Содержание
- 2. Тема:1 1.1.Кристаллические структуры металлов и сплавов Металлы и их сплавы в твердом состоянии представляют собой кристаллические
- 3. Тема:1 Рис. 1.1. Кристаллическое строение металлов: а - схема кристаллической решетки; б - объемно-центрированная кубическая; в
- 4. Тема:1 1.2. Дефекты строения реальных кристаллов Существующие в природе кристаллы, которые получили название реальных, не обладают
- 5. Тема:1 1.3. Кристаллизация металлов Кристаллизация обусловлена стремлением системы при определенных условиях перейти к энергетически более устойчивому
- 6. Тема:1 Рис. 1.3. Изменение свободной энергии F металла в жидком (Fж) и твердом (Fт) состоянии в
- 7. Тема:1 1.4. Полиморфизм металлов Существование разных типов кристаллических решеток у одного и того же вещества при
- 8. Тема:1 1.5. Основные сведения о металлических сплавах В жидком состоянии компоненты сплава в большинстве случаев полностью
- 9. Тема:1 1.6. Диаграммы состояния двойных сплавов Процесс кристаллизации металлических сплавов и связанные с ним закономерности их
- 10. Тема:1 Рис. 1.5. Диаграмма состояния I рода (а), кривые охлаждения сплавов I...V и схемы их структур
- 11. Тема:1 1.6.1. Диаграмма состояния для сплавов, компоненты которых нерастворимы в твердом состоянии (I рода) Компоненты сплава
- 12. Тема:1 1.6.2. Диаграмма состояния для сплавов, компоненты которых неограниченно растворимы в твердом состоянии (II рода) Оба
- 13. Тема:1 1.6.3. Диаграмма состояния для сплавов, компоненты которых ограниченно растворимы в твердом состоянии (III рода) Характерной
- 14. Тема:1 1.6.4. Диаграмма состояния для сплавов, компоненты которых образуют устойчивое химическое соединение (IV рода) Оба компонента
- 15. Тема:1 1.6.5. Связь между свойствами сплавов и типом диаграммы состояния Свойства сплавов зависят от их строения,
- 16. Тема:2 ДИАГРАММА СОСТОЯНИЯ ЖЕЛЕЗОУГЛЕРОДИСТЫХ СПЛАВОВ 2.1. Структурные составляющие сплавов железа с углеродом 2.2. Участок диаграммы состояния
- 17. Тема:2 2.1. Структурные составляющие сплавов железа с углеродом В технике наиболее широко применяют сплавы железа с
- 18. Тема:2 Рис. 1.9. Диаграмма состояния Fе - Fe3C
- 19. Тема:2 2.2. Участок диаграммы состояния Fе - Fе3С с концентрацией углерода 0 ... 2,14 % Рис.
- 20. Тема:2 2.3. Участок диаграммы состояния Fе - Fе3С с концентрацией углерода 2,14 ... 6,67 % Рис.
- 21. Тема:3 ТЕРМИЧЕСКАЯ ОБРАБОТКА 3.1. Основы термической обработки стали 3.1.1. Превращение перлита в аустенит и рост зерна
- 22. Тема:3 3.1. Основы термической обработки стали Термическая обработка заключается в нагреве изделий и заготовок до определенной
- 23. Тема:3 3.1.1. Превращение перлита в аустенит и рост зерна аустенита при нагреве При нагреве сталей выше
- 24. Тема:3 3.1.2. Превращения аустенита при охлаждении Если сталь со структурой аустенита охладить до температуры ниже Аr1,
- 25. Тема:3 3.1.3. Мартенситное превращение В доэвтектоидных сталях при температуре ниже Аr3 превращение аустенита начинается с выделения
- 26. Тема:3 3.1.4. Превращения мартенсита при нагреве Мартенсит и остаточный аустенит являются неравновесными фазами, которые при нагреве
- 27. Тема:3 3.2. Основные виды термической обработки стали Термическая обработка позволяет значительно изменить многие свойства металлов, особенно
- 28. Рис. 2.5. Режим отжига стали: а - полный; б -нормализационный Тема:3 3.2.1. Отжиг сталей Отжиг является
- 29. Тема:3 3.2.2. Закалка сталей Закалка является основным видом упрочняющей термической обработки сталей и чугунов. При закалке
- 30. Тема:3 3.2.3. Закаливаемость и прокаливаемостъ стали Важными характеристиками стали, необходимыми для назначения технологических режимов закалки, являются
- 31. Тема:3 3.2.4. Поверхностная закалка Поверхностной закалкой называют процесс термической обработки, заключающийся в нагреве поверхностного слоя изделия
- 32. Тема:3 3.2.5. Отпуск сталей Отпуском называют финишную термическую обработку, заключающуюся в нагреве закаленной стали до температур
- 33. Тема:3 3.3. Термомеханическая обработка стали Термомеханическая обработка (ТМО) стали заключается в сочетании пластической деформации стали в
- 34. Тема:3 3.4. Термическая обработка чугуна В чугунах, как и в сталях, в твердом состоянии происходят фазовые
- 35. Тема:3 3.5. Дефекты термической обработки стали При термической обработке стали могут возникнуть следующие дефекты: недостаточная твердость,
- 36. Тема: 4 ХИМИКО-ТЕРМИЧЕСКАЯ ОБРАБОТКА 4.1. Основы химико-термической обработки сталей 4.2. Цементация 4.3. Азотирование 4.4. Цианирование 4.5.
- 37. Тема: 4 4.1. Основы химико-термической обработки сталей Химико-термической обработкой называют технологический процесс заключающийся в диффузионном насыщении
- 38. Тема: 4 4.2. Цементация Цементацией называется технологический процесс диффузионного насыщения поверхности стальных изделий углеродом. Цементация применяется
- 39. Тема: 4 4.3. Азотирование Азотированием называется технологический процесс диффузионного насыщения поверхности стальных изделий азотом, в результате
- 40. Тема: 4 4.4. Цианирование Цианирование сталей заключается в поверхностном насыщении стальных изделий одновременно углеродом и азотом
- 41. Тема: 4 4.5. Диффузионная металлизация Диффузионное насыщение поверхностного слоя стальных изделий металлами - диффузионная металлизация -
- 42. Тема:5 УГЛЕРОДИСТЫЕ И ЛЕГИРОВАННЫЕ СТАЛИ 5.1. Влияние примесей на свойства сталей 5.2. Классификация сталей 5.3. Углеродистые
- 43. Тема:5 5.1. Влияние примесей на свойства сталей Свойства сталей зависят не только от их состава и
- 44. Тема:5 5.2. Классификация сталей Стали классифицируют по химическому составу, способу производства, назначению, качеству, степени раскисления, структуре
- 45. Тема:5 5.3. Углеродистые стали Углеродистые стали относятся к числу самых распространенных конструкционных материалов. Объем их производства
- 46. Тема:5 5.4. Легированные стали Основными легирующими элементами являются кремний, никель, марганец, хром. Такие элементы, как вольфрам,
- 47. Тема:5 5.4.1. Конструкционные стали Цементуемые стали обычно содержат 0,1 ... 0,25 % углерода, а в качестве
- 48. Тема:5 5.4.2. Инструментальные стали К инструментальным сталям относятся легированные стали повышенной прокаливаемости и специальные легированные стали
- 49. Тема:5 5.4.3. Стали специального назначения Коррозионно-стойкие (нержавеющие) стали относятся к специальным сталям и идут на изготовление
- 50. Тема:6 ЦВЕТНЫЕ МЕТАЛЛЫ И СПЛАВЫ 6.1. Общее понятие о цветных металлах 6.2. Алюминий и его сплавы
- 51. Тема:6 6.1. Общее понятие о цветных металлах Традиционно к цветным металлам относятся все металлы, кроме железа
- 52. Тема:6 6.2. Алюминий и его сплавы Алюминий имеет гранецентрированную кубическую решетку, которая не претерпевает полиморфных превращений
- 53. Тема:6 6.3. Магний и его сплавы Магний имеет низкую плотность (1,73 г/см3); у него гексагональная плотноупакованная
- 54. Тема:6 6.4. Медь и ее сплавы Медь - металл красного цвета, плотность которого составляет 8,9 г/см3,
- 55. Тема:6 6.5. Титан и его сплавы Титан по распространенности занимает четвертое место среди металлов, его содержание
- 56. Тема:7 КОМПОЗИЦИОННЫЕ МАТЕРИАЛЫ 7.1. Классификация композиционных материалов 7.2. Особенности получения КМ жидкофазными методами 7.3. Особенности получения
- 57. Тема:7 7.1. Классификация композиционных материалов Композиционными материалами (КМ) называют материалы, созданные из двух или более компонентов,
- 58. Рис. 2.7. Схема расположения упрочнителей в композиционных материалах: а - волокнистых; б - слоистых; в -
- 59. Тема:7 7.2. Особенности получения КМ жидкофазными методами Выбор метода получения КМ основан на анализе межфазного взаимодействия
- 60. Тема:7 7.3. Особенности получения КМ твердофазными методами В твердофазных методах получения КМ материал матрицы имеет вид
- 61. Тема:7 7.4. Методы и условия получения эвтектических КМ Эвтектическими КМ называют материалы, полученные кристаллизацией из сплавов
- 62. Тема:7 7.5. Технология изготовления дисперсно-упрочненных КМ Дисперсно-упрочненные КМ относятся к классу порошковых КМ. Упрочняющей фазой являются
- 63. Тема:7 7.6. Технология изготовления слоистых КМ Слоистые материалы в виде листов, труб, прутков, лент, заготовок изготавливают
- 65. Скачать презентацию
Слайд 2 Тема:1
1.1.Кристаллические структуры металлов и сплавов
Металлы и их сплавы в
Тема:1
1.1.Кристаллические структуры металлов и сплавов
Металлы и их сплавы в
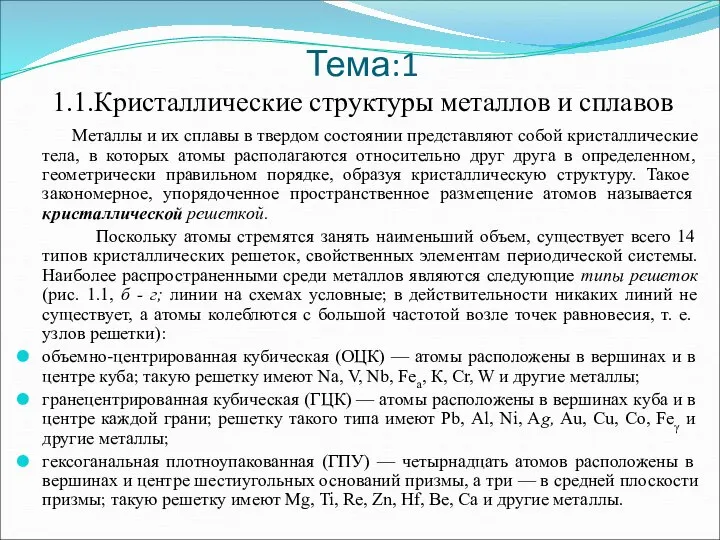
Поскольку атомы стремятся занять наименьший объем, существует всего 14 типов кристаллических решеток, свойственных элементам периодической системы. Наиболее распространенными среди металлов являются следующие типы решеток (рис. 1.1, б - г; линии на схемах условные; в действительности никаких линий не существует, а атомы колеблются с большой частотой возле точек равновесия, т. е. узлов решетки):
объемно-центрированная кубическая (ОЦК) — атомы расположены в вершинах и в центре куба; такую решетку имеют Nа, V, Nb, Fea, К, Сr, W и другие металлы;
гранецентрированная кубическая (ГЦК) — атомы расположены в вершинах куба и в центре каждой грани; решетку такого типа имеют Рb, Аl, Ni, Ag, Аu, Сu, Со, Feγ и другие металлы;
гексоганальная плотноупакованная (ГПУ) — четырнадцать атомов расположены в вершинах и центре шестиугольных оснований призмы, а три — в средней плоскости призмы; такую решетку имеют Мg, Ti, Rе, Zn, Нf, Ве, Са и другие металлы.
Слайд 3 Тема:1
Рис. 1.1. Кристаллическое строение металлов:
а - схема кристаллической решетки; б
Тема:1
Рис. 1.1. Кристаллическое строение металлов:
а - схема кристаллической решетки; б
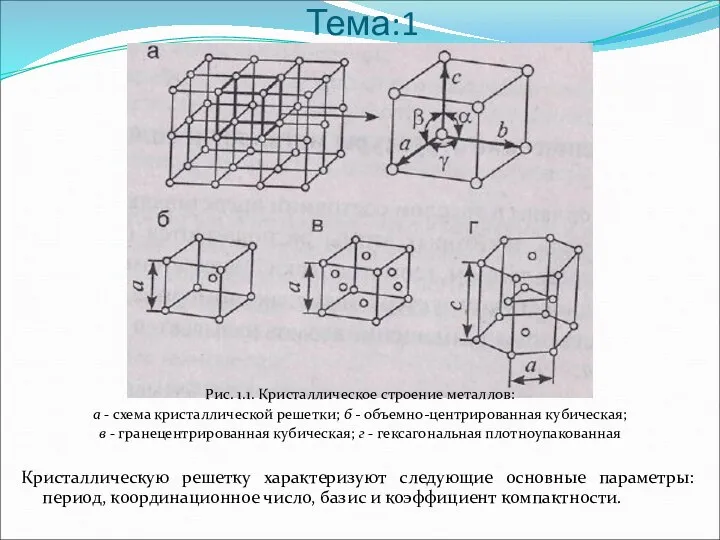
в - гранецентрированная кубическая; г - гексагональная плотноупакованная
Кристаллическую решетку характеризуют следующие основные параметры: период, координационное число, базис и коэффициент компактности.
Слайд 4 Тема:1
1.2. Дефекты строения реальных кристаллов
Существующие в природе кристаллы, которые
Тема:1
1.2. Дефекты строения реальных кристаллов
Существующие в природе кристаллы, которые
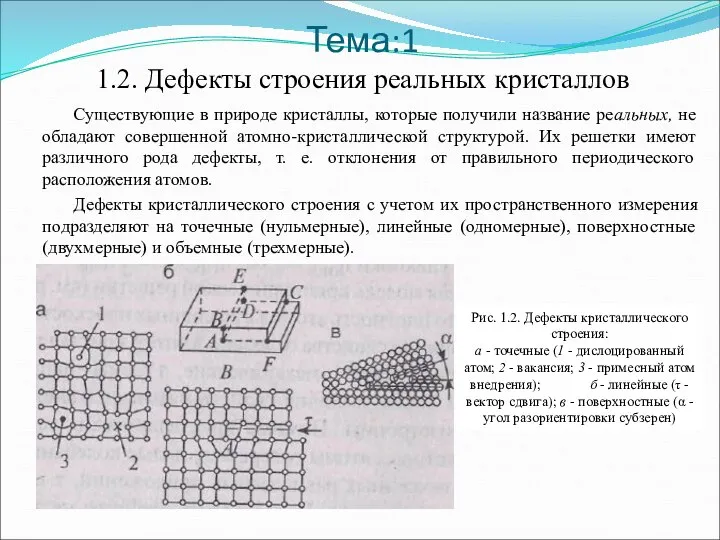
Дефекты кристаллического строения с учетом их пространственного измерения подразделяют на точечные (нульмерные), линейные (одномерные), поверхностные (двухмерные) и объемные (трехмерные).
Рис. 1.2. Дефекты кристаллического строения:
а - точечные (1 - дислоцированный атом; 2 - вакансия; 3 - примесный атом внедрения); б - линейные (τ - вектор сдвига); в - поверхностные (α - угол разориентировки субзерен)
Слайд 5 Тема:1 1.3. Кристаллизация металлов
Кристаллизация обусловлена стремлением системы при определенных условиях
Тема:1 1.3. Кристаллизация металлов
Кристаллизация обусловлена стремлением системы при определенных условиях

Слайд 6 Тема:1
Рис. 1.3. Изменение свободной энергии F металла в жидком (Fж)
Тема:1
Рис. 1.3. Изменение свободной энергии F металла в жидком (Fж)
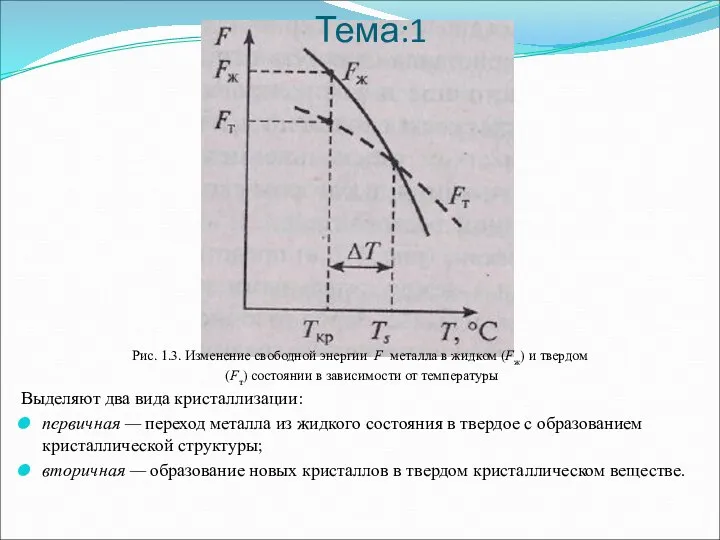
(Fт) состоянии в зависимости от температуры
Выделяют два вида кристаллизации:
первичная — переход металла из жидкого состояния в твердое с образованием кристаллической структуры;
вторичная — образование новых кристаллов в твердом кристаллическом веществе.
Слайд 7 Тема:1
1.4. Полиморфизм металлов
Существование разных типов кристаллических решеток у одного
Тема:1
1.4. Полиморфизм металлов
Существование разных типов кристаллических решеток у одного
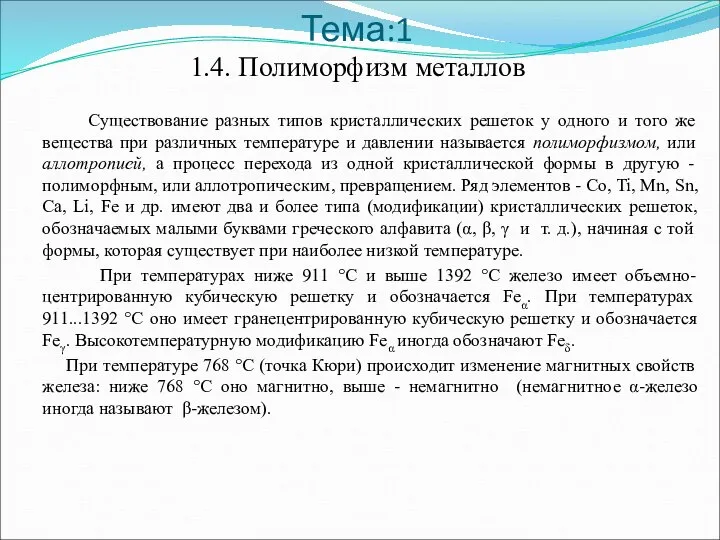
При температурах ниже 911 °С и выше 1392 °С железо имеет объемно-центрированную кубическую решетку и обозначается Fеα. При температурах 911...1392 °С оно имеет гранецентрированную кубическую решетку и обозначается Fеγ. Высокотемпературную модификацию Fеα иногда обозначают Fеδ.
При температуре 768 °С (точка Кюри) происходит изменение магнитных свойств железа: ниже 768 °С оно магнитно, выше - немагнитно (немагнитное α-железо иногда называют β-железом).
Слайд 8 Тема:1
1.5. Основные сведения о металлических сплавах
В жидком состоянии компоненты
Тема:1
1.5. Основные сведения о металлических сплавах
В жидком состоянии компоненты
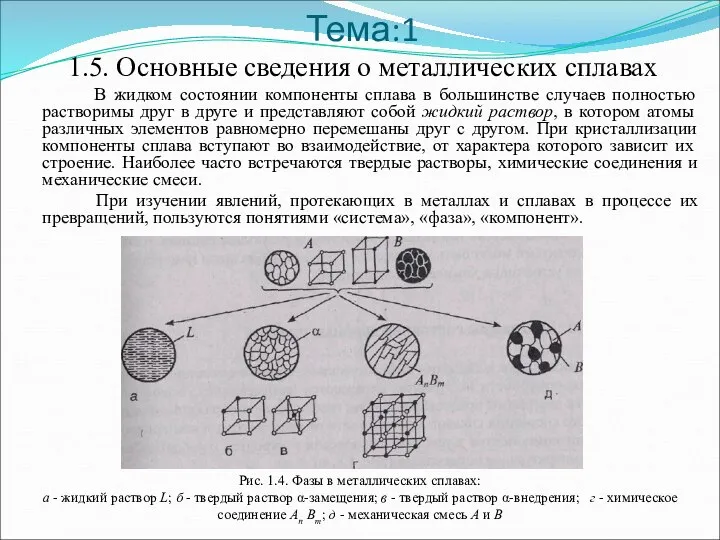
При изучении явлений, протекающих в металлах и сплавах в процессе их превращений, пользуются понятиями «система», «фаза», «компонент».
Рис. 1.4. Фазы в металлических сплавах:
а - жидкий раствор L; б - твердый раствор α-замещения; в - твердый раствор α-внедрения; г - химическое соединение Аn Вm; д - механическая смесь А и В
Слайд 9 Тема:1
1.6. Диаграммы состояния двойных сплавов
Процесс кристаллизации металлических сплавов и
Тема:1
1.6. Диаграммы состояния двойных сплавов
Процесс кристаллизации металлических сплавов и
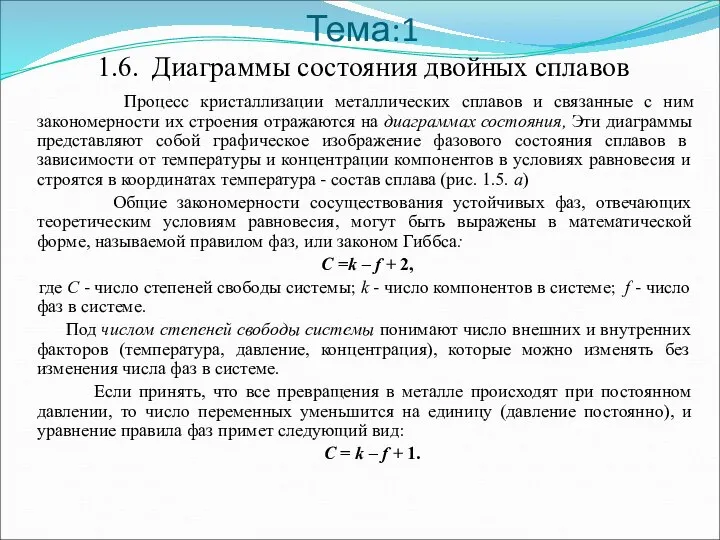
Общие закономерности сосуществования устойчивых фаз, отвечающих теоретическим условиям равновесия, могут быть выражены в математической форме, называемой правилом фаз, или законом Гиббса:
С =k – f + 2,
где С - число степеней свободы системы; k - число компонентов в системе; f - число фаз в системе.
Под числом степеней свободы системы понимают число внешних и внутренних факторов (температура, давление, концентрация), которые можно изменять без изменения числа фаз в системе.
Если принять, что все превращения в металле происходят при постоянном давлении, то число переменных уменьшится на единицу (давление постоянно), и уравнение правила фаз примет следующий вид:
С = k – f + 1.
Слайд 10 Тема:1
Рис. 1.5. Диаграмма состояния I рода (а), кривые охлаждения сплавов
Тема:1
Рис. 1.5. Диаграмма состояния I рода (а), кривые охлаждения сплавов
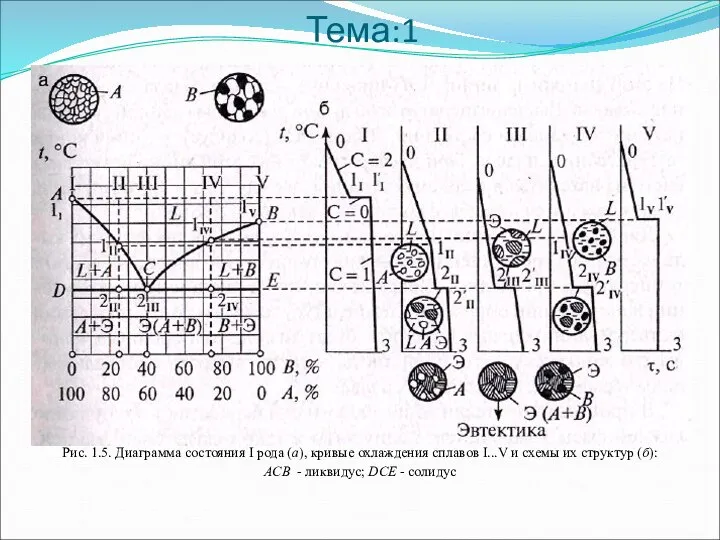
АСВ - ликвидус; DСЕ - солидус
Слайд 11 Тема:1
1.6.1. Диаграмма состояния для сплавов, компоненты которых нерастворимы в твердом
Тема:1 1.6.1. Диаграмма состояния для сплавов, компоненты которых нерастворимы в твердом
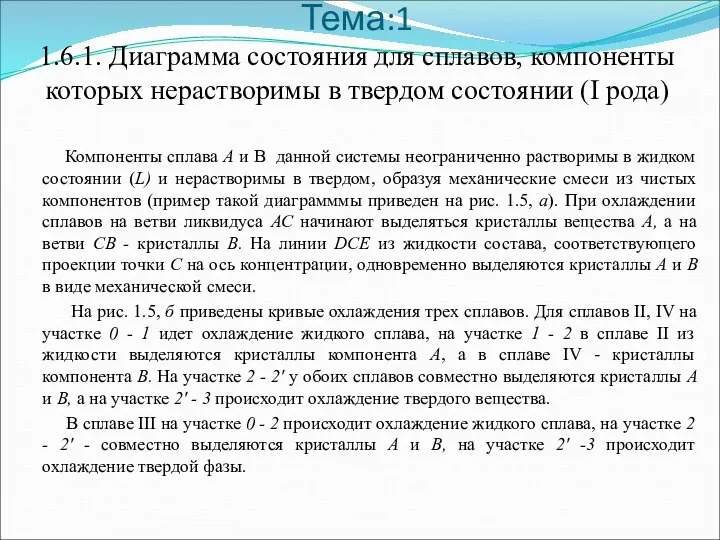
Компоненты сплава А и B данной системы неограниченно растворимы в жидком состоянии (L) и нерастворимы в твердом, образуя механические смеси из чистых компонентов (пример такой диаграмммы приведен на рис. 1.5, а). При охлаждении сплавов на ветви ликвидуса АС начинают выделяться кристаллы вещества А, а на ветви СВ - кристаллы В. На линии DСЕ из жидкости состава, соответствующего проекции точки С на ось концентрации, одновременно выделяются кристаллы А и В в виде механической смеси.
На рис. 1.5, б приведены кривые охлаждения трех сплавов. Для сплавов II, IV на участке 0 - 1 идет охлаждение жидкого сплава, на участке 1 - 2 в сплаве II из жидкости выделяются кристаллы компонента A, а в сплаве IV - кристаллы компонента В. На участке 2 - 2' у обоих сплавов совместно выделяются кристаллы А и В, а на участке 2' - 3 происходит охлаждение твердого вещества.
В сплаве III на участке 0 - 2 происходит охлаждение жидкого сплава, на участке 2 - 2' - совместно выделяются кристаллы А и В, на участке 2' -3 происходит охлаждение твердой фазы.
Слайд 12 Тема:1
1.6.2. Диаграмма состояния для сплавов, компоненты которых неограниченно растворимы в
Тема:1 1.6.2. Диаграмма состояния для сплавов, компоненты которых неограниченно растворимы в
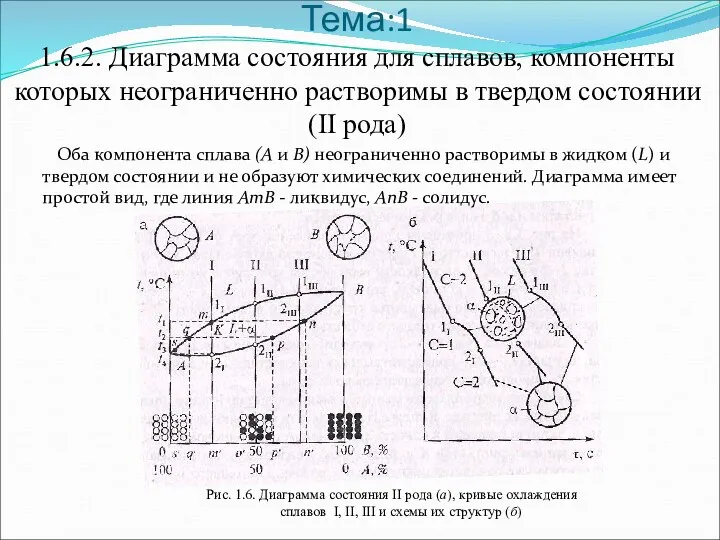
Оба компонента сплава (А и В) неограниченно растворимы в жидком (L) и твердом состоянии и не образуют химических соединений. Диаграмма имеет простой вид, где линия АтВ - ликвидус, AпВ - солидус.
Рис. 1.6. Диаграмма состояния II рода (а), кривые охлаждения
сплавов I, II, III и схемы их структур (б)
Слайд 13 Тема:1
1.6.3. Диаграмма состояния для сплавов, компоненты которых ограниченно растворимы в
Тема:1 1.6.3. Диаграмма состояния для сплавов, компоненты которых ограниченно растворимы в
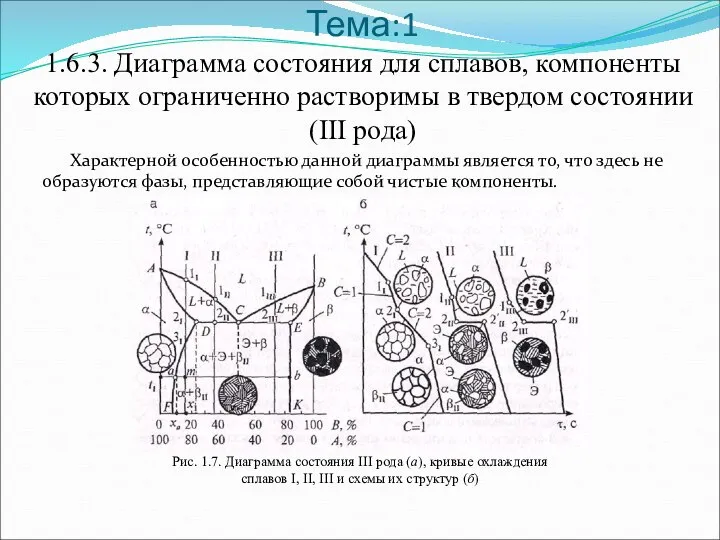
Характерной особенностью данной диаграммы является то, что здесь не образуются фазы, представляющие собой чистые компоненты.
Рис. 1.7. Диаграмма состояния III рода (а), кривые охлаждения
сплавов I, II, III и схемы их структур (б)
Слайд 14 Тема:1
1.6.4. Диаграмма состояния для сплавов, компоненты которых образуют устойчивое химическое
Тема:1 1.6.4. Диаграмма состояния для сплавов, компоненты которых образуют устойчивое химическое
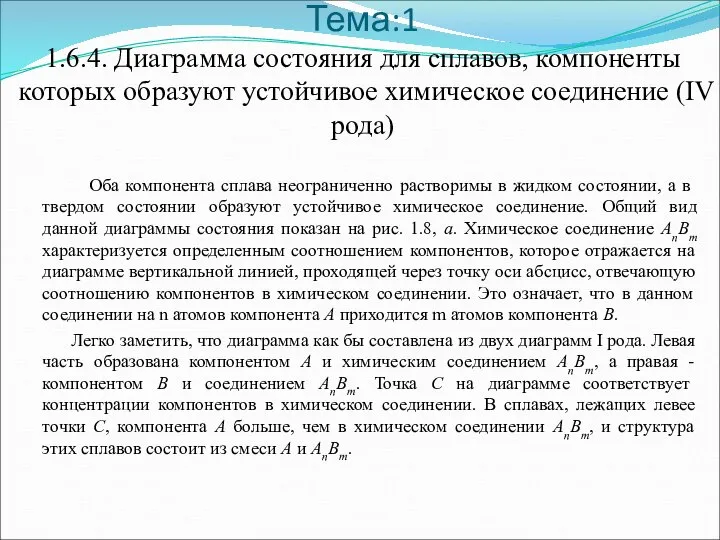
Оба компонента сплава неограниченно растворимы в жидком состоянии, а в твердом состоянии образуют устойчивое химическое соединение. Общий вид данной диаграммы состояния показан на рис. 1.8, а. Химическое соединение АnВm характеризуется определенным соотношением компонентов, которое отражается на диаграмме вертикальной линией, проходящей через точку оси абсцисс, отвечающую соотношению компонентов в химическом соединении. Это означает, что в данном соединении на n атомов компонента А приходится m атомов компонента В.
Легко заметить, что диаграмма как бы составлена из двух диаграмм I рода. Левая часть образована компонентом А и химическим соединением АnВm, а правая - компонентом В и соединением АnВm. Точка С на диаграмме соответствует концентрации компонентов в химическом соединении. В сплавах, лежащих левее точки С, компонента А больше, чем в химическом соединении АnВm, и структура этих сплавов состоит из смеси А и АnВm.
Слайд 15 Тема:1
1.6.5. Связь между свойствами сплавов и типом диаграммы состояния
Тема:1
1.6.5. Связь между свойствами сплавов и типом диаграммы состояния
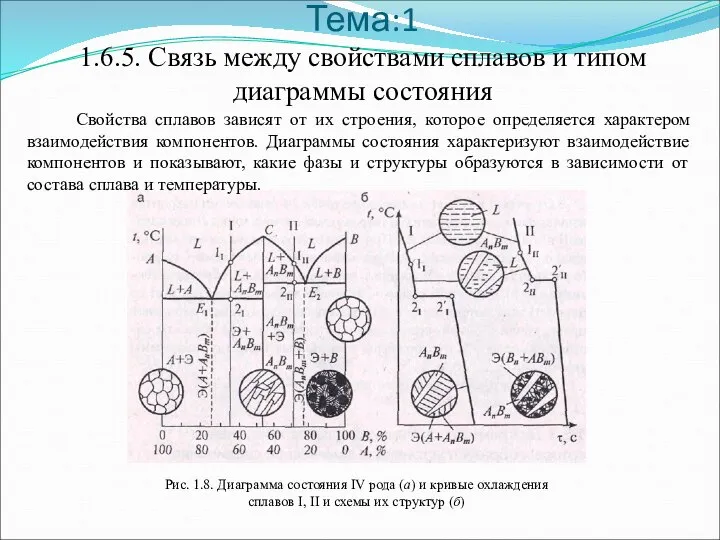
Рис. 1.8. Диаграмма состояния IV рода (а) и кривые охлаждения
сплавов I, II и схемы их структур (б)
Слайд 16 Тема:2
ДИАГРАММА СОСТОЯНИЯ ЖЕЛЕЗОУГЛЕРОДИСТЫХ
СПЛАВОВ
2.1. Структурные составляющие сплавов железа с углеродом
2.2.
Тема:2
ДИАГРАММА СОСТОЯНИЯ ЖЕЛЕЗОУГЛЕРОДИСТЫХ
СПЛАВОВ
2.1. Структурные составляющие сплавов железа с углеродом
2.2.
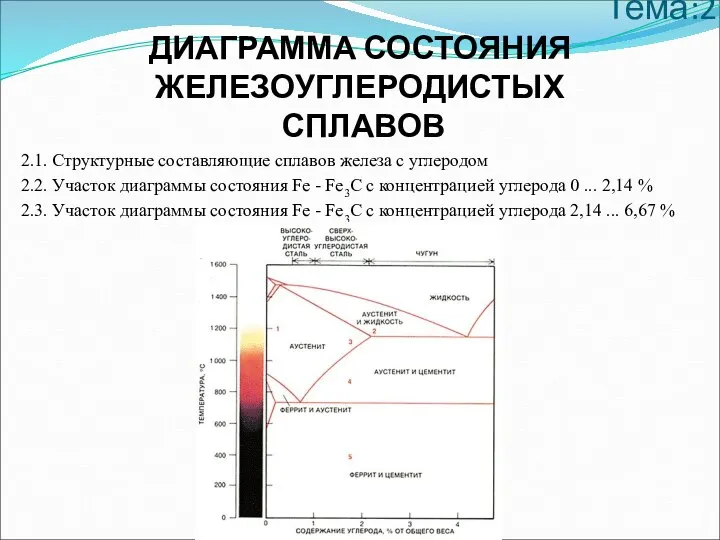
2.3. Участок диаграммы состояния Fе - Fе3С с концентрацией углерода 2,14 ... 6,67 %
Слайд 17 Тема:2
2.1. Структурные составляющие сплавов железа с углеродом
В технике наиболее
Тема:2
2.1. Структурные составляющие сплавов железа с углеродом
В технике наиболее
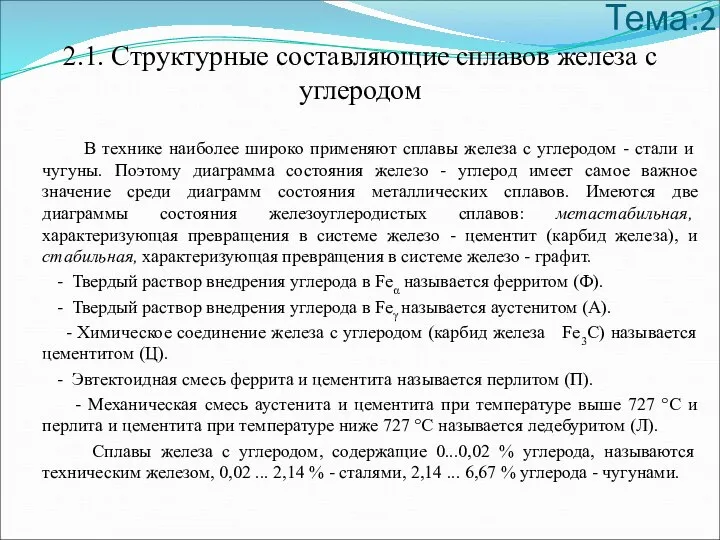
- Твердый раствор внедрения углерода в Fеα называется ферритом (Ф).
- Твердый раствор внедрения углерода в Fеγ называется аустенитом (А).
- Химическое соединение железа с углеродом (карбид железа Fе3С) называется цементитом (Ц).
- Эвтектоидная смесь феррита и цементита называется перлитом (П).
- Механическая смесь аустенита и цементита при температуре выше 727 °С и перлита и цементита при температуре ниже 727 °С называется ледебуритом (Л).
Сплавы железа с углеродом, содержащие 0...0,02 % углерода, называются техническим железом, 0,02 ... 2,14 % - сталями, 2,14 ... 6,67 % углерода - чугунами.
Слайд 18 Тема:2
Рис. 1.9. Диаграмма состояния Fе - Fe3C
Тема:2
Рис. 1.9. Диаграмма состояния Fе - Fe3C
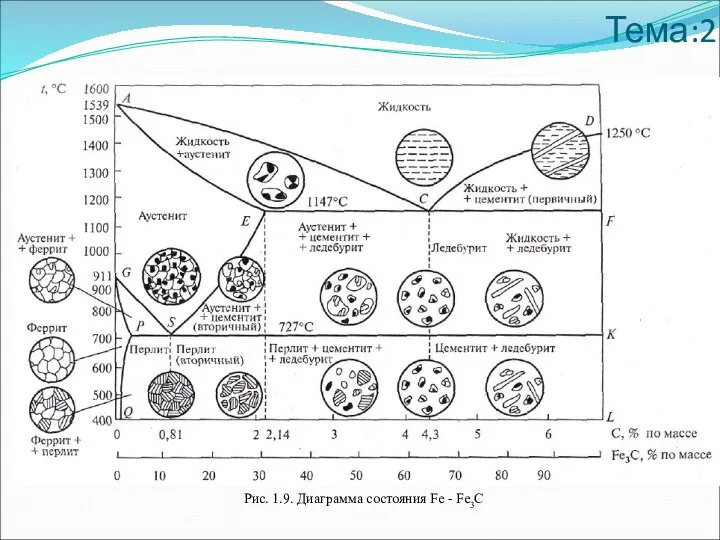
Слайд 19 Тема:2
2.2. Участок диаграммы состояния Fе - Fе3С с концентрацией углерода
Тема:2 2.2. Участок диаграммы состояния Fе - Fе3С с концентрацией углерода
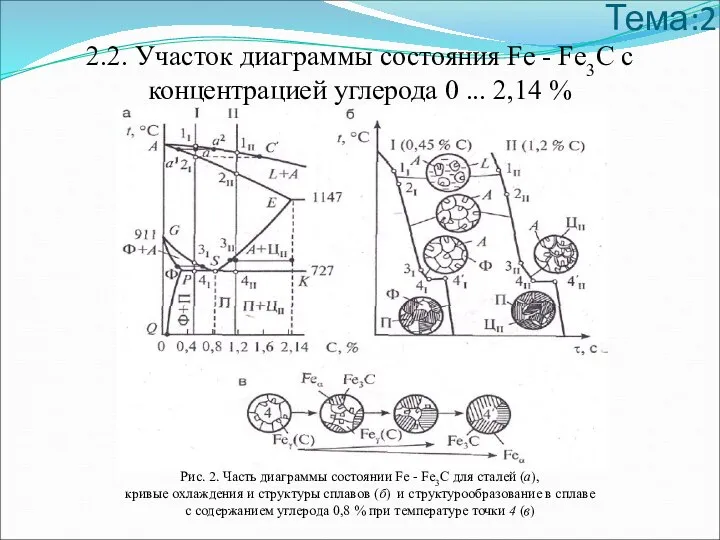
Рис. 2. Часть диаграммы состоянии Fе - Fе3С для сталей (а),
кривые охлаждения и структуры сплавов (б) и структурообразование в сплаве с содержанием углерода 0,8 % при температуре точки 4 (в)
Слайд 20 Тема:2
2.3. Участок диаграммы состояния Fе - Fе3С с концентрацией углерода
Тема:2 2.3. Участок диаграммы состояния Fе - Fе3С с концентрацией углерода
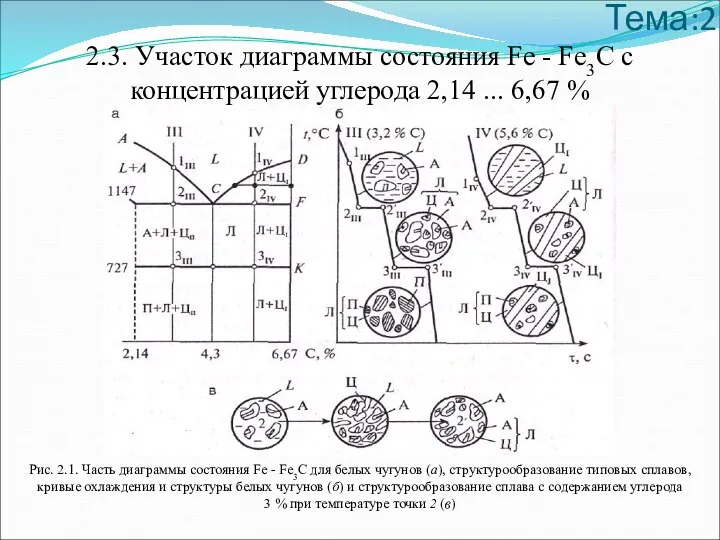
Рис. 2.1. Часть диаграммы состояния Fе - Fе3С для белых чугунов (а), структурообразование типовых сплавов, кривые охлаждения и структуры белых чугунов (б) и структурообразование сплава с содержанием углерода 3 % при температуре точки 2 (в)
Слайд 21 Тема:3
ТЕРМИЧЕСКАЯ ОБРАБОТКА
3.1. Основы термической обработки стали
3.1.1. Превращение перлита в аустенит
Тема:3
ТЕРМИЧЕСКАЯ ОБРАБОТКА
3.1. Основы термической обработки стали
3.1.1. Превращение перлита в аустенит
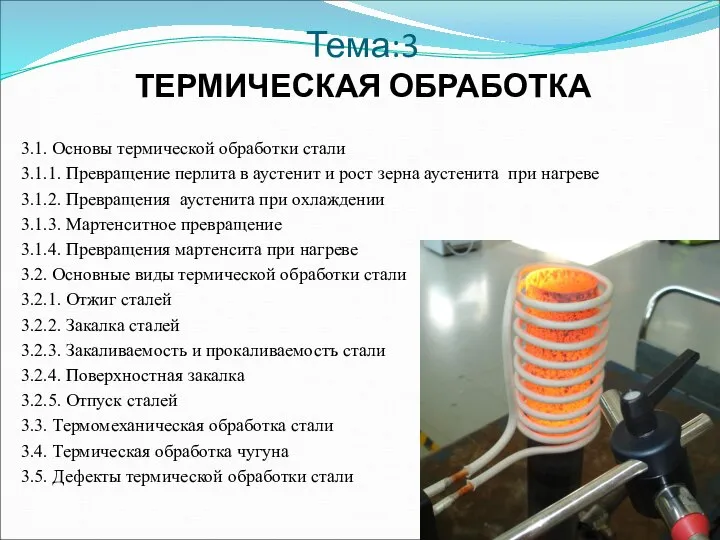
3.1.2. Превращения аустенита при охлаждении
3.1.3. Мартенситное превращение
3.1.4. Превращения мартенсита при нагреве
3.2. Основные виды термической обработки стали
3.2.1. Отжиг сталей
3.2.2. Закалка сталей
3.2.3. Закаливаемость и прокаливаемостъ стали
3.2.4. Поверхностная закалка
3.2.5. Отпуск сталей
3.3. Термомеханическая обработка стали
3.4. Термическая обработка чугуна
3.5. Дефекты термической обработки стали
Слайд 22 Тема:3
3.1. Основы термической обработки стали
Термическая обработка заключается в нагреве
Тема:3
3.1. Основы термической обработки стали
Термическая обработка заключается в нагреве
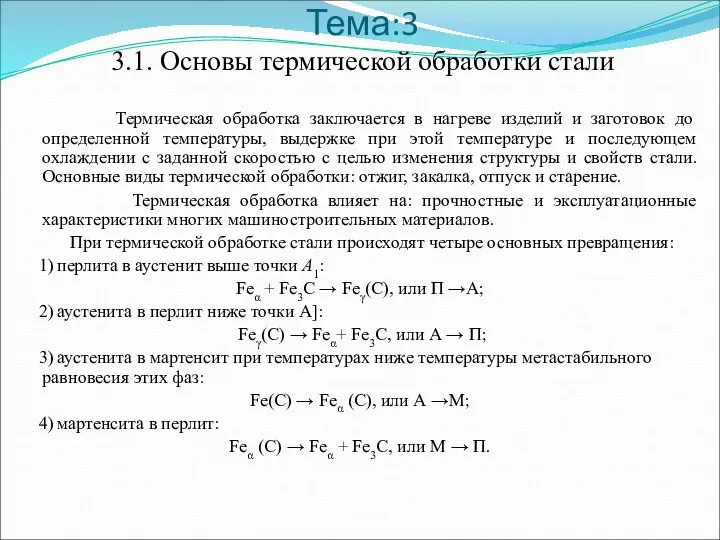
Термическая обработка влияет на: прочностные и эксплуатационные характеристики многих машиностроительных материалов.
При термической обработке стали происходят четыре основных превращения:
1) перлита в аустенит выше точки A1:
Fеα + Fе3С → Fеγ(С), или П →А;
2) аустенита в перлит ниже точки А]:
Fеγ(С) → Fеα+ Fе3С, или А → П;
3) аустенита в мартенсит при температурах ниже температуры метастабильного равновесия этих фаз:
Fе(С) → Fеα (С), или А →М;
4) мартенсита в перлит:
Fеα (С) → Fеα + Fе3С, или М → П.
Слайд 23 Тема:3
3.1.1. Превращение перлита в аустенит и рост зерна аустенита при
Тема:3 3.1.1. Превращение перлита в аустенит и рост зерна аустенита при
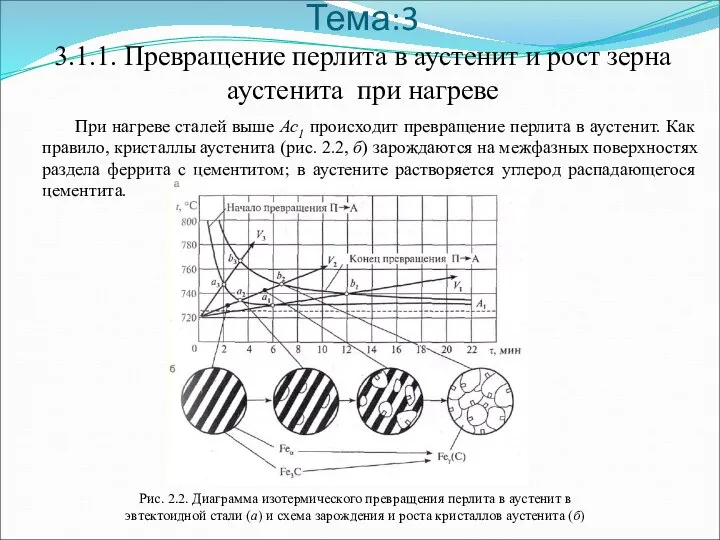
При нагреве сталей выше Ас1 происходит превращение перлита в аустенит. Как правило, кристаллы аустенита (рис. 2.2, б) зарождаются на межфазных поверхностях раздела феррита с цементитом; в аустените растворяется углерод распадающегося цементита.
Рис. 2.2. Диаграмма изотермического превращения перлита в аустенит в
эвтектоидной стали (а) и схема зарождения и роста кристаллов аустенита (б)
Слайд 24 Тема:3
3.1.2. Превращения аустенита при охлаждении
Если сталь со структурой аустенита
Тема:3
3.1.2. Превращения аустенита при охлаждении
Если сталь со структурой аустенита
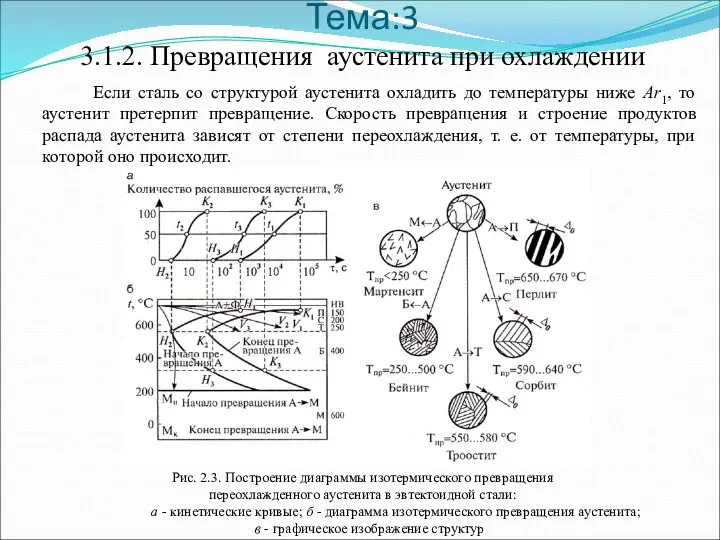
Рис. 2.3. Построение диаграммы изотермического превращения
переохлажденного аустенита в эвтектоидной стали:
а - кинетические кривые; б - диаграмма изотермического превращения аустенита;
в - графическое изображение структур
Слайд 25 Тема:3
3.1.3. Мартенситное превращение
В доэвтектоидных сталях при температуре ниже Аr3
Тема:3
3.1.3. Мартенситное превращение
В доэвтектоидных сталях при температуре ниже Аr3
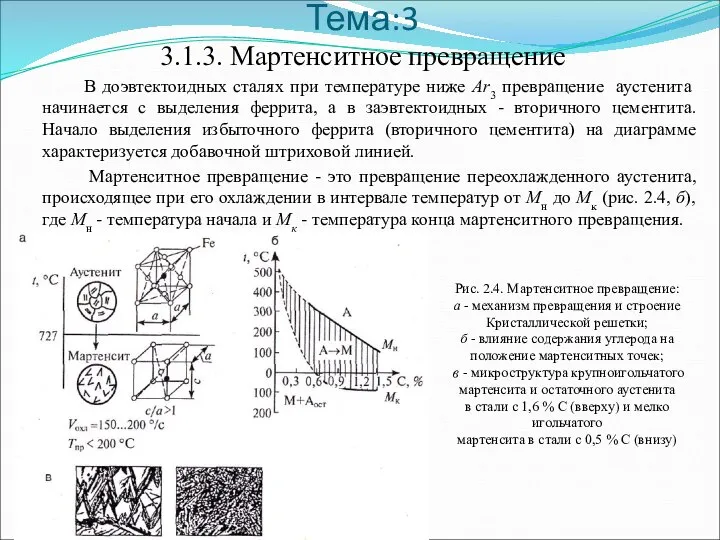
Мартенситное превращение - это превращение переохлажденного аустенита, происходящее при его охлаждении в интервале температур от Мн до Мк (рис. 2.4, б), где Мн - температура начала и Мк - температура конца мартенситного превращения.
Рис. 2.4. Мартенситное превращение:
а - механизм превращения и строение
Кристаллической решетки;
б - влияние содержания углерода на
положение мартенситных точек;
в - микроструктура крупноигольчатого
мартенсита и остаточного аустенита
в стали с 1,6 % С (вверху) и мелко игольчатого
мартенсита в стали с 0,5 % С (внизу)
Слайд 26 Тема:3
3.1.4. Превращения мартенсита при нагреве
Мартенсит и остаточный аустенит являются
Тема:3
3.1.4. Превращения мартенсита при нагреве
Мартенсит и остаточный аустенит являются
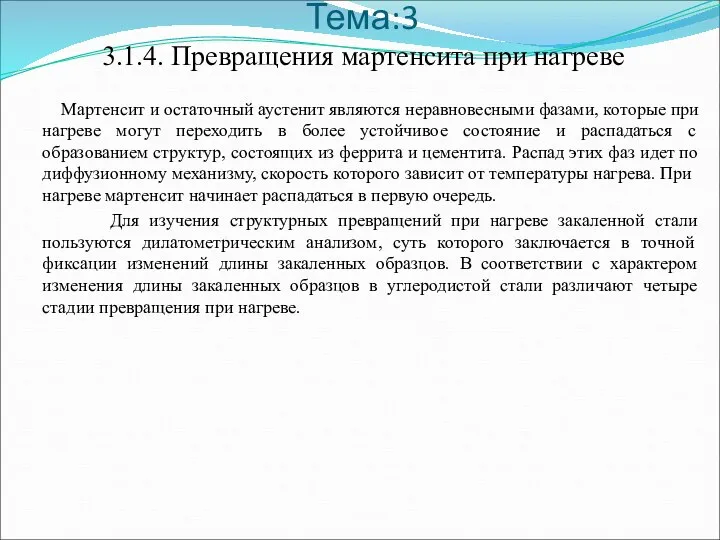
Для изучения структурных превращений при нагреве закаленной стали пользуются дилатометрическим анализом, суть которого заключается в точной фиксации изменений длины закаленных образцов. В соответствии с характером изменения длины закаленных образцов в углеродистой стали различают четыре стадии превращения при нагреве.
Слайд 27 Тема:3
3.2. Основные виды термической обработки стали
Термическая обработка позволяет значительно
Тема:3
3.2. Основные виды термической обработки стали
Термическая обработка позволяет значительно
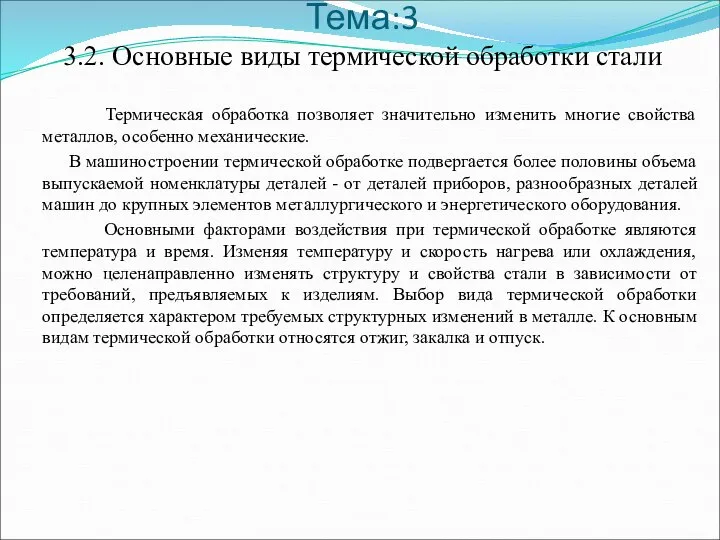
В машиностроении термической обработке подвергается более половины объема выпускаемой номенклатуры деталей - от деталей приборов, разнообразных деталей машин до крупных элементов металлургического и энергетического оборудования.
Основными факторами воздействия при термической обработке являются температура и время. Изменяя температуру и скорость нагрева или охлаждения, можно целенаправленно изменять структуру и свойства стали в зависимости от требований, предъявляемых к изделиям. Выбор вида термической обработки определяется характером требуемых структурных изменений в металле. К основным видам термической обработки относятся отжиг, закалка и отпуск.
Слайд 28Рис. 2.5. Режим отжига стали:
а - полный; б -нормализационный
Тема:3 3.2.1.
Рис. 2.5. Режим отжига стали:
а - полный; б -нормализационный
Тема:3 3.2.1.
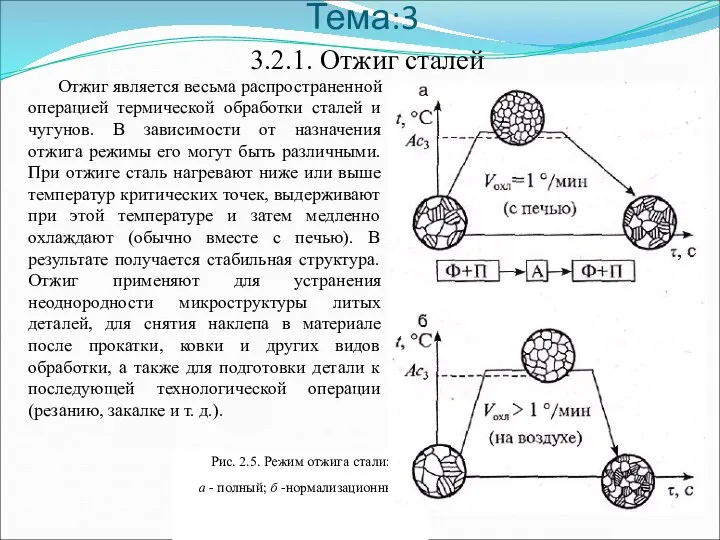
Отжиг является весьма распространенной операцией термической обработки сталей и чугунов. В зависимости от назначения отжига режимы его могут быть различными. При отжиге сталь нагревают ниже или выше температур критических точек, выдерживают при этой температуре и затем медленно охлаждают (обычно вместе с печью). В результате получается стабильная структура. Отжиг применяют для устранения неоднородности микроструктуры литых деталей, для снятия наклепа в материале после прокатки, ковки и других видов обработки, а также для подготовки детали к последующей технологической операции (резанию, закалке и т. д.).
Слайд 29 Тема:3
3.2.2. Закалка сталей
Закалка является основным видом упрочняющей термической обработки
Тема:3
3.2.2. Закалка сталей
Закалка является основным видом упрочняющей термической обработки
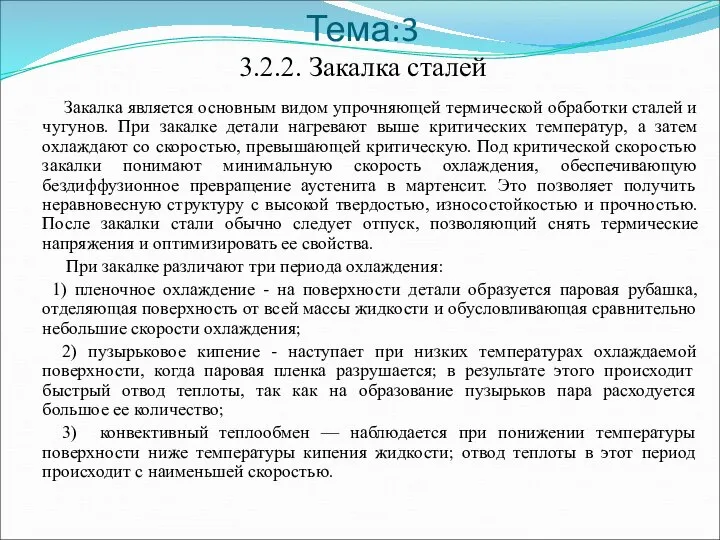
При закалке различают три периода охлаждения:
1) пленочное охлаждение - на поверхности детали образуется паровая рубашка, отделяющая поверхность от всей массы жидкости и обусловливающая сравнительно небольшие скорости охлаждения;
2) пузырьковое кипение - наступает при низких температурах охлаждаемой поверхности, когда паровая пленка разрушается; в результате этого происходит быстрый отвод теплоты, так как на образование пузырьков пара расходуется большое ее количество;
3) конвективный теплообмен — наблюдается при понижении температуры поверхности ниже температуры кипения жидкости; отвод теплоты в этот период происходит с наименьшей скоростью.
Слайд 30 Тема:3
3.2.3. Закаливаемость и прокаливаемостъ стали
Важными характеристиками стали, необходимыми для
Тема:3
3.2.3. Закаливаемость и прокаливаемостъ стали
Важными характеристиками стали, необходимыми для
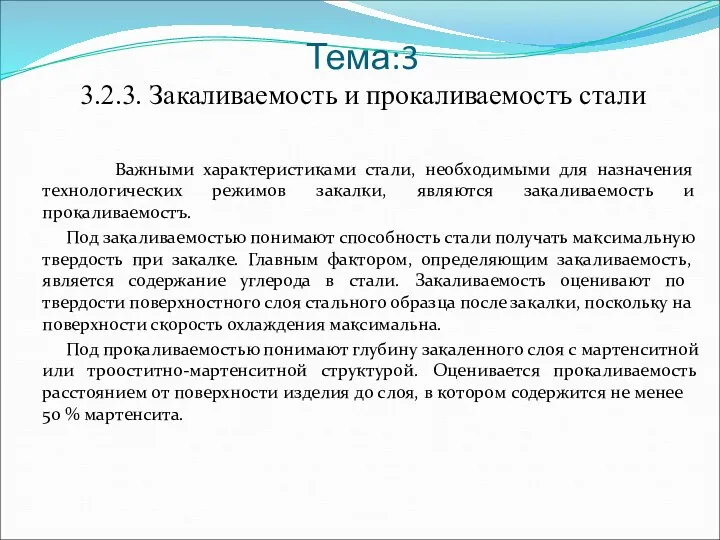
Под закаливаемостью понимают способность стали получать максимальную твердость при закалке. Главным фактором, определяющим закаливаемость, является содержание углерода в стали. Закаливаемость оценивают по твердости поверхностного слоя стального образца после закалки, поскольку на поверхности скорость охлаждения максимальна.
Под прокаливаемостью понимают глубину закаленного слоя с мартенситной или трооститно-мартенситной структурой. Оценивается прокаливаемость расстоянием от поверхности изделия до слоя, в котором содержится не менее 50 % мартенсита.
Слайд 31 Тема:3
3.2.4. Поверхностная закалка
Поверхностной закалкой называют процесс термической обработки, заключающийся
Тема:3
3.2.4. Поверхностная закалка
Поверхностной закалкой называют процесс термической обработки, заключающийся
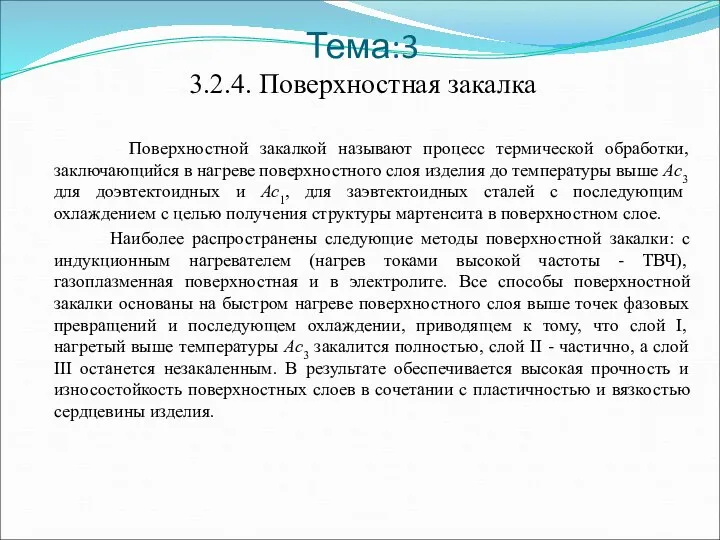
Наиболее распространены следующие методы поверхностной закалки: с индукционным нагревателем (нагрев токами высокой частоты - ТВЧ), газоплазменная поверхностная и в электролите. Все способы поверхностной закалки основаны на быстром нагреве поверхностного слоя выше точек фазовых превращений и последующем охлаждении, приводящем к тому, что слой I, нагретый выше температуры Ас3 закалится полностью, слой II - частично, а слой III останется незакаленным. В результате обеспечивается высокая прочность и износостойкость поверхностных слоев в сочетании с пластичностью и вязкостью сердцевины изделия.
Слайд 32 Тема:3
3.2.5. Отпуск сталей
Отпуском называют финишную термическую обработку, заключающуюся в
Тема:3
3.2.5. Отпуск сталей
Отпуском называют финишную термическую обработку, заключающуюся в
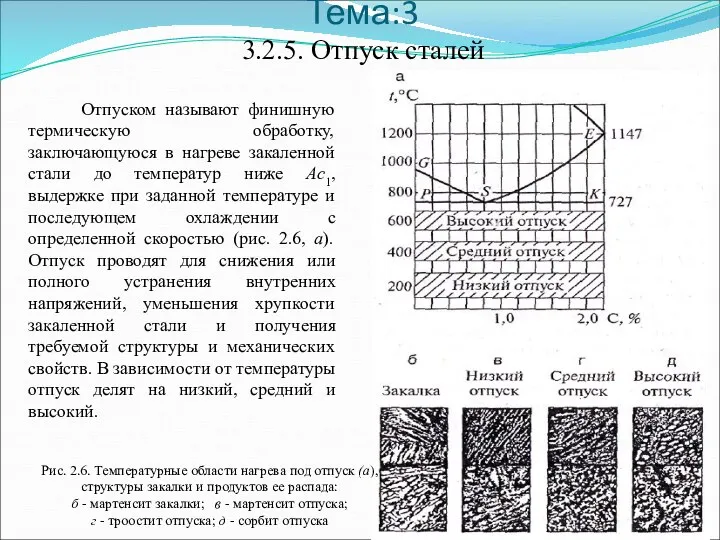
Рис. 2.6. Температурные области нагрева под отпуск (а),
структуры закалки и продуктов ее распада:
б - мартенсит закалки; в - мартенсит отпуска;
г - троостит отпуска; д - сорбит отпуска
Слайд 33 Тема:3
3.3. Термомеханическая обработка стали
Термомеханическая обработка (ТМО) стали заключается в
Тема:3
3.3. Термомеханическая обработка стали
Термомеханическая обработка (ТМО) стали заключается в
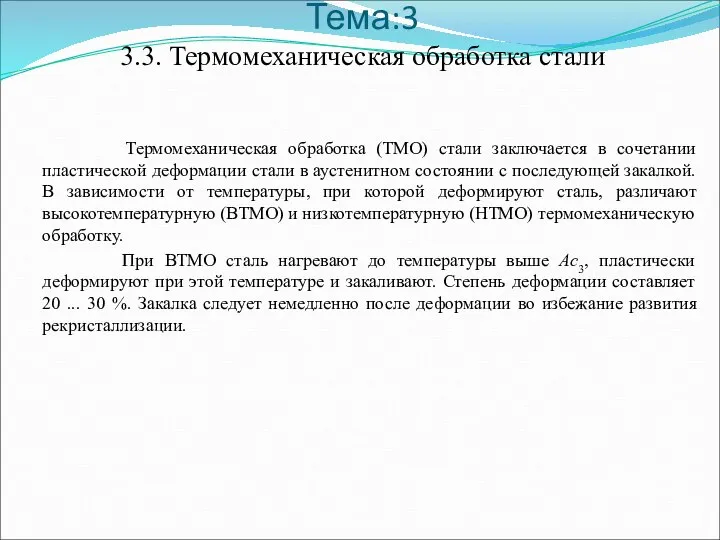
При ВТМО сталь нагревают до температуры выше Ас3, пластически деформируют при этой температуре и закаливают. Степень деформации составляет 20 ... 30 %. Закалка следует немедленно после деформации во избежание развития рекристаллизации.
Слайд 34 Тема:3
3.4. Термическая обработка чугуна
В чугунах, как и в сталях,
Тема:3
3.4. Термическая обработка чугуна
В чугунах, как и в сталях,
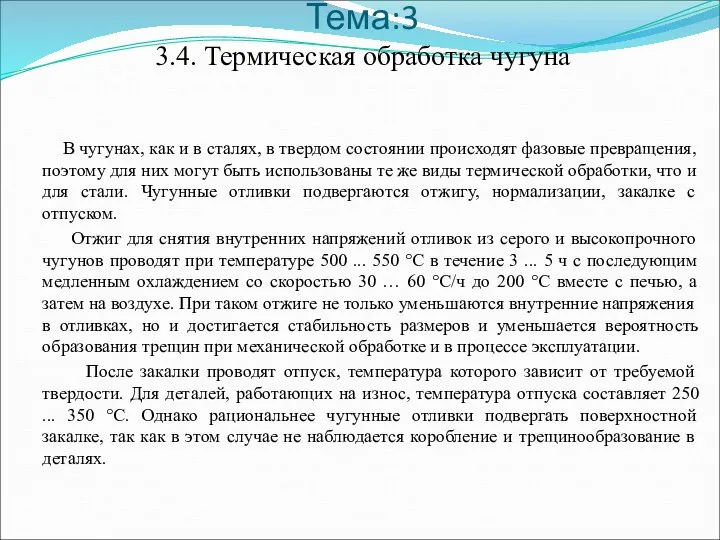
Отжиг для снятия внутренних напряжений отливок из серого и высокопрочного чугунов проводят при температуре 500 ... 550 °С в течение 3 ... 5 ч с последующим медленным охлаждением со скоростью 30 … 60 °С/ч до 200 °С вместе с печью, а затем на воздухе. При таком отжиге не только уменьшаются внутренние напряжения в отливках, но и достигается стабильность размеров и уменьшается вероятность образования трещин при механической обработке и в процессе эксплуатации.
После закалки проводят отпуск, температура которого зависит от требуемой твердости. Для деталей, работающих на износ, температура отпуска составляет 250 ... 350 °С. Однако рациональнее чугунные отливки подвергать поверхностной закалке, так как в этом случае не наблюдается коробление и трещинообразование в деталях.
Слайд 35 Тема:3
3.5. Дефекты термической обработки стали
При термической обработке стали могут
Тема:3
3.5. Дефекты термической обработки стали
При термической обработке стали могут
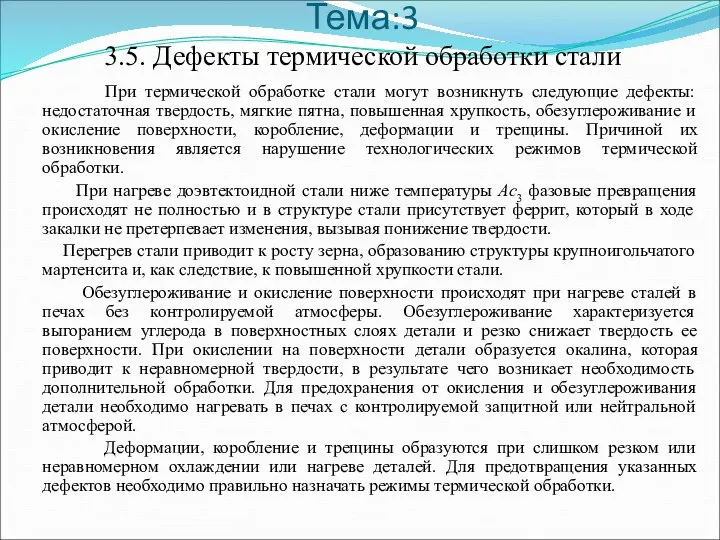
При нагреве доэвтектоидной стали ниже температуры Ас3 фазовые превращения происходят не полностью и в структуре стали присутствует феррит, который в ходе закалки не претерпевает изменения, вызывая понижение твердости.
Перегрев стали приводит к росту зерна, образованию структуры крупноигольчатого мартенсита и, как следствие, к повышенной хрупкости стали.
Обезуглероживание и окисление поверхности происходят при нагреве сталей в печах без контролируемой атмосферы. Обезуглероживание характеризуется выгоранием углерода в поверхностных слоях детали и резко снижает твердость ее поверхности. При окислении на поверхности детали образуется окалина, которая приводит к неравномерной твердости, в результате чего возникает необходимость дополнительной обработки. Для предохранения от окисления и обезуглероживания детали необходимо нагревать в печах с контролируемой защитной или нейтральной атмосферой.
Деформации, коробление и трещины образуются при слишком резком или неравномерном охлаждении или нагреве деталей. Для предотвращения указанных дефектов необходимо правильно назначать режимы термической обработки.
Слайд 36 Тема: 4
ХИМИКО-ТЕРМИЧЕСКАЯ ОБРАБОТКА
4.1. Основы химико-термической обработки сталей
4.2. Цементация
4.3. Азотирование
4.4. Цианирование
4.5.
Тема: 4
ХИМИКО-ТЕРМИЧЕСКАЯ ОБРАБОТКА
4.1. Основы химико-термической обработки сталей
4.2. Цементация
4.3. Азотирование
4.4. Цианирование
4.5.
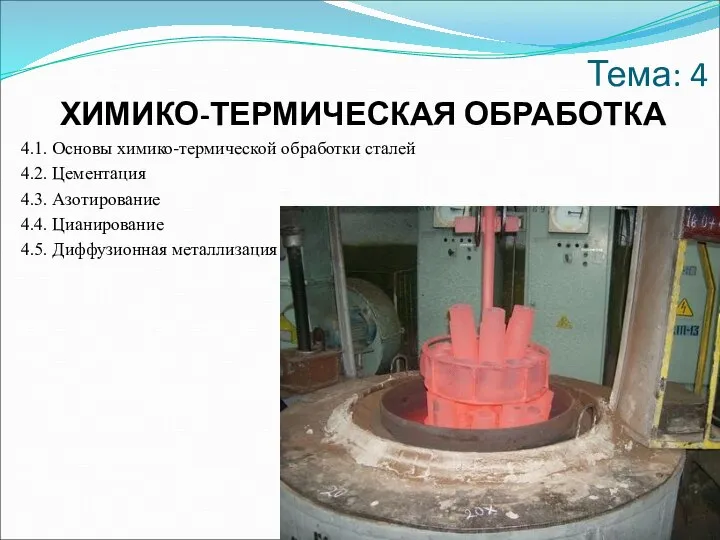
Слайд 37 Тема: 4
4.1. Основы химико-термической обработки сталей
Химико-термической обработкой называют технологический
Тема: 4
4.1. Основы химико-термической обработки сталей
Химико-термической обработкой называют технологический
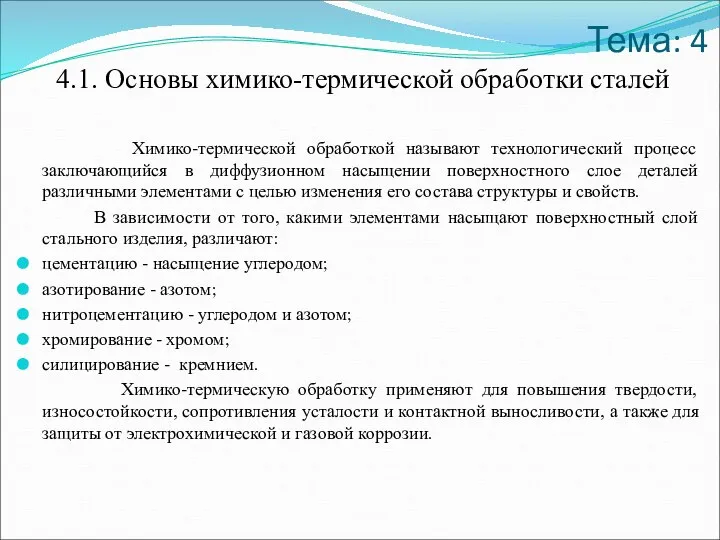
В зависимости от того, какими элементами насыщают поверхностный слой стального изделия, различают:
цементацию - насыщение углеродом;
азотирование - азотом;
нитроцементацию - углеродом и азотом;
хромирование - хромом;
силицирование - кремнием.
Химико-термическую обработку применяют для повышения твердости, износостойкости, сопротивления усталости и контактной выносливости, а также для защиты от электрохимической и газовой коррозии.
Слайд 38 Тема: 4
4.2. Цементация
Цементацией называется технологический процесс диффузионного насыщения поверхности
Тема: 4
4.2. Цементация
Цементацией называется технологический процесс диффузионного насыщения поверхности
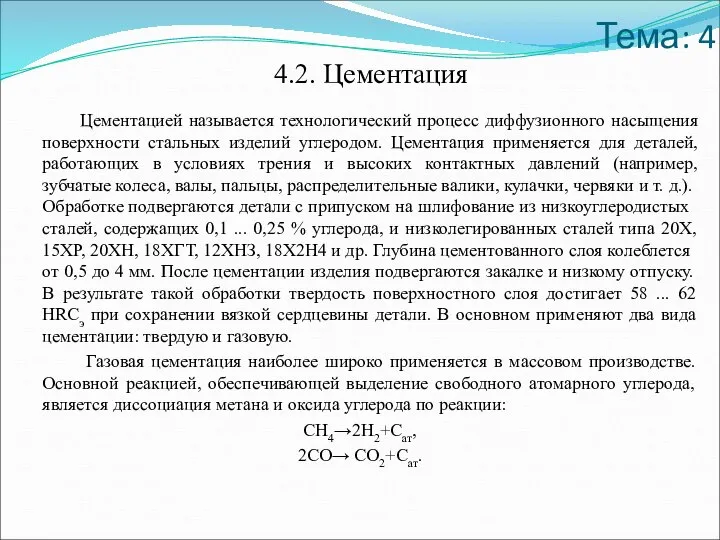
Газовая цементация наиболее широко применяется в массовом производстве. Основной реакцией, обеспечивающей выделение свободного атомарного углерода, является диссоциация метана и оксида углерода по реакции:
CH4→2H2+Cат,
2СO→ СO2+Cат.
Слайд 39 Тема: 4
4.3. Азотирование
Азотированием называется технологический процесс диффузионного насыщения поверхности
Тема: 4
4.3. Азотирование
Азотированием называется технологический процесс диффузионного насыщения поверхности
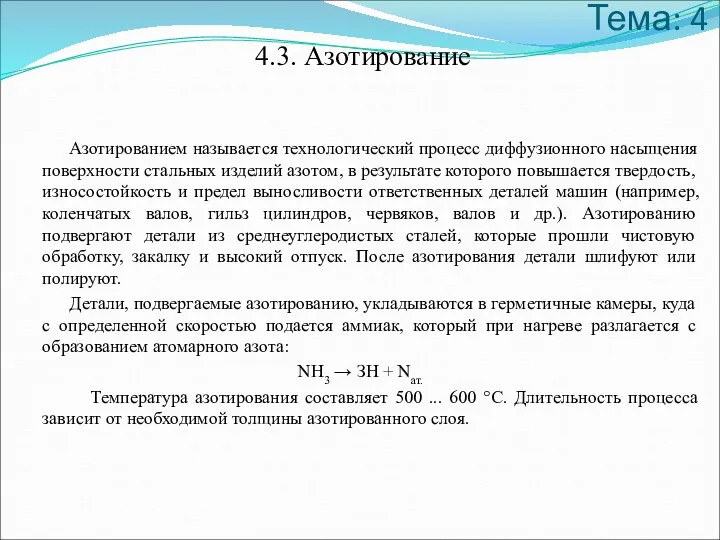
Детали, подвергаемые азотированию, укладываются в герметичные камеры, куда с определенной скоростью подается аммиак, который при нагреве разлагается с образованием атомарного азота:
NН3 → ЗН + Nат.
Температура азотирования составляет 500 ... 600 °С. Длительность процесса зависит от необходимой толщины азотированного слоя.
Слайд 40 Тема: 4
4.4. Цианирование
Цианирование сталей заключается в поверхностном насыщении стальных
Тема: 4
4.4. Цианирование
Цианирование сталей заключается в поверхностном насыщении стальных
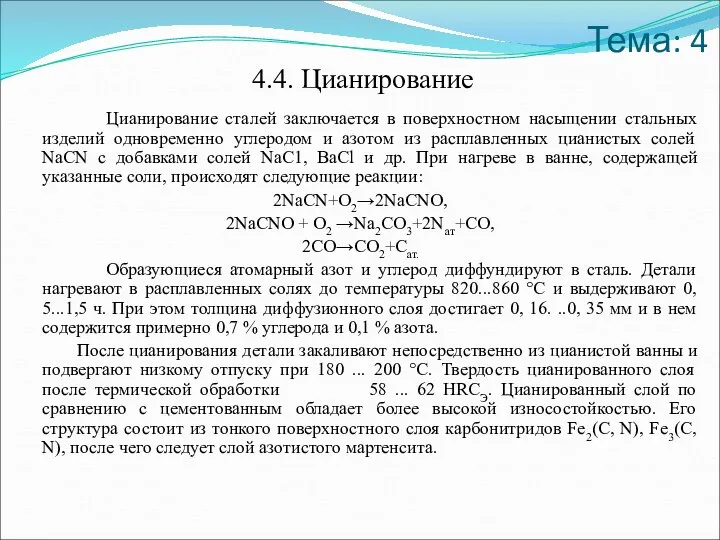
2NaCN+O2→2NaCNO,
2NaCNO + O2 →Na2CO3+2Nат+CO,
2СO→СO2+Cат.
Образующиеся атомарный азот и углерод диффундируют в сталь. Детали нагревают в расплавленных солях до температуры 820...860 °С и выдерживают 0, 5...1,5 ч. При этом толщина диффузионного слоя достигает 0, 16. ..0, 35 мм и в нем содержится примерно 0,7 % углерода и 0,1 % азота.
После цианирования детали закаливают непосредственно из цианистой ванны и подвергают низкому отпуску при 180 ... 200 °С. Твердость цианированного слоя после термической обработки 58 ... 62 НRСЭ. Цианированный слой по сравнению с цементованным обладает более высокой износостойкостью. Его структура состоит из тонкого поверхностного слоя карбонитридов Fе2(С, N), Fе3(С, N), после чего следует слой азотистого мартенсита.
Слайд 41 Тема: 4
4.5. Диффузионная металлизация
Диффузионное насыщение поверхностного слоя стальных изделий
Тема: 4
4.5. Диффузионная металлизация
Диффузионное насыщение поверхностного слоя стальных изделий
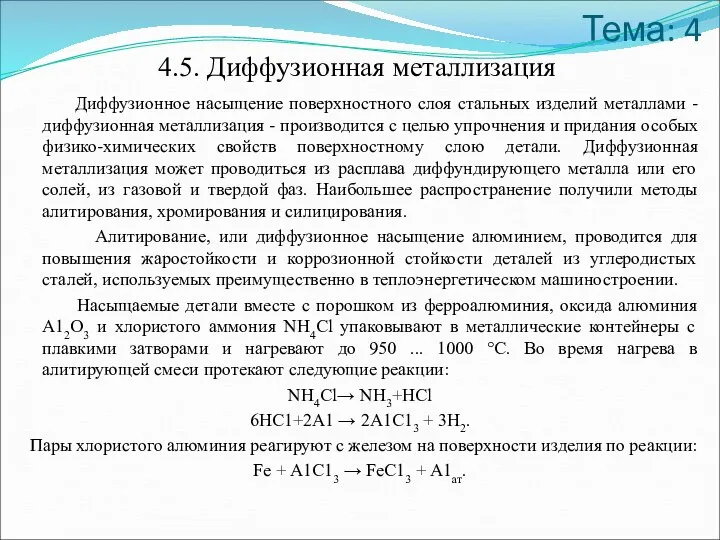
Алитирование, или диффузионное насыщение алюминием, проводится для повышения жаростойкости и коррозионной стойкости деталей из углеродистых сталей, используемых преимущественно в теплоэнергетическом машиностроении.
Насыщаемые детали вместе с порошком из ферроалюминия, оксида алюминия А12O3 и хлористого аммония NН4Сl упаковывают в металлические контейнеры с плавкими затворами и нагревают до 950 ... 1000 °С. Во время нагрева в алитирующей смеси протекают следующие реакции:
NН4Сl→ NН3+HCl
6НС1+2А1 → 2А1С13 + 3Н2.
Пары хлористого алюминия реагируют с железом на поверхности изделия по реакции:
Fе + А1С13 → FеС13 + А1ат.
Слайд 42 Тема:5
УГЛЕРОДИСТЫЕ И ЛЕГИРОВАННЫЕ СТАЛИ
5.1. Влияние примесей на свойства сталей
5.2. Классификация
Тема:5
УГЛЕРОДИСТЫЕ И ЛЕГИРОВАННЫЕ СТАЛИ
5.1. Влияние примесей на свойства сталей
5.2. Классификация
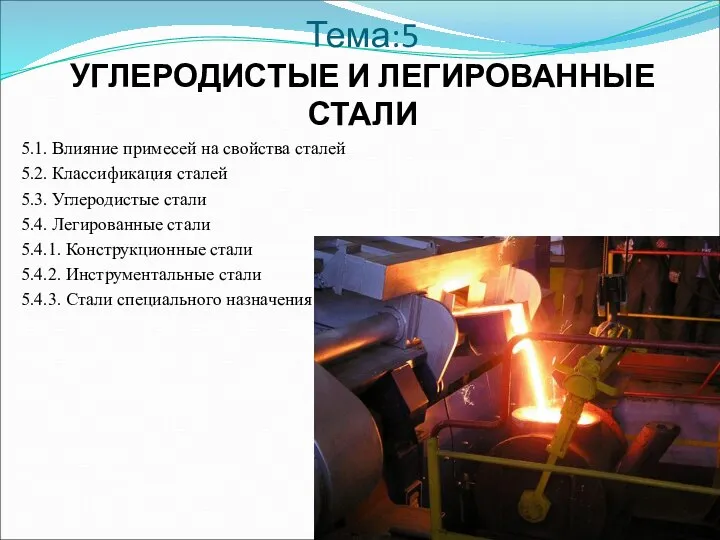
5.3. Углеродистые стали
5.4. Легированные стали
5.4.1. Конструкционные стали
5.4.2. Инструментальные стали
5.4.3. Стали специального назначения
Слайд 43 Тема:5
5.1. Влияние примесей на свойства сталей
Свойства сталей зависят не
Тема:5
5.1. Влияние примесей на свойства сталей
Свойства сталей зависят не
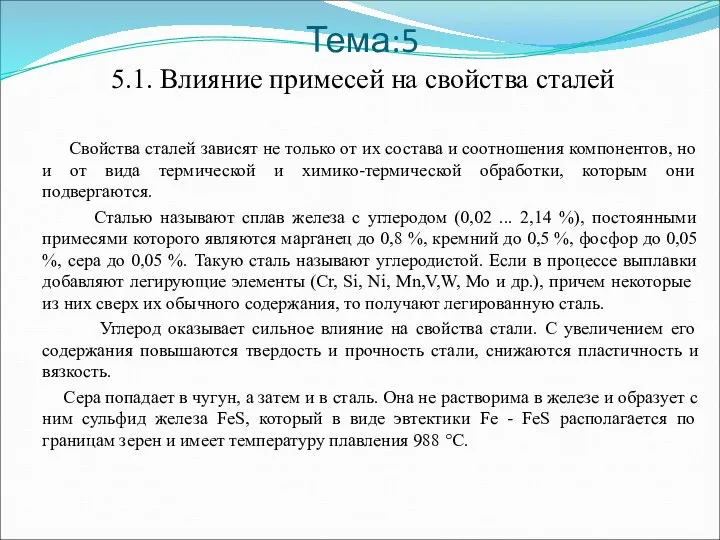
Сталью называют сплав железа с углеродом (0,02 ... 2,14 %), постоянными примесями которого являются марганец до 0,8 %, кремний до 0,5 %, фосфор до 0,05 %, сера до 0,05 %. Такую сталь называют углеродистой. Если в процессе выплавки добавляют легирующие элементы (Сr, Si, Ni, Мn,V,W, Мо и др.), причем некоторые из них сверх их обычного содержания, то получают легированную сталь.
Углерод оказывает сильное влияние на свойства стали. С увеличением его содержания повышаются твердость и прочность стали, снижаются пластичность и вязкость.
Сера попадает в чугун, а затем и в сталь. Она не растворима в железе и образует с ним сульфид железа FеS, который в виде эвтектики Fе - FеS располагается по границам зерен и имеет температуру плавления 988 °С.
Слайд 44 Тема:5
5.2. Классификация сталей
Стали классифицируют по химическому составу, способу производства,
Тема:5
5.2. Классификация сталей
Стали классифицируют по химическому составу, способу производства,
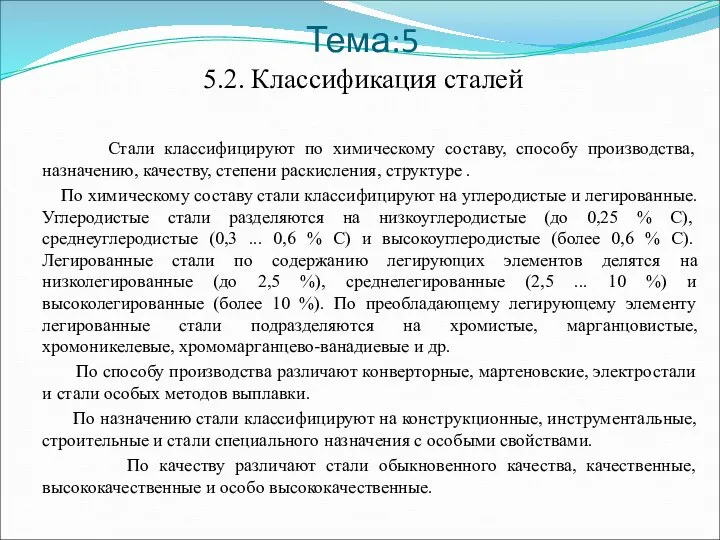
По химическому составу стали классифицируют на углеродистые и легированные. Углеродистые стали разделяются на низкоуглеродистые (до 0,25 % С), среднеуглеродистые (0,3 ... 0,6 % С) и высокоуглеродистые (более 0,6 % С). Легированные стали по содержанию легирующих элементов делятся на низколегированные (до 2,5 %), среднелегированные (2,5 ... 10 %) и высоколегированные (более 10 %). По преобладающему легирующему элементу легированные стали подразделяются на хромистые, марганцовистые, хромоникелевые, хромомарганцево-ванадиевые и др.
По способу производства различают конверторные, мартеновские, электростали и стали особых методов выплавки.
По назначению стали классифицируют на конструкционные, инструментальные, строительные и стали специального назначения с особыми свойствами.
По качеству различают стали обыкновенного качества, качественные, высококачественные и особо высококачественные.
Слайд 45 Тема:5
5.3. Углеродистые стали
Углеродистые стали относятся к числу самых распространенных
Тема:5
5.3. Углеродистые стали
Углеродистые стали относятся к числу самых распространенных
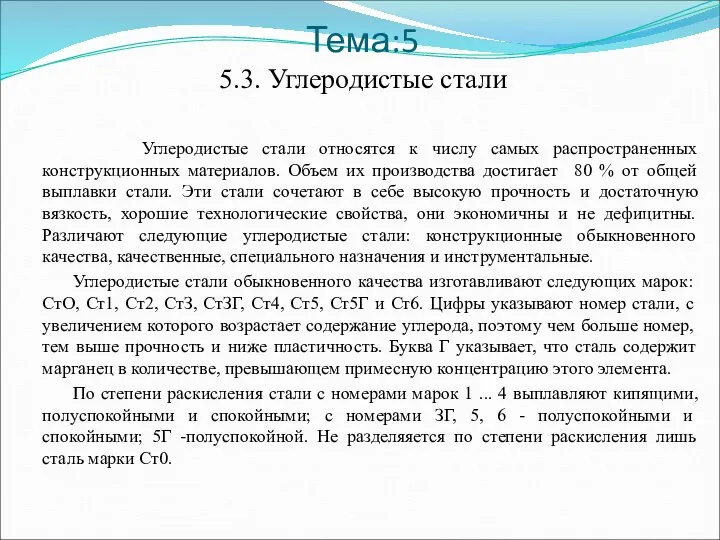
Углеродистые стали обыкновенного качества изготавливают следующих марок: СтО, Ст1, Ст2, СтЗ, СтЗГ, Ст4, Ст5, Ст5Г и Ст6. Цифры указывают номер стали, с увеличением которого возрастает содержание углерода, поэтому чем больше номер, тем выше прочность и ниже пластичность. Буква Г указывает, что сталь содержит марганец в количестве, превышающем примесную концентрацию этого элемента.
По степени раскисления стали с номерами марок 1 ... 4 выплавляют кипящими, полуспокойными и спокойными; с номерами ЗГ, 5, 6 - полуспокойными и спокойными; 5Г -полуспокойной. Не разделяяется по степени раскисления лишь сталь марки Ст0.
Слайд 46 Тема:5
5.4. Легированные стали
Основными легирующими элементами являются кремний, никель, марганец,
Тема:5
5.4. Легированные стали
Основными легирующими элементами являются кремний, никель, марганец,

Легирующие элементы, растворяясь в феррите, упрочняют его. Однако упрочнение феррита приводит к снижению ударной вязкости, особенно если концентрация легирующих элементов больше 1 %. Исключение составляет никель, который не снижает вязкости стали.
Слайд 47 Тема:5
5.4.1. Конструкционные стали
Цементуемые стали обычно содержат 0,1 ... 0,25
Тема:5
5.4.1. Конструкционные стали
Цементуемые стали обычно содержат 0,1 ... 0,25
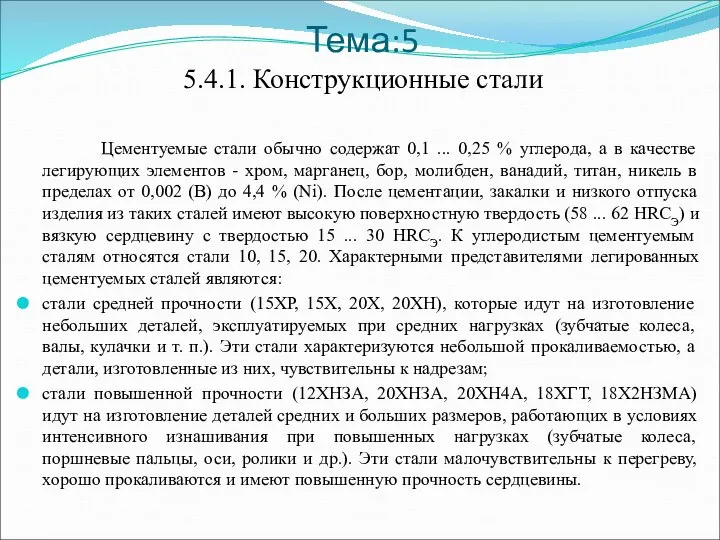
стали средней прочности (15ХР, 15Х, 20Х, 20ХН), которые идут на изготовление небольших деталей, эксплуатируемых при средних нагрузках (зубчатые колеса, валы, кулачки и т. п.). Эти стали характеризуются небольшой прокаливаемостью, а детали, изготовленные из них, чувствительны к надрезам;
стали повышенной прочности (12ХНЗА, 20ХНЗА, 20ХН4А, 18ХГТ, 18Х2НЗМА) идут на изготовление деталей средних и больших размеров, работающих в условиях интенсивного изнашивания при повышенных нагрузках (зубчатые колеса, поршневые пальцы, оси, ролики и др.). Эти стали малочувствительны к перегреву, хорошо прокаливаются и имеют повышенную прочность сердцевины.
Слайд 48 Тема:5
5.4.2. Инструментальные стали
К инструментальным сталям относятся легированные стали повышенной
Тема:5
5.4.2. Инструментальные стали
К инструментальным сталям относятся легированные стали повышенной
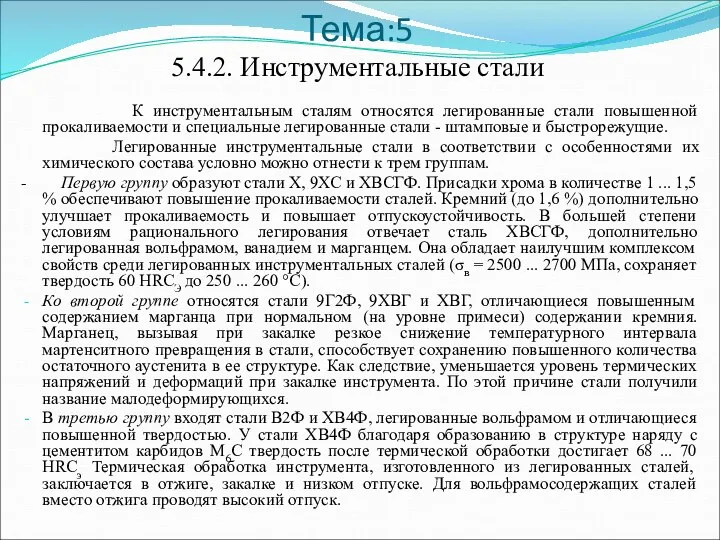
Легированные инструментальные стали в соответствии с особенностями их химического состава условно можно отнести к трем группам.
- Первую группу образуют стали X, 9ХС и ХВСГФ. Присадки хрома в количестве 1 ... 1,5 % обеспечивают повышение прокаливаемости сталей. Кремний (до 1,6 %) дополнительно улучшает прокаливаемость и повышает отпускоустойчивость. В большей степени условиям рационального легирования отвечает сталь ХВСГФ, дополнительно легированная вольфрамом, ванадием и марганцем. Она обладает наилучшим комплексом свойств среди легированных инструментальных сталей (σв = 2500 ... 2700 МПа, сохраняет твердость 60 НRСЭ до 250 ... 260 °С).
Ко второй группе относятся стали 9Г2Ф, 9ХВГ и ХВГ, отличающиеся повышенным содержанием марганца при нормальном (на уровне примеси) содержании кремния. Марганец, вызывая при закалке резкое снижение температурного интервала мартенситного превращения в стали, способствует сохранению повышенного количества остаточного аустенита в ее структуре. Как следствие, уменьшается уровень термических напряжений и деформаций при закалке инструмента. По этой причине стали получили название малодеформирующихся.
В третью группу входят стали В2Ф и ХВ4Ф, легированные вольфрамом и отличающиеся повышенной твердостью. У стали ХВ4Ф благодаря образованию в структуре наряду с цементитом карбидов М6С твердость после термической обработки достигает 68 ... 70 НRСэ Термическая обработка инструмента, изготовленного из легированных сталей, заключается в отжиге, закалке и низком отпуске. Для вольфрамосодержащих сталей вместо отжига проводят высокий отпуск.
Слайд 49 Тема:5
5.4.3. Стали специального назначения
Коррозионно-стойкие (нержавеющие) стали относятся к специальным
Тема:5
5.4.3. Стали специального назначения
Коррозионно-стойкие (нержавеющие) стали относятся к специальным
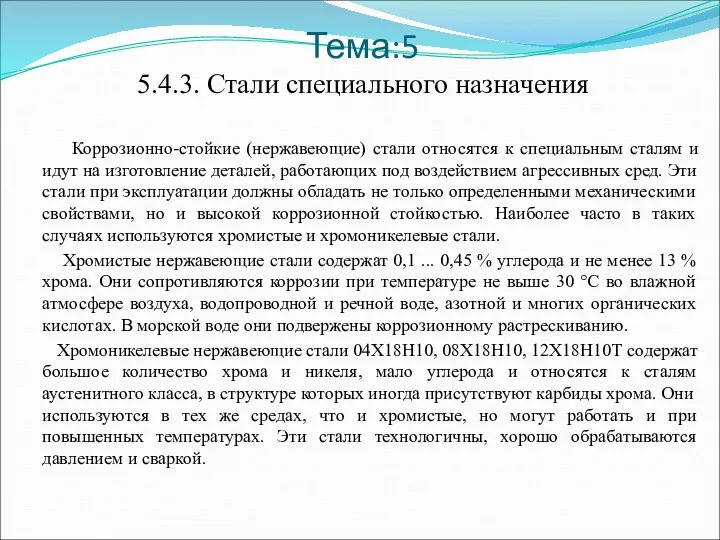
Хромистые нержавеющие стали содержат 0,1 ... 0,45 % углерода и не менее 13 % хрома. Они сопротивляются коррозии при температуре не выше 30 °С во влажной атмосфере воздуха, водопроводной и речной воде, азотной и многих органических кислотах. В морской воде они подвержены коррозионному растрескиванию.
Хромоникелевые нержавеющие стали 04Х18Н10, 08Х18H10, 12Х18Н10Т содержат большое количество хрома и никеля, мало углерода и относятся к сталям аустенитного класса, в структуре которых иногда присутствуют карбиды хрома. Они используются в тех же средах, что и хромистые, но могут работать и при повышенных температурах. Эти стали технологичны, хорошо обрабатываются давлением и сваркой.
Слайд 50 Тема:6 ЦВЕТНЫЕ МЕТАЛЛЫ И СПЛАВЫ
6.1. Общее понятие о цветных металлах
6.2. Алюминий
Тема:6 ЦВЕТНЫЕ МЕТАЛЛЫ И СПЛАВЫ
6.1. Общее понятие о цветных металлах
6.2. Алюминий
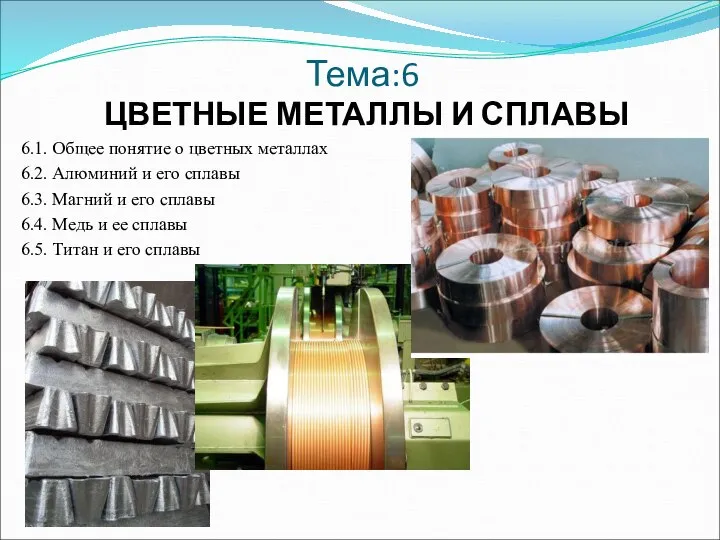
6.3. Магний и его сплавы
6.4. Медь и ее сплавы
6.5. Титан и его сплавы
Слайд 51 Тема:6 6.1. Общее понятие о цветных металлах
Традиционно к цветным металлам
Тема:6 6.1. Общее понятие о цветных металлах
Традиционно к цветным металлам
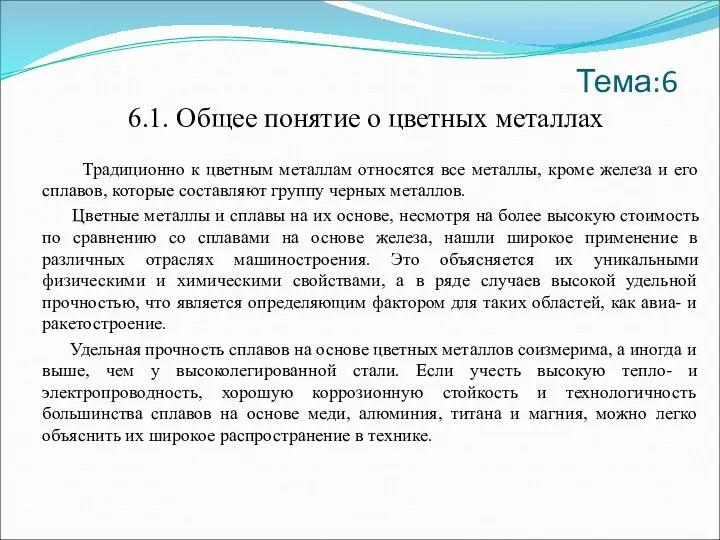
Цветные металлы и сплавы на их основе, несмотря на более высокую стоимость по сравнению со сплавами на основе железа, нашли широкое применение в различных отраслях машиностроения. Это объясняется их уникальными физическими и химическими свойствами, а в ряде случаев высокой удельной прочностью, что является определяющим фактором для таких областей, как авиа- и ракетостроение.
Удельная прочность сплавов на основе цветных металлов соизмерима, а иногда и выше, чем у высоколегированной стали. Если учесть высокую тепло- и электропроводность, хорошую коррозионную стойкость и технологичность большинства сплавов на основе меди, алюминия, титана и магния, можно легко объяснить их широкое распространение в технике.
Слайд 52 Тема:6 6.2. Алюминий и его сплавы
Алюминий имеет гранецентрированную кубическую решетку,
Тема:6 6.2. Алюминий и его сплавы
Алюминий имеет гранецентрированную кубическую решетку,
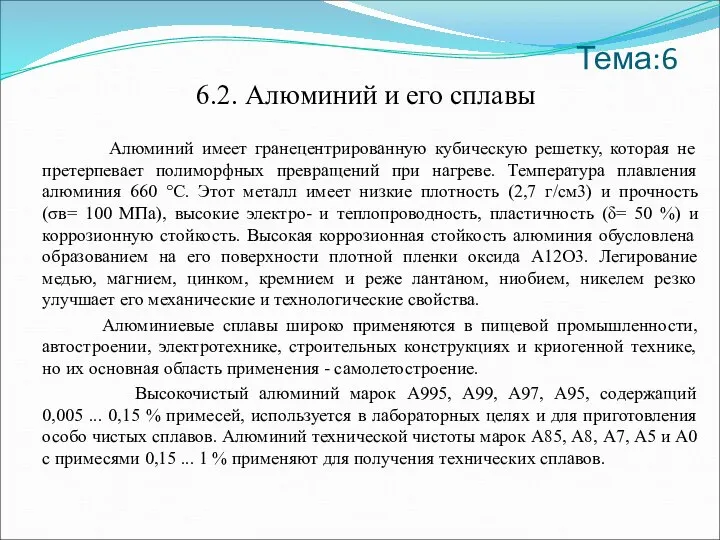
Алюминиевые сплавы широко применяются в пищевой промышленности, автостроении, электротехнике, строительных конструкциях и криогенной технике, но их основная область применения - самолетостроение.
Высокочистый алюминий марок А995, А99, А97, А95, содержащий 0,005 ... 0,15 % примесей, используется в лабораторных целях и для приготовления особо чистых сплавов. Алюминий технической чистоты марок А85, А8, А7, А5 и А0 с примесями 0,15 ... 1 % применяют для получения технических сплавов.
Слайд 53 Тема:6 6.3. Магний и его сплавы
Магний имеет низкую плотность (1,73
Тема:6 6.3. Магний и его сплавы
Магний имеет низкую плотность (1,73
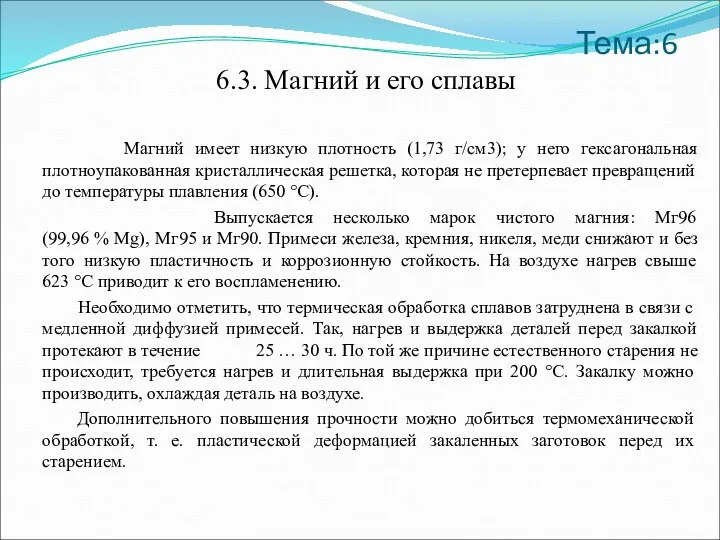
Выпускается несколько марок чистого магния: Мг96 (99,96 % Мg), Мг95 и Мг90. Примеси железа, кремния, никеля, меди снижают и без того низкую пластичность и коррозионную стойкость. На воздухе нагрев свыше 623 °С приводит к его воспламенению.
Необходимо отметить, что термическая обработка сплавов затруднена в связи с медленной диффузией примесей. Так, нагрев и выдержка деталей перед закалкой протекают в течение 25 … 30 ч. По той же причине естественного старения не происходит, требуется нагрев и длительная выдержка при 200 °С. Закалку можно производить, охлаждая деталь на воздухе.
Дополнительного повышения прочности можно добиться термомеханической обработкой, т. е. пластической деформацией закаленных заготовок перед их старением.
Слайд 54 Тема:6 6.4. Медь и ее сплавы
Медь - металл красного цвета,
Тема:6 6.4. Медь и ее сплавы
Медь - металл красного цвета,
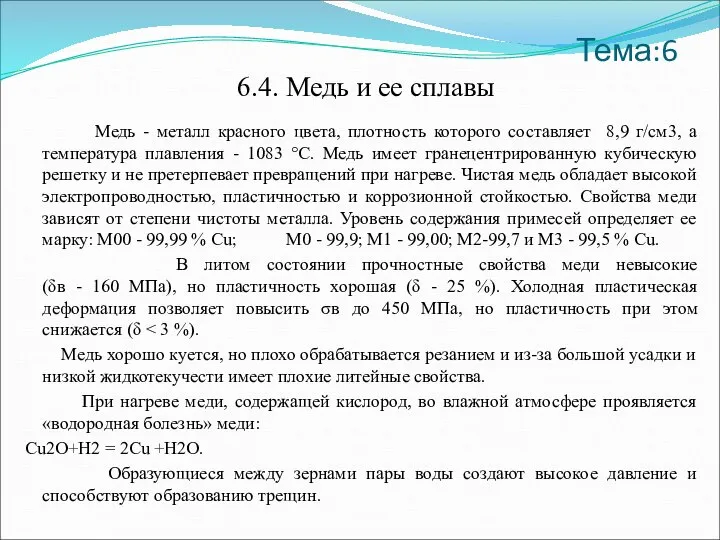
В литом состоянии прочностные свойства меди невысокие (δв - 160 МПа), но пластичность хорошая (δ - 25 %). Холодная пластическая деформация позволяет повысить σв до 450 МПа, но пластичность при этом снижается (δ < 3 %).
Медь хорошо куется, но плохо обрабатывается резанием и из-за большой усадки и низкой жидкотекучести имеет плохие литейные свойства.
При нагреве меди, содержащей кислород, во влажной атмосфере проявляется «водородная болезнь» меди:
Сu2О+H2 = 2Сu +H2О.
Образующиеся между зернами пары воды создают высокое давление и способствуют образованию трещин.
Слайд 55 Тема:6 6.5. Титан и его сплавы
Титан по распространенности занимает четвертое
Тема:6 6.5. Титан и его сплавы
Титан по распространенности занимает четвертое
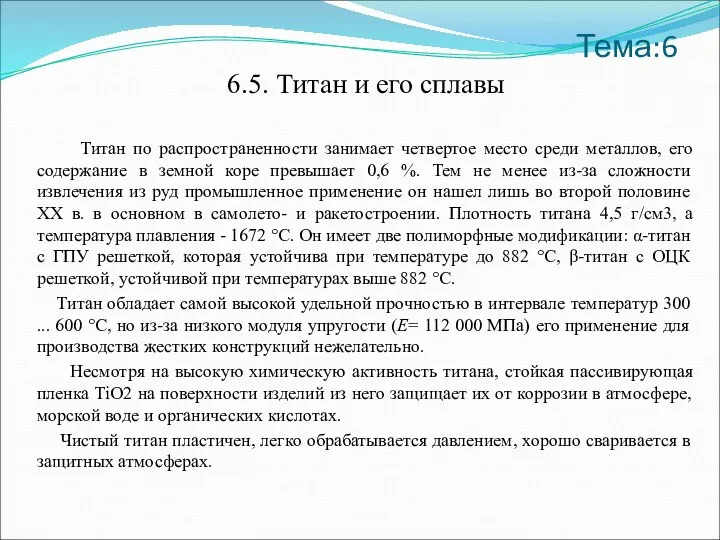
Титан обладает самой высокой удельной прочностью в интервале температур 300 ... 600 °С, но из-за низкого модуля упругости (Е= 112 000 МПа) его применение для производства жестких конструкций нежелательно.
Несмотря на высокую химическую активность титана, стойкая пассивирующая пленка ТiO2 на поверхности изделий из него защищает их от коррозии в атмосфере, морской воде и органических кислотах.
Чистый титан пластичен, легко обрабатывается давлением, хорошо сваривается в защитных атмосферах.
Слайд 56 Тема:7 КОМПОЗИЦИОННЫЕ МАТЕРИАЛЫ
7.1. Классификация композиционных материалов
7.2. Особенности получения КМ жидкофазными методами
7.3.
Тема:7 КОМПОЗИЦИОННЫЕ МАТЕРИАЛЫ
7.1. Классификация композиционных материалов
7.2. Особенности получения КМ жидкофазными методами
7.3.
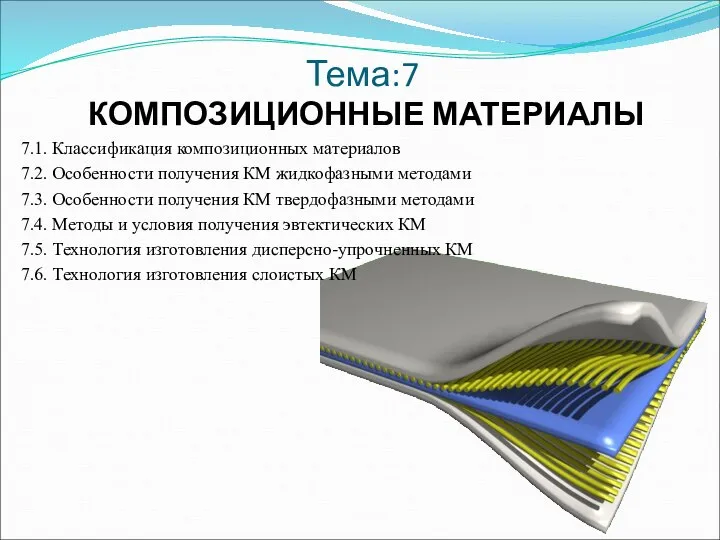
7.4. Методы и условия получения эвтектических КМ
7.5. Технология изготовления дисперсно-упрочненных КМ
7.6. Технология изготовления слоистых КМ
Слайд 57 Тема:7 7.1. Классификация композиционных материалов
Композиционными материалами (КМ) называют материалы, созданные
Тема:7 7.1. Классификация композиционных материалов
Композиционными материалами (КМ) называют материалы, созданные
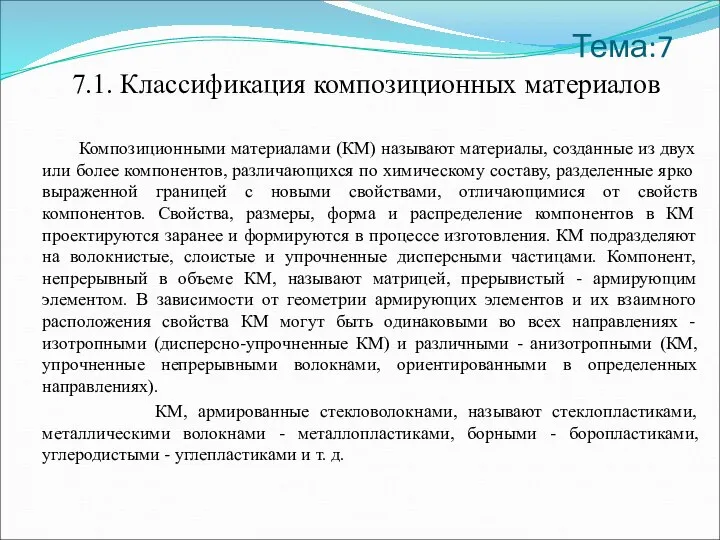
КМ, армированные стекловолокнами, называют стеклопластиками, металлическими волокнами - металлопластиками, борными - боропластиками, углеродистыми - углепластиками и т. д.
Слайд 58Рис. 2.7. Схема расположения упрочнителей в композиционных материалах:
а - волокнистых; б -
Рис. 2.7. Схема расположения упрочнителей в композиционных материалах:
а - волокнистых; б -
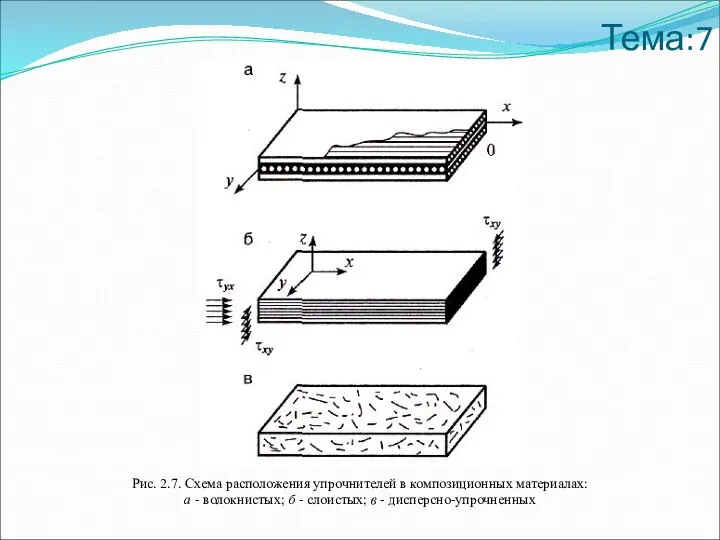
Тема:7
Слайд 59 Тема:7 7.2. Особенности получения КМ жидкофазными методами
Выбор метода получения КМ
Тема:7 7.2. Особенности получения КМ жидкофазными методами
Выбор метода получения КМ
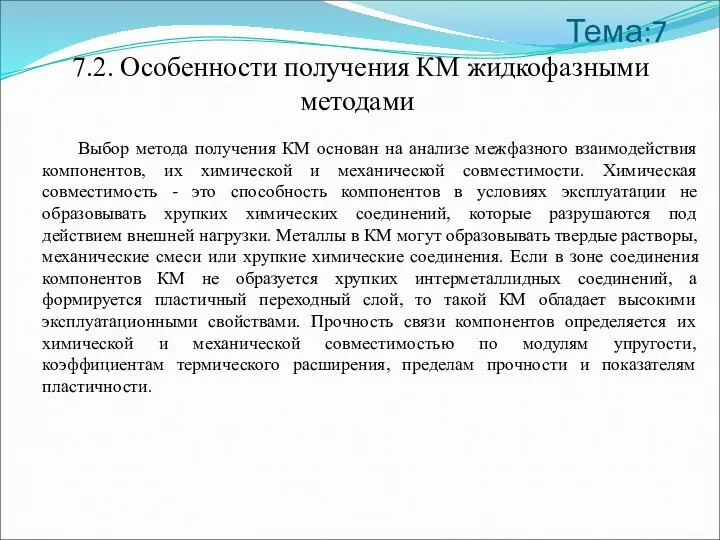
Слайд 60 Тема:7 7.3. Особенности получения КМ твердофазными методами
В твердофазных методах получения
Тема:7 7.3. Особенности получения КМ твердофазными методами
В твердофазных методах получения
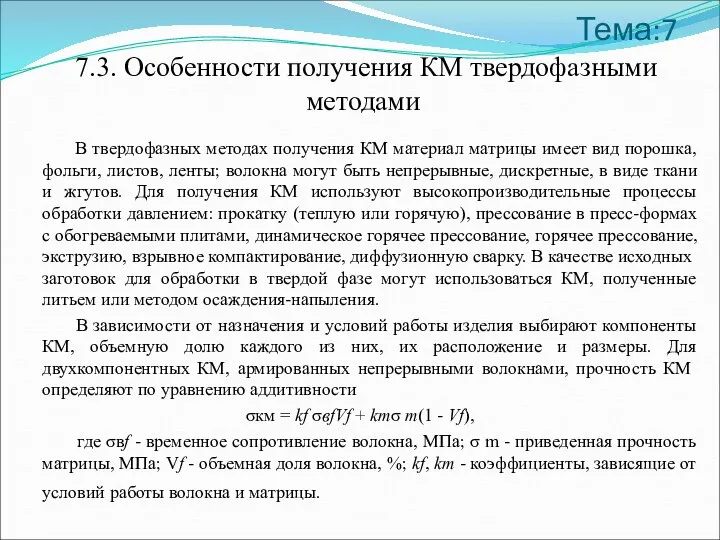
В зависимости от назначения и условий работы изделия выбирают компоненты КМ, объемную долю каждого из них, их расположение и размеры. Для двухкомпонентных КМ, армированных непрерывными волокнами, прочность КМ определяют по уравнению аддитивности
σкм = kf σвfVf + kmσ m(1 - Vf),
где σвf - временное сопротивление волокна, МПа; σ m - приведенная прочность матрицы, МПа; Vf - объемная доля волокна, %; kf, km - коэффициенты, зависящие от условий работы волокна и матрицы.
Слайд 61 Тема:7 7.4. Методы и условия получения эвтектических КМ
Эвтектическими КМ называют
Тема:7 7.4. Методы и условия получения эвтектических КМ
Эвтектическими КМ называют

Эвтектические КМ изготавливают на основе сплавов алюминия (А1 - А13Ni, А1 - СuА12, А1 - Ве, А1 - Si), никеля (Ni - NiВе, Ni - Сr, Ni - NiМо, Ni - W), кобальта (Со - СоА1, Со - NbС, Со - Со7N6, (Со – Ni – Сr - А1 - ТаС) и т. д.
Высокопрочные эвтектические КМ имеют совершенную структуру, термически стабильную вплоть до температур плавления эвтектики.
Слайд 62 Тема:7 7.5. Технология изготовления дисперсно-упрочненных КМ
Дисперсно-упрочненные КМ относятся к классу
Тема:7 7.5. Технология изготовления дисперсно-упрочненных КМ
Дисперсно-упрочненные КМ относятся к классу
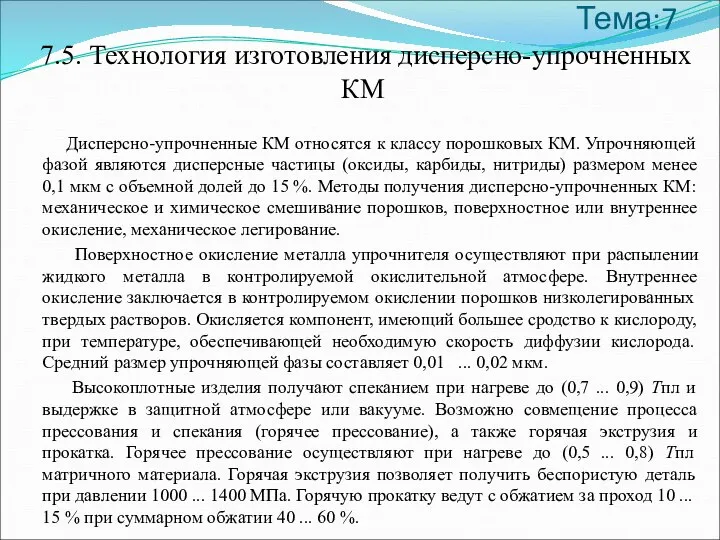
Поверхностное окисление металла упрочнителя осуществляют при распылении жидкого металла в контролируемой окислительной атмосфере. Внутреннее окисление заключается в контролируемом окислении порошков низколегированных твердых растворов. Окисляется компонент, имеющий большее сродство к кислороду, при температуре, обеспечивающей необходимую скорость диффузии кислорода. Средний размер упрочняющей фазы составляет 0,01 ... 0,02 мкм.
Высокоплотные изделия получают спеканием при нагреве до (0,7 ... 0,9) Тпл и выдержке в защитной атмосфере или вакууме. Возможно совмещение процесса прессования и спекания (горячее прессование), а также горячая экструзия и прокатка. Горячее прессование осуществляют при нагреве до (0,5 ... 0,8) Тпл матричного материала. Горячая экструзия позволяет получить беспористую деталь при давлении 1000 ... 1400 МПа. Горячую прокатку ведут с обжатием за проход 10 ... 15 % при суммарном обжатии 40 ... 60 %.
Слайд 63 Тема:7 7.6. Технология изготовления слоистых КМ
Слоистые материалы в виде листов,
Тема:7 7.6. Технология изготовления слоистых КМ
Слоистые материалы в виде листов,
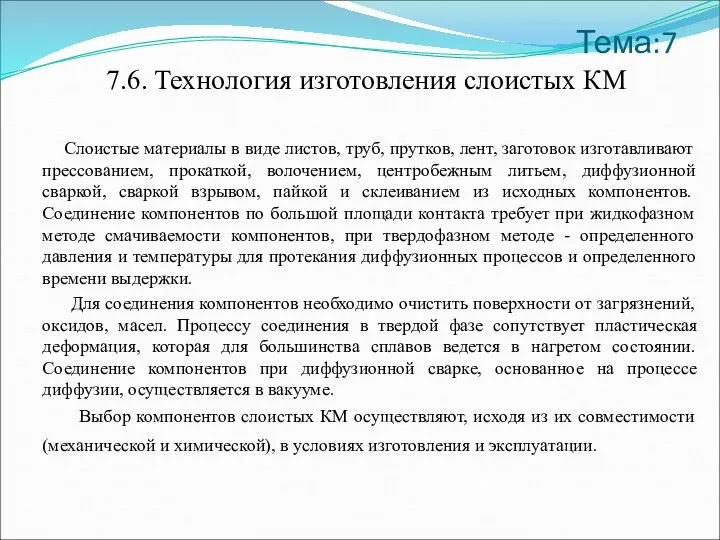
Для соединения компонентов необходимо очистить поверхности от загрязнений, оксидов, масел. Процессу соединения в твердой фазе сопутствует пластическая деформация, которая для большинства сплавов ведется в нагретом состоянии. Соединение компонентов при диффузионной сварке, основанное на процессе диффузии, осуществляется в вакууме.
Выбор компонентов слоистых КМ осуществляют, исходя из их совместимости (механической и химической), в условиях изготовления и эксплуатации.