Содержание
- 2. Обкатка — операция технологического процесса ремонта, при которой реализуется процесс приработки рабочих поверхностей деталей. Это приводит
- 3. В комплект стенда входит реостат, позволяющий регулировать частоту вращения двигателя при «холодной» обкатке и обеспечивать нагружение
- 4. Обкатку агрегатов ходовой части выполняют также на специальных стендах. Так, для обкатки кареток гусеничных тракторов служит
- 5. ИСПЫТАНИЕ ОТРЕМОНТИРОВАННЫХ МАШИН: НАЗНАЧЕНИЕ, РЕЖИМЫ, КОНТРОЛИРУЕМЫЕ ПАРАМЕТРЫ Испытание объектов — операция технологического процесса, при которой оценивают
- 6. Мощность двигателя при работе на прямой передаче определяют по формуле где Мкр = 0,7162Р — крутящий
- 7. По окончании обкатки и испытания двигатель осматривают, снимают с обкаточного стенда и устанавливают на стенд контрольного
- 8. Окраска. Окраской предохраняют части машины от вредных атмосферных воздействий, улучшают их внешний вид и видимость при
- 9. Недостатки этого способа: значительные потери краски при распылении, пожароопасность и токсичность. Окраску распылением следует выполнять в
- 10. Окраска безвоздушным распылением является более прогрессивным способом, она получила в настоящее время широкое распространение. Установки безвоздушного
- 11. Окраска окунанием заключается в погружении изделия в ванну с лакокрасочным материалом. Через некоторое время изделие вынимают
- 12. Сушка. После нанесения каждого слоя лакокрасочных материалов проводится сушка. Она может быть естественной и искусственной. Процессы
- 13. Контроль качества окраски изделий. Контроль осуществляют осмотром, измерениями толщины нанесенного слоя пленки и адгезионных свойств подготовленной
- 14. Цифровой толщиномер лакокрасочных и порошковых покрытий Elcometer 415 Новый толшиномер покрытий Elcometer 415 предназначен для быстрого
- 16. Скачать презентацию
Слайд 2 Обкатка — операция технологического процесса ремонта, при которой реализуется процесс приработки рабочих
Обкатка — операция технологического процесса ремонта, при которой реализуется процесс приработки рабочих
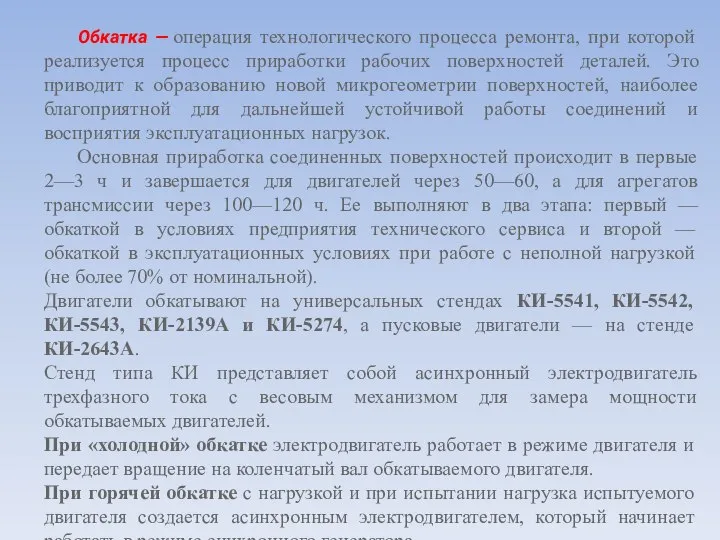
Основная приработка соединенных поверхностей происходит в первые 2—3 ч и завершается для двигателей через 50—60, а для агрегатов трансмиссии через 100—120 ч. Ее выполняют в два этапа: первый — обкаткой в условиях предприятия технического сервиса и второй — обкаткой в эксплуатационных условиях при работе с неполной нагрузкой (не более 70% от номинальной).
Двигатели обкатывают на универсальных стендах КИ-5541, КИ-5542, КИ-5543, КИ-2139А и КИ-5274, а пусковые двигатели — на стенде КИ-2643А.
Стенд типа КИ представляет собой асинхронный электродвигатель трехфазного тока с весовым механизмом для замера мощности обкатываемых двигателей.
При «холодной» обкатке электродвигатель работает в режиме двигателя и передает вращение на коленчатый вал обкатываемого двигателя.
При горячей обкатке с нагрузкой и при испытании нагрузка испытуемого двигателя создается асинхронным электродвигателем, который начинает работать в режиме синхронного генератора.
Слайд 3 В комплект стенда входит реостат, позволяющий регулировать частоту вращения двигателя при
В комплект стенда входит реостат, позволяющий регулировать частоту вращения двигателя при
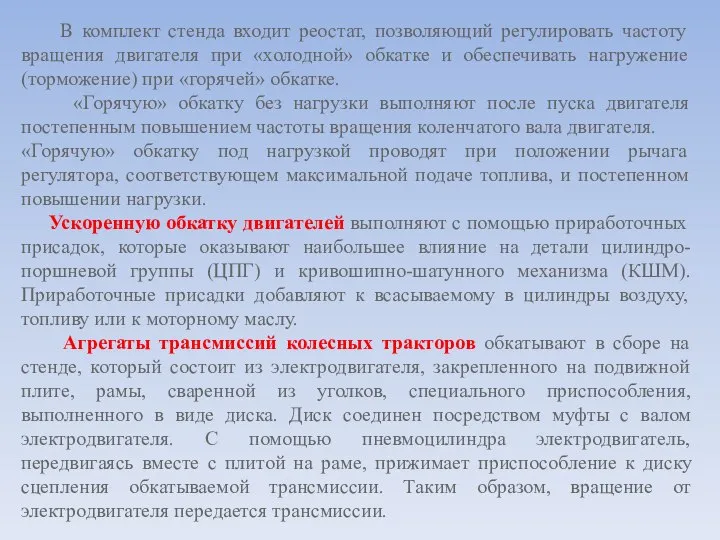
«Горячую» обкатку без нагрузки выполняют после пуска двигателя постепенным повышением частоты вращения коленчатого вала двигателя.
«Горячую» обкатку под нагрузкой проводят при положении рычага регулятора, соответствующем максимальной подаче топлива, и постепенном повышении нагрузки.
Ускоренную обкатку двигателей выполняют с помощью приработочных присадок, которые оказывают наибольшее влияние на детали цилиндро-поршневой группы (ЦПГ) и кривошипно-шатунного механизма (КШМ). Приработочные присадки добавляют к всасываемому в цилиндры воздуху, топливу или к моторному маслу.
Агрегаты трансмиссий колесных тракторов обкатывают в сборе на стенде, который состоит из электродвигателя, закрепленного на подвижной плите, рамы, сваренной из уголков, специального приспособления, выполненного в виде диска. Диск соединен посредством муфты с валом электродвигателя. С помощью пневмоцилиндра электродвигатель, передвигаясь вместе с плитой на раме, прижимает приспособление к диску сцепления обкатываемой трансмиссии. Таким образом, вращение от электродвигателя передается трансмиссии.
Слайд 4 Обкатку агрегатов ходовой части выполняют также на специальных стендах. Так, для
Обкатку агрегатов ходовой части выполняют также на специальных стендах. Так, для
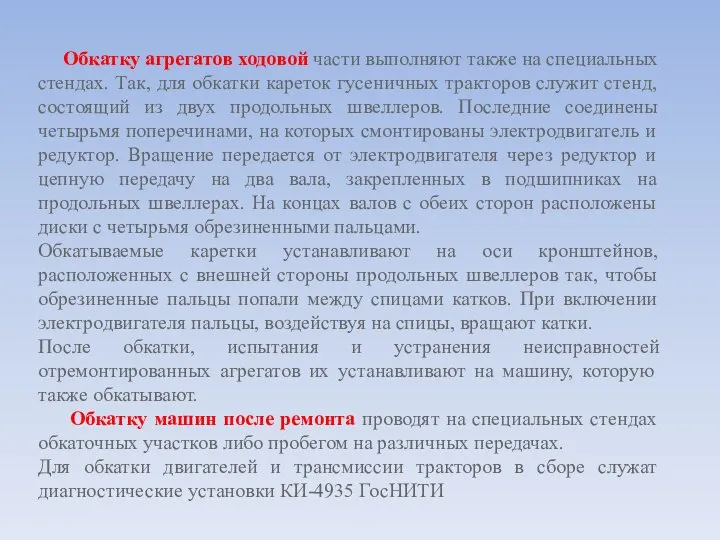
Обкатываемые каретки устанавливают на оси кронштейнов, расположенных с внешней стороны продольных швеллеров так, чтобы обрезиненные пальцы попали между спицами катков. При включении электродвигателя пальцы, воздействуя на спицы, вращают катки.
После обкатки, испытания и устранения неисправностей отремонтированных агрегатов их устанавливают на машину, которую также обкатывают.
Обкатку машин после ремонта проводят на специальных стендах обкаточных участков либо пробегом на различных передачах.
Для обкатки двигателей и трансмиссии тракторов в сборе служат диагностические установки КИ-4935 ГосНИТИ
Слайд 5ИСПЫТАНИЕ ОТРЕМОНТИРОВАННЫХ МАШИН: НАЗНАЧЕНИЕ, РЕЖИМЫ, КОНТРОЛИРУЕМЫЕ ПАРАМЕТРЫ
Испытание объектов — операция технологического процесса,
ИСПЫТАНИЕ ОТРЕМОНТИРОВАННЫХ МАШИН: НАЗНАЧЕНИЕ, РЕЖИМЫ, КОНТРОЛИРУЕМЫЕ ПАРАМЕТРЫ
Испытание объектов — операция технологического процесса,
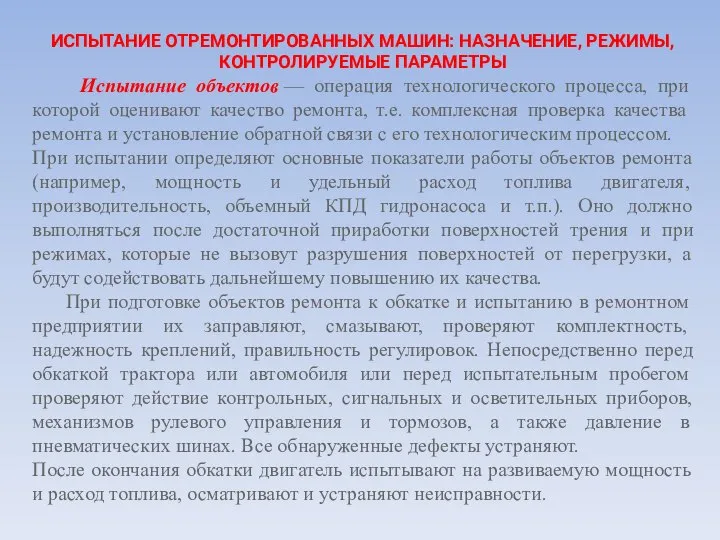
При испытании определяют основные показатели работы объектов ремонта (например, мощность и удельный расход топлива двигателя, производительность, объемный КПД гидронасоса и т.п.). Оно должно выполняться после достаточной приработки поверхностей трения и при режимах, которые не вызовут разрушения поверхностей от перегрузки, а будут содействовать дальнейшему повышению их качества.
При подготовке объектов ремонта к обкатке и испытанию в ремонтном предприятии их заправляют, смазывают, проверяют комплектность, надежность креплений, правильность регулировок. Непосредственно перед обкаткой трактора или автомобиля или перед испытательным пробегом проверяют действие контрольных, сигнальных и осветительных приборов, механизмов рулевого управления и тормозов, а также давление в пневматических шинах. Все обнаруженные дефекты устраняют.
После окончания обкатки двигатель испытывают на развиваемую мощность и расход топлива, осматривают и устраняют неисправности.
Слайд 6Мощность двигателя при работе на прямой передаче определяют по формуле
где Мкр = 0,7162Р — крутящий момент
Мощность двигателя при работе на прямой передаче определяют по формуле
где Мкр = 0,7162Р — крутящий момент
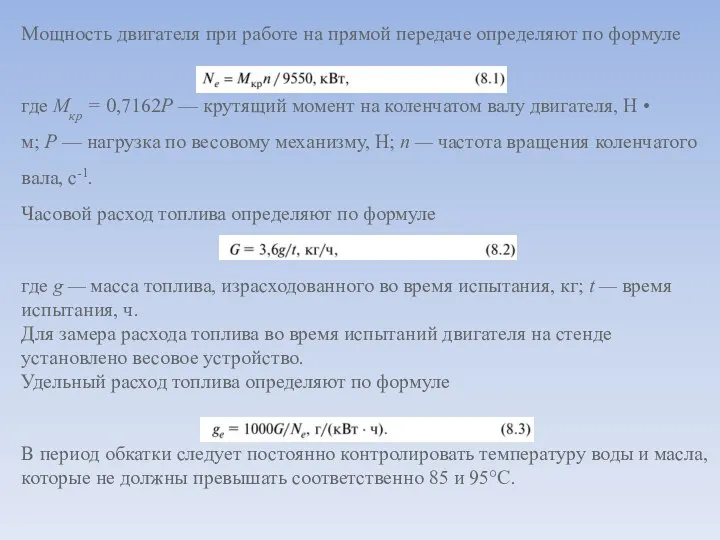
Часовой расход топлива определяют по формуле
где g — масса топлива, израсходованного во время испытания, кг; t — время испытания, ч.
Для замера расхода топлива во время испытаний двигателя на стенде установлено весовое устройство.
Удельный расход топлива определяют по формуле
В период обкатки следует постоянно контролировать температуру воды и масла, которые не должны превышать соответственно 85 и 95°С.
Слайд 7 По окончании обкатки и испытания двигатель осматривают, снимают с обкаточного стенда
По окончании обкатки и испытания двигатель осматривают, снимают с обкаточного стенда
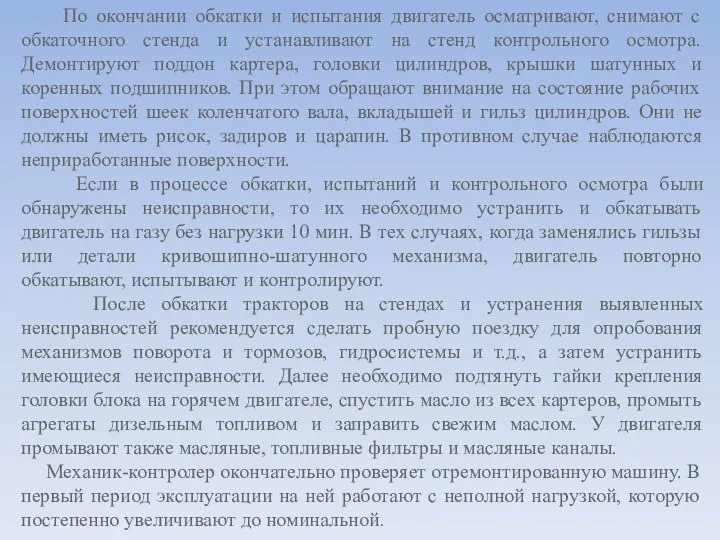
Если в процессе обкатки, испытаний и контрольного осмотра были обнаружены неисправности, то их необходимо устранить и обкатывать двигатель на газу без нагрузки 10 мин. В тех случаях, когда заменялись гильзы или детали кривошипно-шатунного механизма, двигатель повторно обкатывают, испытывают и контролируют.
После обкатки тракторов на стендах и устранения выявленных неисправностей рекомендуется сделать пробную поездку для опробования механизмов поворота и тормозов, гидросистемы и т.д., а затем устранить имеющиеся неисправности. Далее необходимо подтянуть гайки крепления головки блока на горячем двигателе, спустить масло из всех картеров, промыть агрегаты дизельным топливом и заправить свежим маслом. У двигателя промывают также масляные, топливные фильтры и масляные каналы.
Механик-контролер окончательно проверяет отремонтированную машину. В первый период эксплуатации на ней работают с неполной нагрузкой, которую постепенно увеличивают до номинальной.
Слайд 8Окраска.
Окраской предохраняют части машины от вредных атмосферных воздействий, улучшают их внешний
Окраска.
Окраской предохраняют части машины от вредных атмосферных воздействий, улучшают их внешний
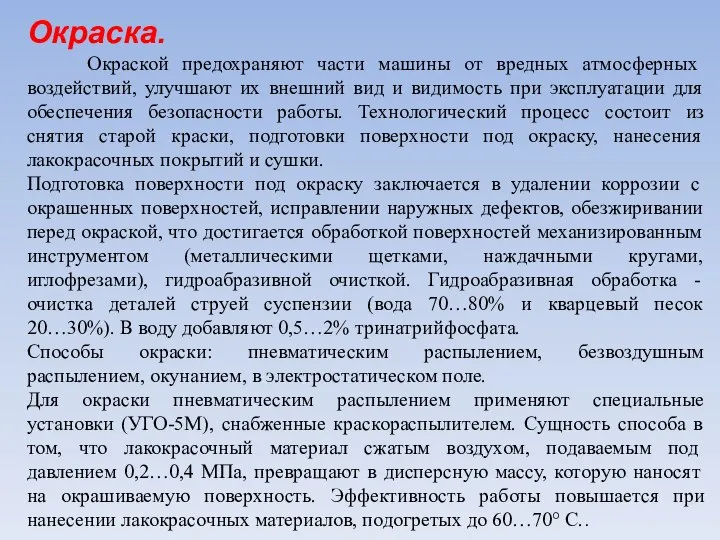
Подготовка поверхности под окраску заключается в удалении коррозии с окрашенных поверхностей, исправлении наружных дефектов, обезжиривании перед окраской, что достигается обработкой поверхностей механизированным инструментом (металлическими щетками, наждачными кругами, иглофрезами), гидроабразивной очисткой. Гидроабразивная обработка - очистка деталей струей суспензии (вода 70…80% и кварцевый песок 20…30%). В воду добавляют 0,5…2% тринатрийфосфата.
Способы окраски: пневматическим распылением, безвоздушным распылением, окунанием, в электростатическом поле.
Для окраски пневматическим распылением применяют специальные установки (УГО-5М), снабженные краскораспылителем. Сущность способа в том, что лакокрасочный материал сжатым воздухом, подаваемым под давлением 0,2…0,4 МПа, превращают в дисперсную массу, которую наносят на окрашиваемую поверхность. Эффективность работы повышается при нанесении лакокрасочных материалов, подогретых до 60…70° С..
Слайд 9 Недостатки этого способа: значительные потери краски при распылении, пожароопасность и токсичность.
Недостатки этого способа: значительные потери краски при распылении, пожароопасность и токсичность.
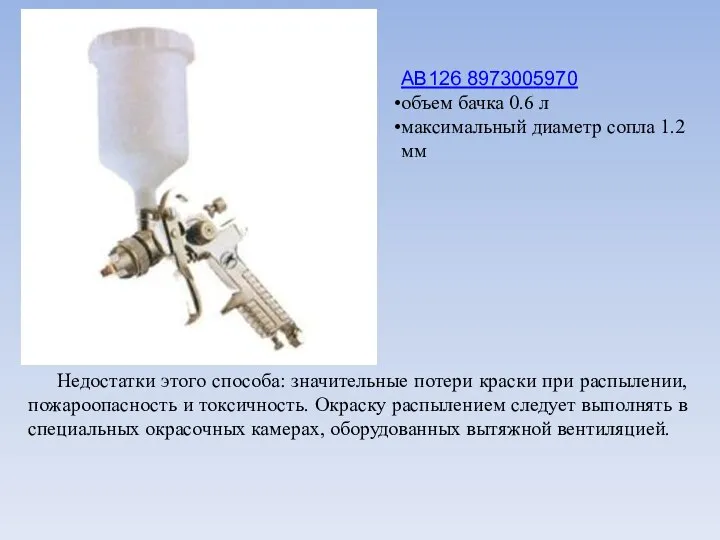
Краскопульт пневматический ABAC AB126 8973005970
объем бачка 0.6 л
максимальный диаметр сопла 1.2 мм
Слайд 10Окраска безвоздушным распылением является более прогрессивным способом, она получила в настоящее время
Окраска безвоздушным распылением является более прогрессивным способом, она получила в настоящее время
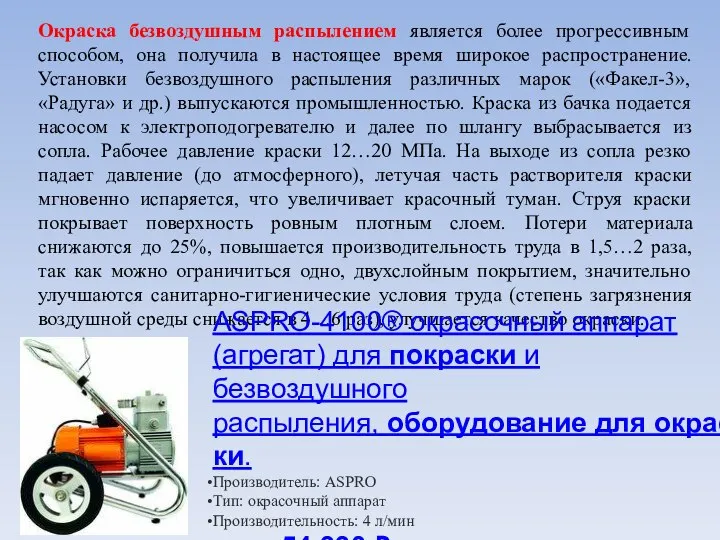
ASPRO-4100® окрасочный аппарат (агрегат) для покраски и безвоздушного распыления, оборудование для окраски.
Производитель: ASPRO
Тип: окрасочный аппарат
Производительность: 4 л/мин
ASPRO 54 990 ₽
Слайд 11 Окраска окунанием заключается в погружении изделия в ванну с лакокрасочным материалом.
Окраска окунанием заключается в погружении изделия в ванну с лакокрасочным материалом.
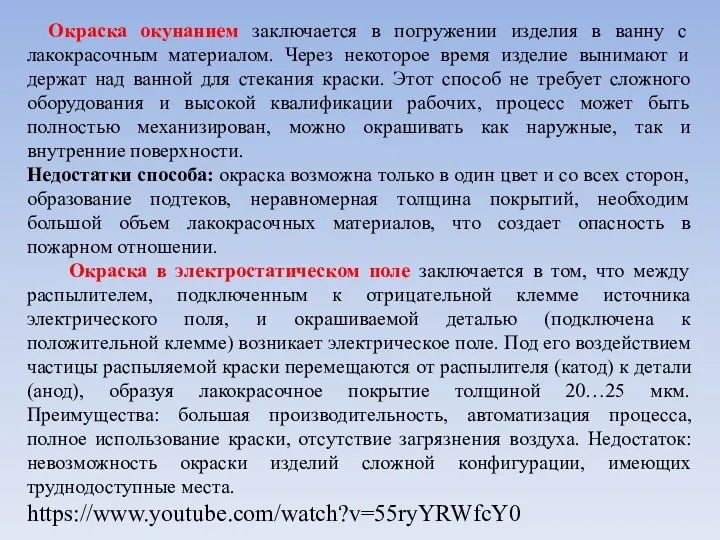
Недостатки способа: окраска возможна только в один цвет и со всех сторон, образование подтеков, неравномерная толщина покрытий, необходим большой объем лакокрасочных материалов, что создает опасность в пожарном отношении.
Окраска в электростатическом поле заключается в том, что между распылителем, подключенным к отрицательной клемме источника электрического поля, и окрашиваемой деталью (подключена к положительной клемме) возникает электрическое поле. Под его воздействием частицы распыляемой краски перемещаются от распылителя (катод) к детали (анод), образуя лакокрасочное покрытие толщиной 20…25 мкм. Преимущества: большая производительность, автоматизация процесса, полное использование краски, отсутствие загрязнения воздуха. Недостаток: невозможность окраски изделий сложной конфигурации, имеющих труднодоступные места.
https://www.youtube.com/watch?v=55ryYRWfcY0
Слайд 12 Сушка. После нанесения каждого слоя лакокрасочных материалов проводится сушка. Она может быть
Сушка. После нанесения каждого слоя лакокрасочных материалов проводится сушка. Она может быть
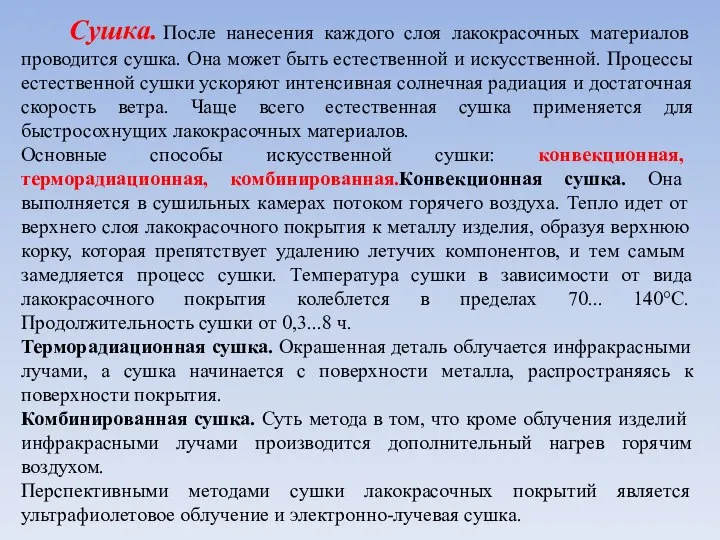
Основные способы искусственной сушки: конвекционная, терморадиационная, комбинированная.Конвекционная сушка. Она выполняется в сушильных камерах потоком горячего воздуха. Тепло идет от верхнего слоя лакокрасочного покрытия к металлу изделия, образуя верхнюю корку, которая препятствует удалению летучих компонентов, и тем самым замедляется процесс сушки. Температура сушки в зависимости от вида лакокрасочного покрытия колеблется в пределах 70... 140°С. Продолжительность сушки от 0,3...8 ч.
Терморадиационная сушка. Окрашенная деталь облучается инфракрасными лучами, а сушка начинается с поверхности металла, распространяясь к поверхности покрытия.
Комбинированная сушка. Суть метода в том, что кроме облучения изделий инфракрасными лучами производится дополнительный нагрев горячим воздухом.
Перспективными методами сушки лакокрасочных покрытий является ультрафиолетовое облучение и электронно-лучевая сушка.
Слайд 13Контроль качества окраски изделий.
Контроль осуществляют осмотром, измерениями толщины нанесенного слоя пленки и адгезионных
Контроль качества окраски изделий.
Контроль осуществляют осмотром, измерениями толщины нанесенного слоя пленки и адгезионных
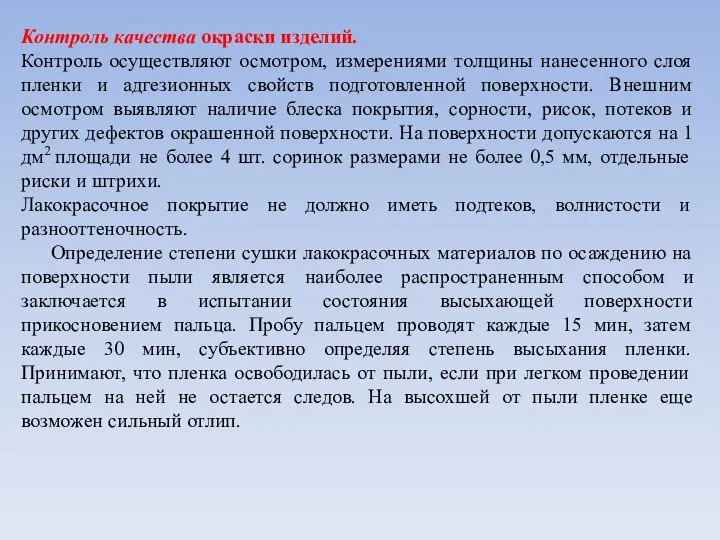
Лакокрасочное покрытие не должно иметь подтеков, волнистости и разнооттеночность.
Определение степени сушки лакокрасочных материалов по осаждению на поверхности пыли является наиболее распространенным способом и заключается в испытании состояния высыхающей поверхности прикосновением пальца. Пробу пальцем проводят каждые 15 мин, затем каждые 30 мин, субъективно определяя степень высыхания пленки. Принимают, что пленка освободилась от пыли, если при легком проведении пальцем на ней не остается следов. На высохшей от пыли пленке еще возможен сильный отлип.
Слайд 14Цифровой толщиномер лакокрасочных и порошковых покрытий Elcometer 415
Новый толшиномер покрытий Elcometer 415
Цифровой толщиномер лакокрасочных и порошковых покрытий Elcometer 415
Новый толшиномер покрытий Elcometer 415
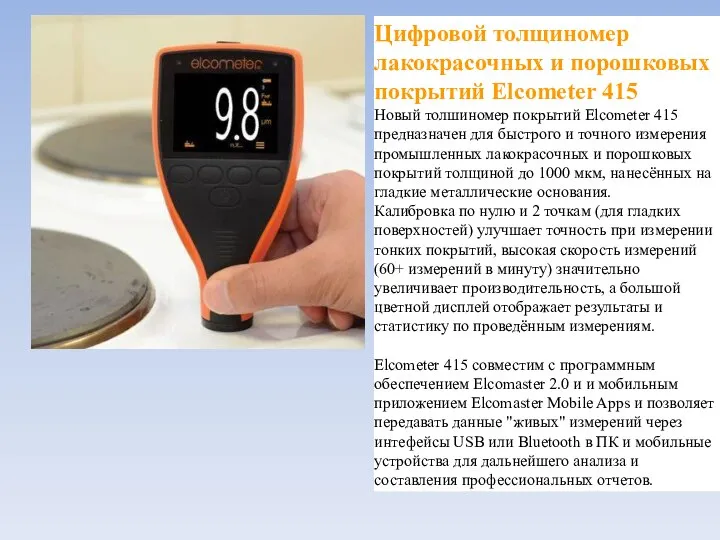
Калибровка по нулю и 2 точкам (для гладких поверхностей) улучшает точность при измерении тонких покрытий, высокая скорость измерений (60+ измерений в минуту) значительно увеличивает производительность, а большой цветной дисплей отображает результаты и статистику по проведённым измерениям. Elcometer 415 совместим с программным обеспечением Elcomaster 2.0 и и мобильным приложением Elcomaster Mobile Apps и позволяет передавать данные "живых" измерений через интефейсы USB или Bluetooth в ПК и мобильные устройства для дальнейшего анализа и составления профессиональных отчетов.