Слайд 2 Введение
Бесперебойная работа правильной машины и получение высокосортной продукции в значительной
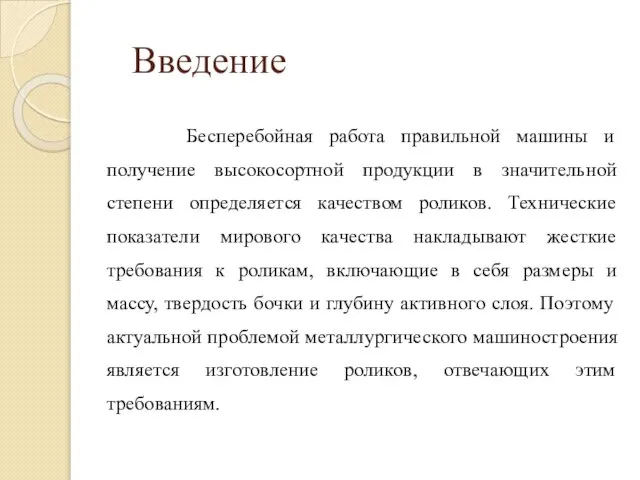
степени определяется качеством роликов. Технические показатели мирового качества накладывают жесткие требования к роликам, включающие в себя размеры и массу, твердость бочки и глубину активного слоя. Поэтому актуальной проблемой металлургического машиностроения является изготовление роликов, отвечающих этим требованиям.
Слайд 3Способы обработки поверхности рабочих роликов
методом закалки погружением
газопламенная закалка
закалка ТВЧ
термодиффузионного легирования поверхностей
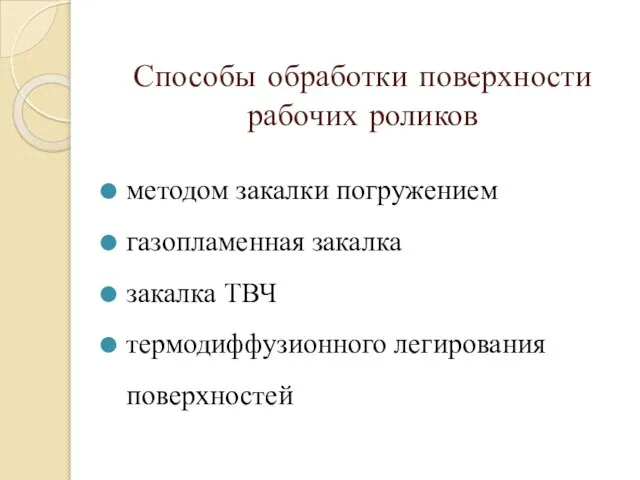
Слайд 4Способ термодиффузионного легирования поверхностей
Наиболее близким техническим решением, принятым за прототип, является
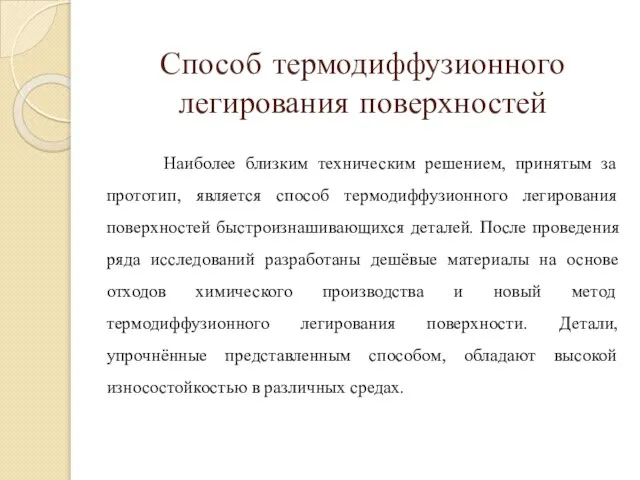
способ термодиффузионного легирования поверхностей быстроизнашивающихся деталей. После проведения ряда исследований разработаны дешёвые материалы на основе отходов химического производства и новый метод термодиффузионного легирования поверхности. Детали, упрочнённые представленным способом, обладают высокой износостойкостью в различных средах.
Слайд 5Цель курсового проекта
Целью заявленного технического решения является повышение эксплуатационной стойкости роликов
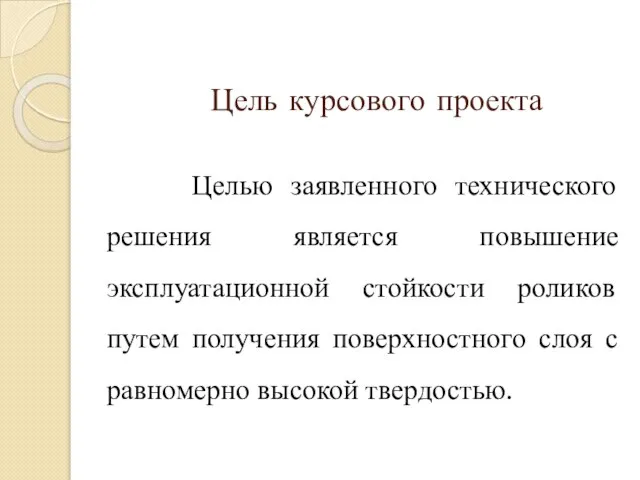
путем получения поверхностного слоя с равномерно высокой твердостью.
Слайд 6
Сущность
Данная цель достигается путем:
подвержение облучению с плотностью мощности в пределах (1,7-6)∙106 кВт/м2
выбора
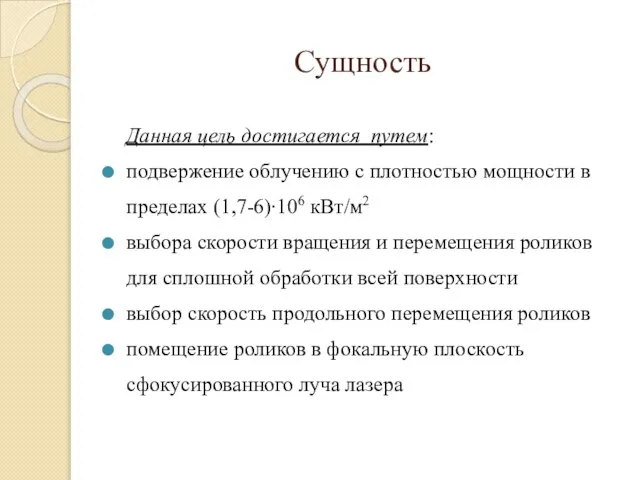
скорости вращения и перемещения роликов для сплошной обработки всей поверхности
выбор скорость продольного перемещения роликов
помещение роликов в фокальную плоскость сфокусированного луча лазера
Слайд 7Формула изобретения
Способ поверхностной закалки роликов преимущественно из хромистой стали, включающий обработку
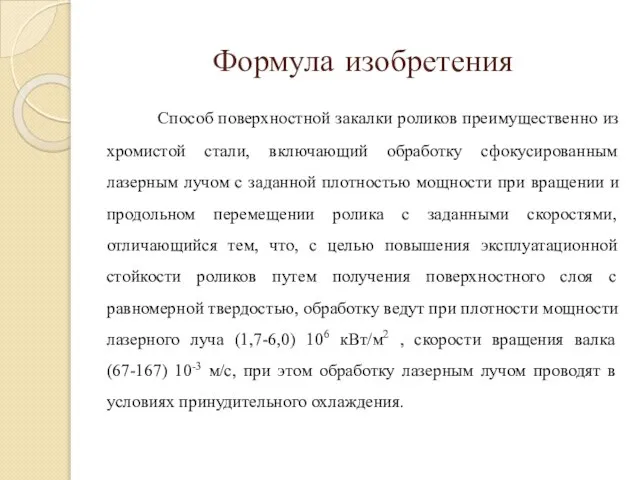
сфокусированным лазерным лучом с заданной плотностью мощности при вращении и продольном перемещении ролика с заданными скоростями, отличающийся тем, что, с целью повышения эксплуатационной стойкости роликов путем получения поверхностного слоя с равномерной твердостью, обработку ведут при плотности мощности лазерного луча (1,7-6,0) 106 кВт/м2 , скорости вращения валка (67-167) 10-3 м/с, при этом обработку лазерным лучом проводят в условиях принудительного охлаждения.