Слайд 2Деформации и напряжения
общее понятие
Прочностью металла называют способность
его сопративлятся разрушению под действием сил.
Деформацией
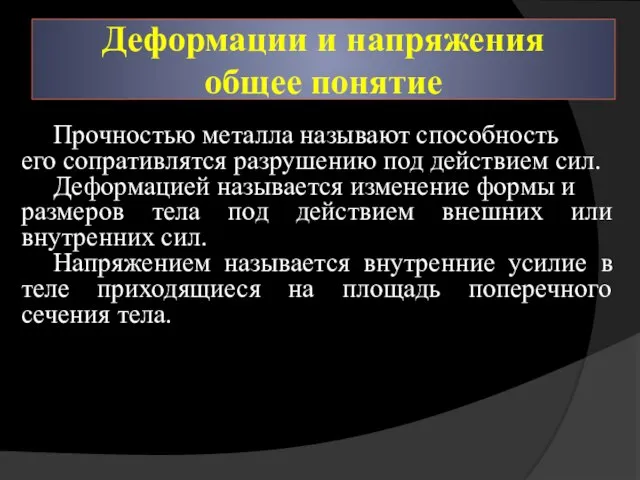
называется изменение формы и
размеров тела под действием внешних или внутренних сил.
Напряжением называется внутренние усилие в теле приходящиеся на площадь поперечного сечения тела.
Слайд 3Деформация и напряжения при сварке
Любой металл при нагревании расширяется, а при охлаждении
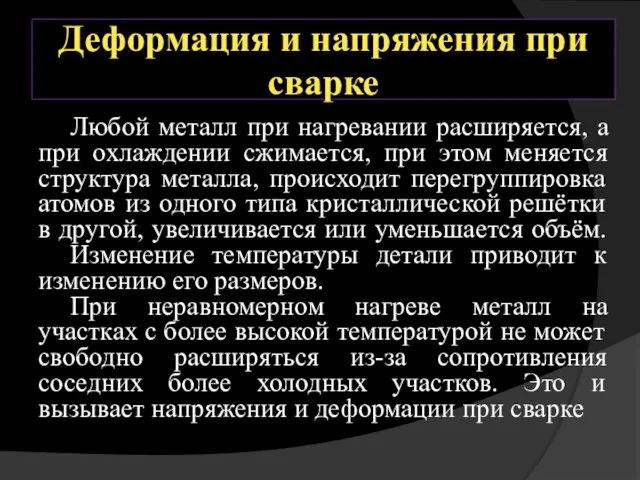
сжимается, при этом меняется структура металла, происходит перегруппировка атомов из одного типа кристаллической решётки в другой, увеличивается или уменьшается объём. Изменение температуры детали приводит к изменению его размеров.
При неравномерном нагреве металл на участках с более высокой температурой не может свободно расширяться из-за сопротивления соседних более холодных участков. Это и вызывает напряжения и деформации при сварке
Слайд 4Деформации при сварке
Деформации при сварке могут быть временные и остаточные, местные и
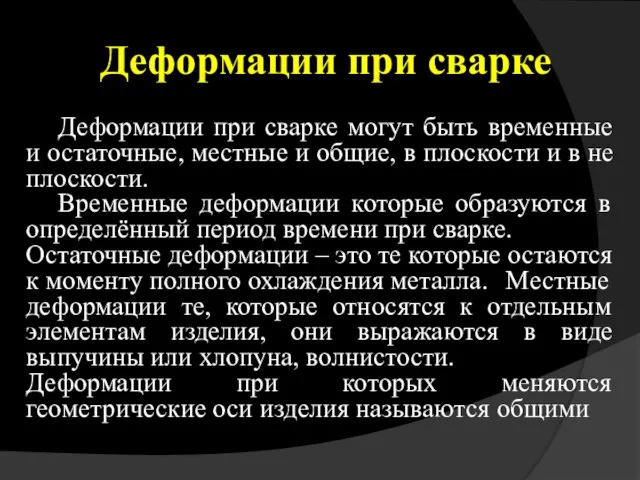
общие, в плоскости и в не плоскости.
Временные деформации которые образуются в определённый период времени при сварке. Остаточные деформации – это те которые остаются к моменту полного охлаждения металла. Местные деформации те, которые относятся к отдельным элементам изделия, они выражаются в виде выпучины или хлопуна, волнистости. Деформации при которых меняются геометрические оси изделия называются общими
Слайд 6Конструктивные способы борьбы со сварочными деформациями
1.Уменьшение сварных швов и их сечения
2. Симметричное
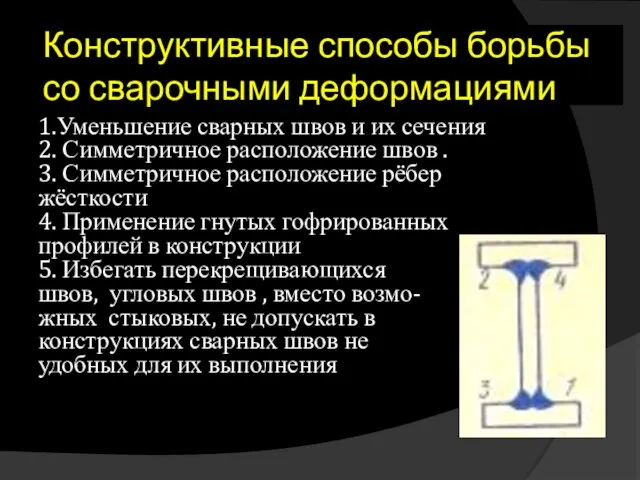
расположение швов .
3. Симметричное расположение рёбер
жёсткости
4. Применение гнутых гофрированных
профилей в конструкции
5. Избегать перекрещивающихся
швов, угловых швов , вместо возмо-
жных стыковых, не допускать в
конструкциях сварных швов не
удобных для их выполнения
Слайд 7Технологические способы по уменьшению деформации
1. Рациональная технология сборки и сварки.
2. Правильный выбор
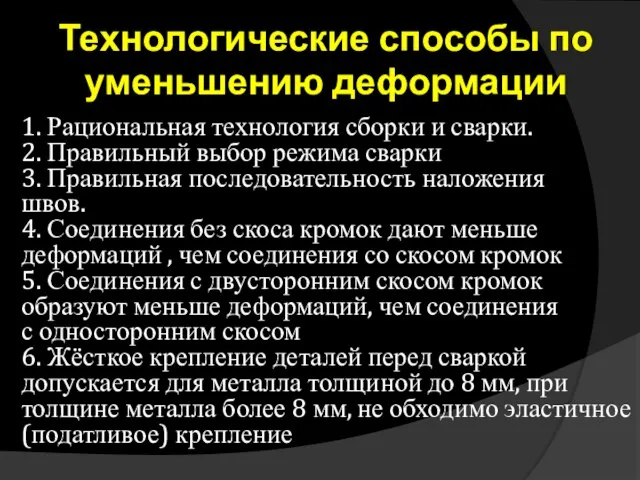
режима сварки
3. Правильная последовательность наложения
швов.
4. Соединения без скоса кромок дают меньше
деформаций , чем соединения со скосом кромок
5. Соединения с двусторонним скосом кромок
образуют меньше деформаций, чем соединения
с односторонним скосом
6. Жёсткое крепление деталей перед сваркой
допускается для металла толщиной до 8 мм, при
толщине металла более 8 мм, не обходимо эластичное (податливое) крепление
Слайд 8Технологические способы уменьшения деформаций
7. Применение предварительного подогрева для
Мало пластичных металлов, для сталей
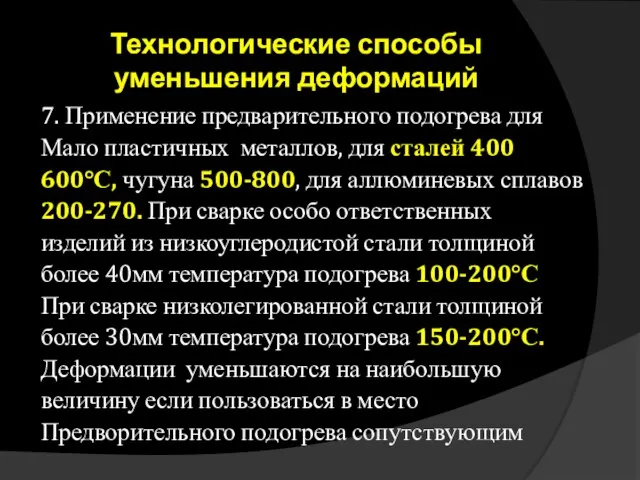
400
600°С, чугуна 500-800, для аллюминевых сплавов
200-270. При сварке особо ответственных
изделий из низкоуглеродистой стали толщиной
более 40мм температура подогрева 100-200°С
При сварке низколегированной стали толщиной
более 30мм температура подогрева 150-200°С.
Деформации уменьшаются на наибольшую
величину если пользоваться в место
Предворительного подогрева сопутствующим