Слайд 2Неразрушающий контроль
Задача неразрушающего контроля различных металлических конструкции в настоящее время актуальна, потому
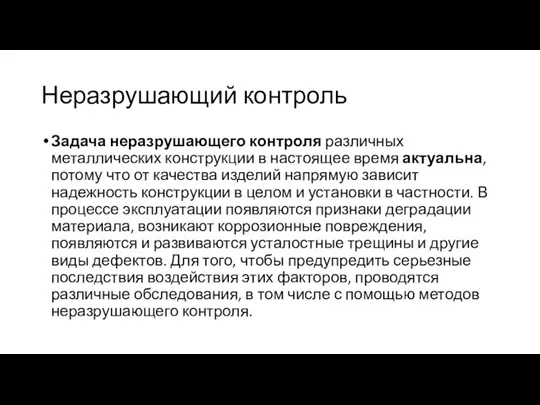
что от качества изделий напрямую зависит надежность конструкции в целом и установки в частности. В процессе эксплуатации появляются признаки деградации материала, возникают коррозионные повреждения, появляются и развиваются усталостные трещины и другие виды дефектов. Для того, чтобы предупредить серьезные последствия воздействия этих факторов, проводятся различные обследования, в том числе с помощью методов неразрушающего контроля.
Слайд 3Актуальность
Повреждения и разрушение компонентов различных металлоконструкций могут приводить к серьезным экономическим потерям
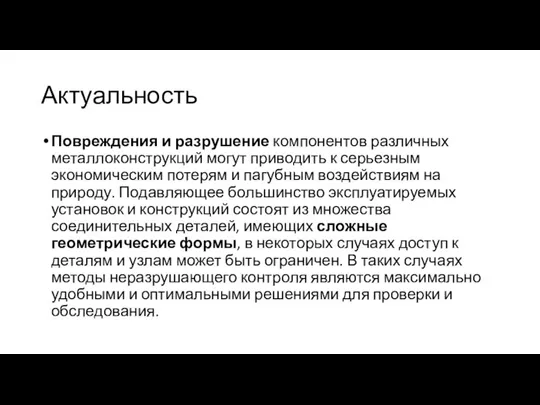
и пагубным воздействиям на природу. Подавляющее большинство эксплуатируемых установок и конструкций состоят из множества соединительных деталей, имеющих сложные геометрические формы, в некоторых случаях доступ к деталям и узлам может быть ограничен. В таких случаях методы неразрушающего контроля являются максимально удобными и оптимальными решениями для проверки и обследования.
Слайд 4Цель и задачи
Целью разработки устройства является выявление в металлической детали неоднородности магнитного
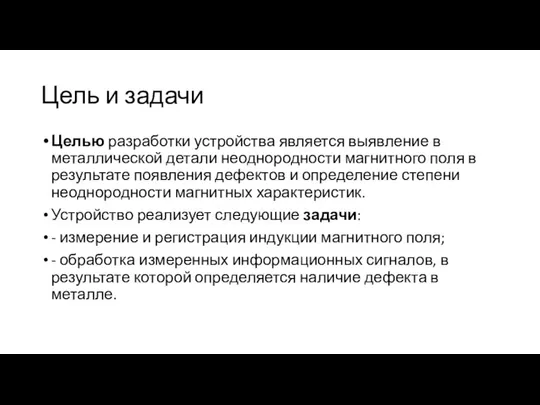
поля в результате появления дефектов и определение степени неоднородности магнитных характеристик.
Устройство реализует следующие задачи:
- измерение и регистрация индукции магнитного поля;
- обработка измеренных информационных сигналов, в результате которой определяется наличие дефекта в металле.
Слайд 5Устройство измерения магнитных характеристик ферромагнитных материалов предназначено для измерения и регистрации индукции
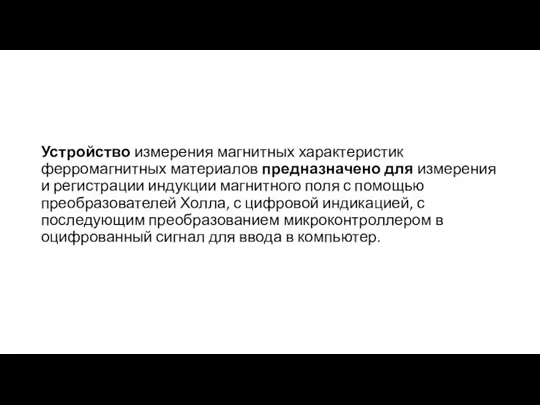
магнитного поля с помощью преобразователей Холла, с цифровой индикацией, с последующим преобразованием микроконтроллером в оцифрованный сигнал для ввода в компьютер.
Слайд 7Выводы
1. Работа, проведенная в рамках дипломного исследования, подтвердила актуальность темы. На сегодняшний
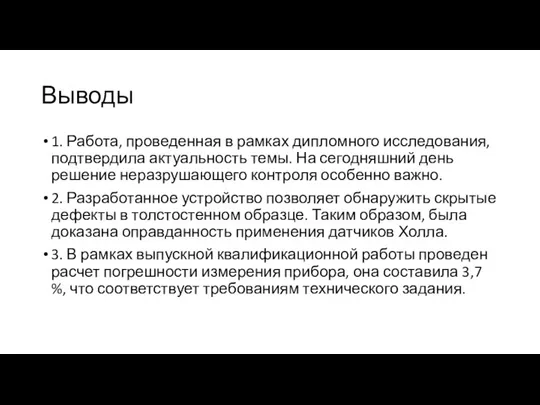
день решение неразрушающего контроля особенно важно.
2. Разработанное устройство позволяет обнаружить скрытые дефекты в толстостенном образце. Таким образом, была доказана оправданность применения датчиков Холла.
3. В рамках выпускной квалификационной работы проведен расчет погрешности измерения прибора, она составила 3,7 %, что соответствует требованиям технического задания.