Содержание
- 2. * Plasma etching involves the generation of chemically reactive neutrals (e.g., F, Cl), and ions (e.g.,
- 3. * Asymmetric electrodes and low chamber pressures (5 Pa) are characteristic of RIE operation. Inductively coupled
- 4. * A different, purely physical method of etching is ion milling, in which noble-gas ions (usually
- 5. * Deep Reactive ion Etching (DRIE) DRIE evolved in the mid 1990s from the need within
- 6. * Another approach currently used by Alcatel, PlasmaTherm, and Surface Technology Systems (STS) follows a method
- 7. * The etch step has both vertical and isotropic character, resulting in a slight mask undercut
- 8. * Table 3.3 Process Characteristics of DRIE in the STS System Etch step 5–15s SF6 flow
- 9. * scalloping effect = эффект гребешка is exagerrated = усилен
- 10. *
- 11. * The repetitive alternation of the etch and passivation steps results in a very directional etch
- 12. * The etch rate is limited by the flux of reactants (namely, F radicals) and drops
- 13. * Figure 3.13 ARDE in DRIE. The etch rate decreases with increasing trench aspect ratio. (Courtesy
- 14. *
- 15. * The high selectivity to silicon dioxide makes it possible to etch deep trenches and stop
- 16. *
- 17. * Advanced Process Tools Anodic Bonding Anodic bonding, also known as field-assisted bonding or Mallory bonding,
- 18. *
- 19. * The bonding is complete when the ion current (measured externally as an electron current) vanishes,
- 20. * The coefficient of thermal expansion of the glass substrate is preferably matched to that of
- 21. * Silicon Direct Bonding Silicon direct bonding, also known as silicon fusion bonding, is a process
- 22. * Silicon direct bonding can be performed between two bare single-crystal silicon surfaces or polished polysilicon.
- 23. * The direct bonding process starts with cleaning and hydration of the surfaces. The following is
- 24. * Finally, an RCA-2 clean (hot hydrochloric acid and hydrogen peroxide solution) is done to remove
- 25. * In some cases, features on the two bond surfaces must be aligned to each other
- 26. * A mechanical clamping fixture holds the aligned wafers in position, separated by thin spacers at
- 27. * Grinding (шлифовка), Polishing, and Chemical-Mechanical Polishing Some applications use a thin layer of silicon (5
- 28. * The thickness reduction is achieved using grinding and polishing. The wafer stack is mounted on
- 29. * A wheel with a felt-like (фетровый) texture polishes the wafer surface using a slurry containing
- 30. * Chemical mechanical polishing, also known as chemical mechanical planarization (CMP), is commonly used in the
- 31. * Водоро́дный показа́тель Водоро́дный показа́тель, pH (произносится «пэ аш», английское произношение англ. pH — pi:eɪtʃ —
- 32. * Вывод значения pH В чистой водеВ чистой воде при 25 °C концентрации ионов водорода ([H+])
- 33. * Так как в кислых растворах [H+] > 10−7, то у кислых растворов pH 7. pH
- 34. * Некоторые значения pH ЭлектролитЭлектролит в свинцовых аккумуляторах Желудочный сок 1,0—2,0 ЛимонныйЛимонный сок (5% р-р лимонной
- 35. * Sol-Gel Deposition Methods A sol-gel process is a chemical reaction between solid particles in colloidal
- 36. * A widespread application of sol-gel processing is in the coating of surfaces with optical absorption
- 37. * Electroceramic properties Being piezoelectricBeing piezoelectric, it develops a voltage (or potential difference) across two of
- 38. * Varieties of PZTs Сommonly studied chemical composition is PbСommonly studied chemical composition is PbZr0.52Ti0.48O3. The
- 39. * A sol-gel process starts by dissolving appropriate chemical precursors in a liquid to form a
- 40. * For example, TEOS in water can be converted into a silica gel by hydrolysis (Гидро́лиз
- 41. * Silica gel is a granular is a granular, vitreous (стекловидный), porous, porous form of silicon
- 42. * Sodium silicate is the common name for a compound sodium metasilicate, Na2SiO3, also known as
- 44. Скачать презентацию
Слайд 2*
Plasma etching involves the generation of chemically reactive neutrals (e.g., F, Cl),
*
Plasma etching involves the generation of chemically reactive neutrals (e.g., F, Cl),
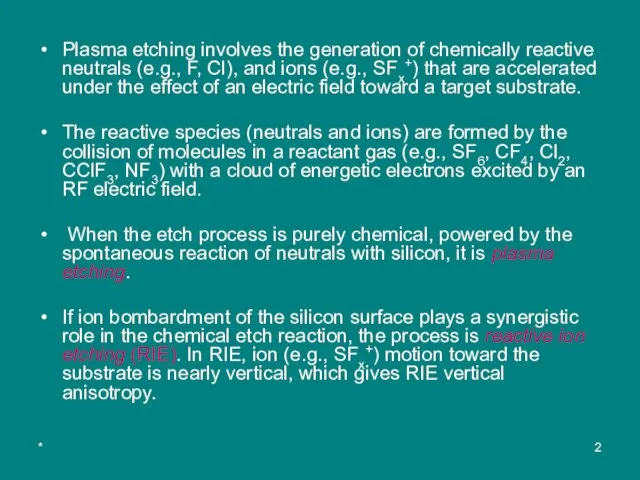
The reactive species (neutrals and ions) are formed by the collision of molecules in a reactant gas (e.g., SF6, CF4, Cl2, CClF3, NF3) with a cloud of energetic electrons excited by an RF electric field.
When the etch process is purely chemical, powered by the spontaneous reaction of neutrals with silicon, it is plasma etching.
If ion bombardment of the silicon surface plays a synergistic role in the chemical etch reaction, the process is reactive ion etching (RIE). In RIE, ion (e.g., SFx+) motion toward the substrate is nearly vertical, which gives RIE vertical anisotropy.
Слайд 3*
Asymmetric electrodes and low chamber pressures (5 Pa) are characteristic of RIE
*
Asymmetric electrodes and low chamber pressures (5 Pa) are characteristic of RIE
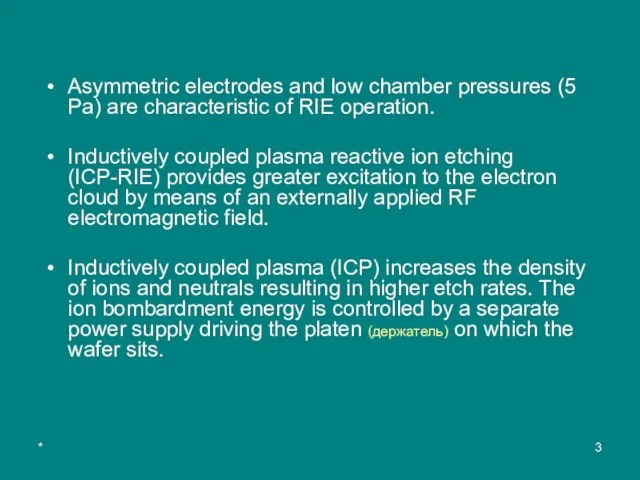
Inductively coupled plasma reactive ion etching (ICP-RIE) provides greater excitation to the electron cloud by means of an externally applied RF electromagnetic field.
Inductively coupled plasma (ICP) increases the density of ions and neutrals resulting in higher etch rates. The ion bombardment energy is controlled by a separate power supply driving the platen (держатель) on which the wafer sits.
Слайд 4*
A different, purely physical method of etching is ion milling, in which
*
A different, purely physical method of etching is ion milling, in which
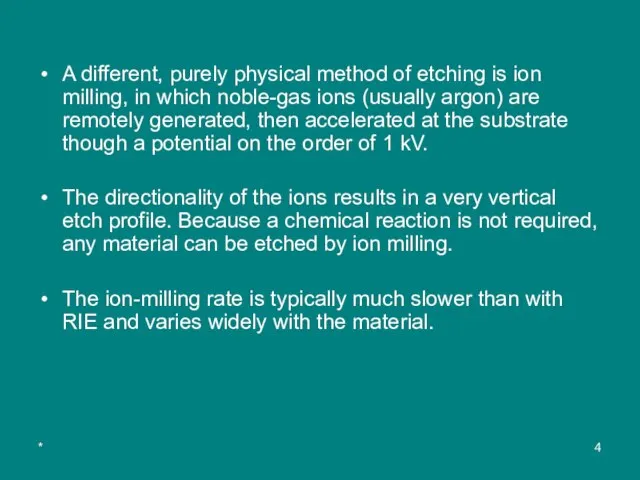
The directionality of the ions results in a very vertical etch profile. Because a chemical reaction is not required, any material can be etched by ion milling.
The ion-milling rate is typically much slower than with RIE and varies widely with the material.
Слайд 5*
Deep Reactive ion Etching (DRIE)
DRIE evolved in the mid 1990s from
*
Deep Reactive ion Etching (DRIE)
DRIE evolved in the mid 1990s from
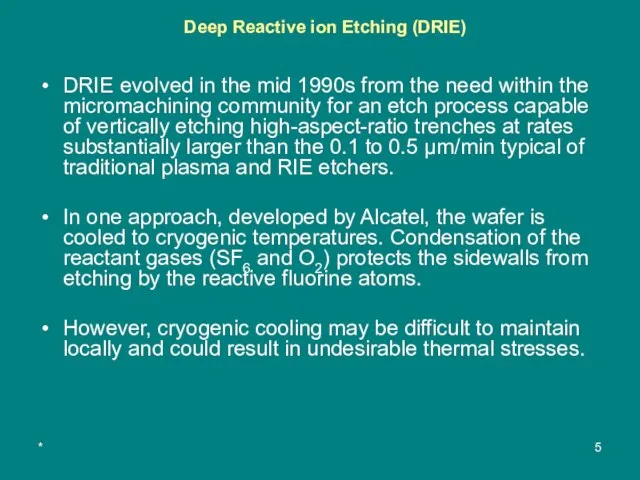
In one approach, developed by Alcatel, the wafer is cooled to cryogenic temperatures. Condensation of the reactant gases (SF6 and O2) protects the sidewalls from etching by the reactive fluorine atoms.
However, cryogenic cooling may be difficult to maintain locally and could result in undesirable thermal stresses.
Слайд 6*
Another approach currently used by Alcatel, PlasmaTherm, and Surface Technology Systems (STS)
*
Another approach currently used by Alcatel, PlasmaTherm, and Surface Technology Systems (STS)
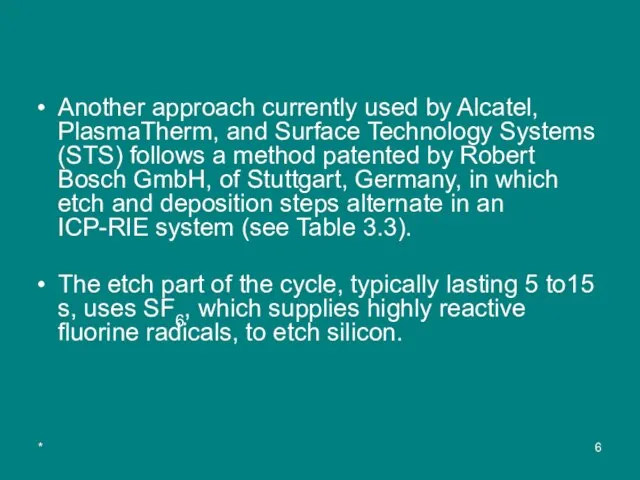
The etch part of the cycle, typically lasting 5 to15 s, uses SF6, which supplies highly reactive fluorine radicals, to etch silicon.
Слайд 7*
The etch step has both vertical and isotropic character, resulting in a
*
The etch step has both vertical and isotropic character, resulting in a
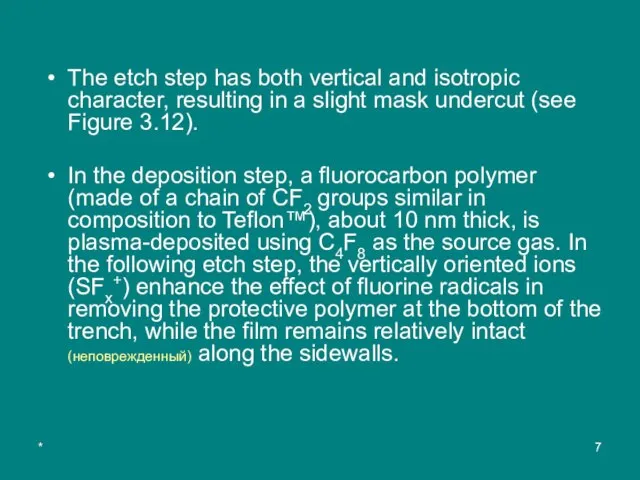
In the deposition step, a fluorocarbon polymer (made of a chain of CF2 groups similar in composition to Teflon™), about 10 nm thick, is plasma-deposited using C4F8 as the source gas. In the following etch step, the vertically oriented ions (SFx+) enhance the effect of fluorine radicals in removing the protective polymer at the bottom of the trench, while the film remains relatively intact (неповрежденный) along the sidewalls.
Слайд 8*
Table 3.3 Process Characteristics of DRIE in the STS System
Etch step
*
Table 3.3 Process Characteristics of DRIE in the STS System
Etch step
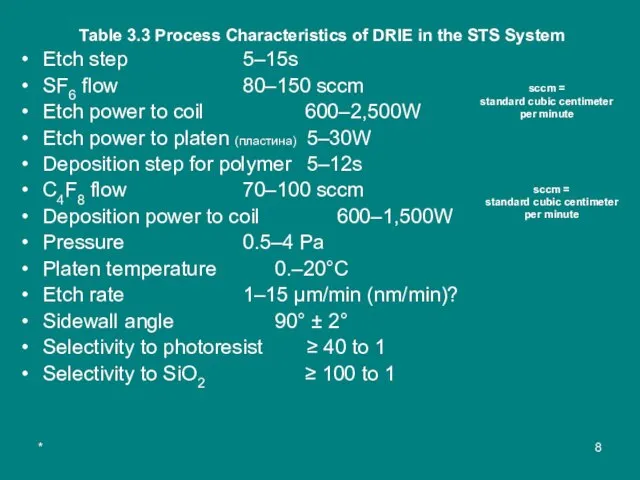
SF6 flow 80–150 sccm
Etch power to coil 600–2,500W
Etch power to platen (пластина) 5–30W
Deposition step for polymer 5–12s
C4F8 flow 70–100 sccm
Deposition power to coil 600–1,500W
Pressure 0.5–4 Pa
Platen temperature 0.–20°C
Etch rate 1–15 µm/min (nm/min)?
Sidewall angle 90° ± 2°
Selectivity to photoresist ≥ 40 to 1
Selectivity to SiO2 ≥ 100 to 1
sccm =
standard cubic centimeter per minute
sccm =
standard cubic centimeter per minute
Слайд 9*
scalloping effect = эффект гребешка
is exagerrated = усилен
*
scalloping effect = эффект гребешка
is exagerrated = усилен
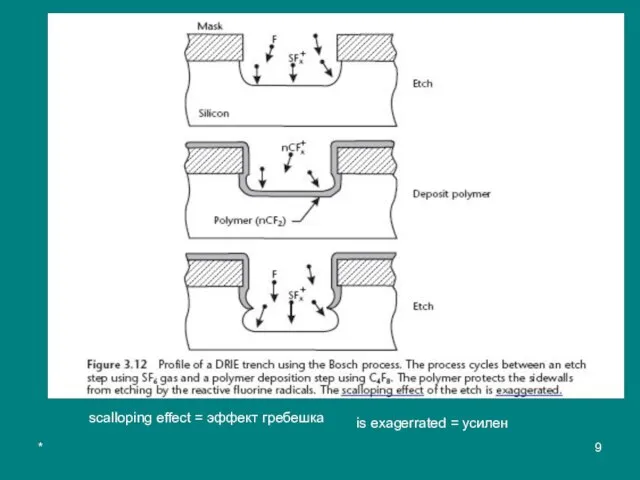
Слайд 11*
The repetitive alternation of the etch and passivation steps results in a
*
The repetitive alternation of the etch and passivation steps results in a
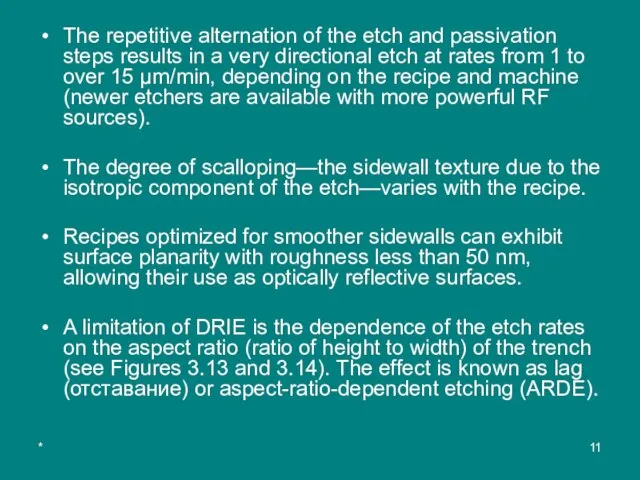
The degree of scalloping—the sidewall texture due to the isotropic component of the etch—varies with the recipe.
Recipes optimized for smoother sidewalls can exhibit surface planarity with roughness less than 50 nm, allowing their use as optically reflective surfaces.
A limitation of DRIE is the dependence of the etch rates on the aspect ratio (ratio of height to width) of the trench (see Figures 3.13 and 3.14). The effect is known as lag (отставание) or aspect-ratio-dependent etching (ARDE).
Слайд 12*
The etch rate is limited by the flux of reactants (namely, F
*
The etch rate is limited by the flux of reactants (namely, F
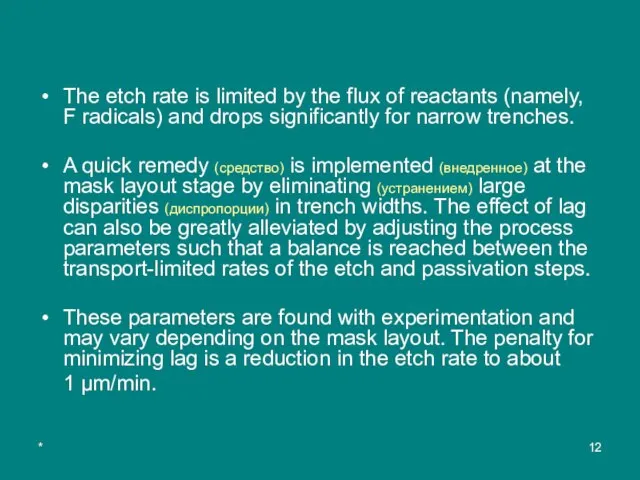
A quick remedy (средство) is implemented (внедренное) at the mask layout stage by eliminating (устранением) large disparities (диспропорции) in trench widths. The effect of lag can also be greatly alleviated by adjusting the process parameters such that a balance is reached between the transport-limited rates of the etch and passivation steps.
These parameters are found with experimentation and may vary depending on the mask layout. The penalty for minimizing lag is a reduction in the etch rate to about
1 µm/min.
Слайд 13*
Figure 3.13 ARDE in DRIE. The etch rate decreases with increasing trench
*
Figure 3.13 ARDE in DRIE. The etch rate decreases with increasing trench
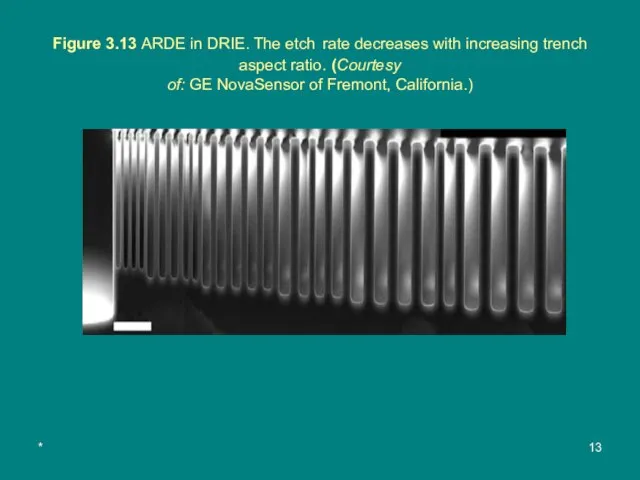
Слайд 15*
The high selectivity to silicon dioxide makes it possible to etch deep
*
The high selectivity to silicon dioxide makes it possible to etch deep
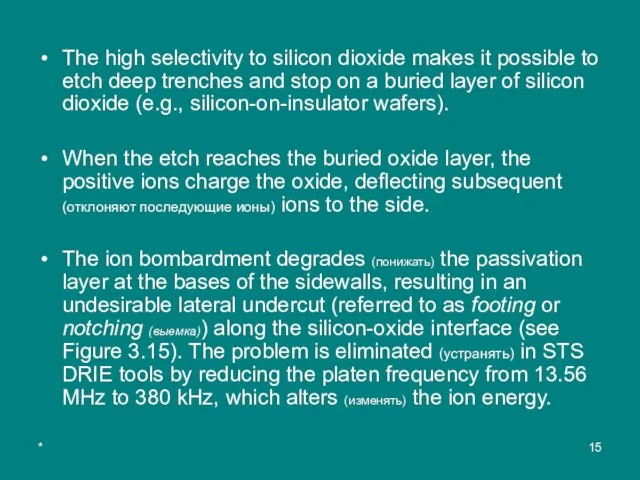
When the etch reaches the buried oxide layer, the positive ions charge the oxide, deflecting subsequent (отклоняют последующие ионы) ions to the side.
The ion bombardment degrades (понижать) the passivation layer at the bases of the sidewalls, resulting in an undesirable lateral undercut (referred to as footing or notching (выемка)) along the silicon-oxide interface (see Figure 3.15). The problem is eliminated (устранять) in STS DRIE tools by reducing the platen frequency from 13.56 MHz to 380 kHz, which alters (изменять) the ion energy.
Слайд 17*
Advanced Process Tools
Anodic Bonding
Anodic bonding, also known as field-assisted bonding or Mallory
*
Advanced Process Tools
Anodic Bonding
Anodic bonding, also known as field-assisted bonding or Mallory

It is used in the manufacturing of a variety of sensors, including pressure sensors, because it provides a rigid support to the silicon that mechanically isolates it from packaging stress.
The bonding is performed at a temperature between 200° and 500°C in vacuum, air, or in an inert gas environment.
The application of 500 to 1,500V across the two substrates, with the glass held at the negative potential, causes mobile positive ions (mostly Na+) in the glass to migrate away from the silicon-glass interface toward the cathode, leaving behind fixed negative charges in the glass (see Figure 3.16)
Слайд 19*
The bonding is complete when the ion current (measured externally as an
*
The bonding is complete when the ion current (measured externally as an
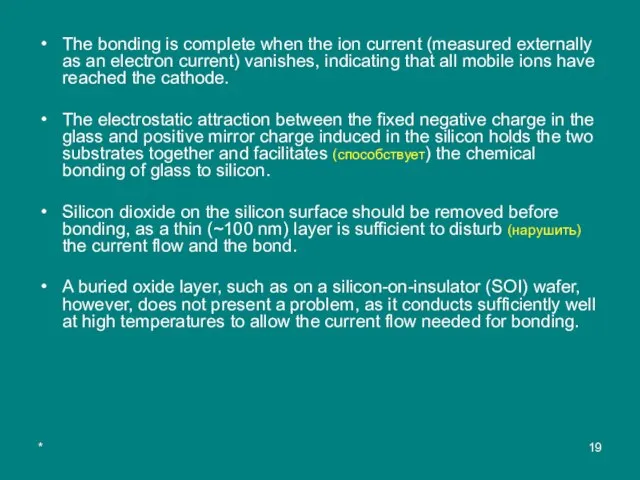
The electrostatic attraction between the fixed negative charge in the glass and positive mirror charge induced in the silicon holds the two substrates together and facilitates (способствует) the chemical bonding of glass to silicon.
Silicon dioxide on the silicon surface should be removed before bonding, as a thin (~100 nm) layer is sufficient to disturb (нарушить) the current flow and the bond.
A buried oxide layer, such as on a silicon-on-insulator (SOI) wafer, however, does not present a problem, as it conducts sufficiently well at high temperatures to allow the current flow needed for bonding.
Слайд 20*
The coefficient of thermal expansion of the glass substrate is preferably matched
*
The coefficient of thermal expansion of the glass substrate is preferably matched
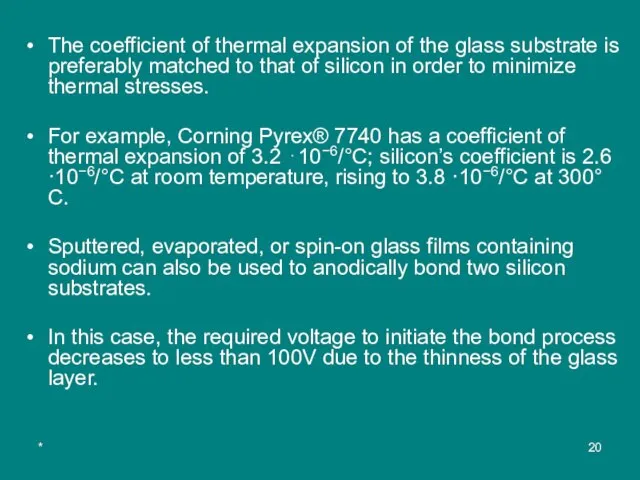
For example, Corning Pyrex® 7740 has a coefficient of thermal expansion of 3.2 ⋅10−6/°C; silicon’s coefficient is 2.6 ·10−6/°C at room temperature, rising to 3.8 ·10−6/°C at 300°C.
Sputtered, evaporated, or spin-on glass films containing sodium can also be used to anodically bond two silicon substrates.
In this case, the required voltage to initiate the bond process decreases to less than 100V due to the thinness of the glass layer.
Слайд 21*
Silicon Direct Bonding
Silicon direct bonding, also known as silicon fusion bonding, is
*
Silicon Direct Bonding
Silicon direct bonding, also known as silicon fusion bonding, is
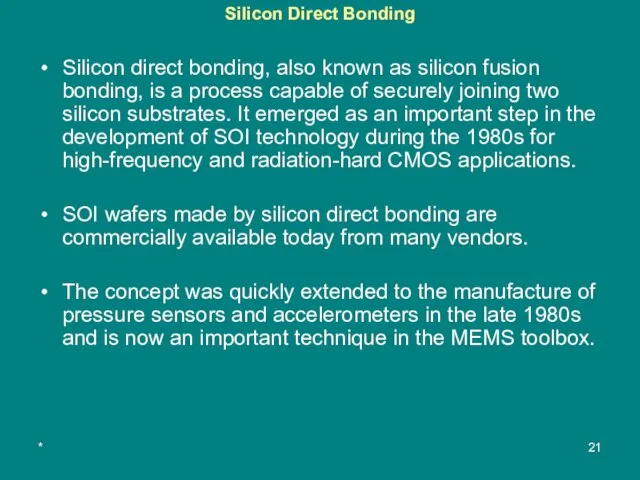
SOI wafers made by silicon direct bonding are commercially available today from many vendors.
The concept was quickly extended to the manufacture of pressure sensors and accelerometers in the late 1980s and is now an important technique in the MEMS toolbox.
Слайд 22*
Silicon direct bonding can be performed between two bare single-crystal silicon surfaces
*
Silicon direct bonding can be performed between two bare single-crystal silicon surfaces
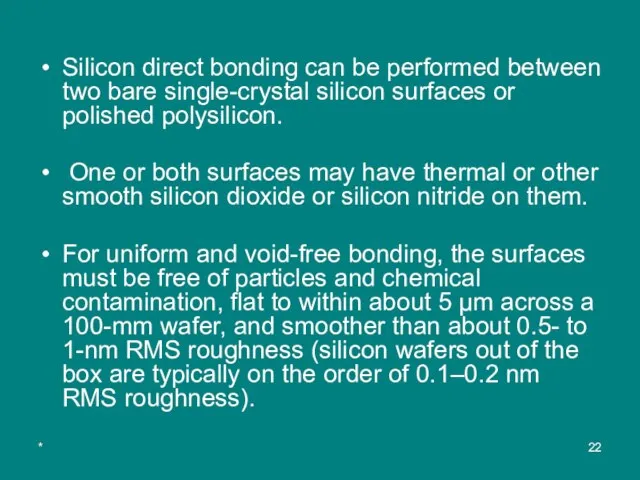
One or both surfaces may have thermal or other smooth silicon dioxide or silicon nitride on them.
For uniform and void-free bonding, the surfaces must be free of particles and chemical contamination, flat to within about 5 µm across a 100-mm wafer, and smoother than about 0.5- to 1-nm RMS roughness (silicon wafers out of the box are typically on the order of 0.1–0.2 nm RMS roughness).
Слайд 23*
The direct bonding process starts with cleaning and hydration of the surfaces.
The
*
The direct bonding process starts with cleaning and hydration of the surfaces.
The
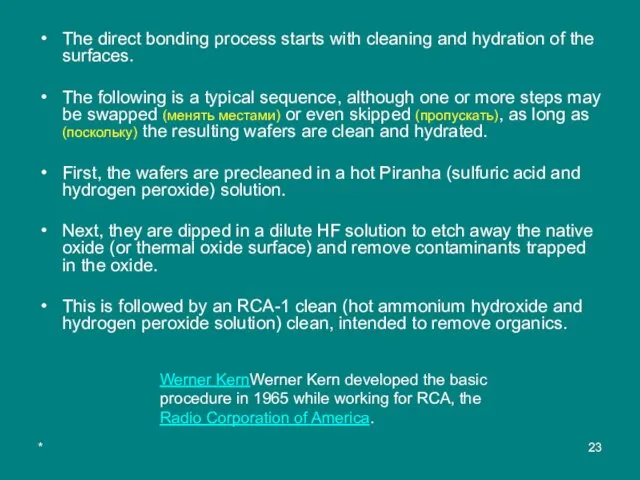
First, the wafers are precleaned in a hot Piranha (sulfuric acid and hydrogen peroxide) solution.
Next, they are dipped in a dilute HF solution to etch away the native oxide (or thermal oxide surface) and remove contaminants trapped in the oxide.
This is followed by an RCA-1 clean (hot ammonium hydroxide and hydrogen peroxide solution) clean, intended to remove organics.
Werner KernWerner Kern developed the basic procedure in 1965 while working for RCA, the Radio Corporation of America.
Слайд 24*
Finally, an RCA-2 clean (hot hydrochloric acid and hydrogen peroxide solution) is
*
Finally, an RCA-2 clean (hot hydrochloric acid and hydrogen peroxide solution) is
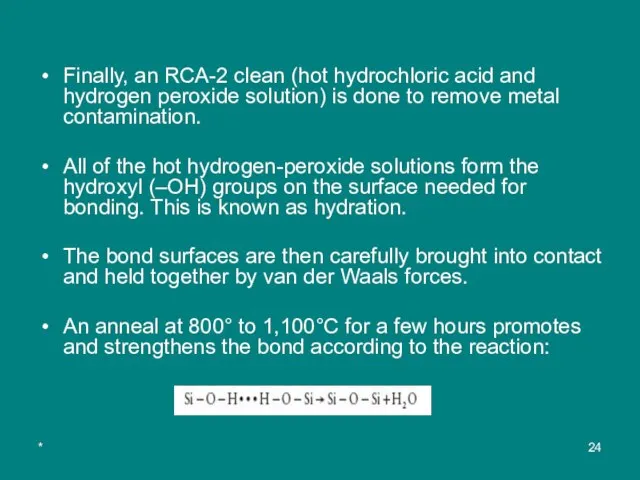
All of the hot hydrogen-peroxide solutions form the hydroxyl (–OH) groups on the surface needed for bonding. This is known as hydration.
The bond surfaces are then carefully brought into contact and held together by van der Waals forces.
An anneal at 800° to 1,100°C for a few hours promotes and strengthens the bond according to the reaction:
Слайд 25*
In some cases, features on the two bond surfaces must be aligned
*
In some cases, features on the two bond surfaces must be aligned
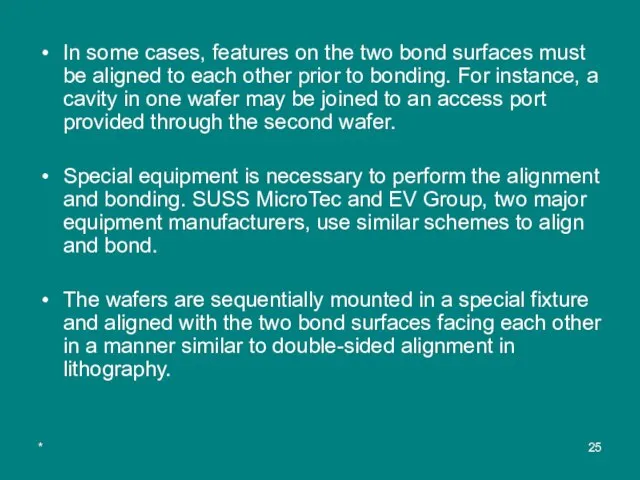
Special equipment is necessary to perform the alignment and bonding. SUSS MicroTec and EV Group, two major equipment manufacturers, use similar schemes to align and bond.
The wafers are sequentially mounted in a special fixture and aligned with the two bond surfaces facing each other in a manner similar to double-sided alignment in lithography.
Слайд 26*
A mechanical clamping fixture holds the aligned wafers in position, separated by
*
A mechanical clamping fixture holds the aligned wafers in position, separated by
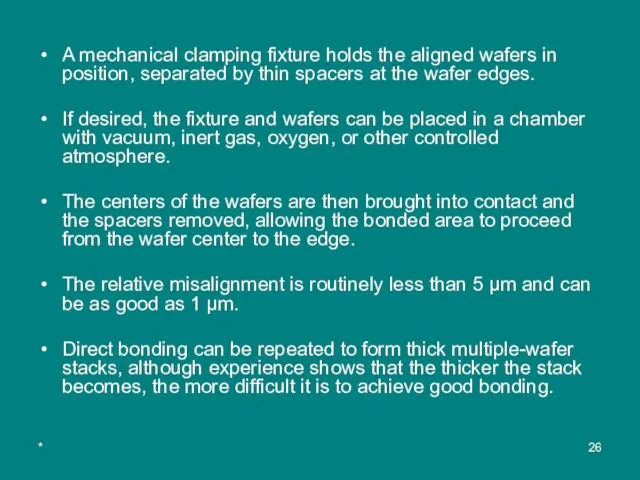
If desired, the fixture and wafers can be placed in a chamber with vacuum, inert gas, oxygen, or other controlled atmosphere.
The centers of the wafers are then brought into contact and the spacers removed, allowing the bonded area to proceed from the wafer center to the edge.
The relative misalignment is routinely less than 5 µm and can be as good as 1 µm.
Direct bonding can be repeated to form thick multiple-wafer stacks, although experience shows that the thicker the stack becomes, the more difficult it is to achieve good bonding.
Слайд 27*
Grinding (шлифовка), Polishing, and Chemical-Mechanical Polishing
Some applications use a thin layer of
*
Grinding (шлифовка), Polishing, and Chemical-Mechanical Polishing
Some applications use a thin layer of
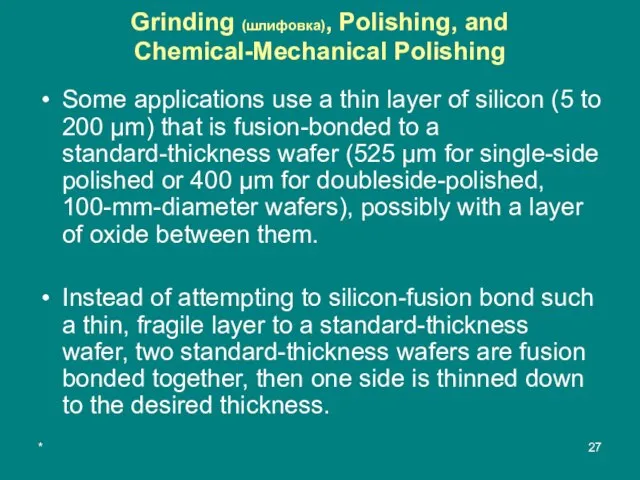
Instead of attempting to silicon-fusion bond such a thin, fragile layer to a standard-thickness wafer, two standard-thickness wafers are fusion bonded together, then one side is thinned down to the desired thickness.
Слайд 28*
The thickness reduction is achieved using grinding and polishing. The wafer stack
*
The thickness reduction is achieved using grinding and polishing. The wafer stack
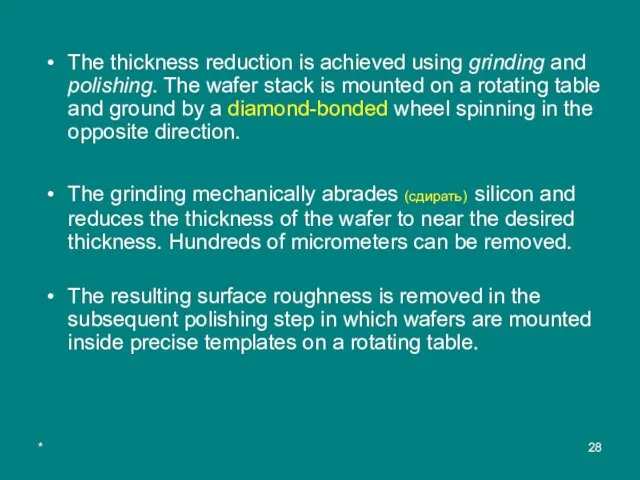
The grinding mechanically abrades (сдирать) silicon and reduces the thickness of the wafer to near the desired thickness. Hundreds of micrometers can be removed.
The resulting surface roughness is removed in the subsequent polishing step in which wafers are mounted inside precise templates on a rotating table.
Слайд 29*
A wheel with a felt-like (фетровый) texture polishes the wafer surface
*
A wheel with a felt-like (фетровый) texture polishes the wafer surface
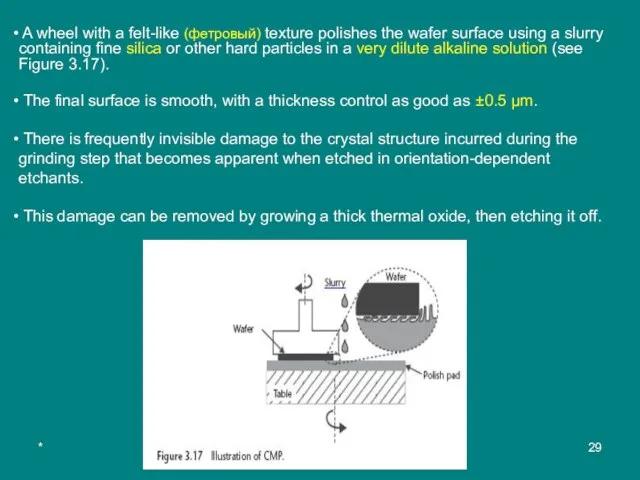
The final surface is smooth, with a thickness control as good as ±0.5 µm.
There is frequently invisible damage to the crystal structure incurred during the grinding step that becomes apparent when etched in orientation-dependent etchants.
This damage can be removed by growing a thick thermal oxide, then etching it off.
Слайд 30*
Chemical mechanical polishing, also known as chemical mechanical planarization (CMP), is commonly
*
Chemical mechanical polishing, also known as chemical mechanical planarization (CMP), is commonly
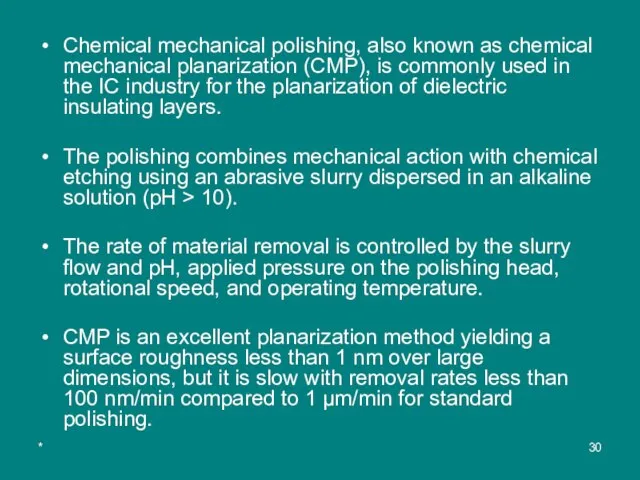
The polishing combines mechanical action with chemical etching using an abrasive slurry dispersed in an alkaline solution (pH > 10).
The rate of material removal is controlled by the slurry flow and pH, applied pressure on the polishing head, rotational speed, and operating temperature.
CMP is an excellent planarization method yielding a surface roughness less than 1 nm over large dimensions, but it is slow with removal rates less than 100 nm/min compared to 1 µm/min for standard polishing.
Слайд 31*
Водоро́дный показа́тель
Водоро́дный показа́тель, pH (произносится «пэ аш», английское произношение англ. pH — pi:eɪtʃ — pi:eɪtʃ, «пи эйч») — мера активности — pi:eɪtʃ, «пи эйч») — мера активности (в очень разбавленных
*
Водоро́дный показа́тель
Водоро́дный показа́тель, pH (произносится «пэ аш», английское произношение англ. pH — pi:eɪtʃ — pi:eɪtʃ, «пи эйч») — мера активности — pi:eɪtʃ, «пи эйч») — мера активности (в очень разбавленных
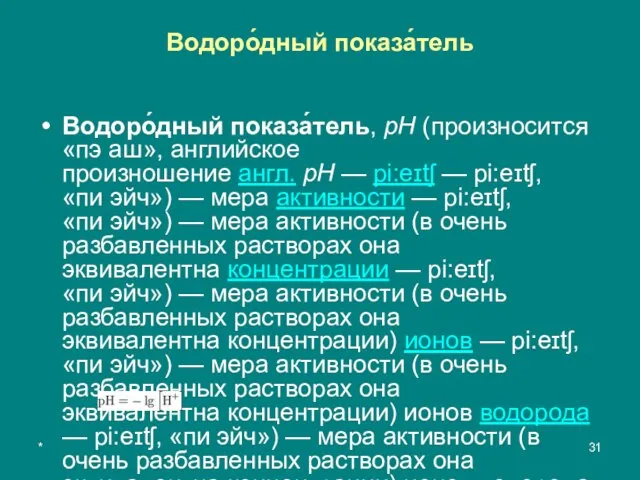
Слайд 32*
Вывод значения pH
В чистой водеВ чистой воде при 25 °C концентрации ионов водорода ([H+]) и гидроксид-ионов ([OH−]) одинаковы и составляют
*
Вывод значения pH
В чистой водеВ чистой воде при 25 °C концентрации ионов водорода ([H+]) и гидроксид-ионов ([OH−]) одинаковы и составляют
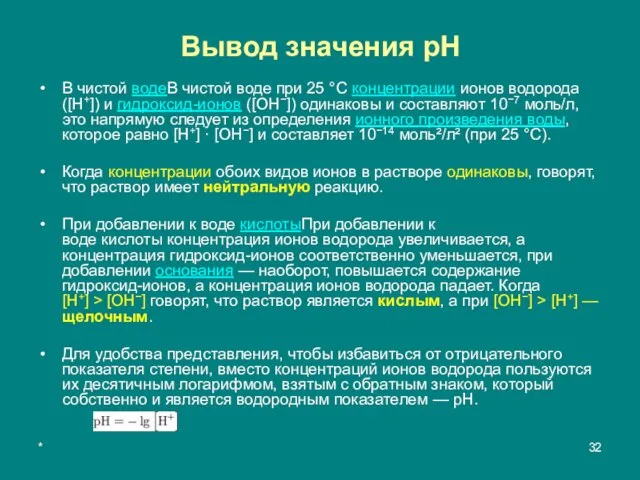
Когда концентрации обоих видов ионов в растворе одинаковы, говорят, что раствор имеет нейтральную реакцию.
При добавлении к воде кислотыПри добавлении к воде кислоты концентрация ионов водорода увеличивается, а концентрация гидроксид-ионов соответственно уменьшается, при добавлении основания — наоборот, повышается содержание гидроксид-ионов, а концентрация ионов водорода падает. Когда [H+] > [OH−] говорят, что раствор является кислым, а при [OH−] > [H+] —щелочным.
Для удобства представления, чтобы избавиться от отрицательного показателя степени, вместо концентраций ионов водорода пользуются их десятичным логарифмом, взятым с обратным знаком, который собственно и является водородным показателем — pH.
Слайд 33*
Так как в кислых растворах [H+] > 10−7, то у кислых растворов
*
Так как в кислых растворах [H+] > 10−7, то у кислых растворов
![* Так как в кислых растворах [H+] > 10−7, то у кислых](/_ipx/f_webp&q_80&fit_contain&s_1440x1080/imagesDir/jpg/378459/slide-32.jpg)
pH нейтральных растворов равен 7.
При более высоких температурах константа электролитической диссоциации воды повышается, соответственно увеличивается ионное произведение воды, поэтому нейтральной оказывается pH < 7 (что соответствует одновременно возросшим концентрациям как H+, так и OH−); при понижении температуры, напротив, нейтральная pH возрастает.
Слайд 34*
Некоторые значения pH
ЭлектролитЭлектролит в свинцовых аккумуляторах<1.0
Желудочный сок 1,0—2,0
ЛимонныйЛимонный сок (5% р-р лимонной кислоты)2,0±0,3
Пищевой уксус 2,4
Кока-кола 3,0±0,3
Яблочный сок 3,0
Пиво
*
Некоторые значения pH
ЭлектролитЭлектролит в свинцовых аккумуляторах<1.0
Желудочный сок 1,0—2,0
ЛимонныйЛимонный сок (5% р-р лимонной кислоты)2,0±0,3
Пищевой уксус 2,4
Кока-кола 3,0±0,3
Яблочный сок 3,0
Пиво
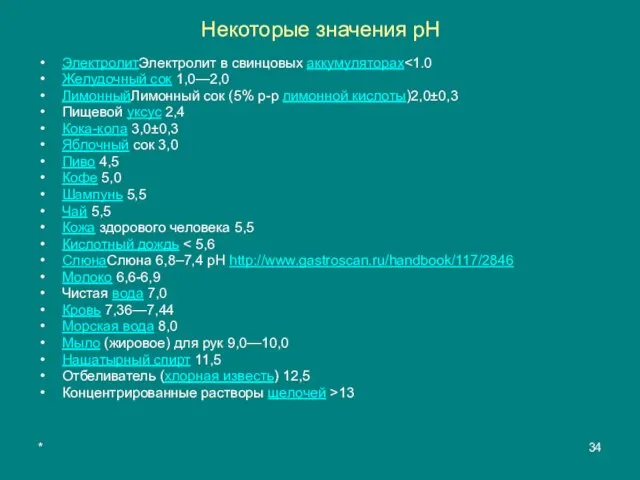
Кофе 5,0
Шампунь 5,5
Чай 5,5
Кожа здорового человека 5,5
Кислотный дождь < 5,6
СлюнаСлюна 6,8–7,4 pH http://www.gastroscan.ru/handbook/117/2846
Молоко 6,6-6,9
Чистая вода 7,0
Кровь 7,36—7,44
Морская вода 8,0
Мыло (жировое) для рук 9,0—10,0
Нашатырный спирт 11,5
Отбеливатель (хлорная известь) 12,5
Концентрированные растворы щелочей >13
Слайд 35*
Sol-Gel Deposition Methods
A sol-gel process is a chemical reaction between solid particles
*
Sol-Gel Deposition Methods
A sol-gel process is a chemical reaction between solid particles
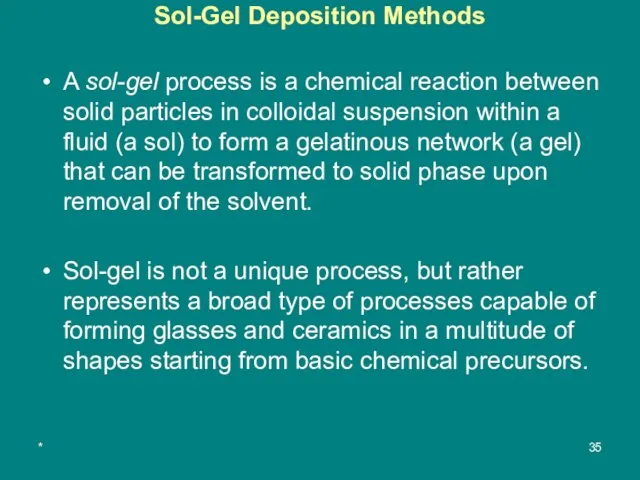
Sol-gel is not a unique process, but rather represents a broad type of processes capable of forming glasses and ceramics in a multitude of shapes starting from basic chemical precursors.
Слайд 36*
A widespread application of sol-gel processing is in the coating of surfaces
*
A widespread application of sol-gel processing is in the coating of surfaces
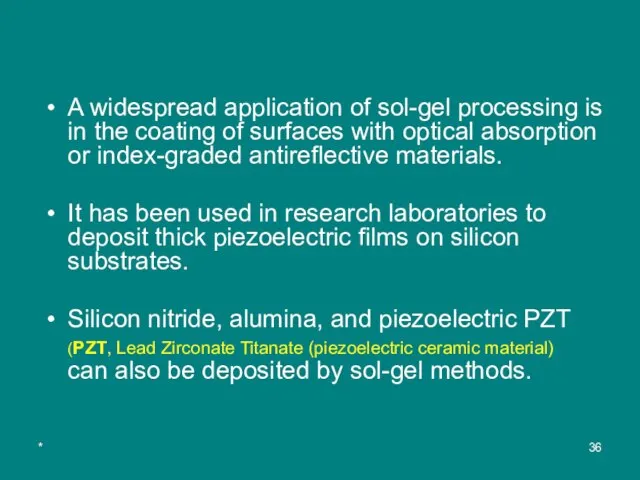
It has been used in research laboratories to deposit thick piezoelectric films on silicon substrates.
Silicon nitride, alumina, and piezoelectric PZT (PZT, Lead Zirconate Titanate (piezoelectric ceramic material) can also be deposited by sol-gel methods.
Слайд 37*
Electroceramic properties
Being piezoelectricBeing piezoelectric, it develops a voltage (or potential difference) across two of its faces
*
Electroceramic properties
Being piezoelectricBeing piezoelectric, it develops a voltage (or potential difference) across two of its faces
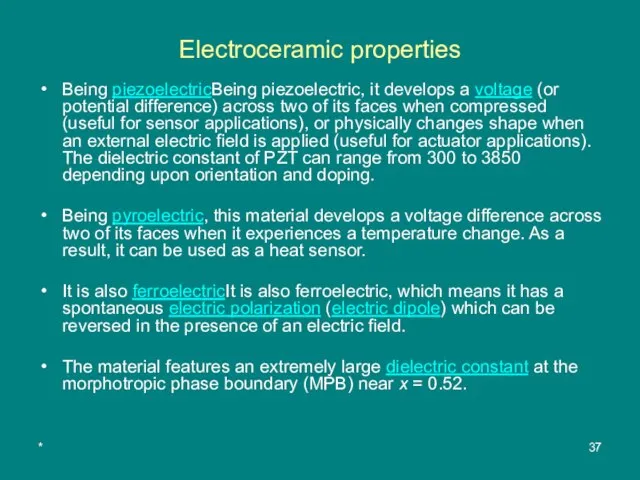
Being pyroelectric, this material develops a voltage difference across two of its faces when it experiences a temperature change. As a result, it can be used as a heat sensor.
It is also ferroelectricIt is also ferroelectric, which means it has a spontaneous electric polarization (electric dipole) which can be reversed in the presence of an electric field.
The material features an extremely large dielectric constant at the morphotropic phase boundary (MPB) near x = 0.52.
Слайд 38*
Varieties of PZTs
Сommonly studied chemical composition is PbСommonly studied chemical composition is PbZr0.52Ti0.48O3. The
*
Varieties of PZTs
Сommonly studied chemical composition is PbСommonly studied chemical composition is PbZr0.52Ti0.48O3. The
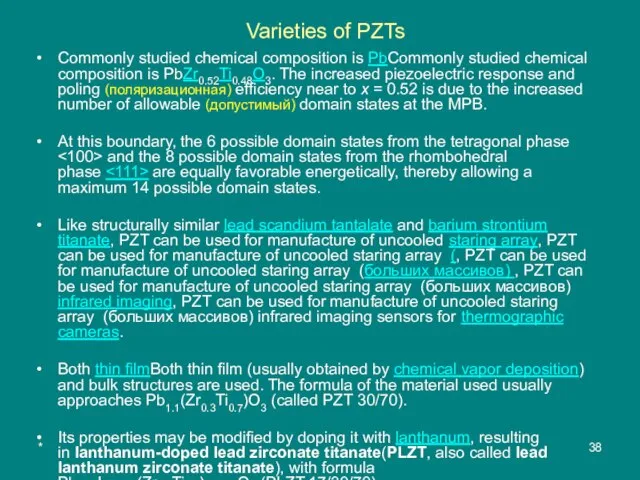
At this boundary, the 6 possible domain states from the tetragonal phase <100> and the 8 possible domain states from the rhombohedral phase <111> are equally favorable energetically, thereby allowing a maximum 14 possible domain states.
Like structurally similar lead scandium tantalate and barium strontium titanate, PZT can be used for manufacture of uncooled staring array, PZT can be used for manufacture of uncooled staring array (, PZT can be used for manufacture of uncooled staring array (больших массивов) , PZT can be used for manufacture of uncooled staring array (больших массивов) infrared imaging, PZT can be used for manufacture of uncooled staring array (больших массивов) infrared imaging sensors for thermographic cameras.
Both thin filmBoth thin film (usually obtained by chemical vapor deposition) and bulk structures are used. The formula of the material used usually approaches Pb1.1(Zr0.3Ti0.7)O3 (called PZT 30/70).
Its properties may be modified by doping it with lanthanum, resulting in lanthanum-doped lead zirconate titanate(PLZT, also called lead lanthanum zirconate titanate), with formula Pb0.83La0.17(Zr0.3Ti0.7)0.9575O3 (PLZT 17/30/70).
Слайд 39*
A sol-gel process starts by dissolving appropriate chemical precursors in a
*
A sol-gel process starts by dissolving appropriate chemical precursors in a
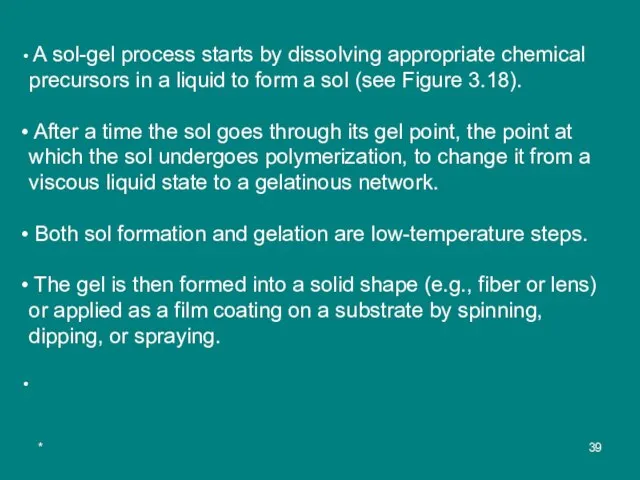
After a time the sol goes through its gel point, the point at which the sol undergoes polymerization, to change it from a viscous liquid state to a gelatinous network.
Both sol formation and gelation are low-temperature steps.
The gel is then formed into a solid shape (e.g., fiber or lens) or applied as a film coating on a substrate by spinning, dipping, or spraying.
Слайд 40*
For example, TEOS in water can be converted into a silica gel
*
For example, TEOS in water can be converted into a silica gel
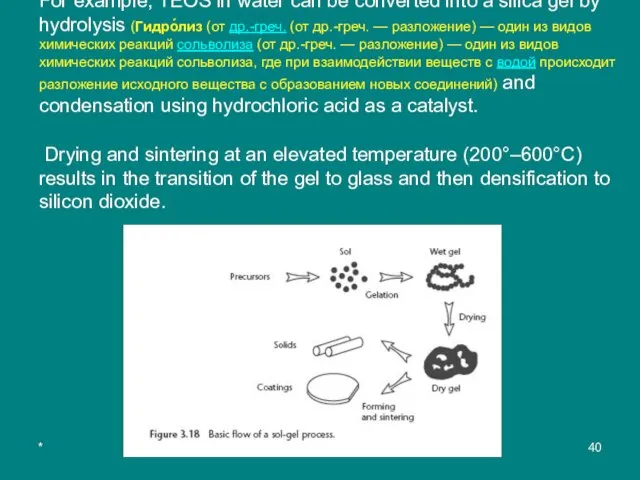
Слайд 41*
Silica gel is a granular is a granular, vitreous (стекловидный), porous, porous form of silicon dioxide, porous form of silicon dioxide made synthetically from sodium silicate.
Silica
*
Silica gel is a granular is a granular, vitreous (стекловидный), porous, porous form of silicon dioxide, porous form of silicon dioxide made synthetically from sodium silicate.
Silica
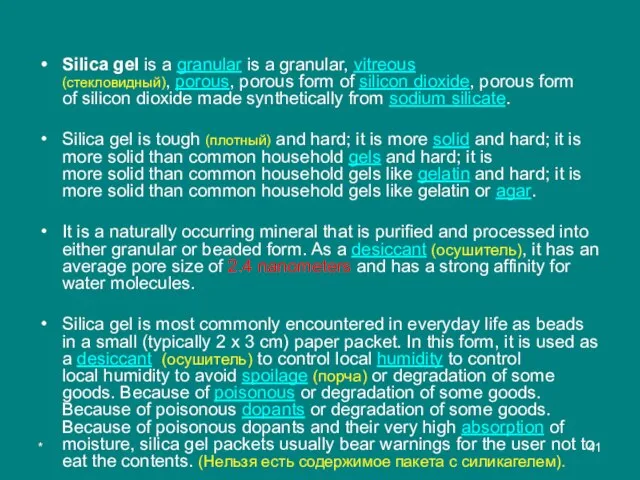
It is a naturally occurring mineral that is purified and processed into either granular or beaded form. As a desiccant (осушитель), it has an average pore size of 2.4 nanometers and has a strong affinity for water molecules.
Silica gel is most commonly encountered in everyday life as beads in a small (typically 2 x 3 cm) paper packet. In this form, it is used as a desiccant (осушитель) to control local humidity to control local humidity to avoid spoilage (порча) or degradation of some goods. Because of poisonous or degradation of some goods. Because of poisonous dopants or degradation of some goods. Because of poisonous dopants and their very high absorption of moisture, silica gel packets usually bear warnings for the user not to eat the contents. (Нельзя есть содержимое пакета с силикагелем).
Слайд 42*
Sodium silicate is the common name for a compound sodium metasilicate, Na2SiO3, also
*
Sodium silicate is the common name for a compound sodium metasilicate, Na2SiO3, also
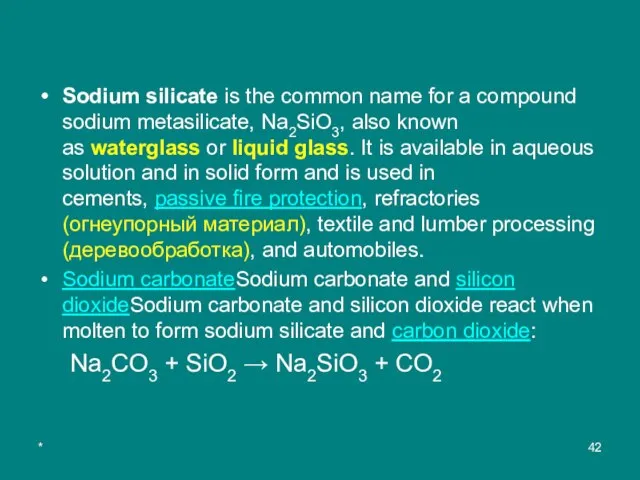
Sodium carbonateSodium carbonate and silicon dioxideSodium carbonate and silicon dioxide react when molten to form sodium silicate and carbon dioxide:
Na2CO3 + SiO2 → Na2SiO3 + CO2