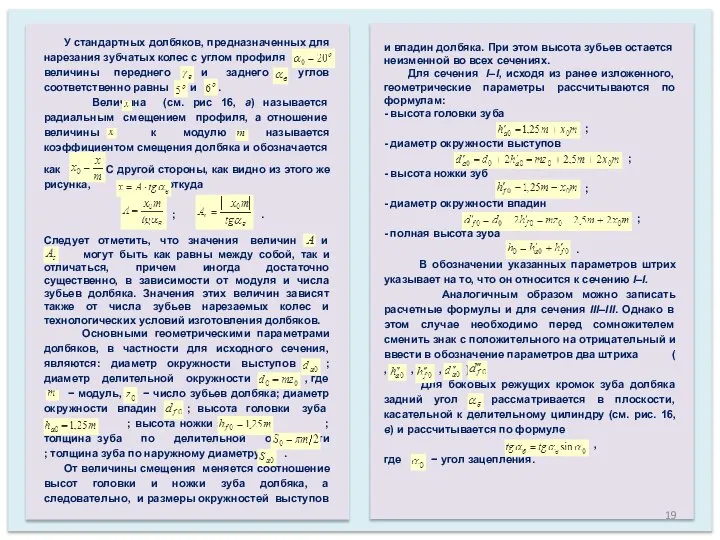
величины переднего и заднего углов соответственно равны и .
Величина (см. рис 16, а) называется радиальным смещением профиля, а отношение
величины к модулю называется коэффициентом смещения долбяка и обозначается
как . С другой стороны, как видно из этого же рисунка, , откуда
; .
Следует отметить, что значения величин и
могут быть как равны между собой, так и отличаться, причем иногда достаточно существенно, в зависимости от модуля и числа зубьев долбяка. Значения этих величин зависят также от числа зубьев нарезаемых колес и технологических условий изготовления долбяков.
Основными геометрическими параметрами долбяков, в частности для исходного сечения, являются: диаметр окружности выступов ; диаметр делительной окружности , где
− модуль, − число зубьев долбяка; диаметр окружности впадин ; высота головки зуба
; высота ножки зуба ; толщина зуба по делительной окружности ; толщина зуба по наружному диаметру .
От величины смещения меняется соотношение высот головки и ножки зуба долбяка, а следовательно, и размеры окружностей выступов
и впадин долбяка. При этом высота зубьев остается неизменной во всех сечениях.
Для сечения I‒I, исходя из ранее изложенного, геометрические параметры рассчитываются по формулам:
- высота головки зуба
;
- диаметр окружности выступов
;
- высота ножки зуб
;
- диаметр окружности впадин
;
- полная высота зуба
.
В обозначении указанных параметров штрих указывает на то, что он относится к сечению I‒I.
Аналогичным образом можно записать расчетные формулы и для сечения III‒III. Однако в этом случае необходимо перед сомножителем сменить знак с положительного на отрицательный и ввести в обозначение параметров два штриха ( , , , ).
Для боковых режущих кромок зуба долбяка задний угол рассматривается в плоскости, касательной к делительному цилиндру (см. рис. 16, в) и рассчитывается по формуле
,
где − угол зацепления.
Слайд 20 Период стойкости Т для долбяка выбирается в зависимости от значения модуля
Период стойкости Т для долбяка выбирается в зависимости от значения модуля
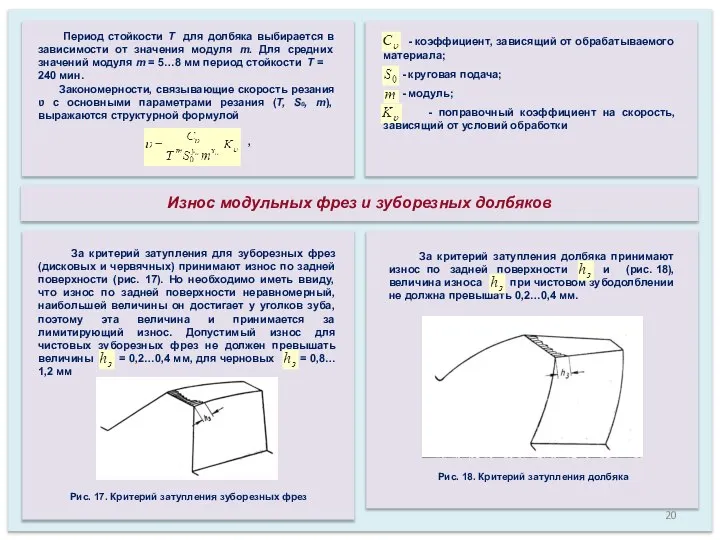
240 мин.
Закономерности, связывающие скорость резания ʋ с основными параметрами резания (T, S0, m), выражаются структурной формулой
,
- коэффициент, зависящий от обрабатываемого материала;
- круговая подача;
- модуль;
- поправочный коэффициент на скорость, зависящий от условий обработки
Износ модульных фрез и зуборезных долбяков
За критерий затупления долбяка принимают износ по задней поверхности и (рис. 18), величина износа при чистовом зубодолблении не должна превышать 0,2…0,4 мм.
Рис. 18. Критерий затупления долбяка
За критерий затупления для зуборезных фрез (дисковых и червячных) принимают износ по задней поверхности (рис. 17). Но необходимо иметь ввиду, что износ по задней поверхности неравномерный, наибольшей величины он достигает у уголков зуба, поэтому эта величина и принимается за лимитирующий износ. Допустимый износ для чистовых зуборезных фрез не должен превышать величины = 0,2…0,4 мм, для черновых = 0,8… 1,2 мм
Рис. 17. Критерий затупления зуборезных фрез
Слайд 21Рис. 2.9. Конструктивные параметры дискового шевера
ЗУБООТДЕЛОЧНЫЕ ОПЕРАЦИИ
ШЕВИНГОВАНИЕ
Для повышения степени точности и
Рис. 2.9. Конструктивные параметры дискового шевера
ЗУБООТДЕЛОЧНЫЕ ОПЕРАЦИИ
ШЕВИНГОВАНИЕ
Для повышения степени точности и
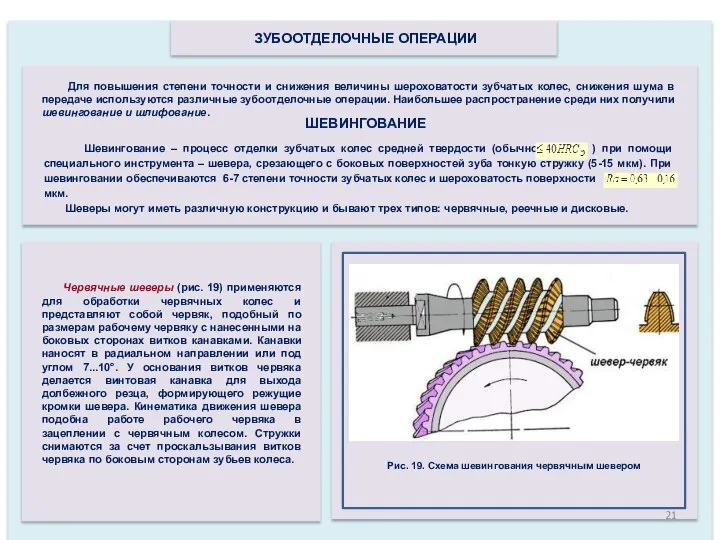
Шевингование – процесс отделки зубчатых колес средней твердости (обычно ) при помощи специального инструмента – шевера, срезающего с боковых поверхностей зуба тонкую стружку (5-15 мкм). При шевинговании обеспечиваются 6-7 степени точности зубчатых колес и шероховатость поверхности
мкм.
Шеверы могут иметь различную конструкцию и бывают трех типов: червячные, реечные и дисковые.
Рис. 19. Схема шевингования червячным шевером
Червячные шеверы (рис. 19) применяются для обработки червячных колес и представляют собой червяк, подобный по размерам рабочему червяку с нанесенными на боковых сторонах витков канавками. Канавки наносят в радиальном направлении или под углом 7...10°. У основания витков червяка делается винтовая канавка для выхода долбежного резца, формирующего режущие кромки шевера. Кинематика движения шевера подобна работе рабочего червяка в зацеплении с червячным колесом. Стружки снимаются за счет проскальзывания витков червяка по боковым сторонам зубьев колеса.
Слайд 22 Реечные шеверы (рис. 20, а) предназначены для обработки цилиндрических колес с
Реечные шеверы (рис. 20, а) предназначены для обработки цилиндрических колес с
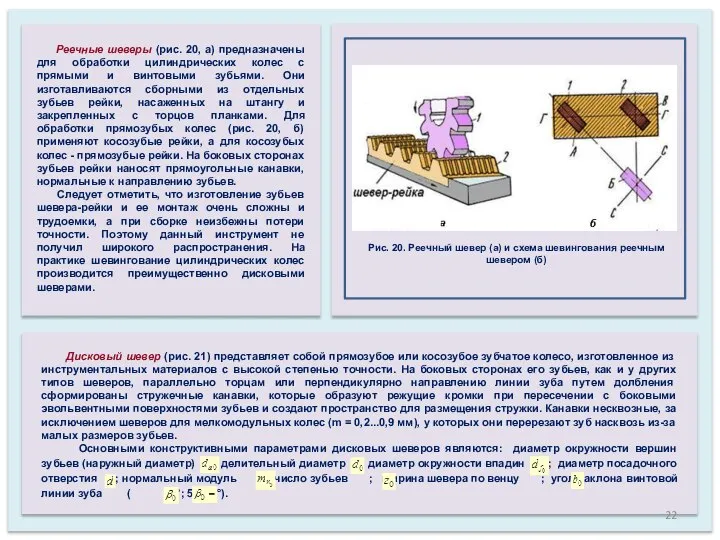
Следует отметить, что изготовление зубьев шевера-рейки и ее монтаж очень сложны и трудоемки, а при сборке неизбежны потери точности. Поэтому данный инструмент не получил широкого распространения. На практике шевингование цилиндрических колес производится преимущественно дисковыми шеверами.
Рис. 20. Реечный шевер (а) и схема шевингования реечным шевером (б)
Дисковый шевер (рис. 21) представляет собой прямозубое или косозубое зубчатое колесо, изготовленное из инструментальных материалов с высокой степенью точности. На боковых сторонах его зубьев, как и у других типов шеверов, параллельно торцам или перпендикулярно направлению линии зуба путем долбления сформированы стружечные канавки, которые образуют режущие кромки при пересечении с боковыми эвольвентными поверхностями зубьев и создают пространство для размещения стружки. Канавки несквозные, за исключением шеверов для мелкомодульных колес (m = 0,2...0,9 мм), у которых они перерезают зуб насквозь из-за малых размеров зубьев.
Основными конструктивными параметрами дисковых шеверов являются: диаметр окружности вершин зубьев (наружный диаметр) ; делительный диаметр ; диаметр окружности впадин ; диаметр посадочного отверстия ; нормальный модуль ; число зубьев ; ширина шевера по венцу ; угол наклона винтовой линии зуба ( 0°; 5°; 15°).
Слайд 23
а
б
Рис. 21. Общий вид (а) и конструктивные параметры дискового шевера (б)
а
б
Рис. 21. Общий вид (а) и конструктивные параметры дискового шевера (б)
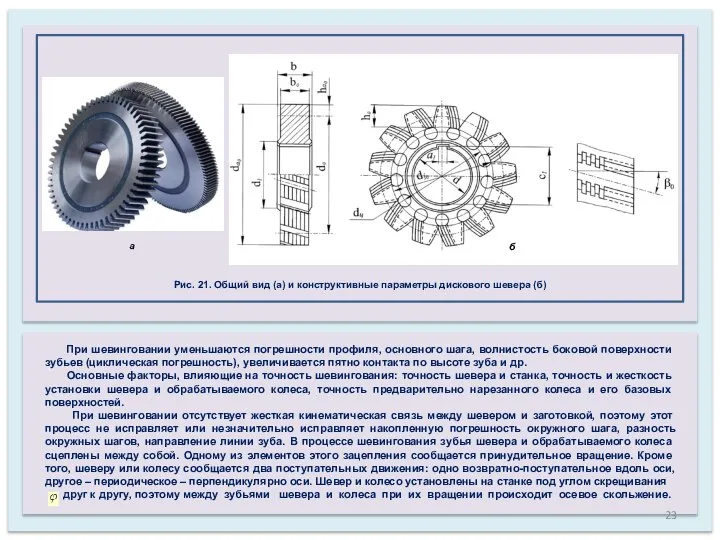
Основные факторы, влияющие на точность шевингования: точность шевера и станка, точность и жесткость установки шевера и обрабатываемого колеса, точность предварительно нарезанного колеса и его базовых поверхностей.
При шевинговании отсутствует жесткая кинематическая связь между шевером и заготовкой, поэтому этот процесс не исправляет или незначительно исправляет накопленную погрешность окружного шага, разность окружных шагов, направление линии зуба. В процессе шевингования зубья шевера и обрабатываемого колеса сцеплены между собой. Одному из элементов этого зацепления сообщается принудительное вращение. Кроме того, шеверу или колесу сообщается два поступательных движения: одно возвратно-поступательное вдоль оси, другое ‒ периодическое ‒ перпендикулярно оси. Шевер и колесо установлены на станке под углом скрещивания
друг к другу, поэтому между зубьями шевера и колеса при их вращении происходит осевое скольжение.
Слайд 24 Зубья шевера закалены до высокой твердости (63...66 HRCэ) и имеют на
Зубья шевера закалены до высокой твердости (63...66 HRCэ) и имеют на
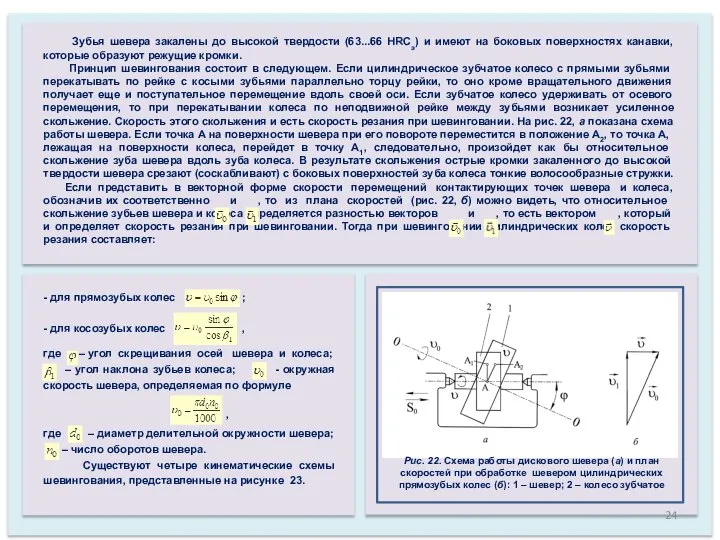
Принцип шевингования состоит в следующем. Если цилиндрическое зубчатое колесо с прямыми зубьями перекатывать по рейке с косыми зубьями параллельно торцу рейки, то оно кроме вращательного движения получает еще и поступательное перемещение вдоль своей оси. Если зубчатое колесо удерживать от осевого перемещения, то при перекатывании колеса по неподвижной рейке между зубьями возникает усиленное скольжение. Скорость этого скольжения и есть скорость резания при шевинговании. На рис. 22, а показана схема работы шевера. Если точка А на поверхности шевера при его повороте переместится в положение А2, то точка А, лежащая на поверхности колеса, перейдет в точку А1, следовательно, произойдет как бы относительное скольжение зуба шевера вдоль зуба колеса. В результате скольжения острые кромки закаленного до высокой твердости шевера срезают (соскабливают) с боковых поверхностей зуба колеса тонкие волосообразные стружки.
Если представить в векторной форме скорости перемещений контактирующих точек шевера и колеса,
обозначив их соответственно и , то из плана скоростей (рис. 22, б) можно видеть, что относительное скольжение зубьев шевера и колеса определяется разностью векторов и , то есть вектором , который
и определяет скорость резания при шевинговании. Тогда при шевинговании цилиндрических колес скорость резания составляет:
Рис. 22. Схема работы дискового шевера (а) и план скоростей при обработке шевером цилиндрических прямозубых колес (б): 1 – шевер; 2 – колесо зубчатое
- для прямозубых колес ;
- для косозубых колес ,
где ‒ угол скрещивания осей шевера и колеса;
‒ угол наклона зубьев колеса; - окружная скорость шевера, определяемая по формуле
,
где ‒ диаметр делительной окружности шевера;
‒ число оборотов шевера.
Существуют четыре кинематические схемы шевингования, представленные на рисунке 23.
Слайд 25Рис. 23. Схема шевингования:
а – с продольной подачей; б – с диагональной
Рис. 23. Схема шевингования:
а – с продольной подачей; б – с диагональной
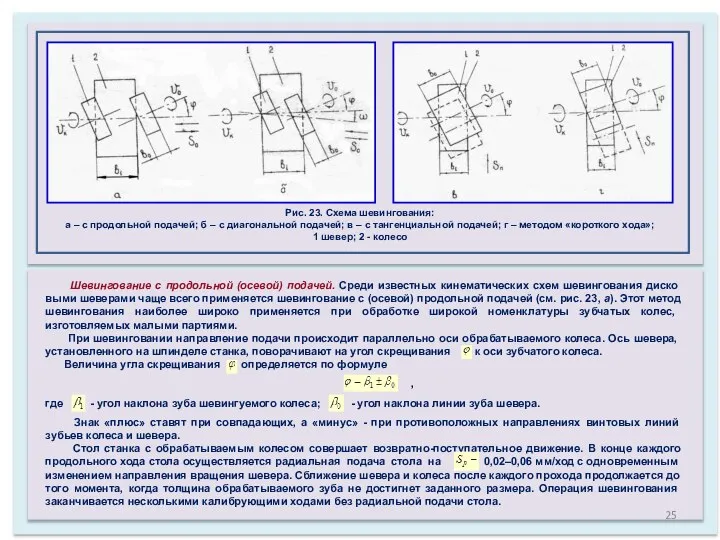
1 шевер; 2 - колесо
Шевингование с продольной (осевой) подачей. Среди известных кинематических схем шевингования дисковыми шеверами чаще всего применяется шевингование с (осевой) продольной подачей (см. рис. 23, а). Этот метод шевингования наиболее широко применяется при обработке широкой номенклатуры зубчатых колес, изготовляемых малыми партиями.
При шевинговании направление подачи происходит параллельно оси обрабатываемого колеса. Ось шевера, установленного на шпинделе станка, поворачивают на угол скрещивания к оси зубчатого колеса.
Величина угла скрещивания определяется по формуле
,
где - угол наклона зуба шевингуемого колеса; - угол наклона линии зуба шевера.
Знак «плюс» ставят при совпадающих, а «минус» - при противоположных направлениях винтовых линий зубьев колеса и шевера.
Стол станка с обрабатываемым колесом совершает возвратно-поступательное движение. В конце каждого продольного хода стола осуществляется радиальная подача стола на 0,02–0,06 мм/ход с одновременным изменением направления вращения шевера. Сближение шевера и колеса после каждого прохода продолжается до того момента, когда толщина обрабатываемого зуба не достигнет заданного размера. Операция шевингования заканчивается несколькими калибрующими ходами без радиальной подачи стола.
Слайд 26 Шевингование с диагональной подачей. Этот метод шевингования производится на станках, допускающих
Шевингование с диагональной подачей. Этот метод шевингования производится на станках, допускающих
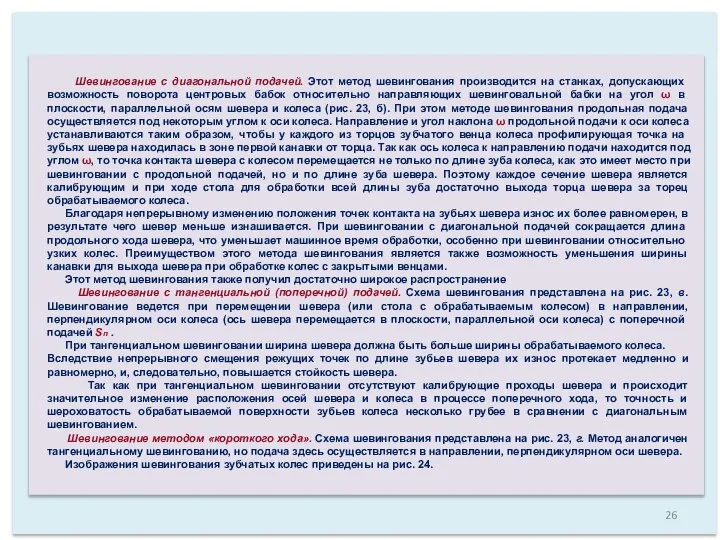
Благодаря непрерывному изменению положения точек контакта на зубьях шевера износ их более равномерен, в результате чего шевер меньше изнашивается. При шевинговании с диагональной подачей сокращается длина продольного хода шевера, что уменьшает машинное время обработки, особенно при шевинговании относительно узких колес. Преимуществом этого метода шевингования является также возможность уменьшения ширины канавки для выхода шевера при обработке колес с закрытыми венцами.
Этот метод шевингования также получил достаточно широкое распространение
Шевингование с тангенциальной (поперечной) подачей. Схема шевингования представлена на рис. 23, в. Шевингование ведется при перемещении шевера (или стола с обрабатываемым колесом) в направлении, перпендикулярном оси колеса (ось шевера перемещается в плоскости, параллельной оси колеса) с поперечной подачей Sп .
При тангенциальном шевинговании ширина шевера должна быть больше ширины обрабатываемого колеса.
Вследствие непрерывного смещения режущих точек по длине зубьев шевера их износ протекает медленно и равномерно, и, следовательно, повышается стойкость шевера.
Так как при тангенциальном шевинговании отсутствуют калибрующие проходы шевера и происходит значительное изменение расположения осей шевера и колеса в процессе поперечного хода, то точность и шероховатость обрабатываемой поверхности зубьев колеса несколько грубее в сравнении с диагональным шевингованием.
Шевингование методом «короткого хода». Схема шевингования представлена на рис. 23, г. Метод аналогичен тангенциальному шевингованию, но подача здесь осуществляется в направлении, перпендикулярном оси шевера.
Изображения шевингования зубчатых колес приведены на рис. 24.
Слайд 27а
б
Рис. 24. Процессы шевингования:
а – косозубого зубчатого колеса; б – много шестеренчатого
а
б
Рис. 24. Процессы шевингования:
а – косозубого зубчатого колеса; б – много шестеренчатого
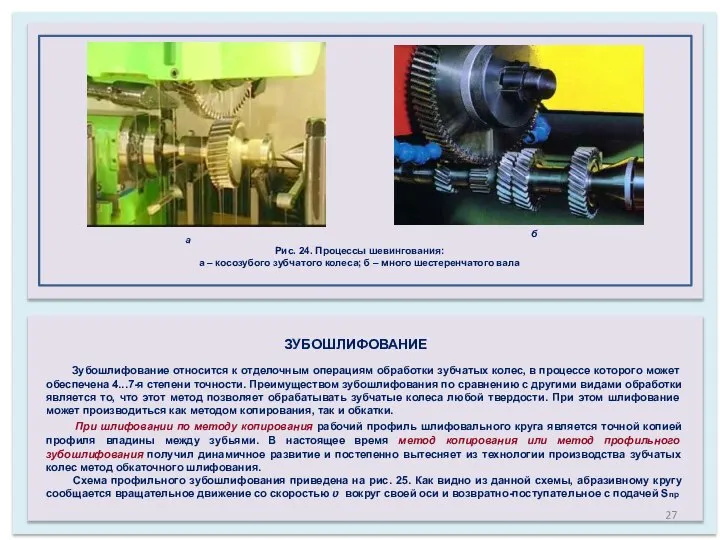
ЗУБОШЛИФОВАНИЕ
Зубошлифование относится к отделочным операциям обработки зубчатых колес, в процессе которого может обеспечена 4...7-я степени точности. Преимуществом зубошлифования по сравнению с другими видами обработки является то, что этот метод позволяет обрабатывать зубчатые колеса любой твердости. При этом шлифование может производиться как методом копирования, так и обкатки.
При шлифовании по методу копирования рабочий профиль шлифовального круга является точной копией профиля впадины между зубьями. В настоящее время метод копирования или метод профильного зубошлифования получил динамичное развитие и постепенно вытесняет из технологии производства зубчатых колес метод обкаточного шлифования.
Схема профильного зубошлифования приведена на рис. 25. Как видно из данной схемы, абразивному кругу сообщается вращательное движение со скоростью ʋ вокруг своей оси и возвратно-поступательное с подачей Sпр
Слайд 28Рис. 25. Схема профильного зубошлифования [3]
вдоль образующей зуба, а радиальная подача Sp
Рис. 25. Схема профильного зубошлифования [3]
вдоль образующей зуба, а радиальная подача Sp
![Рис. 25. Схема профильного зубошлифования [3] вдоль образующей зуба, а радиальная подача](/_ipx/f_webp&q_80&fit_contain&s_1440x1080/imagesDir/jpg/1132734/slide-27.jpg)
На рис. 26. приведена схема расположения осей и направление движения круга и заготовки для обеспечения процесса профильного зубошлифования при горизонтальном расположении оси заготовки. Движение А вокруг оcи X обеспечивает поворот (деление) при переходе обработки от зуба к зубу. Вдоль оси Y осуществляется радиальная подача на врезание и обеспечивается размер зуба по толщине. Движение В вокруг оси Y необходимо для разворота круга при обработке косозубых колес. Оси V и W требуются для двухкоординатного механизма правки шлифовального круга.
Рис. 26. Схема расположения осей при профильном зубошлифовании [3]
Слайд 29 На рис. 26 приведены процессы профильного зубошлифования прямозубой и косозубой шестерен
На рис. 26 приведены процессы профильного зубошлифования прямозубой и косозубой шестерен
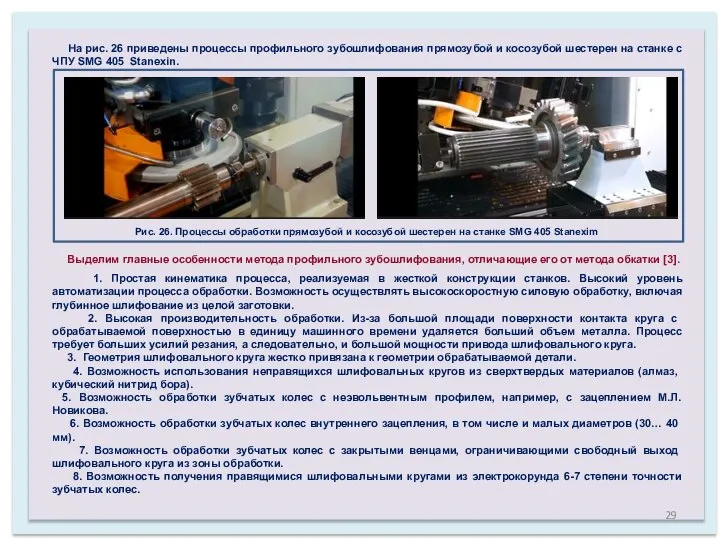
Выделим главные особенности метода профильного зубошлифования, отличающие его от метода обкатки [3].
1. Простая кинематика процесса, реализуемая в жесткой конструкции станков. Высокий уровень автоматизации процесса обработки. Возможность осуществлять высокоскоростную силовую обработку, включая глубинное шлифование из целой заготовки.
2. Высокая производительность обработки. Из-за большой площади поверхности контакта круга с обрабатываемой поверхностью в единицу машинного времени удаляется больший объем металла. Процесс требует больших усилий резания, а следовательно, и большой мощности привода шлифовального круга.
3. Геометрия шлифовального круга жестко привязана к геометрии обрабатываемой детали.
4. Возможность использования неправящихся шлифовальных кругов из сверхтвердых материалов (алмаз, кубический нитрид бора).
5. Возможность обработки зубчатых колес с неэвольвентным профилем, например, с зацеплением М.Л. Новикова.
6. Возможность обработки зубчатых колес внутреннего зацепления, в том числе и малых диаметров (30… 40 мм).
7. Возможность обработки зубчатых колес с закрытыми венцами, ограничивающими свободный выход шлифовального круга из зоны обработки.
8. Возможность получения правящимися шлифовальными кругами из электрокорунда 6-7 степени точности зубчатых колес.
Рис. 26. Процессы обработки прямозубой и косозубой шестерен на станке SMG 405 Stanexim
Слайд 30 Развитию процесса профильного шлифования способствовало создание фирмой КАРР процесса зубошлифования на
Развитию процесса профильного шлифования способствовало создание фирмой КАРР процесса зубошлифования на
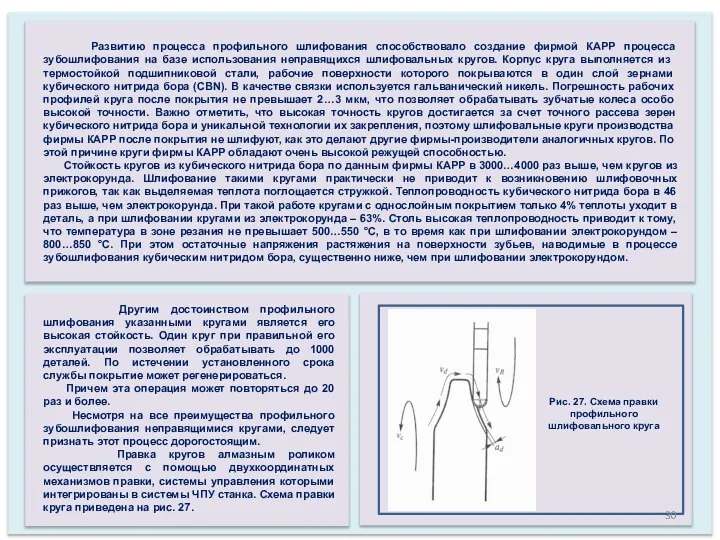
Стойкость кругов из кубического нитрида бора по данным фирмы КАРР в 3000…4000 раз выше, чем кругов из электрокорунда. Шлифование такими кругами практически не приводит к возникновению шлифовочных прижогов, так как выделяемая теплота поглощается стружкой. Теплопроводность кубического нитрида бора в 46 раз выше, чем электрокорунда. При такой работе кругами с однослойным покрытием только 4% теплоты уходит в деталь, а при шлифовании кругами из электрокорунда – 63%. Столь высокая теплопроводность приводит к тому, что температура в зоне резания не превышает 500…550 °С, в то время как при шлифовании электрокорундом – 800…850 °С. При этом остаточные напряжения растяжения на поверхности зубьев, наводимые в процессе зубошлифования кубическим нитридом бора, существенно ниже, чем при шлифовании электрокорундом.
Рис. 27. Схема правки профильного шлифовального круга
Другим достоинством профильного шлифования указанными кругами является его высокая стойкость. Один круг при правильной его эксплуатации позволяет обрабатывать до 1000 деталей. По истечении установленного срока службы покрытие может регенерироваться.
Причем эта операция может повторяться до 20 раз и более.
Несмотря на все преимущества профильного зубошлифования неправящимися кругами, следует признать этот процесс дорогостоящим.
Правка кругов алмазным роликом осуществляется с помощью двухкоординатных механизмов правки, системы управления которыми интегрированы в системы ЧПУ станка. Схема правки круга приведена на рис. 27.
Слайд 31 Станки для шлифования зубчатых колес профильными кругами выпускаются многими западными фирмами,
Станки для шлифования зубчатых колес профильными кругами выпускаются многими западными фирмами,
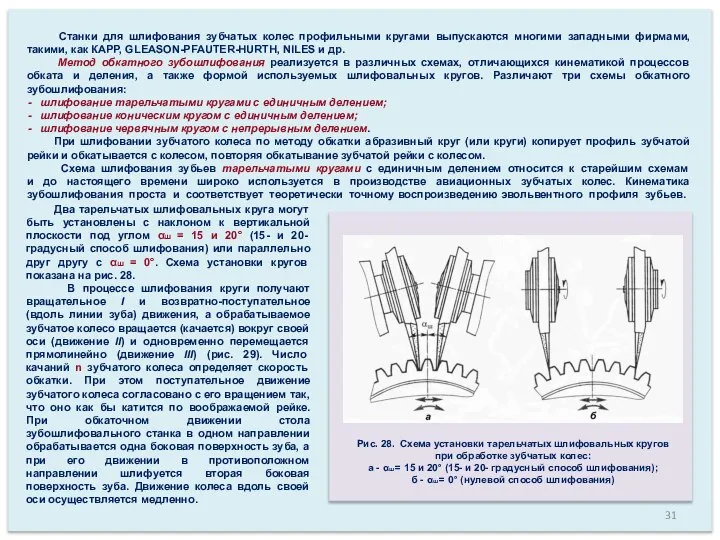
Метод обкатного зубошлифования реализуется в различных схемах, отличающихся кинематикой процессов обката и деления, а также формой используемых шлифовальных кругов. Различают три схемы обкатного зубошлифования:
шлифование тарельчатыми кругами с единичным делением;
шлифование коническим кругом с единичным делением;
шлифование червячным кругом с непрерывным делением.
При шлифовании зубчатого колеса по методу обкатки абразивный круг (или круги) копирует профиль зубчатой рейки и обкатывается с колесом, повторяя обкатывание зубчатой рейки с колесом.
Схема шлифования зубьев тарельчатыми кругами с единичным делением относится к старейшим схемам и до настоящего времени широко используется в производстве авиационных зубчатых колес. Кинематика зубошлифования проста и соответствует теоретически точному воспроизведению эвольвентного профиля зубьев.
Рис. 28. Схема установки тарельчатых шлифовальных кругов при обработке зубчатых колес:
а - αш = 15 и 20° (15- и 20- градусный способ шлифования); б - αш = 0° (нулевой способ шлифования)
Два тарельчатых шлифовальных круга могут быть установлены с наклоном к вертикальной плоскости под углом αш = 15 и 20° (15- и 20- градусный способ шлифования) или параллельно друг другу с αш = 0°. Схема установки кругов показана на рис. 28.
В процессе шлифования круги получают вращательное I и возвратно-поступательное (вдоль линии зуба) движения, а обрабатываемое зубчатое колесо вращается (качается) вокруг своей оси (движение II) и одновременно перемещается прямолинейно (движение III) (рис. 29). Число качаний n зубчатого колеса определяет скорость обкатки. При этом поступательное движение зубчатого колеса согласовано с его вращением так, что оно как бы катится по воображаемой рейке. При обкаточном движении стола зубошлифовального станка в одном направлении обрабатывается одна боковая поверхность зуба, а при его движении в противоположном направлении шлифуется вторая боковая поверхность зуба. Движение колеса вдоль своей оси осуществляется медленно.
Слайд 32Рис. 30. Следы резов от шлифовальных кругов
на боковых поверхностях зубьев [3]:
а
Рис. 30. Следы резов от шлифовальных кругов
на боковых поверхностях зубьев [3]:
а
![Рис. 30. Следы резов от шлифовальных кругов на боковых поверхностях зубьев [3]:](/_ipx/f_webp&q_80&fit_contain&s_1440x1080/imagesDir/jpg/1132734/slide-31.jpg)
нулевом способе шлифования шлифовании
Рис. 29. Движения, необходимые при шлифовании тарельчатыми кругами.
Глубина резания задается смещением кругов. Скорость это движения определяет осевую подачу S. После обработки одной впадины колесо поворачивается на один зуб, т.е. осуществляется делительное движение.
Несмотря на одинаковое движение обкатки, разная установка кругов при 15-градусном и нулевом способах шлифования приводят к различным схемам образования резов на поверхностях зубьев. Следы резов представляют собой характерную сетку при 15-градусном способе (рис. 30, а) и серию параллельных штрихов при нулевом способе (рис. 30, б).
При нулевом способе шлифования выше производительность и качество обработки. Для него характерны более короткий ход обкатки, сокращенная длина продольного хода шлифуемого колеса, а также меньшая шероховатость поверхности (Ra = 0,25…0,63 мкм) из-за отсутствия характерной сетки.
Основным преимуществом данной схемы шлифования зубьев является высокая точность шлифования профиля (4-5 степень точности). Так как при данной схеме профилирования площадка контакта режущей кромки круга с обрабатываемой поверхностью весьма мала, то форма шлифовального круга практически не оказывает влияния на погрешность профиля зуба. Высокая точность обработки также обусловлена наличием специального компенсационного механизма, контролирующего неизбежный в процессе шлифования износ абразивных кругов и автоматически перемещающих их в исходное положение.
Другой важной особенностью данной схемы зубошлифования, имеющей определяющее значение при шлифовании зубчатых колес, применяемых в авиационном двигателестроении, является низкая теплонапряженность процесса и, как следствие, меньшая склонность (по сравнению с другими схемами) к появлению шлифовочных дефектов в виде шлифовочных прижогов и микротрещин [3].
Слайд 33 Этому способствуют два обстоятельства. Во-первых, шлифование зубьев можно производить пористыми и
Этому способствуют два обстоятельства. Во-первых, шлифование зубьев можно производить пористыми и
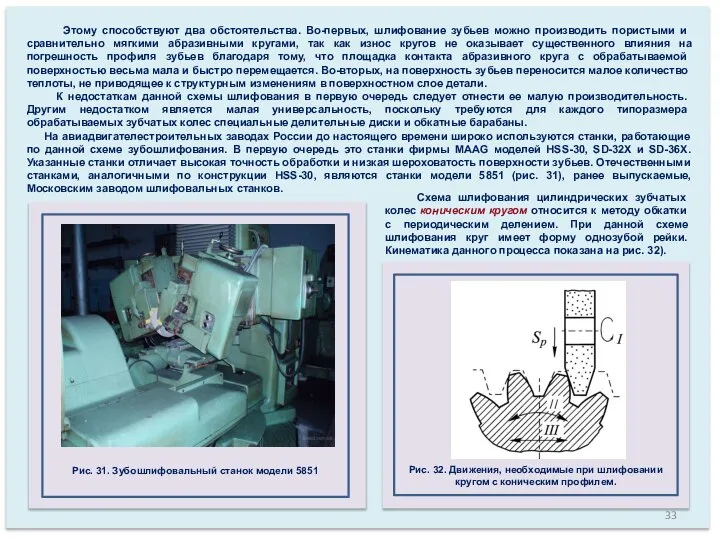
К недостаткам данной схемы шлифования в первую очередь следует отнести ее малую производительность. Другим недостатком является малая универсальность, поскольку требуются для каждого типоразмера обрабатываемых зубчатых колес специальные делительные диски и обкатные барабаны.
На авиадвигателестроительных заводах России до настоящего времени широко используются станки, работающие по данной схеме зубошлифования. В первую очередь это станки фирмы MAAG моделей HSS-30, SD-32X и SD-36X. Указанные станки отличает высокая точность обработки и низкая шероховатость поверхности зубьев. Отечественными станками, аналогичными по конструкции HSS-30, являются станки модели 5851 (рис. 31), ранее выпускаемые, Московским заводом шлифовальных станков.
Рис. 31. Зубошлифовальный станок модели 5851
Схема шлифования цилиндрических зубчатых колес коническим кругом относится к методу обкатки с периодическим делением. При данной схеме шлифования круг имеет форму однозубой рейки. Кинематика данного процесса показана на рис. 32).
Рис. 32. Движения, необходимые при шлифовании кругом с коническим профилем.
Слайд 34 При шлифовании зубчатых колес коническим кругом существует два способа шлифования –
При шлифовании зубчатых колес коническим кругом существует два способа шлифования –
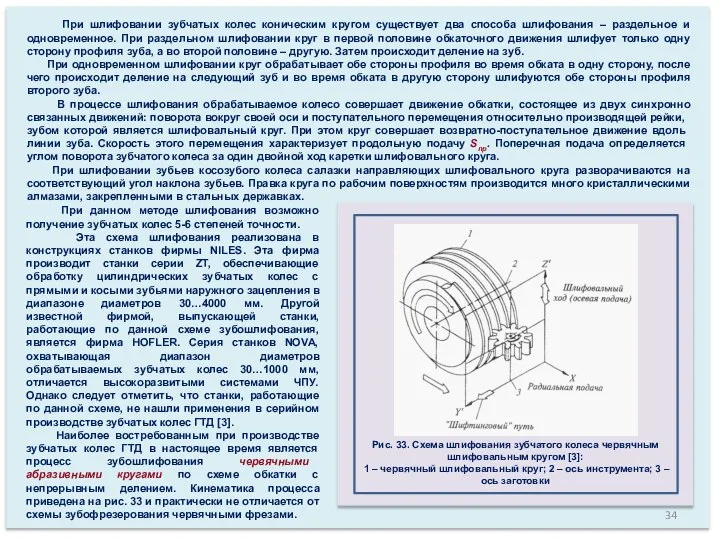
При одновременном шлифовании круг обрабатывает обе стороны профиля во время обката в одну сторону, после чего происходит деление на следующий зуб и во время обката в другую сторону шлифуются обе стороны профиля второго зуба.
В процессе шлифования обрабатываемое колесо совершает движение обкатки, состоящее из двух синхронно связанных движений: поворота вокруг своей оси и поступательного перемещения относительно производящей рейки, зубом которой является шлифовальный круг. При этом круг совершает возвратно-поступательное движение вдоль линии зуба. Скорость этого перемещения характеризует продольную подачу Snp. Поперечная подача определяется углом поворота зубчатого колеса за один двойной ход каретки шлифовального круга.
При шлифовании зубьев косозубого колеса салазки направляющих шлифовального круга разворачиваются на соответствующий угол наклона зубьев. Правка круга по рабочим поверхностям производится много кристаллическими алмазами, закрепленными в стальных державках.
При данном методе шлифования возможно получение зубчатых колес 5-6 степеней точности.
Эта схема шлифования реализована в конструкциях станков фирмы NILES. Эта фирма производит станки серии ZT, обеспечивающие обработку цилиндрических зубчатых колес с прямыми и косыми зубьями наружного зацепления в диапазоне диаметров 30…4000 мм. Другой известной фирмой, выпускающей станки, работающие по данной схеме зубошлифования, является фирма HOFLER. Серия станков NOVA, охватывающая диапазон диаметров обрабатываемых зубчатых колес 30…1000 мм, отличается высокоразвитыми системами ЧПУ. Однако следует отметить, что станки, работающие по данной схеме, не нашли применения в серийном производстве зубчатых колес ГТД [3].
Наиболее востребованным при производстве зубчатых колес ГТД в настоящее время является процесс зубошлифования червячными абразивными кругами по схеме обкатки с непрерывным делением. Кинематика процесса приведена на рис. 33 и практически не отличается от схемы зубофрезерования червячными фрезами.
Рис. 33. Схема шлифования зубчатого колеса червячным шлифовальным кругом [3]:
1 – червячный шлифовальный круг; 2 – ось инструмента; 3 – ось заготовки
Слайд 35 Основным движением станка, определяющим точность обработки деталей, является согласованное движение (вращение)
Основным движением станка, определяющим точность обработки деталей, является согласованное движение (вращение)
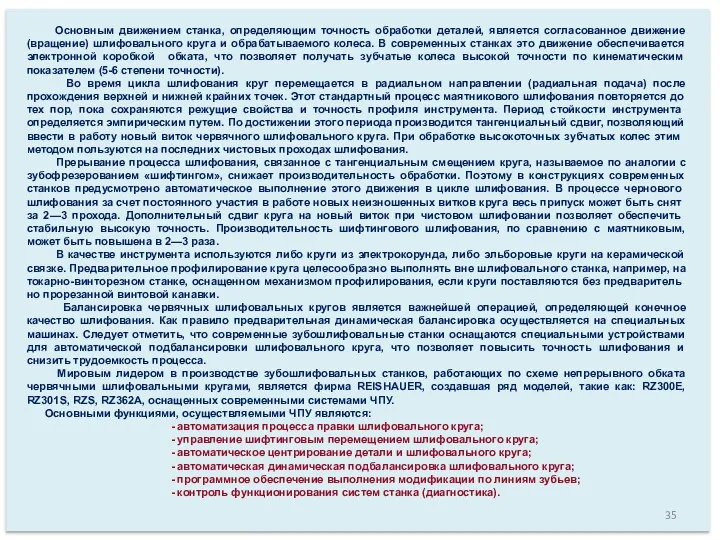
Во время цикла шлифования круг перемещается в радиальном направлении (радиальная подача) после прохождения верхней и нижней крайних точек. Этот стандартный процесс маятникового шлифования повторяется до тех пор, пока сохраняются режущие свойства и точность профиля инструмента. Период стойкости инструмента определяется эмпирическим путем. По достижении этого периода производится тангенциальный сдвиг, позволяющий ввести в работу новый виток червячного шлифовального круга. При обработке высокоточных зубчатых колес этим методом пользуются на последних чистовых проходах шлифования.
Прерывание процесса шлифования, связанное с тангенциальным смещением круга, называемое по аналогии с зубофрезерованием «шифтингом», снижает производительность обработки. Поэтому в конструкциях современных станков предусмотрено автоматическое выполнение этого движения в цикле шлифования. В процессе чернового шлифования за счет постоянного участия в работе новых неизношенных витков круга весь припуск может быть снят за 2—3 прохода. Дополнительный сдвиг круга на новый виток при чистовом шлифовании позволяет обеспечить стабильную высокую точность. Производительность шифтингового шлифования, по сравнению с маятниковым, может быть повышена в 2—3 раза.
В качестве инструмента используются либо круги из электрокорунда, либо эльборовые круги на керамической связке. Предварительное профилирование круга целесообразно выполнять вне шлифовального станка, например, на токарно-винторезном станке, оснащенном механизмом профилирования, если круги поставляются без предварительно прорезанной винтовой канавки.
Балансировка червячных шлифовальных кругов является важнейшей операцией, определяющей конечное качество шлифования. Как правило предварительная динамическая балансировка осуществляется на специальных машинах. Следует отметить, что современные зубошлифовальные станки оснащаются специальными устройствами для автоматической подбалансировки шлифовального круга, что позволяет повысить точность шлифования и снизить трудоемкость процесса.
Мировым лидером в производстве зубошлифовальных станков, работающих по схеме непрерывного обката червячными шлифовальными кругами, является фирма REISHAUER, создавшая ряд моделей, такие как: RZ300E, RZ301S, RZS, RZ362A, оснащенных современными системами ЧПУ.
Основными функциями, осуществляемыми ЧПУ являются:
- автоматизация процесса правки шлифовального круга;
- управление шифтинговым перемещением шлифовального круга;
- автоматическое центрирование детали и шлифовального круга;
- автоматическая динамическая подбалансировка шлифовального круга;
- программное обеспечение выполнения модификации по линиям зубьев;
- контроль функционирования систем станка (диагностика).
Слайд 36
Получил распространение также станок TAG 400 CNC, являющийся совместной разработкой
Получил распространение также станок TAG 400 CNC, являющийся совместной разработкой
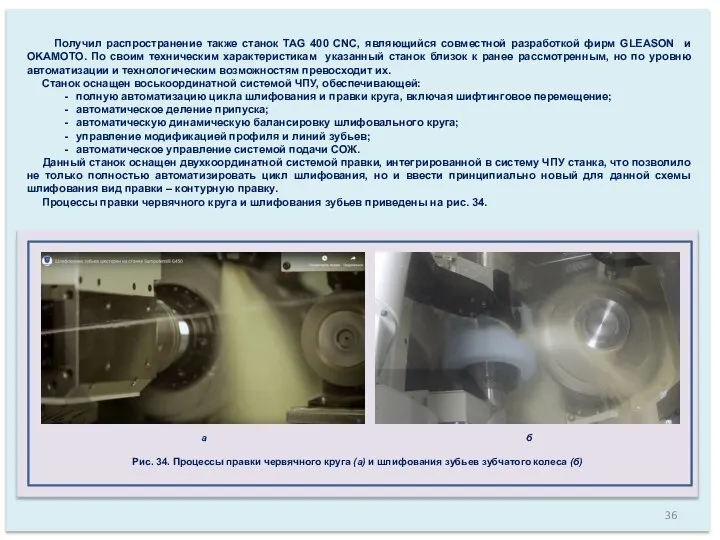
Станок оснащен воськоординатной системой ЧПУ, обеспечивающей:
полную автоматизацию цикла шлифования и правки круга, включая шифтинговое перемещение;
автоматическое деление припуска;
автоматическую динамическую балансировку шлифовального круга;
управление модификацией профиля и линий зубьев;
автоматическое управление системой подачи СОЖ.
Данный станок оснащен двухкоординатной системой правки, интегрированной в систему ЧПУ станка, что позволило не только полностью автоматизировать цикл шлифования, но и ввести принципиально новый для данной схемы шлифования вид правки – контурную правку.
Процессы правки червячного круга и шлифования зубьев приведены на рис. 34.
а б
Рис. 34. Процессы правки червячного круга (а) и шлифования зубьев зубчатого колеса (б)
Слайд 37 КАЧЕСТВО ПОВЕРХНОСТНОГО СЛОЯ ПРИ ЗУБОШЛИФОВАНИИ
ПОНЯТИЕ КАЧЕСТВА ПОВЕРХНОСТЕЙ ДЕТАЛЕЙ МАШИН
Под качеством поверхности
КАЧЕСТВО ПОВЕРХНОСТНОГО СЛОЯ ПРИ ЗУБОШЛИФОВАНИИ
ПОНЯТИЕ КАЧЕСТВА ПОВЕРХНОСТЕЙ ДЕТАЛЕЙ МАШИН
Под качеством поверхности
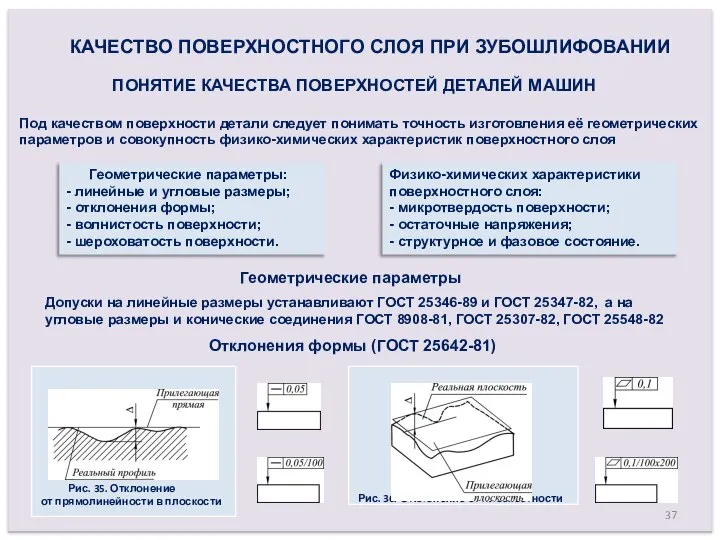
Геометрические параметры:
- линейные и угловые размеры;
- отклонения формы;
- волнистость поверхности;
- шероховатость поверхности.
Физико-химических характеристики поверхностного слоя:
- микротвердость поверхности;
- остаточные напряжения;
- структурное и фазовое состояние.
Геометрические параметры
Допуски на линейные размеры устанавливают ГОСТ 25346-89 и ГОСТ 25347-82, а на угловые размеры и конические соединения ГОСТ 8908-81, ГОСТ 25307-82, ГОСТ 25548-82
Отклонения формы (ГОСТ 25642-81)
Слайд 38 Отклонения формы
а б в
Рис. 37. Отклонение от круглости и ее
Отклонения формы
а б в
Рис. 37. Отклонение от круглости и ее
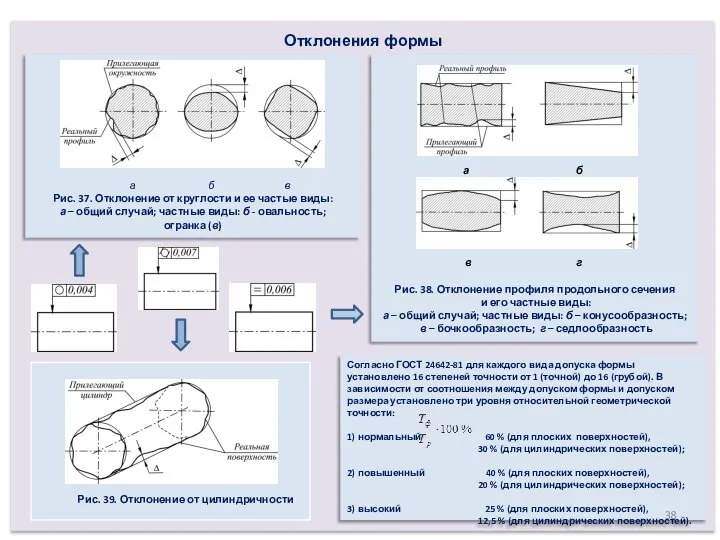
а – общий случай; частные виды: б - овальность;
огранка (в)
а б
в г
Рис. 38. Отклонение профиля продольного сечения
и его частные виды:
а – общий случай; частные виды: б – конусообразность;
в – бочкообразность; г – седлообразность
Согласно ГОСТ 24642-81 для каждого вида допуска формы установлено 16 степеней точности от 1 (точной) до 16 (грубой). В зависимости от соотношения между допуском формы и допуском размера установлено три уровня относительной геометрической точности:
1) нормальный 60 % (для плоских поверхностей),
30 % (для цилиндрических поверхностей);
2) повышенный 40 % (для плоских поверхностей),
20 % (для цилиндрических поверхностей);
3) высокий 25 % (для плоских поверхностей),
12,5 % (для цилиндрических поверхностей).
Слайд 39 Волнистость поверхности (РС 3951-73)
Волнистость поверхности представляет собой совокупность периодически повторяющихся неровностей
Волнистость поверхности (РС 3951-73)
Волнистость поверхности представляет собой совокупность периодически повторяющихся неровностей
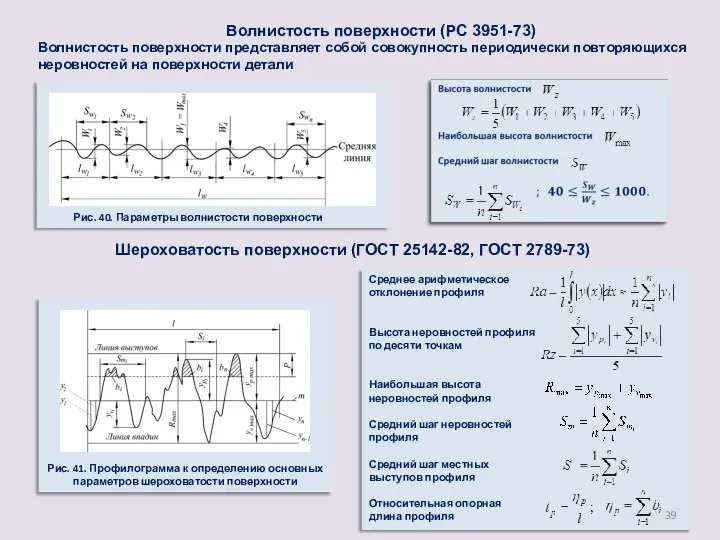
Рис. 40. Параметры волнистости поверхности
Шероховатость поверхности (ГОСТ 25142-82, ГОСТ 2789-73)
Рис. 41. Профилограмма к определению основных параметров шероховатости поверхности
Среднее арифметическое
отклонение профиля
Высота неровностей профиля
по десяти точкам
Наибольшая высота
неровностей профиля
Средний шаг неровностей
профиля
Средний шаг местных
выступов профиля
Относительная опорная
длина профиля
Слайд 40Механизм формирования шероховатости поверхности
На формирование шероховатости поверхности в процессе обработки оказывают влияние
Механизм формирования шероховатости поверхности
На формирование шероховатости поверхности в процессе обработки оказывают влияние
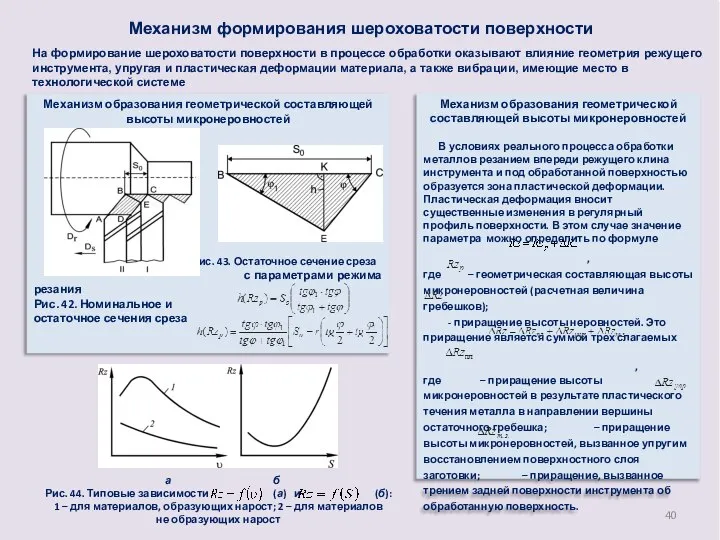
Механизм образования геометрической составляющей высоты микронеровностей
Рис. 43. Остаточное сечение среза
с параметрами режима резания
Рис. 42. Номинальное и
остаточное сечения среза
а б
Рис. 44. Типовые зависимости (а) и (б):
1 – для материалов, образующих нарост; 2 – для материалов
не образующих нарост
Механизм образования геометрической составляющей высоты микронеровностей
В условиях реального процесса обработки металлов резанием впереди режущего клина инструмента и под обработанной поверхностью образуется зона пластической деформации. Пластическая деформация вносит существенные изменения в регулярный профиль поверхности. В этом случае значение параметра можно определить по формуле
,
где – геометрическая составляющая высоты микронеровностей (расчетная величина гребешков);
- приращение высоты неровностей. Это приращение является суммой трех слагаемых
,
где – приращение высоты микронеровностей в результате пластического течения металла в направлении вершины остаточного гребешка; – приращение высоты микронеровностей, вызванное упругим восстановлением поверхностного слоя заготовки; – приращение, вызванное трением задней поверхности инструмента об обработанную поверхность.
Слайд 41Физико-химические характеристики поверхностного слоя
При резании поверхностный слой обрабатываемой детали деформируется и изменяются
Физико-химические характеристики поверхностного слоя
При резании поверхностный слой обрабатываемой детали деформируется и изменяются
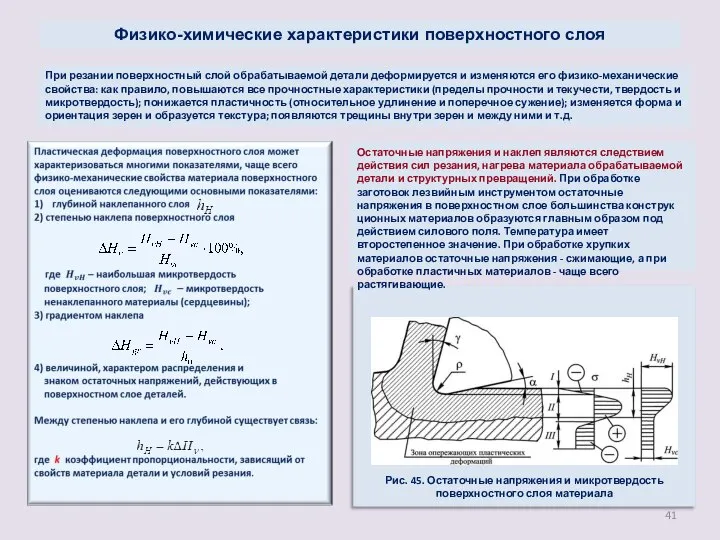
Рис. 45. Остаточные напряжения и микротвердость
поверхностного слоя материала
Остаточные напряжения и наклеп являются следствием действия сил резания, нагрева материала обрабатываемой детали и структурных превращений. При обработке заготовок лезвийным инструментом остаточные напряжения в поверхностном слое большинства конструкционных материалов образуются главным образом под действием силового поля. Температура имеет второстепенное значение. При обработке хрупких материалов остаточные напряжения - сжимающие, а при обработке пластичных материалов - чаще всего растягивающие.
Слайд 42
а б
Рисунок 46 – Зависимости степени наклепа и глубины наклепа от подачи
а б
Рисунок 46 – Зависимости степени наклепа и глубины наклепа от подачи

Рисунок 47 - Характер влияния условий резания на окружные остаточные напряжения и глубину их залегания
Слайд 43Методы контроля микротвердости и остаточных напряжений
Рис. 50. Автоматизированная установка для определения остаточных
Методы контроля микротвердости и остаточных напряжений
Рис. 50. Автоматизированная установка для определения остаточных
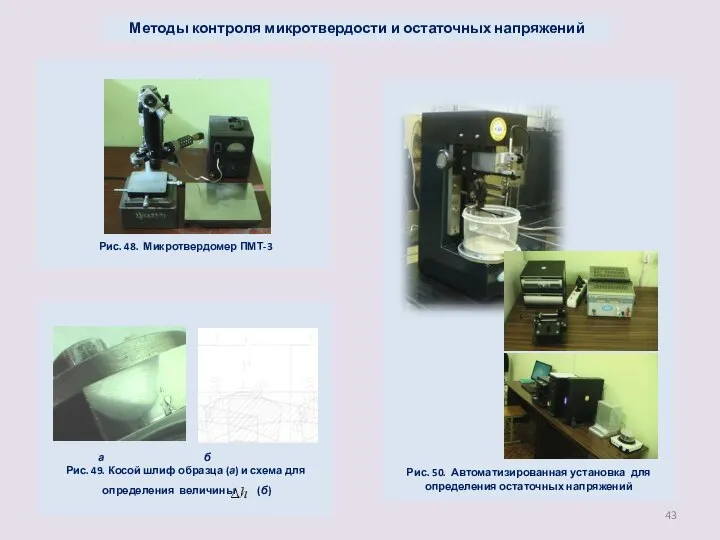
а б
Рис. 49. Косой шлиф образца (а) и схема для
определения величины (б)
Рис. 48. Микротвердомер ПМТ-3
Слайд 44Механизм формирования остаточных напряжений
Рис. 52. Условная схема свободного
резания малопластичных материалов
Рис.
Механизм формирования остаточных напряжений
Рис. 52. Условная схема свободного
резания малопластичных материалов
Рис.
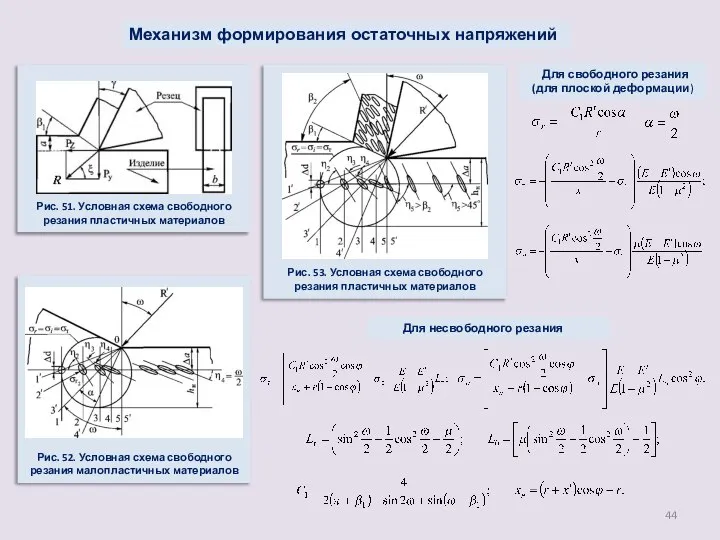
резания пластичных материалов
Рис. 51. Условная схема свободного
резания пластичных материалов
Для свободного резания
(для плоской деформации)
Для несвободного резания
Слайд 45СТРУКТУРНЫЕ ИЗМЕНЕНИЯ В ПОВЕРХНОСТНОМ СЛОЕ ПРИ ШЛИФОВАНИИ
Эффективно устраняя деформации и коробление,
СТРУКТУРНЫЕ ИЗМЕНЕНИЯ В ПОВЕРХНОСТНОМ СЛОЕ ПРИ ШЛИФОВАНИИ
Эффективно устраняя деформации и коробление,
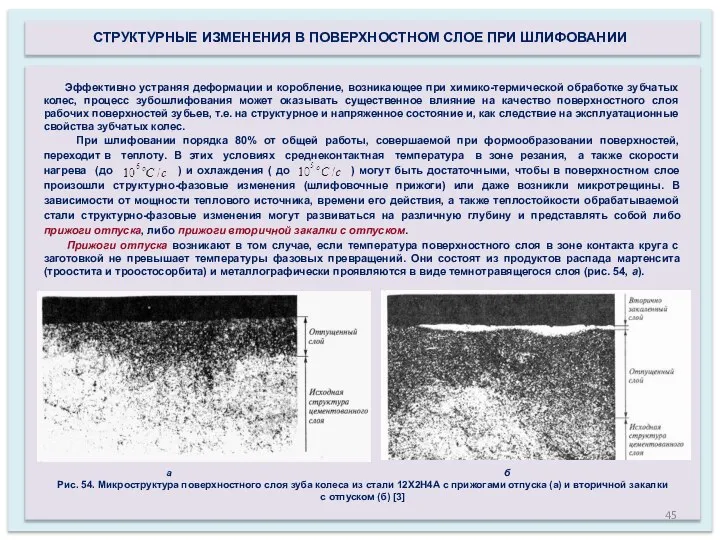
При шлифовании порядка 80% от общей работы, совершаемой при формообразовании поверхностей, переходит в теплоту. В этих условиях среднеконтактная температура в зоне резания, а также скорости нагрева (до ) и охлаждения ( до ) могут быть достаточными, чтобы в поверхностном слое произошли структурно-фазовые изменения (шлифовочные прижоги) или даже возникли микротрещины. В зависимости от мощности теплового источника, времени его действия, а также теплостойкости обрабатываемой стали структурно-фазовые изменения могут развиваться на различную глубину и представлять собой либо прижоги отпуска, либо прижоги вторичной закалки с отпуском.
Прижоги отпуска возникают в том случае, если температура поверхностного слоя в зоне контакта круга с заготовкой не превышает температуры фазовых превращений. Они состоят из продуктов распада мартенсита (троостита и троостосорбита) и металлографически проявляются в виде темнотравящегося слоя (рис. 54, а).
а б
Рис. 54. Микроструктура поверхностного слоя зуба колеса из стали 12Х2Н4А с прижогами отпуска (а) и вторичной закалки
с отпуском (б) [3]
Слайд 46 Прижоги закалки с отпуском (рис. 54, б) возникают при нагреве шлифуемой
Прижоги закалки с отпуском (рис. 54, б) возникают при нагреве шлифуемой
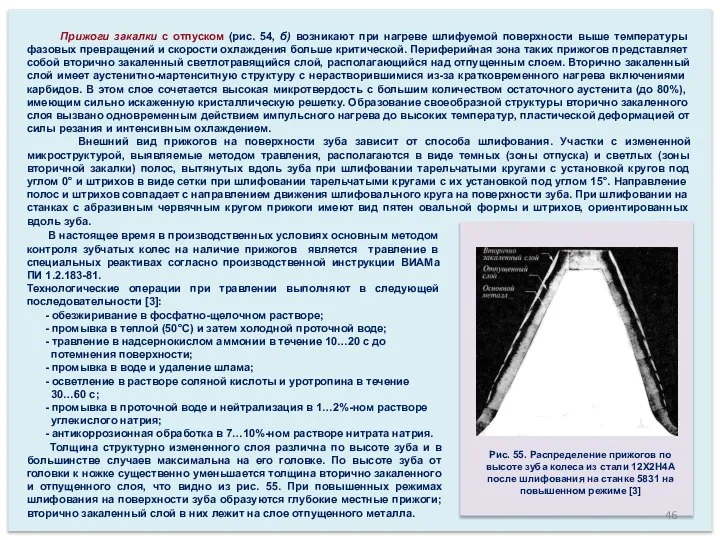
Внешний вид прижогов на поверхности зуба зависит от способа шлифования. Участки с измененной микроструктурой, выявляемые методом травления, располагаются в виде темных (зоны отпуска) и светлых (зоны вторичной закалки) полос, вытянутых вдоль зуба при шлифовании тарельчатыми кругами с установкой кругов под углом 0° и штрихов в виде сетки при шлифовании тарельчатыми кругами с их установкой под углом 15°. Направление полос и штрихов совпадает с направлением движения шлифовального круга на поверхности зуба. При шлифовании на станках с абразивным червячным кругом прижоги имеют вид пятен овальной формы и штрихов, ориентированных вдоль зуба.
В настоящее время в производственных условиях основным методом контроля зубчатых колес на наличие прижогов является травление в специальных реактивах согласно производственной инструкции ВИАМа ПИ 1.2.183-81.
Технологические операции при травлении выполняют в следующей последовательности [3]:
- обезжиривание в фосфатно-щелочном растворе;
- промывка в теплой (50°С) и затем холодной проточной воде;
- травление в надсернокислом аммонии в течение 10…20 с до
потемнения поверхности;
- промывка в воде и удаление шлама;
- осветление в растворе соляной кислоты и уротропина в течение
30…60 с;
- промывка в проточной воде и нейтрализация в 1…2%-ном растворе
углекислого натрия;
- антикоррозионная обработка в 7…10%-ном растворе нитрата натрия.
Толщина структурно измененного слоя различна по высоте зуба и в большинстве случаев максимальна на его головке. По высоте зуба от головки к ножке существенно уменьшается толщина вторично закаленного и отпущенного слоя, что видно из рис. 55. При повышенных режимах шлифования на поверхности зуба образуются глубокие местные прижоги; вторично закаленный слой в них лежит на слое отпущенного металла.
Рис. 55. Распределение прижогов по высоте зуба колеса из стали 12Х2Н4А после шлифования на станке 5831 на повышенном режиме [3]
Слайд 47ИЗМЕНЕНИЕ СВОЙСТВ ПОВЕРХНОСТНОГО СЛОЯ ЗУБЬЕВ ПРИ ШЛИФОВАНИИ С ПРИЖОГАМИ
Появление шлифовочных прижогов
ИЗМЕНЕНИЕ СВОЙСТВ ПОВЕРХНОСТНОГО СЛОЯ ЗУБЬЕВ ПРИ ШЛИФОВАНИИ С ПРИЖОГАМИ
Появление шлифовочных прижогов
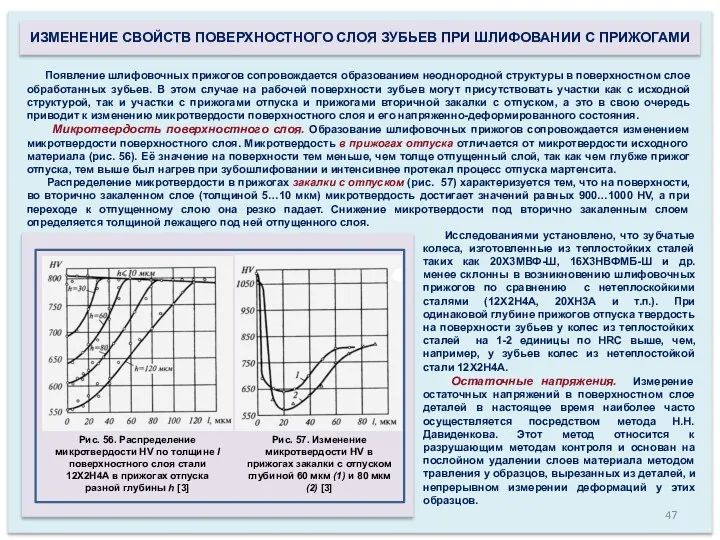
Микротвердость поверхностного слоя. Образование шлифовочных прижогов сопровождается изменением микротвердости поверхностного слоя. Микротвердость в прижогах отпуска отличается от микротвердости исходного материала (рис. 56). Её значение на поверхности тем меньше, чем толще отпущенный слой, так как чем глубже прижог отпуска, тем выше был нагрев при зубошлифовании и интенсивнее протекал процесс отпуска мартенсита.
Распределение микротвердости в прижогах закалки с отпуском (рис. 57) характеризуется тем, что на поверхности, во вторично закаленном слое (толщиной 5…10 мкм) микротвердость достигает значений равных 900…1000 HV, а при переходе к отпущенному слою она резко падает. Снижение микротвердости под вторично закаленным слоем определяется толщиной лежащего под ней отпущенного слоя.
Рис. 56. Распределение микротвердости HV по толщине l поверхностного слоя стали 12Х2Н4А в прижогах отпуска разной глубины h [3]
Рис. 57. Изменение микротвердости HV в прижогах закалки с отпуском глубиной 60 мкм (1) и 80 мкм (2) [3]
Исследованиями установлено, что зубчатые колеса, изготовленные из теплостойких сталей таких как 20Х3МВФ-Ш, 16Х3НВФМБ-Ш и др. менее склонны в возникновению шлифовочных прижогов по сравнению с нетеплоскойкими сталями (12Х2Н4А, 20ХН3А и т.п.). При одинаковой глубине прижогов отпуска твердость на поверхности зубьев у колес из теплостойких сталей на 1-2 единицы по HRC выше, чем, например, у зубьев колес из нетеплостойкой стали 12Х2Н4А.
Остаточные напряжения. Измерение остаточных напряжений в поверхностном слое деталей в настоящее время наиболее часто осуществляется посредством метода Н.Н. Давиденкова. Этот метод относится к разрушающим методам контроля и основан на послойном удалении слоев материала методом травления у образцов, вырезанных из деталей, и непрерывном измерении деформаций у этих образцов.
Слайд 48Рис. 58. Распределение остаточных напряжений по толщине l поверхностного слоя [3]:
а –
Рис. 58. Распределение остаточных напряжений по толщине l поверхностного слоя [3]:
а –
![Рис. 58. Распределение остаточных напряжений по толщине l поверхностного слоя [3]: а](/_ipx/f_webp&q_80&fit_contain&s_1440x1080/imagesDir/jpg/1132734/slide-47.jpg)
У зубчатых колес, обработанных на режиме, не вызывающем возникновение шлифовочных прижогов (рис. 58, а; графики 3-4), в поверхностном слое рабочих поверхностей зубьев в окружном (тангенциальном) направлении формируются либо небольшие остаточные напряжения сжатия, либо (чаще всего) остаточные напряжения растяжения величиной 100…300 МПа.
При шлифовании на интенсивных режимах, сопровождающихся возникновением шлифовочных прижогов (рис. 53, б; при t = 0,06 мм и t = 0,09 мм), в поверхностном слое зубьев формируются остаточные напряжения растяжения. Их величина и характер распределения будут зависеть от средней контактной температуры в зоне резания, а также скоростей нагрева и охлаждения обрабатываемых поверхностей заготовки. Возникающие при прижогах отпуска сорбит, троостит и троостомартенсит, а при прижогах вторичной закалки – остаточный аустенит имеют меньший удельный объем по сравнению с мартенситом, что способствует формированию в поверхностном слое зубьев остаточных напряжений растяжения.
Следует отметить, что остаточные напряжения на ножке зуба несколько меньше, чем, например, в зоне делительной окружности, что обусловлено меньшей температурой нагрева верхних слоев и меньшей толщиной структурно измененного слоя. Это связано с тем, что по мере приближения к ножке зуба увеличивается его масса и, следовательно, улучшаются условия отвода теплоты из зоны обработки.
Слайд 49 Влияние шлифовочных прижогов на выносливость зубьев при изгибе. Шлифовочные прижоги снижают
Влияние шлифовочных прижогов на выносливость зубьев при изгибе. Шлифовочные прижоги снижают
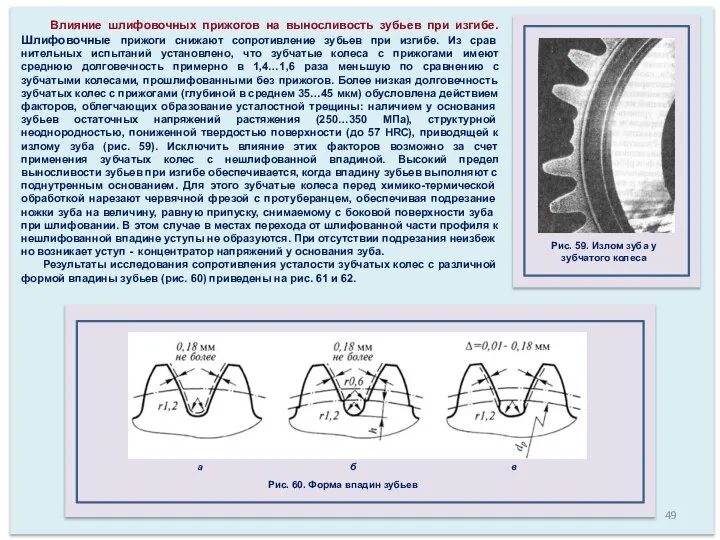
Результаты исследования сопротивления усталости зубчатых колес с различной формой впадины зубьев (рис. 60) приведены на рис. 61 и 62.
а б в
Рис. 60. Форма впадин зубьев
Рис. 59. Излом зуба у зубчатого колеса
Слайд 50Рис. 61. Кривые усталости зубчатых колес из стали 12Х2Н4А [3]:
1- с нешлифованной
Рис. 61. Кривые усталости зубчатых колес из стали 12Х2Н4А [3]:
1- с нешлифованной
![Рис. 61. Кривые усталости зубчатых колес из стали 12Х2Н4А [3]: 1- с](/_ipx/f_webp&q_80&fit_contain&s_1440x1080/imagesDir/jpg/1132734/slide-49.jpg)
Рис. 62. Кривые усталости зубчатых колес из стали 12Х2НВФА [3]:
1- с нешлифованной впадиной с выкружкой; 2 – со шлифованной впадиной
Как следует из кривых усталости, представленных на рис. 61 и 62, долговечность колес со шлифованной впадиной с поднутренным основанием зубьев в 2…2,5 раза выше, чем колес со шлифованной переходной кривой. Зубчатые колеса с нешлифованной впадиной с уступом у основания зуба не имеют преимущества со шлифованной переходной кривой. Линии усталости для этих двух типов колес практически совпадают. Усталостные разрушения колес с уступом, как правило, начинаются от имеющегося концентратора напряжений. Интенсивность влияния этого концентратора усиливают возникающие в месте уступа остаточные напряжения растяжения и шлифовочные прижоги.
Слайд 51ПРОГРЕССИВНЫЕ АБРАЗИВНЫЕ ИНСТРУМЕНТЫ ДЛЯ ЗУБОШЛИФОВАНИЯ
К прогрессивным абразивным инструментам, применяемым для процессов
ПРОГРЕССИВНЫЕ АБРАЗИВНЫЕ ИНСТРУМЕНТЫ ДЛЯ ЗУБОШЛИФОВАНИЯ
К прогрессивным абразивным инструментам, применяемым для процессов
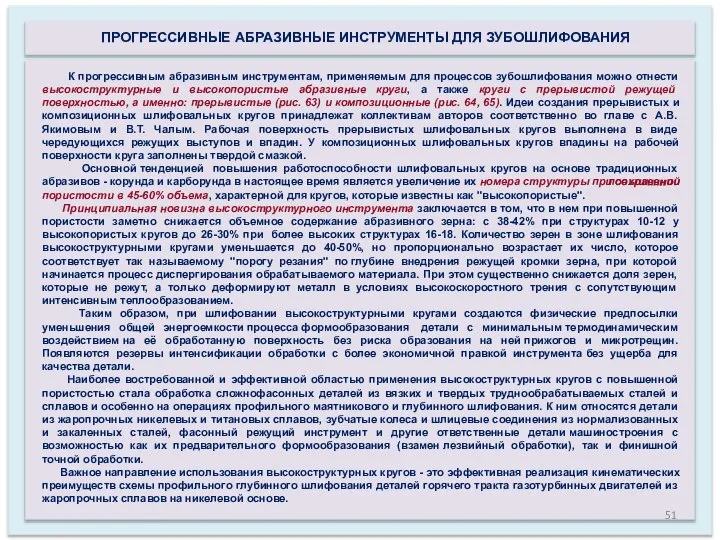
Основной тенденцией повышения работоспособности шлифовальных кругов на основе традиционных абразивов - корунда и карборунда в настоящее время является увеличение их номера структуры при сохранении повышенной пористости в 45-60% объема, характерной для кругов, которые известны как "высокопористые".
Принципиальная новизна высокоструктурного инструмента заключается в том, что в нем при повышенной пористости заметно снижается объемное содержание абразивного зерна: с 38-42% при структурах 10-12 у высокопористых кругов до 26-30% при более высоких структурах 16-18. Количество зерен в зоне шлифования высокоструктурными кругами уменьшается до 40-50%, но пропорционально возрастает их число, которое соответствует так называемому "порогу резания" по глубине внедрения режущей кромки зерна, при которой начинается процесс диспергирования обрабатываемого материала. При этом существенно снижается доля зерен, которые не режут, а только деформируют металл в условиях высокоскоростного трения с сопутствующим интенсивным теплообразованием.
Таким образом, при шлифовании высокоструктурными кругами создаются физические предпосылки уменьшения общей энергоемкости процесса формообразования детали с минимальным термодинамическим воздействием на её обработанную поверхность без риска образования на ней прижогов и микротрещин. Появляются резервы интенсификации обработки с более экономичной правкой инструмента без ущерба для качества детали.
Наиболее востребованной и эффективной областью применения высокоструктурных кругов с повышенной пористостью стала обработка сложнофасонных деталей из вязких и твердых труднообрабатываемых сталей и сплавов и особенно на операциях профильного маятникового и глубинного шлифования. К ним относятся детали из жаропрочных никелевых и титановых сплавов, зубчатые колеса и шлицевые соединения из нормализованных и закаленных сталей, фасонный режущий инструмент и другие ответственные детали машиностроения с возможностью как их предварительного формообразования (взамен лезвийный обработки), так и финишной точной обработки.
Важное направление использования высокоструктурных кругов - это эффективная реализация кинематических преимуществ схемы профильного глубинного шлифования деталей горячего тракта газотурбинных двигателей из жаропрочных сплавов на никелевой основе.
Слайд 52Рис. 63. Прерывистые шлифовальные круги:
а – цельный; б – составной (1 –
Рис. 63. Прерывистые шлифовальные круги:
а – цельный; б – составной (1 –
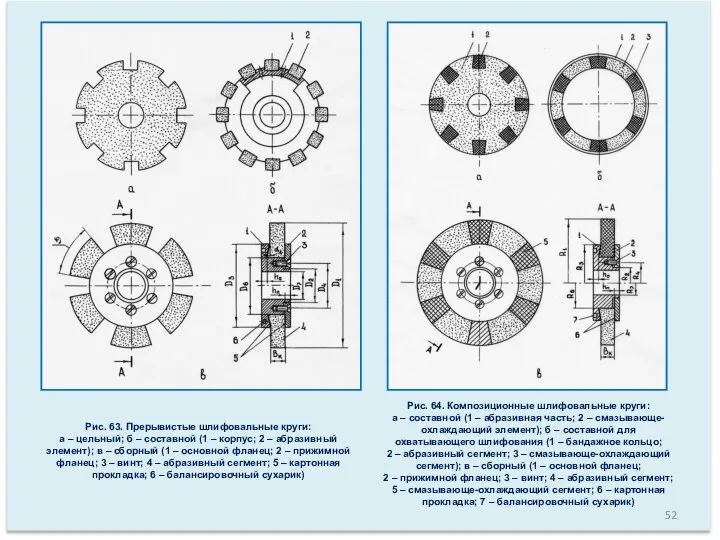
Рис. 64. Композиционные шлифовальные круги:
а – составной (1 – абразивная часть; 2 – смазывающе-охлаждающий элемент); б – составной для охватывающего шлифования (1 – бандажное кольцо; 2 – абразивный сегмент; 3 – смазывающе-охлаждающий сегмент); в – сборный (1 – основной фланец; 2 – прижимной фланец; 3 – винт; 4 – абразивный сегмент; 5 – смазывающе-охлаждающий сегмент; 6 – картонная прокладка; 7 – балансировочный сухарик)
Слайд 53Рис. 65. Сборный композиционный круг для профильного зубошлифования
Рис. 66. Схема работы абразивных
Рис. 65. Сборный композиционный круг для профильного зубошлифования
Рис. 66. Схема работы абразивных
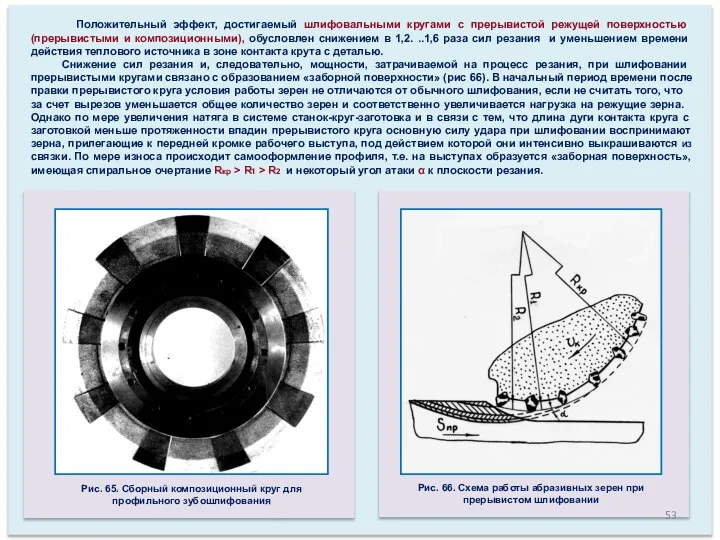
Положительный эффект, достигаемый шлифовальными кругами с прерывистой режущей поверхностью (прерывистыми и композиционными), обусловлен снижением в 1,2. ..1,6 раза сил резания и уменьшением времени действия теплового источника в зоне контакта крута с деталью.
Снижение сил резания и, следовательно, мощности, затрачиваемой на процесс резания, при шлифовании прерывистыми кругами связано с образованием «заборной поверхности» (рис 66). В начальный период времени после правки прерывистого круга условия работы зерен не отличаются от обычного шлифования, если не считать того, что за счет вырезов уменьшается общее количество зерен и соответственно увеличивается нагрузка на режущие зерна. Однако по мере увеличения натяга в системе станок-круг-заготовка и в связи с тем, что длина дуги контакта круга с заготовкой меньше протяженности впадин прерывистого круга основную силу удара при шлифовании воспринимают зерна, прилегающие к передней кромке рабочего выступа, под действием которой они интенсивно выкрашиваются из связки. По мере износа происходит самооформление профиля, т.е. на выступах образуется «заборная поверхность», имеющая спиральное очертание Rкр > R1 > R2 и некоторый угол атаки α к плоскости резания.
Слайд 54А это приводит к перераспределению глубины резания между зернами, т.е. к коренному
А это приводит к перераспределению глубины резания между зернами, т.е. к коренному
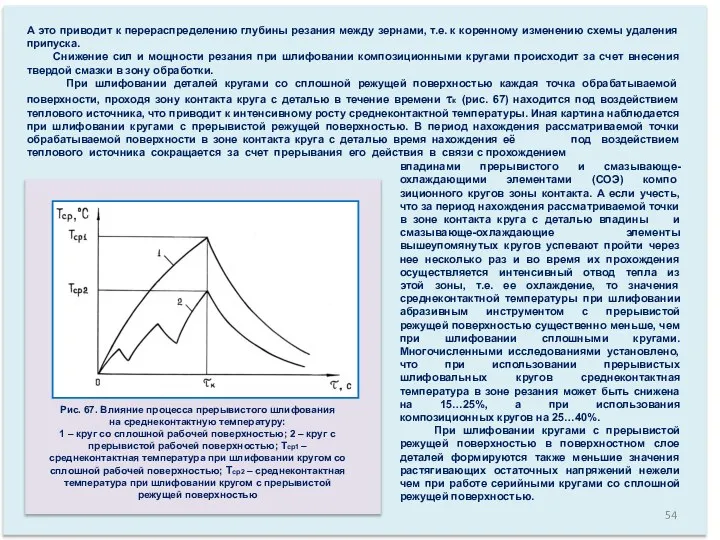
Снижение сил и мощности резания при шлифовании композиционными кругами происходит за счет внесения твердой смазки в зону обработки.
При шлифовании деталей кругами со сплошной режущей поверхностью каждая точка обрабатываемой поверхности, проходя зону контакта круга с деталью в течение времени τк (рис. 67) находится под воздействием теплового источника, что приводит к интенсивному росту среднеконтактной температуры. Иная картина наблюдается при шлифовании кругами с прерывистой режущей поверхностью. В период нахождения рассматриваемой точки обрабатываемой поверхности в зоне контакта круга с деталью время нахождения её под воздействием теплового источника сокращается за счет прерывания его действия в связи с прохождением
Рис. 67. Влияние процесса прерывистого шлифования на среднеконтактную температуру:
1 – круг со сплошной рабочей поверхностью; 2 – круг с прерывистой рабочей поверхностью; Тср1 – среднеконтактная температура при шлифовании кругом со сплошной рабочей поверхностью; Тср2 – среднеконтактная температура при шлифовании кругом с прерывистой режущей поверхностью
впадинами прерывистого и смазывающе-охлаждающими элементами (СОЭ) композиционного кругов зоны контакта. А если учесть, что за период нахождения рассматриваемой точки в зоне контакта круга с деталью впадины и смазывающе-охлаждающие элементы вышеупомянутых кругов успевают пройти через нее несколько раз и во время их прохождения осуществляется интенсивный отвод тепла из этой зоны, т.е. ее охлаждение, то значения среднеконтактной температуры при шлифовании абразивным инструментом с прерывистой режущей поверхностью существенно меньше, чем при шлифовании сплошными кругами. Многочисленными исследованиями установлено, что при использовании прерывистых шлифовальных кругов среднеконтактная температура в зоне резания может быть снижена на 15…25%, а при использования композиционных кругов на 25…40%.
При шлифовании кругами с прерывистой режущей поверхностью в поверхностном слое деталей формируются также меньшие значения растягивающих остаточных напряжений нежели чем при работе серийными кругами со сплошной режущей поверхностью.