Содержание
- 2. 11.1 ОБРЕЗКА ОБЛОЯ И ПРОБИВКА ПЕРЕМЫЧЕК Основные технологические отходы в КШП: облой, перемычки сквозных отверстий поковок.
- 3. Штампы, предназначенные для выполнения одной из отделочных операций, называют простыми, рисунок 11.1. Рисунок 11.1 – Схема
- 4. 11.2 ЗАЧИСТКА ЗАУСЕНЦЕВ И ДЕФЕКТНЫХ УЧАСТКОВ Удаление дефектов на поверхности исходных заготовок и промежуточных деформированных полуфабрикатов
- 5. Эти процессы применяют соответственно для устранения искажений формы поковок и для повышения точности формы и размеров
- 6. Рисунок 11.2 – Схема правильного пресса с программным управлением 1 – подающе-удаляющее устройство; 2 – клещи;
- 7. Заготовка 10 захватывается клещами 2 и переносится на ось центров 5 и зажимается. Датчики 6 измеряют
- 8. Калибровку проводят на прессах, отличающихся повышенной жесткостью, в штампах. Объемная калибровка обеспечивает более точную форму поковок,
- 9. Применяемая термообработка включает нормализацию, изотермический отжиг, улучшение. Она позволяет улучшать обрабатываемость заготовок резанием. При нормализации поковки
- 11. Скачать презентацию
Слайд 211.1 ОБРЕЗКА ОБЛОЯ И ПРОБИВКА ПЕРЕМЫЧЕК
Основные технологические отходы в КШП: облой, перемычки
11.1 ОБРЕЗКА ОБЛОЯ И ПРОБИВКА ПЕРЕМЫЧЕК
Основные технологические отходы в КШП: облой, перемычки

Малый облой простых по конфигурации изделий удаляют вместе с припусками при механической обработке. При содержании углерода в материале до 0,45 % обрезка облоя выполняется в холодном состоянии.
Слайд 3 Штампы, предназначенные для выполнения одной из отделочных операций, называют простыми, рисунок 11.1.
Штампы, предназначенные для выполнения одной из отделочных операций, называют простыми, рисунок 11.1.
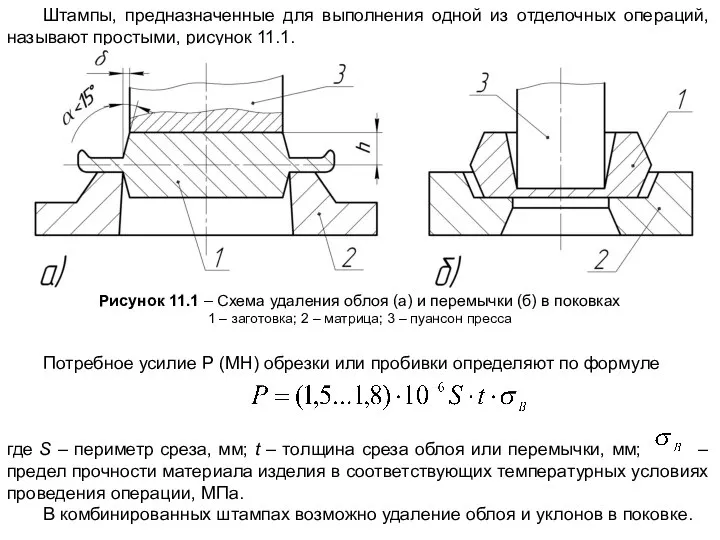
Рисунок 11.1 – Схема удаления облоя (а) и перемычки (б) в поковках
1 – заготовка; 2 – матрица; 3 – пуансон пресса
Потребное усилие Р (МН) обрезки или пробивки определяют по формуле
где S – периметр среза, мм; t – толщина среза облоя или перемычки, мм; – предел прочности материала изделия в соответствующих температурных условиях проведения операции, МПа.
В комбинированных штампах возможно удаление облоя и уклонов в поковке.
Слайд 411.2 ЗАЧИСТКА ЗАУСЕНЦЕВ И ДЕФЕКТНЫХ УЧАСТКОВ
Удаление дефектов на поверхности исходных заготовок
11.2 ЗАЧИСТКА ЗАУСЕНЦЕВ И ДЕФЕКТНЫХ УЧАСТКОВ
Удаление дефектов на поверхности исходных заготовок
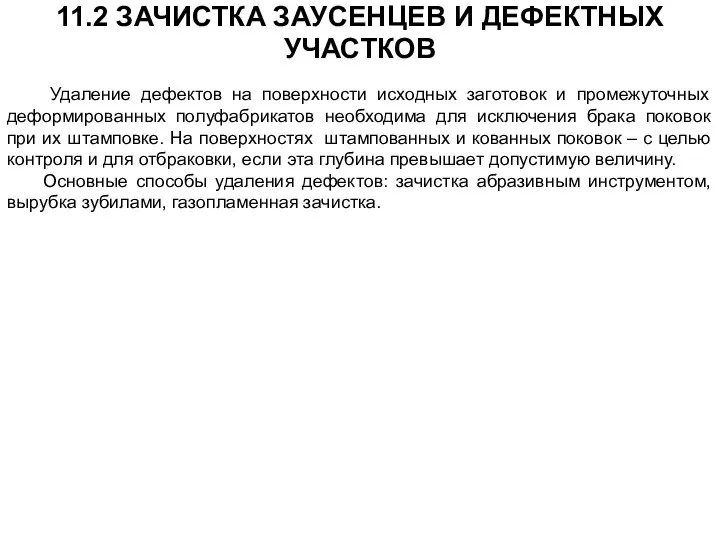
Основные способы удаления дефектов: зачистка абразивным инструментом, вырубка зубилами, газопламенная зачистка.
Слайд 5 Эти процессы применяют соответственно для устранения искажений формы поковок и для повышения
Эти процессы применяют соответственно для устранения искажений формы поковок и для повышения
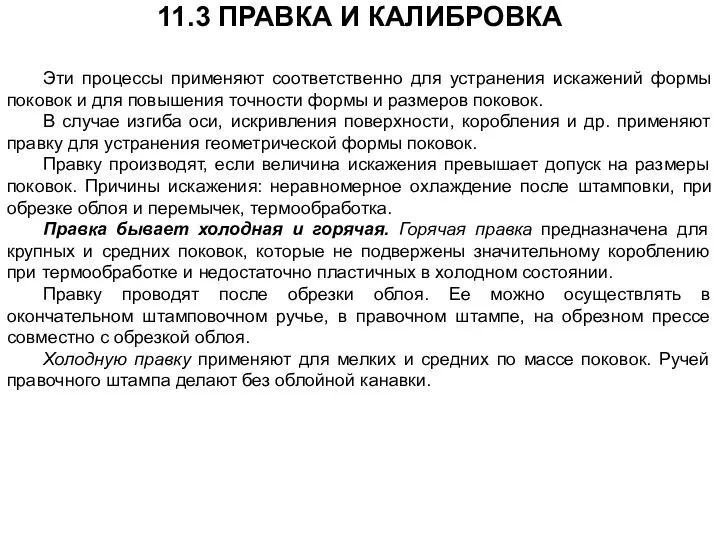
В случае изгиба оси, искривления поверхности, коробления и др. применяют правку для устранения геометрической формы поковок.
Правку производят, если величина искажения превышает допуск на размеры поковок. Причины искажения: неравномерное охлаждение после штамповки, при обрезке облоя и перемычек, термообработка.
Правка бывает холодная и горячая. Горячая правка предназначена для крупных и средних поковок, которые не подвержены значительному короблению при термообработке и недостаточно пластичных в холодном состоянии.
Правку проводят после обрезки облоя. Ее можно осуществлять в окончательном штамповочном ручье, в правочном штампе, на обрезном прессе совместно с обрезкой облоя.
Холодную правку применяют для мелких и средних по массе поковок. Ручей правочного штампа делают без облойной канавки.
11.3 ПРАВКА И КАЛИБРОВКА
Слайд 6Рисунок 11.2 – Схема правильного пресса с программным управлением
1 – подающе-удаляющее
Рисунок 11.2 – Схема правильного пресса с программным управлением
1 – подающе-удаляющее
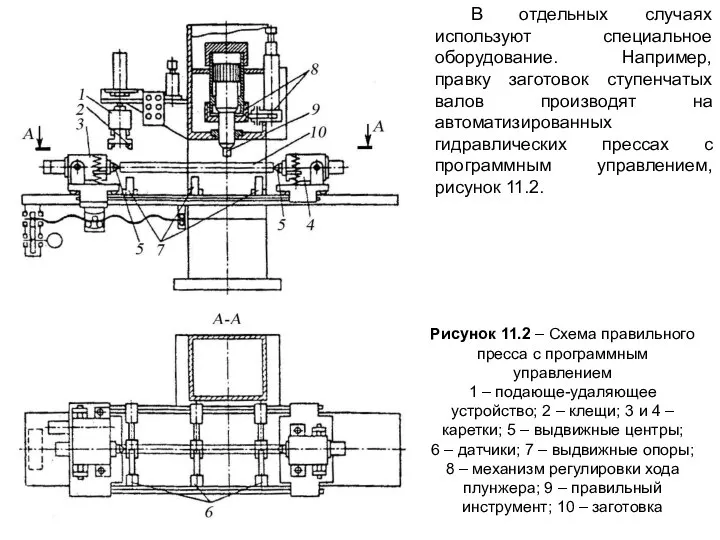
6 – датчики; 7 – выдвижные опоры; 8 – механизм регулировки хода плунжера; 9 – правильный инструмент; 10 – заготовка
В отдельных случаях используют специальное оборудование. Например, правку заготовок ступенчатых валов производят на автоматизированных гидравлических прессах с программным управлением, рисунок 11.2.
Слайд 7 Заготовка 10 захватывается клещами 2 и переносится на ось центров 5 и
Заготовка 10 захватывается клещами 2 и переносится на ось центров 5 и
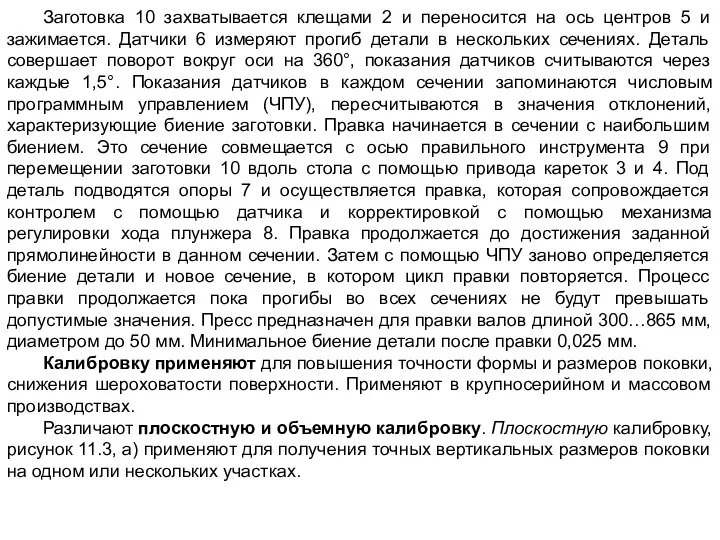
Калибровку применяют для повышения точности формы и размеров поковки, снижения шероховатости поверхности. Применяют в крупносерийном и массовом производствах.
Различают плоскостную и объемную калибровку. Плоскостную калибровку, рисунок 11.3, а) применяют для получения точных вертикальных размеров поковки на одном или нескольких участках.
Слайд 8 Калибровку проводят на прессах, отличающихся повышенной жесткостью, в штампах.
Объемная калибровка обеспечивает более
Калибровку проводят на прессах, отличающихся повышенной жесткостью, в штампах.
Объемная калибровка обеспечивает более
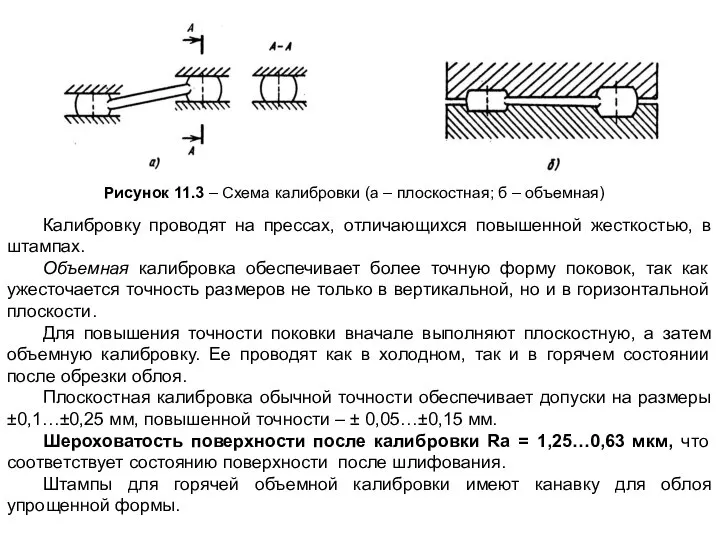
Для повышения точности поковки вначале выполняют плоскостную, а затем объемную калибровку. Ее проводят как в холодном, так и в горячем состоянии после обрезки облоя.
Плоскостная калибровка обычной точности обеспечивает допуски на размеры ±0,1…±0,25 мм, повышенной точности – ± 0,05…±0,15 мм.
Шероховатость поверхности после калибровки Ra = 1,25…0,63 мкм, что соответствует состоянию поверхности после шлифования.
Штампы для горячей объемной калибровки имеют канавку для облоя упрощенной формы.
Рисунок 11.3 – Схема калибровки (а – плоскостная; б – объемная)
Слайд 9 Применяемая термообработка включает нормализацию, изотермический отжиг, улучшение. Она позволяет улучшать обрабатываемость заготовок
Применяемая термообработка включает нормализацию, изотермический отжиг, улучшение. Она позволяет улучшать обрабатываемость заготовок
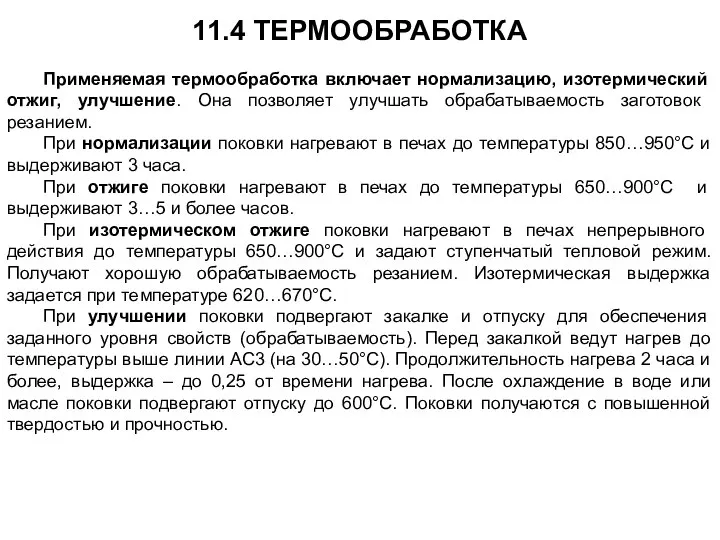
При нормализации поковки нагревают в печах до температуры 850…950°С и выдерживают 3 часа.
При отжиге поковки нагревают в печах до температуры 650…900°С и выдерживают 3…5 и более часов.
При изотермическом отжиге поковки нагревают в печах непрерывного действия до температуры 650…900°С и задают ступенчатый тепловой режим. Получают хорошую обрабатываемость резанием. Изотермическая выдержка задается при температуре 620…670°С.
При улучшении поковки подвергают закалке и отпуску для обеспечения заданного уровня свойств (обрабатываемость). Перед закалкой ведут нагрев до температуры выше линии АС3 (на 30…50°С). Продолжительность нагрева 2 часа и более, выдержка – до 0,25 от времени нагрева. После охлаждение в воде или масле поковки подвергают отпуску до 600°С. Поковки получаются с повышенной твердостью и прочностью.
11.4 ТЕРМООБРАБОТКА