Содержание
- 2. Abstract Two phase thermal passive systems do not have moving parts and are compact, reliable, and
- 3. Boiling and condensation are the key heat-transfer modes with high heat transfer coefficients and widespread applications
- 4. Part 1 Contracts: Short Historical overeviews of the Porous media laboratory Luikov HMTI NAN, Belarus with
- 5. 1. № HTS-HMTI- 01, YB2014090048. 30.09.2014 “To research and develop the technology to enhance the hot
- 6. 2.Contracts between BELHUAWEI (SOW) and Porous media Lab., Luikov Insitute, HMTI NAN Belarus , 2018 –
- 7. 1. № YBN 2017060028 , 11.2017 – 2018, “Anti-Gravity Heat Pipe” Developed and tested antigravity copper
- 8. Temperature/time dependence of the heat pipe evaporator and condenser at various heat loads: 6-condenser, 7 –
- 9. 1. “Development, fabrication and research of compressible vapor chamber (CVC)”, 2018. 2. “To improve the thermal
- 10. The Compressible Vapor Chamber (CVC) and Capillary Week Structure Porous wick
- 11. 1.Compressible vapor chamber (CVC) Rth CVC sample CVC sample of the 1st stage tested data Experimental
- 12. Conclusions 1. In the process of performing the work, three CVC constructions have been developed, manufactured
- 13. 2. Statement of Work No. 2 (SOW-2) Improvement made the thermal performance of the existing vapor
- 14. SOW-2 VC thermal resistance depending of the heat load Characteristics of the innovated VC: VC heat
- 15. 1. BELHUAWEI SOW №1, 2019-2020 “Development, Fabrication and testing of the alumina loop thermosyphon (LTS) with
- 16. SOW №1, 2019-2020 “Development, Fabrication and testing of the alumina loop thermosyphon (LTS) with specified technical
- 18. Скачать презентацию
Слайд 2Abstract
Two phase thermal passive systems do not have moving parts and
Two phase thermal passive systems do not have moving parts and
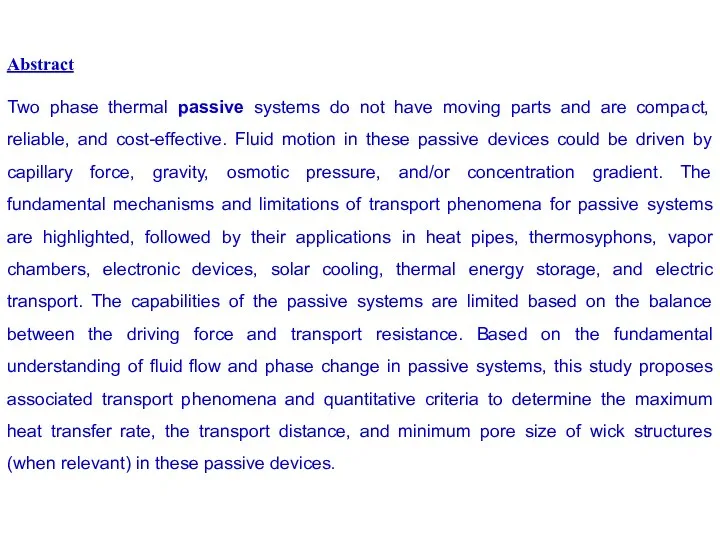
Слайд 3Boiling and condensation are the key heat-transfer modes with high heat transfer
Boiling and condensation are the key heat-transfer modes with high heat transfer
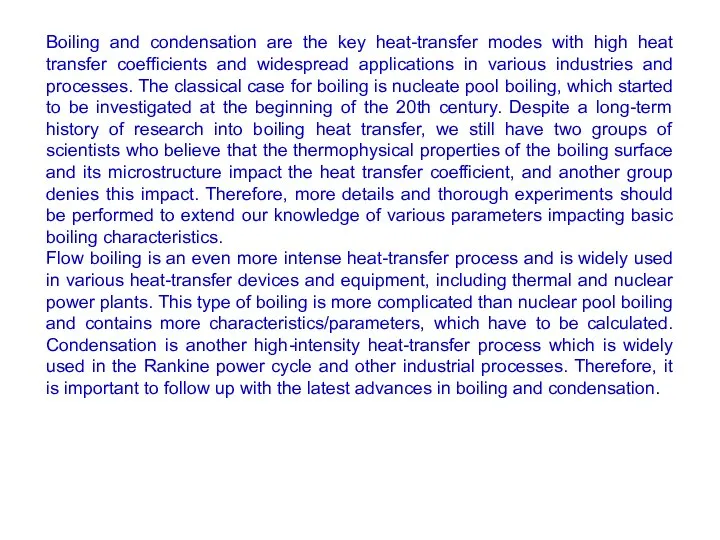
Flow boiling is an even more intense heat-transfer process and is widely used in various heat-transfer devices and equipment, including thermal and nuclear power plants. This type of boiling is more complicated than nuclear pool boiling and contains more characteristics/parameters, which have to be calculated. Condensation is another high-intensity heat-transfer process which is widely used in the Rankine power cycle and other industrial processes. Therefore, it is important to follow up with the latest advances in boiling and condensation.
Слайд 4Part 1
Contracts:
Short Historical overeviews of the Porous media laboratory
Luikov HMTI NAN,
Part 1
Contracts:
Short Historical overeviews of the Porous media laboratory
Luikov HMTI NAN,
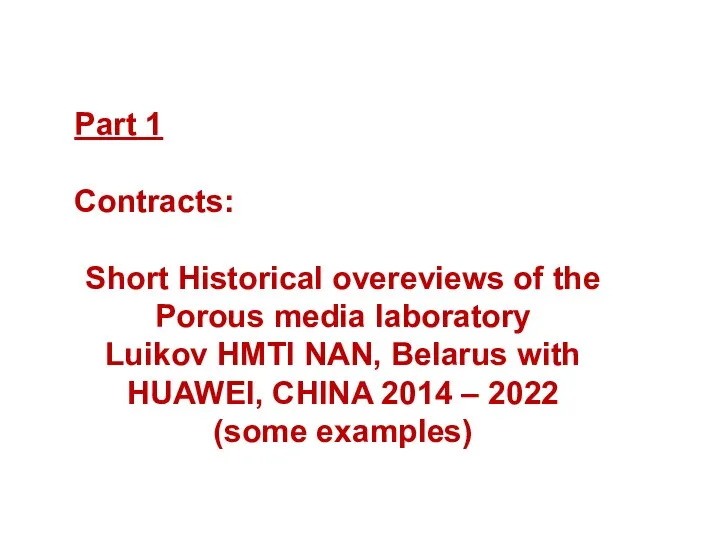
(some examples)
Слайд 5
1. № HTS-HMTI- 01, YB2014090048. 30.09.2014
“To research and develop the technology to
1. № HTS-HMTI- 01, YB2014090048. 30.09.2014
“To research and develop the technology to
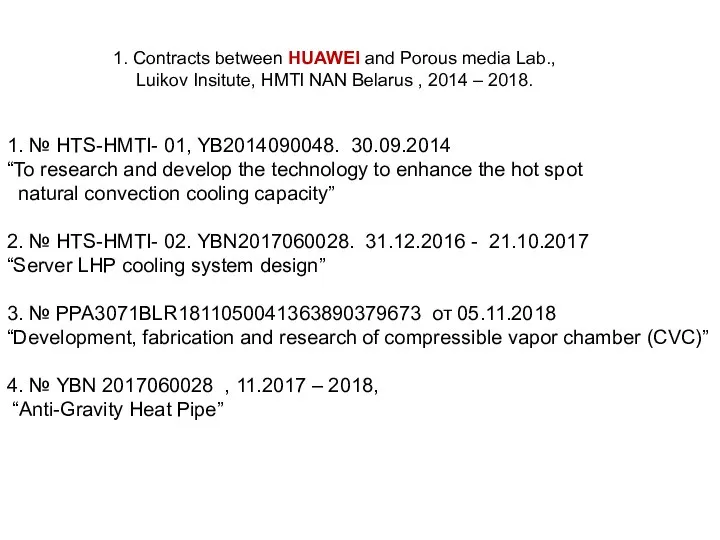
natural convection cooling capacity”
2. № HTS-HMTI- 02. YBN2017060028. 31.12.2016 - 21.10.2017
“Server LHP cooling system design”
3. № PPA3071BLR1811050041363890379673 от 05.11.2018
“Development, fabrication and research of compressible vapor chamber (CVC)”
4. № YBN 2017060028 , 11.2017 – 2018,
“Anti-Gravity Heat Pipe”
1. Contracts between HUAWEI and Porous media Lab.,
Luikov Insitute, HMTI NAN Belarus , 2014 – 2018.
Слайд 62.Contracts between BELHUAWEI (SOW) and Porous media Lab.,
Luikov Insitute, HMTI NAN
Luikov Insitute, HMTI NAN
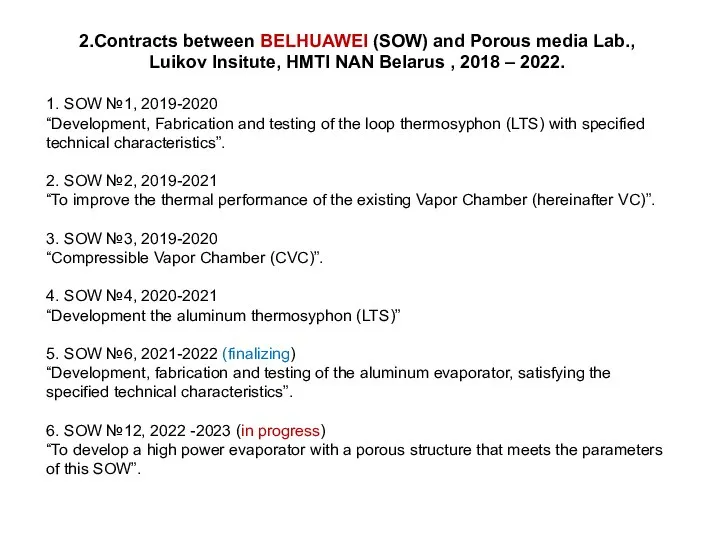
1. SOW №1, 2019-2020
“Development, Fabrication and testing of the loop thermosyphon (LTS) with specified technical characteristics”.
2. SOW №2, 2019-2021
“To improve the thermal performance of the existing Vapor Chamber (hereinafter VC)”.
3. SOW №3, 2019-2020
“Compressible Vapor Chamber (CVC)”.
4. SOW №4, 2020-2021
“Development the aluminum thermosyphon (LTS)”
5. SOW №6, 2021-2022 (finalizing)
“Development, fabrication and testing of the aluminum evaporator, satisfying the specified technical characteristics”.
6. SOW №12, 2022 -2023 (in progress)
“To develop a high power evaporator with a porous structure that meets the parameters of this SOW”.
Слайд 7
1. № YBN 2017060028 , 11.2017 – 2018, “Anti-Gravity Heat Pipe”
Developed and
1. № YBN 2017060028 , 11.2017 – 2018, “Anti-Gravity Heat Pipe”
Developed and
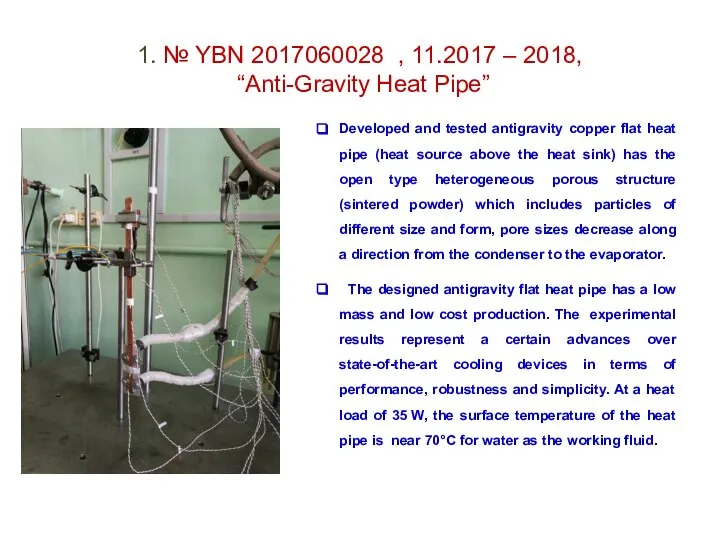
The designed antigravity flat heat pipe has a low mass and low cost production. The experimental results represent a certain advances over state-of-the-art cooling devices in terms of performance, robustness and simplicity. At a heat load of 35 W, the surface temperature of the heat pipe is near 70°C for water as the working fluid.
Слайд 8Temperature/time dependence of the heat pipe evaporator and condenser at various heat
Temperature/time dependence of the heat pipe evaporator and condenser at various heat

Anti-gravity flat heat pipe - 300 mm long, 12 mm width and 3 mm thick
Слайд 91. “Development, fabrication and research of compressible vapor chamber (CVC)”, 2018.
2. “To
2. “To
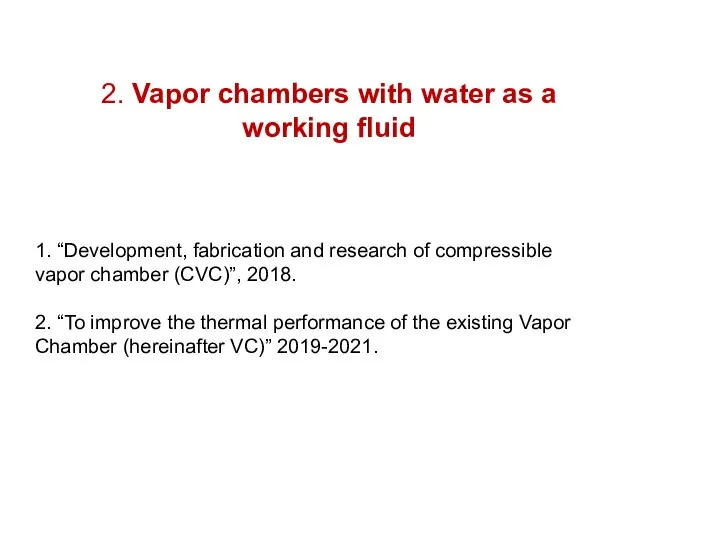
2. Vapor chambers with water as a working fluid
Слайд 10The Compressible Vapor Chamber (CVC) and Capillary Week Structure
Porous wick
The Compressible Vapor Chamber (CVC) and Capillary Week Structure
Porous wick
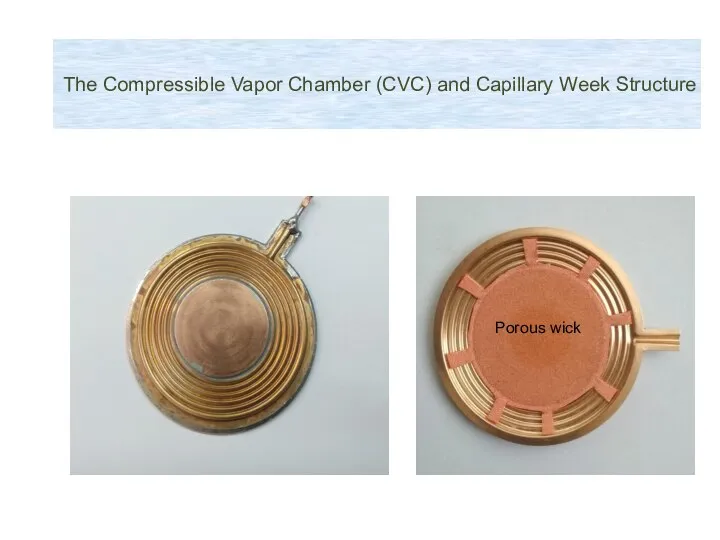
Слайд 111.Compressible vapor chamber (CVC)
Rth < 0.1K/W target was successfully achieved. The main
1.Compressible vapor chamber (CVC)
Rth < 0.1K/W target was successfully achieved. The main
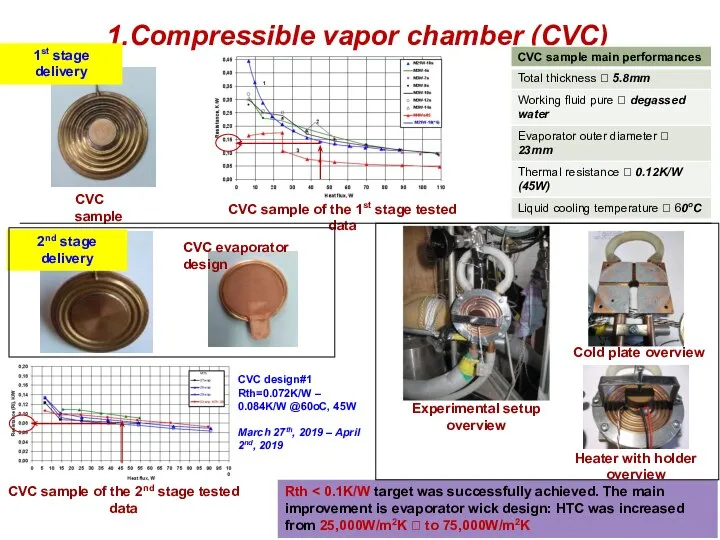
CVC sample
CVC sample of the 1st stage tested data
Experimental setup overview
Cold plate overview
Heater with holder overview
1st stage delivery
CVC design#1
Rth=0.072K/W – 0.084K/W @60oC, 45W
March 27th, 2019 – April 2nd, 2019
CVC evaporator design
2nd stage delivery
CVC sample of the 2nd stage tested data
Слайд 12Conclusions
1. In the process of performing the work, three CVC constructions
Conclusions
1. In the process of performing the work, three CVC constructions
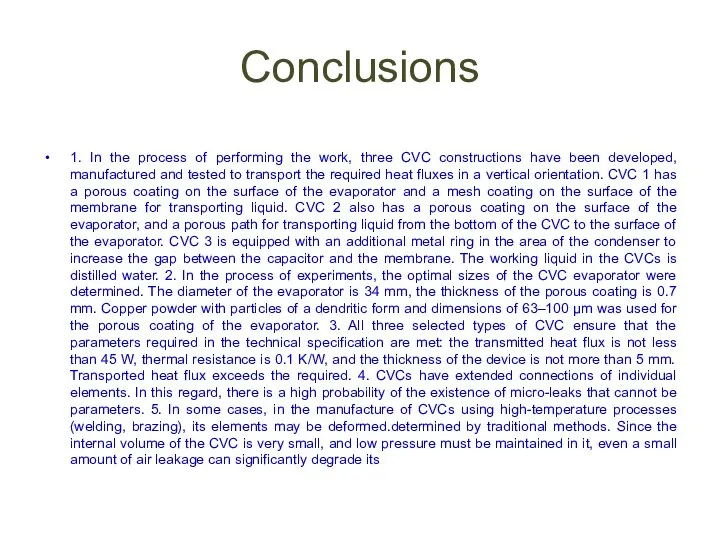
Слайд 13
2. Statement of Work No. 2 (SOW-2)
Improvement made the thermal performance of
2. Statement of Work No. 2 (SOW-2) Improvement made the thermal performance of
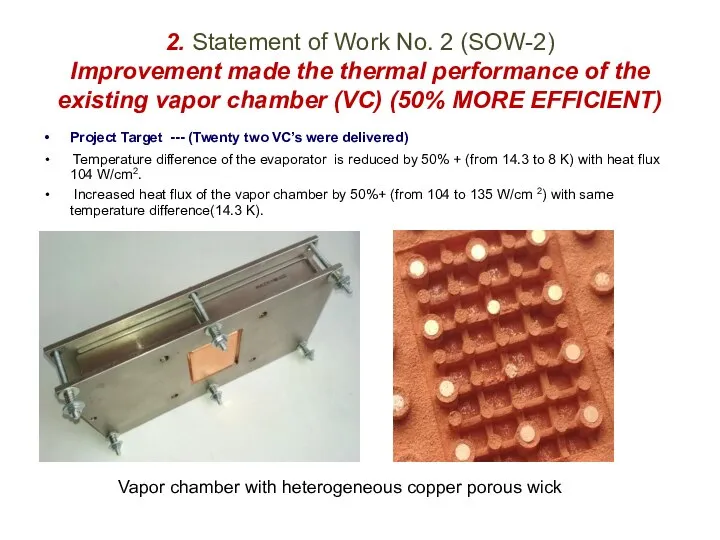
Project Target --- (Twenty two VC’s were delivered)
Temperature difference of the evaporator is reduced by 50% + (from 14.3 to 8 K) with heat flux 104 W/cm2.
Increased heat flux of the vapor chamber by 50%+ (from 104 to 135 W/cm 2) with same temperature difference(14.3 K).
Vapor chamber with heterogeneous copper porous wick
Слайд 14 SOW-2
VC thermal resistance depending of the heat load
Characteristics
SOW-2
VC thermal resistance depending of the heat load
Characteristics
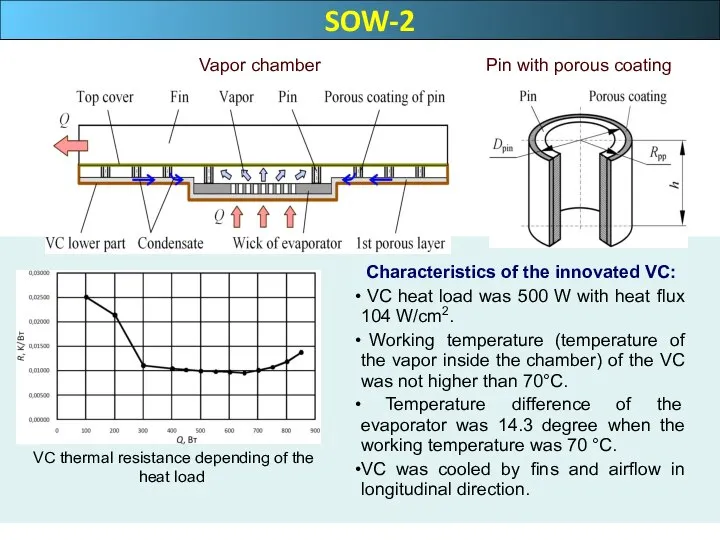
VC heat load was 500 W with heat flux 104 W/cm2.
Working temperature (temperature of the vapor inside the chamber) of the VC was not higher than 70°C.
Temperature difference of the evaporator was 14.3 degree when the working temperature was 70 °C.
VC was cooled by fins and airflow in longitudinal direction.
Vapor chamber
Pin with porous coating
Слайд 151. BELHUAWEI SOW №1, 2019-2020
“Development, Fabrication and testing of the alumina loop
1. BELHUAWEI SOW №1, 2019-2020 “Development, Fabrication and testing of the alumina loop
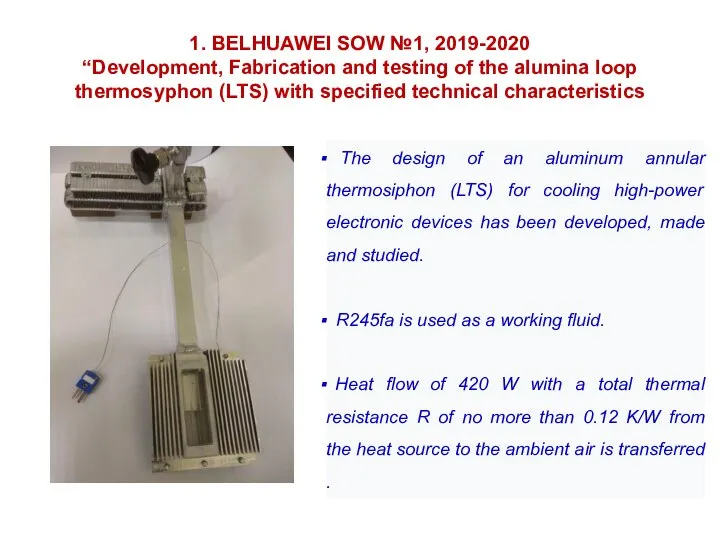
The design of an aluminum annular thermosiphon (LTS) for cooling high-power electronic devices has been developed, made and studied.
R245fa is used as a working fluid.
Heat flow of 420 W with a total thermal resistance R of no more than 0.12 K/W from the heat source to the ambient air is transferred .
Слайд 16SOW №1, 2019-2020
“Development, Fabrication and testing of the alumina loop thermosyphon (LTS)
SOW №1, 2019-2020 “Development, Fabrication and testing of the alumina loop thermosyphon (LTS)
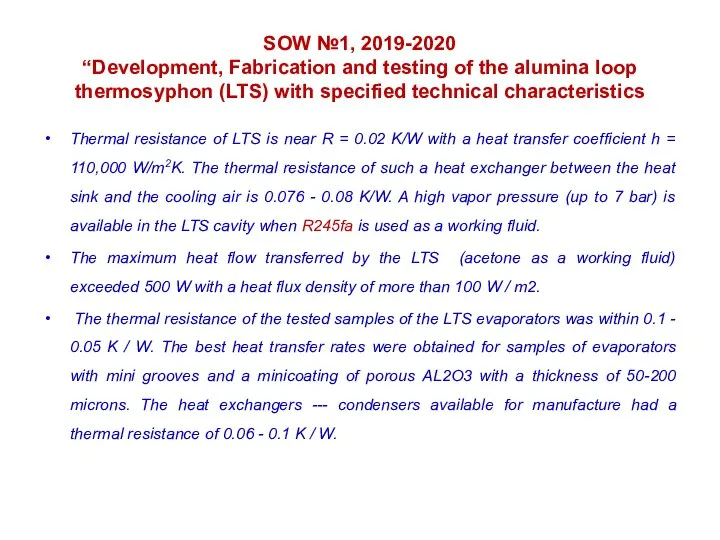
Thermal resistance of LTS is near R = 0.02 K/W with a heat transfer coefficient h = 110,000 W/m2K. The thermal resistance of such a heat exchanger between the heat sink and the cooling air is 0.076 - 0.08 K/W. A high vapor pressure (up to 7 bar) is available in the LTS cavity when R245fa is used as a working fluid.
The maximum heat flow transferred by the LTS (acetone as a working fluid) exceeded 500 W with a heat flux density of more than 100 W / m2.
The thermal resistance of the tested samples of the LTS evaporators was within 0.1 - 0.05 K / W. The best heat transfer rates were obtained for samples of evaporators with mini grooves and a minicoating of porous AL2O3 with a thickness of 50-200 microns. The heat exchangers --- condensers available for manufacture had a thermal resistance of 0.06 - 0.1 K / W.