Содержание
- 2. -Качество уплотнения щебеночных, гравийных и шлаковых оснований и покрытий следует проверять контрольным проходом катка массой 10-13
- 3. Основные параметры и размеры Щебень и гравий выпускают в виде следующих основных фракций: от 5 (3)
- 4. Лабораторные испытания - щебень и гравий из плотных горных пород для строительных работ Проба - определенное
- 5. Таблица 3 Масса лабораторной пробы при приемочном контроле -Указанную пробу используют для всех испытаний, предусмотренных при
- 6. акт отбора проб, включающий наименование и обозначение материала, место и дату отбора пробы, наименование и обозначение
- 8. -Определяют полные остатки на каждом сите в процентах массы пробы, равные сумме частных остатков на данном
- 9. Метод отмучивания -Содержание пылевидных и глинистых частиц в щебне (гравии) определяют по изменению массы пробы после
- 10. -Воду в сосуд для отмучивания щебня (гравия) наливают до верхнего сливного отверстия. Суспензию сливают через два
- 11. Определение содержания зерен пластинчатой (лещадной) и игловатой форм Метод визуальной разборки -Содержание в щебне (гравии) зерен
- 12. Определение дробимости Дробимость щебня (гравия) определяют по степени разрушения зерен при сжатии (раздавливании) в цилиндре. Порядок
- 13. -После сжатия испытываемую пробу высыпают из цилиндра и взвешивают. Затем ее просеивают в зависимости от размера
- 14. Порядок проведения испытания -Аналитическую пробу щебня (гравия) данной фракции равномерно насыпают в металлический сосуд и заливают
- 15. Контроль качества работ при устройстве асфальтобетонных слоев При приготовлении асфальтобетонной смеси следует контролировать: постоянно - температуру
- 16. Качество асфальтобетона по показателям кернов (вырубок) в трех местах на 3000 м/кв покрытия по ГОСТ 9128,
- 17. -Толщина устраиваемого слоя асфальтобетона над прослойкой из геосинтетических материалов должна быть не менее 5 см. -Производить
- 25. Порядок проведения испытания Предел прочности при сжатии образцов определяют на прессах при скорости движения плиты пресса
- 27. -При использовании гидравлических прессов требуемую скорость перед проведением испытания следует установить при холостом ходе поршня. -Образец,
- 28. Определение предела прочности на растяжение при изгибе и показателей деформативности Порядок подготовки и проведения испытания -Для
- 29. Схема испытания образцов-призм на изгиб
- 31. -Порядок подготовки к проведению испытания -Для испытания асфальтобетона на сдвигоустойчивость готовят четное число образцов в количестве
- 35. Определение морозостойкости Сущность метода заключается в оценке потери прочности при сжатии предварительно водонасыщенных образцов после воздействия
- 37. -Метод экстрагирования вяжущего -Метод предусматривает определение содержания вяжущего путем экстрагирования его из смеси в специальных приборах-экстракторах
- 39. Определение зернового состава минеральной части смеси после экстрагирования Проведение испытания и обработка результатов испытания -Пробу минеральной
- 40. -Перед окончанием просеивания для проверки каждое сито вручную интенсивно встряхивают в течение 1 мин над листом
- 43. -Порядок проведения испытания -Химический стакан заполняют на 2/3 объема дистиллированной водой, устанавливают на электроплитку, песчаную баню
- 44. Битумы нефтяные дорожные
- 45. -Вязкие нефтяные дорожные битумы изготовляют окислением продуктов прямой перегонки нефти и селективного разделения нефтепродуктов (асфальтов деасфальтизации,
- 46. - Обезвоженный и расплавленный до подвижного состояния битум процеживают через металлическое сито и наливают в две
- 47. -Затем чашки с битумом помещают в баню для термостатирования при заданной температуре испытания. -Время выдерживания чашек
- 48. -По истечении заданного времени выдерживания чашку с образцом битума вынимают из бани для термостатирования и помещают
- 49. -Доводят кремальеру до верхней площадки плунжера, несущего иглу, и устанавливают стрелку на нуль или отмечают ее
- 50. Метод определения температуры размягчения по кольцу и шару -Битум наливают с некоторым избытком в два гладких
- 51. -После охлаждения колец с битумом на воздухе в течение 30 мин при (25±10) °С избыток битума
- 52. -По истечении 15 мин штатив вынимают из бани, на каждое кольцо в центре поверхности битума кладут
- 53. Метод определения растяжимости -Перед испытанием битум при наличии влаги обезвоживают осторожным нагреванием без перегрева до температуры
- 54. -Полированную металлическую или стеклянную пластинку и внутренние боковые стенки вкладышей "восьмерки" покрывают смесью талька с глицерином
- 55. -По истечении 1 ч формы с битумом вынимают из воды, снимают с пластинки и закрепляют в
- 56. Метод определения температуры вспышки и воспламенения в открытом тигле -Перед каждым испытанием тигель промывают растворителем. Углеродистые
- 57. Проведение испытания -Тигель заполняют нефтепродуктом так, чтобы верхний мениск точно совпадал с меткой. При наполнении тигля
- 58. -Начиная с температуры не менее чем на 28 °С ниже температуры вспышки, каждый раз применяют зажигательное
- 59. Метод определения изменения массы после прогрева -Перед испытанием пробу битума при необходимости обезвоживают нагреванием до температуры
- 60. -После охлаждения битума до комнатной температуры в эксикаторе пробы взвешивают с погрешностью не более 0,01 г.
- 61. По физико-химическим показателям битумы должны соответствовать требованиям и нормам
- 62. СХЕМА ЛАБОРАТОРНОГО КОНТРОЛЯ КАЧЕСТВА БИТУМЫ НЕФТЯНЫЕ, ПБВ
- 64. Приготовление бетонной смеси -должно обеспечивать требуемый объем вовлеченного воздуха с учетом продолжительности ее транспортирования от бетонного
- 65. -Организация работ по устройству двухслойного покрытия должна обеспечивать ритмичную укладку смеси и получение монолитного бетона по
- 66. -При максимальной суточной температуре воздуха 25°С и выше темные пленкообразующие материалы после формирования пленки следует осветлять
- 67. Контроль качества работ -При приготовлении цементобетонной смеси следует контролировать: постоянно - соблюдение технологических режимов приготовления бетонной
- 68. удобоукладываемость и объем вовлеченного воздуха, а также качество работ по уходу за свежеуложенным бетоном с применением
- 69. Бетон - искусственный каменный материал, получаемый из рационально подобранной смеси вяжущего вещества (с водой, реже без
- 70. Классификация бетонов Бетоны классифицируются по следующим признакам: - основное назначение; - стойкость к видам коррозии; -
- 71. В зависимости от основного назначения бетоны подразделяют на: - конструкционные; - специальные (например, теплоизоляционные, радиационностойкие, декоративные).
- 72. По виду вяжущего бетоны подразделяют на: - цементные; - известковые; - шлаковые; - гипсовые; - специальные
- 73. По условиям твердения бетоны подразделяют на твердеющие: - в естественных условиях; - в условиях тепловой обработки
- 74. По средней плотности бетоны подразделяют на: - особо легкие (марки по средней плотности менее D800); -
- 75. По водонепроницаемости бетоны подразделяют на бетоны: - низкой водонепроницаемости (марки по водонепроницаемости менее W4); - средней
- 76. СМЕСИ БЕТОННЫЕ Классификация По типу бетона бетонные смеси подразделяют на: - бетонные смеси тяжелого бетона (БСТ);
- 77. Бетонные смеси характеризуют следующими технологическими показателями качества: — удобоукладываемость; — средняя плотность; — расслаиваемость; — пористость;
- 78. Допустимые отклонения заданных значений удобоукладываемости
- 79. При поставке бетонной смеси допустимое отклонение заданных значений показателей: средней плотности, расслаиваемости, пористости, температуры, и сохраняемости
- 80. Бетонные смеси должны быть приняты по качеству и количеству техническим контролем производителя. Бетонные смеси принимают партиями.
- 81. Заданные технологические показатели качества бетонной смеси производят у производителя через 15 мин после выгрузки бетонной смеси
- 82. МЕТОДЫ КОНТРОЛЯ Пробы бетонной смеси для испытания при производственном контроле следует отбирать: - при производстве сборных
- 83. Бетонные смеси, содержащие воздухововлекающие, газообразующие и пенообразующие добавки, а также предварительно разогретые смеси, перед испытанием не
- 84. Определение удобоукладываемости бетонной смеси Удобоукладываемость бетонной смеси оценивают показателями подвижности или жесткости. Определение подвижности бетонной смеси
- 85. Конус для определения подвижности бетона
- 86. Для определения подвижности бетонной смеси с зернами заполнителя наибольшей крупностью до 40 мм включительно применяют нормальный
- 87. Каждый слой на его высоту уплотняют штыкованием металлическим стержнем: в нормальном конусе - 25 раз, в
- 88. Осадку конуса бетонной смеси, определенную в увеличенном конусе, приводят к осадке нормального конуса умножением осадки увеличенного
- 89. Правила обработки результатов испытаний Осадку и расплыв конуса бетонной смеси определяют дважды. Общее время испытания с
- 90. Определение жесткости бетонной смеси Жесткость бетонной смеси характеризуют временем вибрации в секундах, необходимым для уплотнения бетонной
- 91. Установку типа Вебе Прибор Красного Конус Скрамтаева
- 92. Определение жесткости бетонной смеси на установке типа Вебе Установку собирают и закрепляют на виброплощадке. Далее производится
- 93. Возможно применение цилиндрических форм ФЦ диаметром, соответствующим размеру ребра формы куба. Установленную на виброплощадку форму заполняют
- 94. Затем конус осторожно снимают, и включают одновременно виброплощадку и секундомер. Вибрирование осуществляют до тех пор, пока
- 95. Определение средней плотности бетонной смеси Среднюю плотность бетонной смеси характеризуют отношением массы уплотненной бетонной смеси к
- 96. После уплотнения избыток смеси срезают стальной линейкой, и поверхность тщательно выравнивают вровень с краями мерного сосуда.
- 97. Определение пористости бетонной смеси Пористость бетонной смеси оценивают следующими показателями: объемом воздуха или газа, содержащегося в
- 98. - кельму типа КБ по ГОСТ 9533; - посуду мерную стеклянную по ГОСТ 1770; - прямой
- 99. Объемный метод определения объема вовлеченного воздуха Навеску бетонной смеси помещают в сосуд объемомера и уплотняют В
- 100. После этого взвешиванием определяют суммарную массу всей налитой в сосуд воды с погрешностью до 1 г.
- 101. Пористость бетонной смеси V_в, %, вычисляют с округлением до 0,1% по формуле
- 102. Компрессионный метод определения объема вовлеченного воздуха Бетонную смесь укладывают в чашу поромера и уплотняют. После уплотнения
- 103. Закрывают входной и сливной вентили и насосом поднимают давление в приборе до (110+-5) кПа. Постукивают рукой
- 104. Показатели качества бетона Методы определения прочности по контрольным образцам Определение прочности бетона состоит в измерении минимальных
- 106. Наибольший номинальный размер зерен заполнителя
- 107. Отбор проб бетонной смеси и изготовление контрольных образцов Объем пробы бетонной смеси должен превышать требуемый для
- 108. При уплотнении бетонной смеси марок по удобоукладываемости Ж2, Ж3, Ж4, Ж5 с использованием виброплощадки на форме
- 109. Твердение, хранение и транспортирование образцов Образцы, предназначенные для твердения в нормальных условиях, после изготовления до их
- 110. - При транспортировании образцов необходимо предохранять их от повреждений, изменения влажности и замораживания. - Прочность бетона
- 111. -В случае разрушения образца по одной из неудовлетворительных схем, результат не учитывают, о чем делают запись
- 112. Испытание на растяжение при изгибе - Образец-призму устанавливают в испытательную машину и нагружают до разрушения при
- 113. 1 - образец; 2 - шар; 3 - опорная подушка; 4 - качающаяся призма; 5 -
- 114. ИСПЫТАНИЯ НА РАСТЯЖЕНИЕ ПРИ РАСКАЛЫВАНИИ Схемы испытания на растяжение при раскалывании
- 115. -Образец устанавливают на плиту испытательной машины -С помощью держателя или временных опор проверяют, чтобы образец был
- 116. Испытание на осевое растяжение -Образец закрепляют в разрывной машине по одной из схем, и нагружают до
- 117. ОПРЕДЕЛЕНИЯ МОРОЗОСТОЙКОСТИ
- 118. -Морозостойкость бетона определяют в проектном возрасте (после итоговых испытаний), установленном в нормативно-технической и проектной документации, при
- 119. -Образцы для испытания должны быть без внешних дефектов, средняя плотность которых не отличается от минимальной более
- 120. Соотношение между числом циклов испытаний и маркой бетона
- 121. - В промежуточный срок испытания контролируют состояние образцов: появление трещин, отколов, шелушение поверхности. При появлении указанных
- 122. -Образцы после замораживания оттаивают в ванне с водой при температуре (18±2) °С. -Температуру воздуха в морозильной
- 123. Схемы крепления и герметизации образцов бетона в обоймах 1 - образец бетона; 2 - испытательная обойма;
- 124. Проведение испытания -Образцы в обойме устанавливают в гнезда установки для испытания и надежно закрепляют. -Давление воды
- 125. Пределение истираемости бетона на установках типа "круг истирания" -Испытание бетона на круге истирания проводят на воздушно-сухих
- 126. -После установки образца (образцов) и нанесения на истирающий диск абразива включают привод круга и производят истирание.
- 127. СХЕМА ЛАБОРАТОРНОГО КОНТРОЛЯ КАЧЕСТВА БЕТОННЫЕ СМЕСИ И БЕТОН
- 129. Повторное использование материалов -С целью экономии средств, сегодня нередко прибегают к восстановлению асфальта, уже бывшего в
- 130. Холодный ресайклинг состоит в фрезеровании старого дорожного покрытия, последующем смешении асфальтовой крошки или каменного материала с
- 131. -Холодный ресайклинг как способ ремонта дорожной одежды имеет ряд очевидных преимуществ. Исключена необходимость вывоза удаляемого материала
- 132. Горячее ремиксирование асфальтобетона
- 134. Скачать презентацию
Слайд 2-Качество уплотнения щебеночных, гравийных и шлаковых оснований и покрытий следует проверять контрольным
-Качество уплотнения щебеночных, гравийных и шлаковых оснований и покрытий следует проверять контрольным
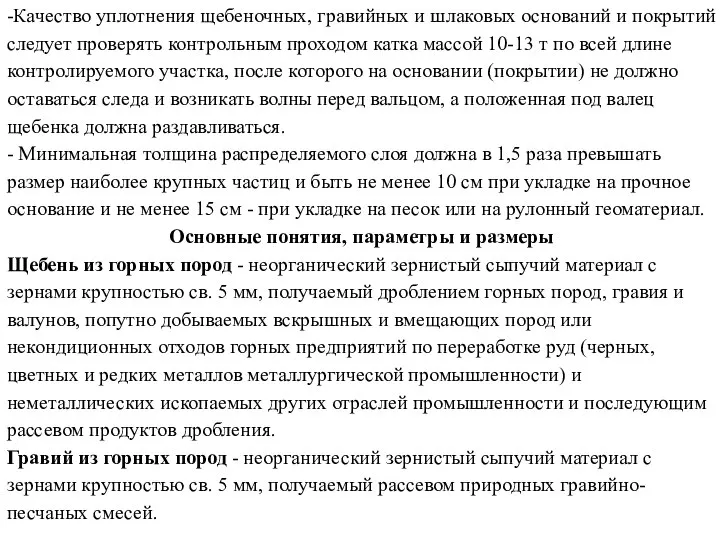
Основные понятия, параметры и размеры
Щебень из горных пород - неорганический зернистый сыпучий материал с зернами крупностью св. 5 мм, получаемый дроблением горных пород, гравия и валунов, попутно добываемых вскрышных и вмещающих пород или некондиционных отходов горных предприятий по переработке руд (черных, цветных и редких металлов металлургической промышленности) и неметаллических ископаемых других отраслей промышленности и последующим рассевом продуктов дробления.
Гравий из горных пород - неорганический зернистый сыпучий материал с зернами крупностью св. 5 мм, получаемый рассевом природных гравийно-песчаных смесей.
Слайд 3Основные параметры и размеры
Щебень и гравий выпускают в виде следующих основных фракций:
Основные параметры и размеры
Щебень и гравий выпускают в виде следующих основных фракций:
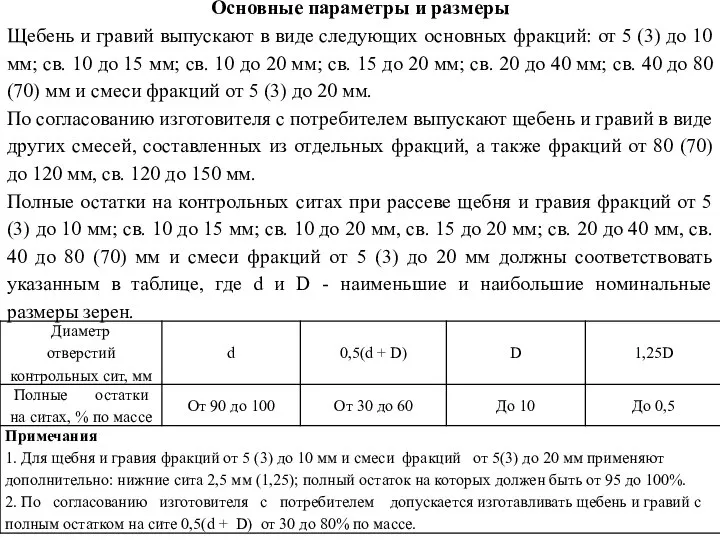
По согласованию изготовителя с потребителем выпускают щебень и гравий в виде других смесей, составленных из отдельных фракций, а также фракций от 80 (70) до 120 мм, св. 120 до 150 мм.
Полные остатки на контрольных ситах при рассеве щебня и гравия фракций от 5 (3) до 10 мм; св. 10 до 15 мм; св. 10 до 20 мм, св. 15 до 20 мм; св. 20 до 40 мм, св. 40 до 80 (70) мм и смеси фракций от 5 (3) до 20 мм должны соответствовать указанным в таблице, где d и D - наименьшие и наибольшие номинальные размеры зерен.
Слайд 4Лабораторные испытания - щебень и гравий из плотных горных пород для строительных
Лабораторные испытания - щебень и гравий из плотных горных пород для строительных

Проба - определенное количество материала, отобранное для испытаний от партии горной породы, щебня (гравия).
Точечная проба - проба материала, взятая единовременно из установленных нормативными документами мест партии.
Объединенная проба - проба материала, состоящая из точечных проб и характеризующая партию в целом.
Лабораторная проба - проба материала, приготовленная из объединенной пробы и предназначенная для всех лабораторных
Аналитическая проба - проба материала, приготовленная из лабораторной пробы и предназначенная для нескольких видов испытаний. Из аналитической пробы отбирают отдельные навески в соответствии с методикой испытаний. Допускается использование одной аналитической пробы для проведения нескольких видов испытаний, если в процессе предшествующих испытаний другие свойства материала не подвергаются изменению
Отбор проб
Масса лабораторной пробы при приемочном контроле на предприятии (карьере)-изготовителе должна быть не менее указанной в таблице
Слайд 5Таблица 3 Масса лабораторной пробы при приемочном контроле
-Указанную пробу используют для всех
Таблица 3 Масса лабораторной пробы при приемочном контроле
-Указанную пробу используют для всех
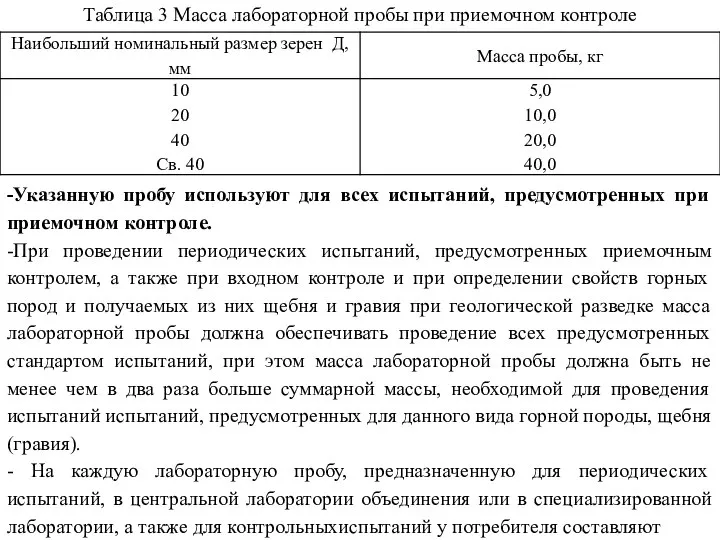
-При проведении периодических испытаний, предусмотренных приемочным контролем, а также при входном контроле и при определении свойств горных пород и получаемых из них щебня и гравия при геологической разведке масса лабораторной пробы должна обеспечивать проведение всех предусмотренных стандартом испытаний, при этом масса лабораторной пробы должна быть не менее чем в два раза больше суммарной массы, необходимой для проведения испытаний испытаний, предусмотренных для данного вида горной породы, щебня (гравия).
- На каждую лабораторную пробу, предназначенную для периодических испытаний, в центральной лаборатории объединения или в специализированной лаборатории, а также для контрольныхиспытаний у потребителя составляют
Слайд 6акт отбора проб, включающий наименование и обозначение материала, место и дату отбора
акт отбора проб, включающий наименование и обозначение материала, место и дату отбора
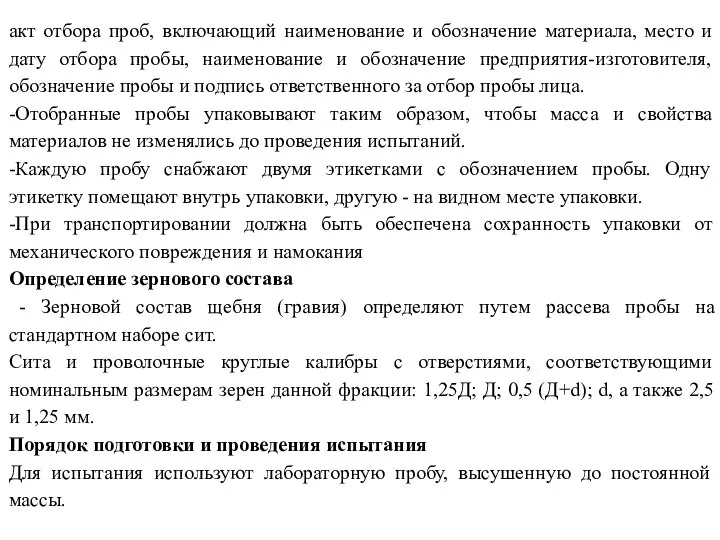
-Отобранные пробы упаковывают таким образом, чтобы масса и свойства материалов не изменялись до проведения испытаний.
-Каждую пробу снабжают двумя этикетками с обозначением пробы. Одну этикетку помещают внутрь упаковки, другую - на видном месте упаковки.
-При транспортировании должна быть обеспечена сохранность упаковки от механического повреждения и намокания
Определение зернового состава
- Зерновой состав щебня (гравия) определяют путем рассева пробы на стандартном наборе сит.
Сита и проволочные круглые калибры с отверстиями, соответствующими номинальным размерам зерен данной фракции: 1,25Д; Д; 0,5 (Д+d); d, а также 2,5 и 1,25 мм.
Порядок подготовки и проведения испытания
Для испытания используют лабораторную пробу, высушенную до постоянной массы.
Слайд 8-Определяют полные остатки на каждом сите в процентах массы пробы, равные сумме
-Определяют полные остатки на каждом сите в процентах массы пробы, равные сумме
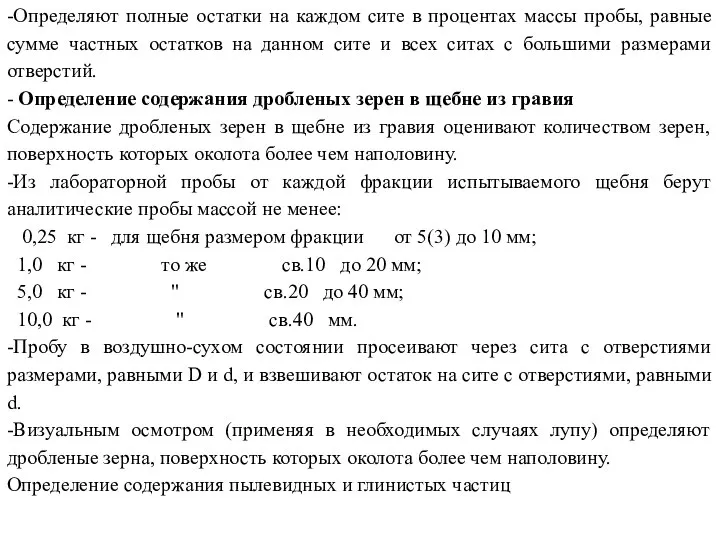
- Определение содержания дробленых зерен в щебне из гравия
Содержание дробленых зерен в щебне из гравия оценивают количеством зерен, поверхность которых околота более чем наполовину.
-Из лабораторной пробы от каждой фракции испытываемого щебня берут аналитические пробы массой не менее:
0,25 кг - для щебня размером фракции от 5(3) до 10 мм;
1,0 кг - то же св.10 до 20 мм;
5,0 кг - " св.20 до 40 мм;
10,0 кг - " св.40 мм.
-Пробу в воздушно-сухом состоянии просеивают через сита с отверстиями размерами, равными D и d, и взвешивают остаток на сите с отверстиями, равными d.
-Визуальным осмотром (применяя в необходимых случаях лупу) определяют дробленые зерна, поверхность которых околота более чем наполовину.
Определение содержания пылевидных и глинистых частиц
Слайд 9Метод отмучивания
-Содержание пылевидных и глинистых частиц в щебне (гравии) определяют по изменению
Метод отмучивания
-Содержание пылевидных и глинистых частиц в щебне (гравии) определяют по изменению

Порядок подготовки и проведения испытания
-Берут аналитическую пробу щебня (гравия) массой не менее 5 кг, высушенную до постоянной массы. При этом для испытания щебня (гравия) фракции от 5(3) до 10 мм используют целиком пробу, применяемую при определении зернового состава.
-Пробу щебня (гравия) помещают в сосуд для отмучивания или ведро, заливают водой несколько выше уровня щебня и оставляют в таком состоянии до полного размокания глинистой пленки (определяется визуально) на зернах щебня (гравия) или комков глины, если они имеются в пробе.
-После этого в сосуд или ведро со щебнем (гравием) доливают воду в таком количестве, чтобы высота слоя воды над щебнем была 200 мм; содержимое сосуда перемешивают деревянной мешалкой и оставляют в покое на 2 мин. Через 2 мин сливают полученную суспензию. При сливе суспензии необходимо оставлять слой ее над щебнем (гравием) высотой не менее 30 мм.
-Затем щебень (гравий) вновь заливают водой до указанного выше уровня. Промывку щебня (гравия) в указанной последовательности повторяют до тех пор, пока вода после промывки не будет оставаться прозрачной.
Слайд 10-Воду в сосуд для отмучивания щебня (гравия) наливают до верхнего сливного отверстия.
-Воду в сосуд для отмучивания щебня (гравия) наливают до верхнего сливного отверстия.
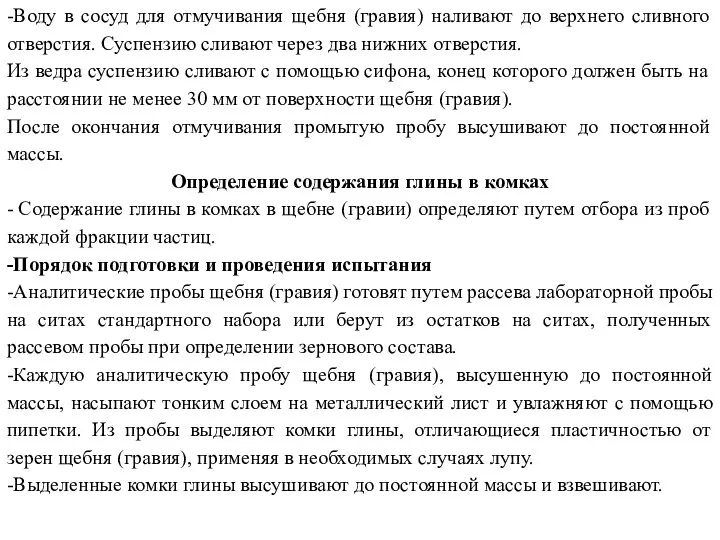
Из ведра суспензию сливают с помощью сифона, конец которого должен быть на расстоянии не менее 30 мм от поверхности щебня (гравия).
После окончания отмучивания промытую пробу высушивают до постоянной массы.
Определение содержания глины в комках
- Содержание глины в комках в щебне (гравии) определяют путем отбора из проб каждой фракции частиц.
-Порядок подготовки и проведения испытания
-Аналитические пробы щебня (гравия) готовят путем рассева лабораторной пробы на ситах стандартного набора или берут из остатков на ситах, полученных рассевом пробы при определении зернового состава.
-Каждую аналитическую пробу щебня (гравия), высушенную до постоянной массы, насыпают тонким слоем на металлический лист и увлажняют с помощью пипетки. Из пробы выделяют комки глины, отличающиеся пластичностью от зерен щебня (гравия), применяя в необходимых случаях лупу.
-Выделенные комки глины высушивают до постоянной массы и взвешивают.
Слайд 11Определение содержания зерен пластинчатой (лещадной) и игловатой форм
Метод визуальной разборки
-Содержание в щебне
Определение содержания зерен пластинчатой (лещадной) и игловатой форм
Метод визуальной разборки
-Содержание в щебне
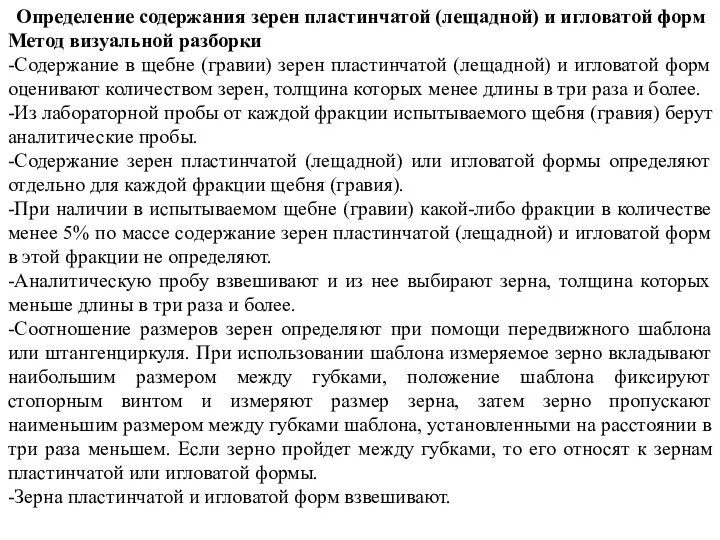
-Из лабораторной пробы от каждой фракции испытываемого щебня (гравия) берут аналитические пробы.
-Содержание зерен пластинчатой (лещадной) или игловатой формы определяют отдельно для каждой фракции щебня (гравия).
-При наличии в испытываемом щебне (гравии) какой-либо фракции в количестве менее 5% по массе содержание зерен пластинчатой (лещадной) и игловатой форм в этой фракции не определяют.
-Аналитическую пробу взвешивают и из нее выбирают зерна, толщина которых меньше длины в три раза и более.
-Соотношение размеров зерен определяют при помощи передвижного шаблона или штангенциркуля. При использовании шаблона измеряемое зерно вкладывают наибольшим размером между губками, положение шаблона фиксируют стопорным винтом и измеряют размер зерна, затем зерно пропускают наименьшим размером между губками шаблона, установленными на расстоянии в три раза меньшем. Если зерно пройдет между губками, то его относят к зернам пластинчатой или игловатой формы.
-Зерна пластинчатой и игловатой форм взвешивают.
Слайд 12Определение дробимости
Дробимость щебня (гравия) определяют по степени разрушения зерен при сжатии (раздавливании)
Определение дробимости
Дробимость щебня (гравия) определяют по степени разрушения зерен при сжатии (раздавливании)
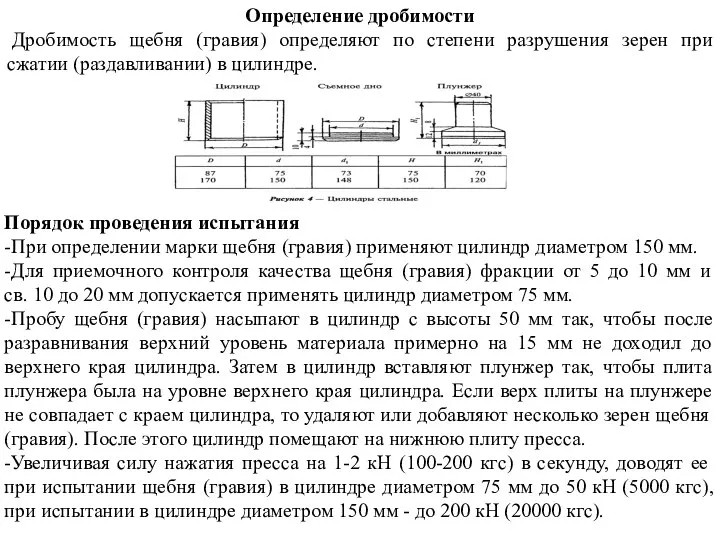
Порядок проведения испытания
-При определении марки щебня (гравия) применяют цилиндр диаметром 150 мм.
-Для приемочного контроля качества щебня (гравия) фракции от 5 до 10 мм и св. 10 до 20 мм допускается применять цилиндр диаметром 75 мм.
-Пробу щебня (гравия) насыпают в цилиндр с высоты 50 мм так, чтобы после разравнивания верхний уровень материала примерно на 15 мм не доходил до верхнего края цилиндра. Затем в цилиндр вставляют плунжер так, чтобы плита плунжера была на уровне верхнего края цилиндра. Если верх плиты на плунжере не совпадает с краем цилиндра, то удаляют или добавляют несколько зерен щебня (гравия). После этого цилиндр помещают на нижнюю плиту пресса.
-Увеличивая силу нажатия пресса на 1-2 кН (100-200 кгс) в секунду, доводят ее при испытании щебня (гравия) в цилиндре диаметром 75 мм до 50 кН (5000 кгс), при испытании в цилиндре диаметром 150 мм - до 200 кН (20000 кгс).
Слайд 13-После сжатия испытываемую пробу высыпают из цилиндра и взвешивают. Затем ее просеивают
-После сжатия испытываемую пробу высыпают из цилиндра и взвешивают. Затем ее просеивают
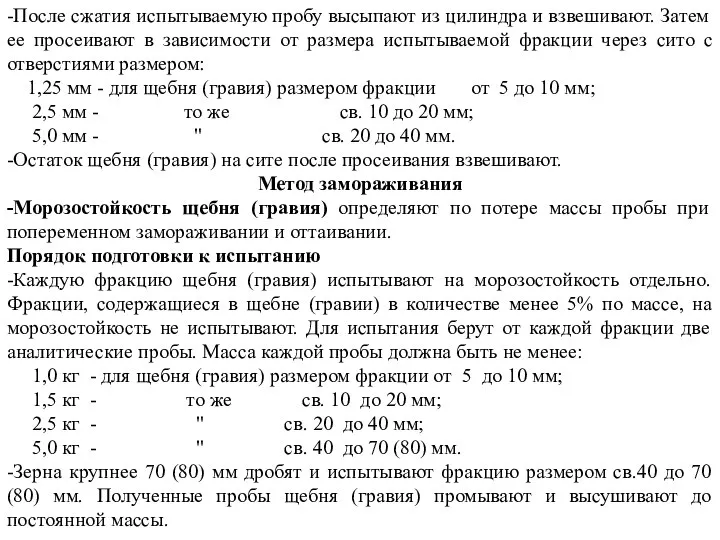
1,25 мм - для щебня (гравия) размером фракции от 5 до 10 мм;
2,5 мм - то же св. 10 до 20 мм;
5,0 мм - " св. 20 до 40 мм.
-Остаток щебня (гравия) на сите после просеивания взвешивают.
Метод замораживания
-Морозостойкость щебня (гравия) определяют по потере массы пробы при попеременном замораживании и оттаивании.
Порядок подготовки к испытанию
-Каждую фракцию щебня (гравия) испытывают на морозостойкость отдельно. Фракции, содержащиеся в щебне (гравии) в количестве менее 5% по массе, на морозостойкость не испытывают. Для испытания берут от каждой фракции две аналитические пробы. Масса каждой пробы должна быть не менее:
1,0 кг - для щебня (гравия) размером фракции от 5 до 10 мм;
1,5 кг - то же св. 10 до 20 мм;
2,5 кг - " св. 20 до 40 мм;
5,0 кг - " св. 40 до 70 (80) мм.
-Зерна крупнее 70 (80) мм дробят и испытывают фракцию размером св.40 до 70 (80) мм. Полученные пробы щебня (гравия) промывают и высушивают до постоянной массы.
Слайд 14Порядок проведения испытания
-Аналитическую пробу щебня (гравия) данной фракции равномерно насыпают в металлический
Порядок проведения испытания
-Аналитическую пробу щебня (гравия) данной фракции равномерно насыпают в металлический
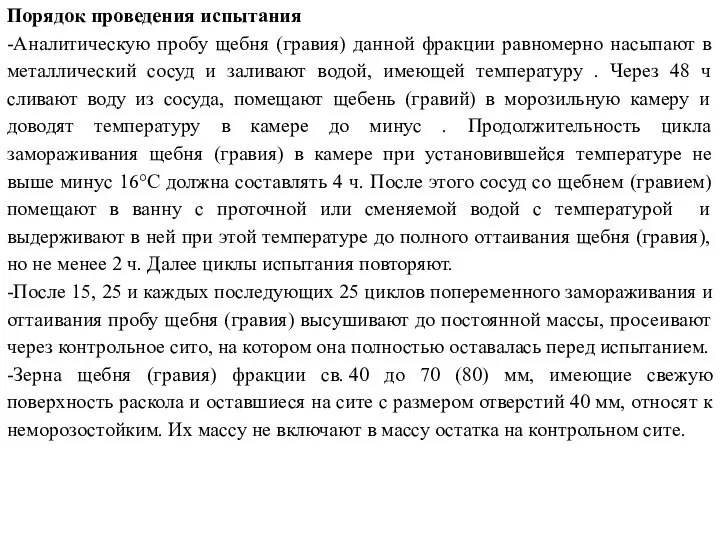
-После 15, 25 и каждых последующих 25 циклов попеременного замораживания и оттаивания пробу щебня (гравия) высушивают до постоянной массы, просеивают через контрольное сито, на котором она полностью оставалась перед испытанием.
-Зерна щебня (гравия) фракции св. 40 до 70 (80) мм, имеющие свежую поверхность раскола и оставшиеся на сите с размером отверстий 40 мм, относят к неморозостойким. Их массу не включают в массу остатка на контрольном сите.
Слайд 15Контроль качества работ при устройстве асфальтобетонных слоев
При приготовлении асфальтобетонной смеси следует контролировать:
постоянно
Контроль качества работ при устройстве асфальтобетонных слоев
При приготовлении асфальтобетонной смеси следует контролировать:
постоянно
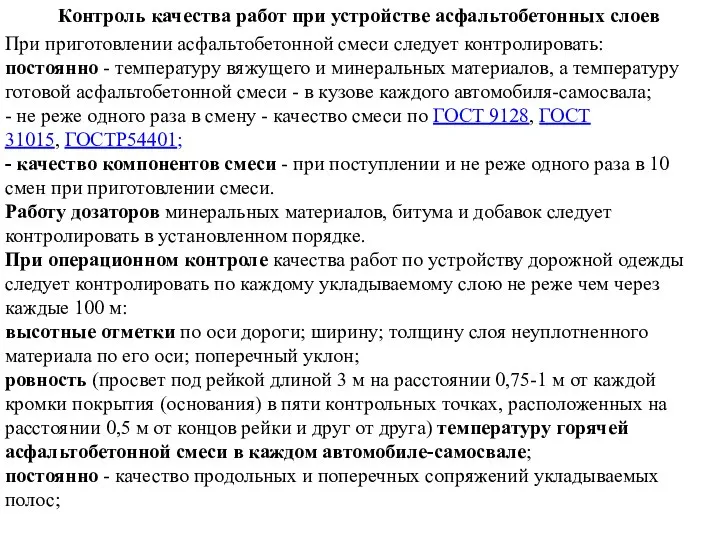
- качество компонентов смеси - при поступлении и не реже одного раза в 10 смен при приготовлении смеси.
Работу дозаторов минеральных материалов, битума и добавок следует контролировать в установленном порядке.
При операционном контроле качества работ по устройству дорожной одежды следует контролировать по каждому укладываемому слою не реже чем через каждые 100 м:
высотные отметки по оси дороги; ширину; толщину слоя неуплотненного материала по его оси; поперечный уклон;
ровность (просвет под рейкой длиной 3 м на расстоянии 0,75-1 м от каждой кромки покрытия (основания) в пяти контрольных точках, расположенных на расстоянии 0,5 м от концов рейки и друг от друга) температуру горячей асфальтобетонной смеси в каждом автомобиле-самосвале;
постоянно - качество продольных и поперечных сопряжений укладываемых полос;
Слайд 16Качество асфальтобетона по показателям кернов (вырубок) в трех местах на 3000 м/кв
Качество асфальтобетона по показателям кернов (вырубок) в трех местах на 3000 м/кв
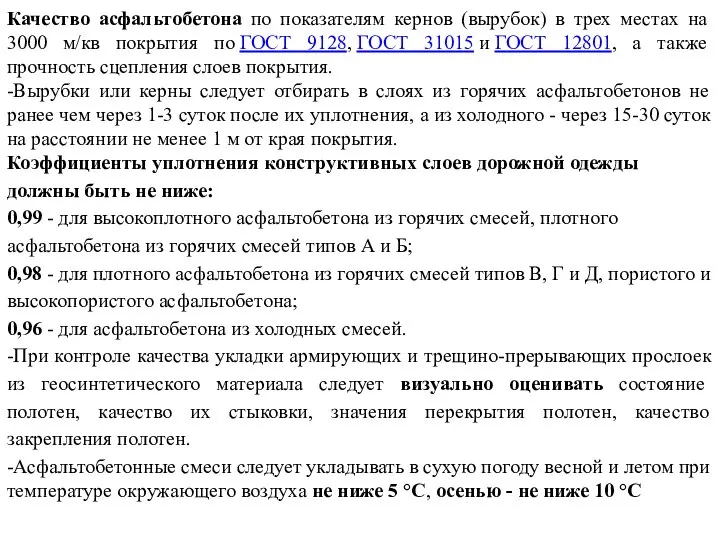
-Вырубки или керны следует отбирать в слоях из горячих асфальтобетонов не ранее чем через 1-3 суток после их уплотнения, а из холодного - через 15-30 суток на расстоянии не менее 1 м от края покрытия.
Коэффициенты уплотнения конструктивных слоев дорожной одежды должны быть не ниже: 0,99 - для высокоплотного асфальтобетона из горячих смесей, плотного асфальтобетона из горячих смесей типов А и Б; 0,98 - для плотного асфальтобетона из горячих смесей типов В, Г и Д, пористого и высокопористого асфальтобетона; 0,96 - для асфальтобетона из холодных смесей.
-При контроле качества укладки армирующих и трещино-прерывающих прослоек из геосинтетического материала следует визуально оценивать состояние полотен, качество их стыковки, значения перекрытия полотен, качество закрепления полотен.
-Асфальтобетонные смеси следует укладывать в сухую погоду весной и летом при температуре окружающего воздуха не ниже 5 °С, осенью - не ниже 10 °С
Слайд 17-Толщина устраиваемого слоя асфальтобетона над прослойкой из геосинтетических материалов должна быть не
-Толщина устраиваемого слоя асфальтобетона над прослойкой из геосинтетических материалов должна быть не
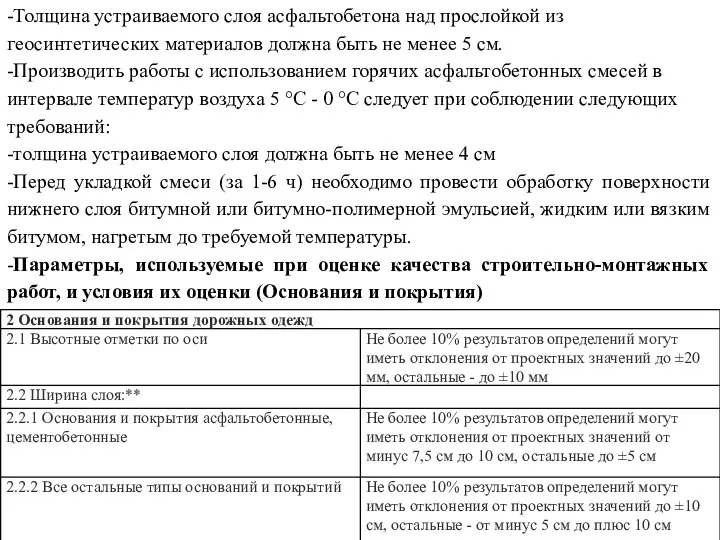
-Производить работы с использованием горячих асфальтобетонных смесей в интервале температур воздуха 5 °С - 0 °С следует при соблюдении следующих требований: -толщина устраиваемого слоя должна быть не менее 4 см
-Перед укладкой смеси (за 1-6 ч) необходимо провести обработку поверхности нижнего слоя битумной или битумно-полимерной эмульсией, жидким или вязким битумом, нагретым до требуемой температуры.
-Параметры, используемые при оценке качества строительно-монтажных работ, и условия их оценки (Основания и покрытия)
Слайд 25Порядок проведения испытания
Предел прочности при сжатии образцов определяют на прессах при скорости
Порядок проведения испытания
Предел прочности при сжатии образцов определяют на прессах при скорости
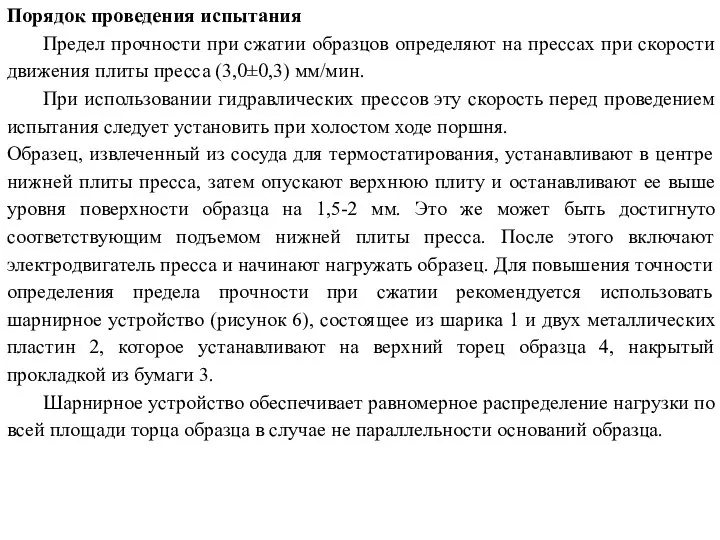
При использовании гидравлических прессов эту скорость перед проведением испытания следует установить при холостом ходе поршня.
Образец, извлеченный из сосуда для термостатирования, устанавливают в центре нижней плиты пресса, затем опускают верхнюю плиту и останавливают ее выше уровня поверхности образца на 1,5-2 мм. Это же может быть достигнуто соответствующим подъемом нижней плиты пресса. После этого включают электродвигатель пресса и начинают нагружать образец. Для повышения точности определения предела прочности при сжатии рекомендуется использовать шарнирное устройство (рисунок 6), состоящее из шарика 1 и двух металлических пластин 2, которое устанавливают на верхний торец образца 4, накрытый прокладкой из бумаги 3.
Шарнирное устройство обеспечивает равномерное распределение нагрузки по всей площади торца образца в случае не параллельности оснований образца.
Слайд 27-При использовании гидравлических прессов требуемую скорость перед проведением испытания следует установить при
-При использовании гидравлических прессов требуемую скорость перед проведением испытания следует установить при
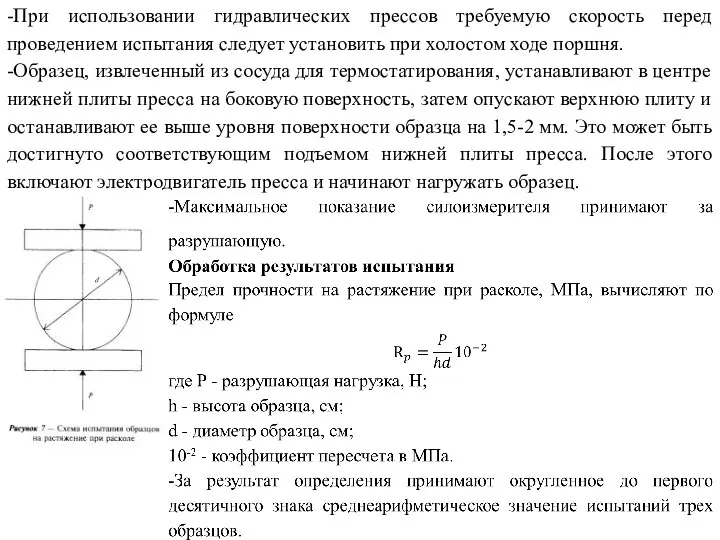
-Образец, извлеченный из сосуда для термостатирования, устанавливают в центре нижней плиты пресса на боковую поверхность, затем опускают верхнюю плиту и останавливают ее выше уровня поверхности образца на 1,5-2 мм. Это может быть достигнуто соответствующим подъемом нижней плиты пресса. После этого включают электродвигатель пресса и начинают нагружать образец.
Слайд 28Определение предела прочности на растяжение при изгибе и показателей деформативности
Порядок подготовки и
Определение предела прочности на растяжение при изгибе и показателей деформативности
Порядок подготовки и
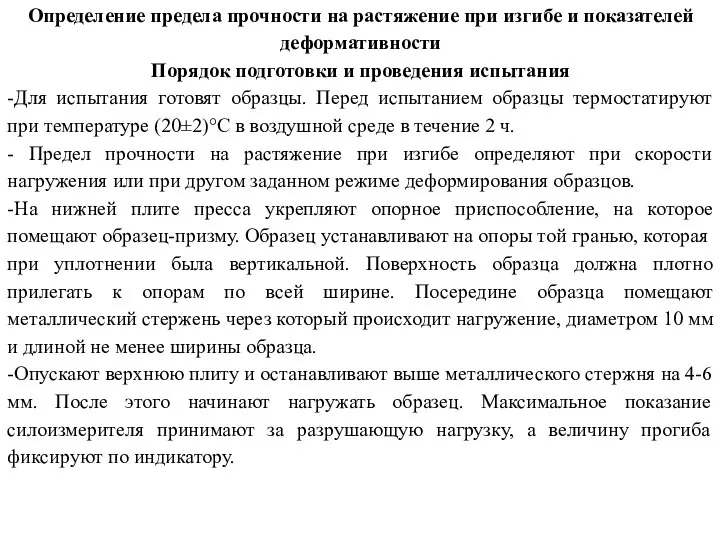
-Для испытания готовят образцы. Перед испытанием образцы термостатируют при температуре (20±2)°С в воздушной среде в течение 2 ч.
- Предел прочности на растяжение при изгибе определяют при скорости нагружения или при другом заданном режиме деформирования образцов.
-На нижней плите пресса укрепляют опорное приспособление, на которое помещают образец-призму. Образец устанавливают на опоры той гранью, которая при уплотнении была вертикальной. Поверхность образца должна плотно прилегать к опорам по всей ширине. Посередине образца помещают металлический стержень через который происходит нагружение, диаметром 10 мм и длиной не менее ширины образца.
-Опускают верхнюю плиту и останавливают выше металлического стержня на 4-6 мм. После этого начинают нагружать образец. Максимальное показание силоизмерителя принимают за разрушающую нагрузку, а величину прогиба фиксируют по индикатору.
Слайд 29
Схема испытания образцов-призм на изгиб
Схема испытания образцов-призм на изгиб
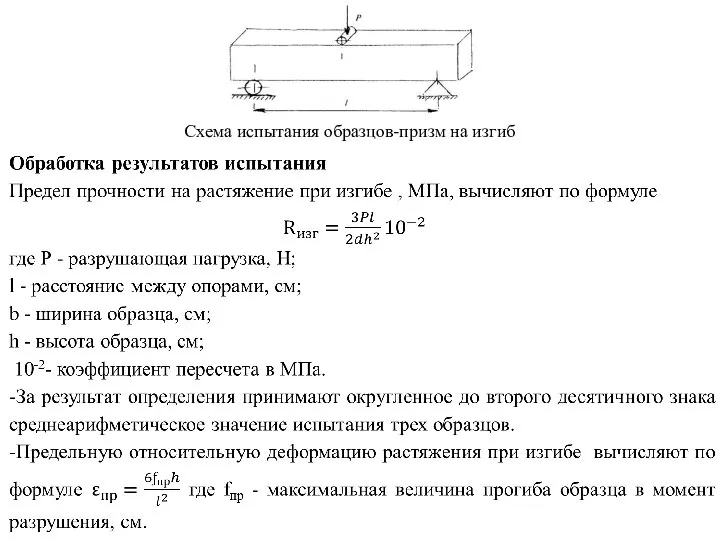
Слайд 31-Порядок подготовки к проведению испытания
-Для испытания асфальтобетона на сдвигоустойчивость готовят четное число
-Порядок подготовки к проведению испытания
-Для испытания асфальтобетона на сдвигоустойчивость готовят четное число
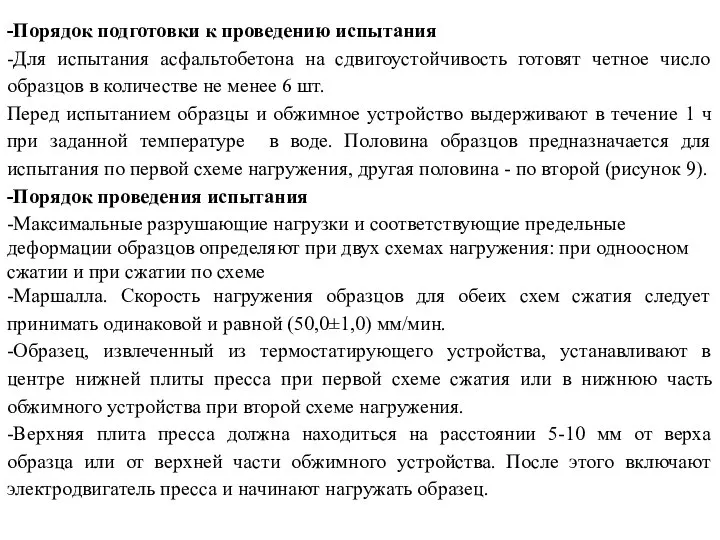
Перед испытанием образцы и обжимное устройство выдерживают в течение 1 ч при заданной температуре в воде. Половина образцов предназначается для испытания по первой схеме нагружения, другая половина - по второй (рисунок 9).
-Порядок проведения испытания
-Максимальные разрушающие нагрузки и соответствующие предельные деформации образцов определяют при двух схемах нагружения: при одноосном сжатии и при сжатии по схеме
-Маршалла. Скорость нагружения образцов для обеих схем сжатия следует принимать одинаковой и равной (50,0±1,0) мм/мин.
-Образец, извлеченный из термостатирующего устройства, устанавливают в центре нижней плиты пресса при первой схеме сжатия или в нижнюю часть обжимного устройства при второй схеме нагружения.
-Верхняя плита пресса должна находиться на расстоянии 5-10 мм от верха образца или от верхней части обжимного устройства. После этого включают электродвигатель пресса и начинают нагружать образец.
Слайд 35Определение морозостойкости
Сущность метода заключается в оценке потери прочности при сжатии предварительно водонасыщенных
Определение морозостойкости
Сущность метода заключается в оценке потери прочности при сжатии предварительно водонасыщенных
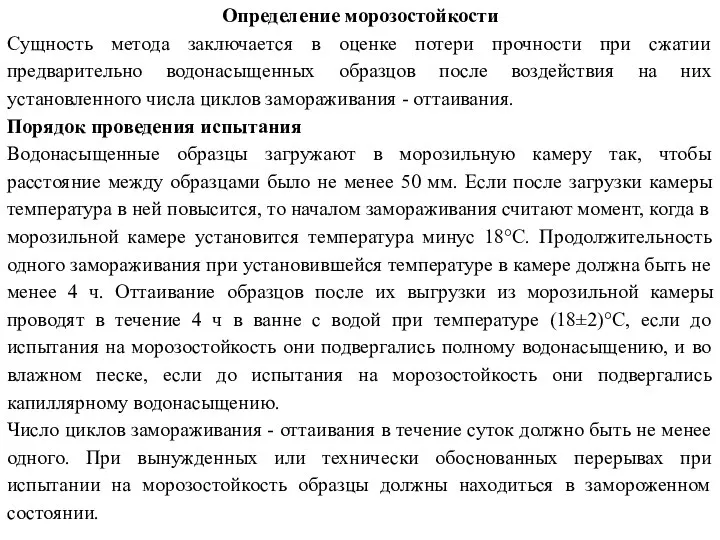
Порядок проведения испытания
Водонасыщенные образцы загружают в морозильную камеру так, чтобы расстояние между образцами было не менее 50 мм. Если после загрузки камеры температура в ней повысится, то началом замораживания считают момент, когда в морозильной камере установится температура минус 18°С. Продолжительность одного замораживания при установившейся температуре в камере должна быть не менее 4 ч. Оттаивание образцов после их выгрузки из морозильной камеры проводят в течение 4 ч в ванне с водой при температуре (18±2)°C, если до испытания на морозостойкость они подвергались полному водонасыщению, и во влажном песке, если до испытания на морозостойкость они подвергались капиллярному водонасыщению.
Число циклов замораживания - оттаивания в течение суток должно быть не менее одного. При вынужденных или технически обоснованных перерывах при испытании на морозостойкость образцы должны находиться в замороженном состоянии.
Слайд 37-Метод экстрагирования вяжущего
-Метод предусматривает определение содержания вяжущего путем экстрагирования его из смеси
-Метод экстрагирования вяжущего
-Метод предусматривает определение содержания вяжущего путем экстрагирования его из смеси
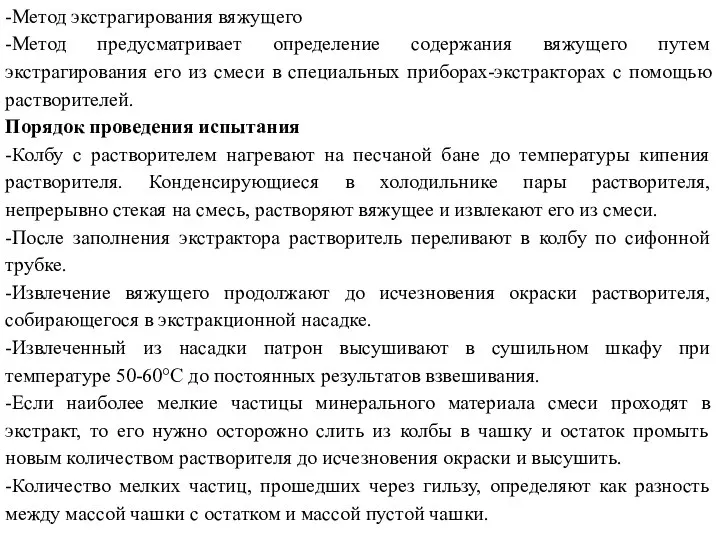
Порядок проведения испытания
-Колбу с растворителем нагревают на песчаной бане до температуры кипения растворителя. Конденсирующиеся в холодильнике пары растворителя, непрерывно стекая на смесь, растворяют вяжущее и извлекают его из смеси.
-После заполнения экстрактора растворитель переливают в колбу по сифонной трубке.
-Извлечение вяжущего продолжают до исчезновения окраски растворителя, собирающегося в экстракционной насадке.
-Извлеченный из насадки патрон высушивают в сушильном шкафу при температуре 50-60°С до постоянных результатов взвешивания.
-Если наиболее мелкие частицы минерального материала смеси проходят в экстракт, то его нужно осторожно слить из колбы в чашку и остаток промыть новым количеством растворителя до исчезновения окраски и высушить.
-Количество мелких частиц, прошедших через гильзу, определяют как разность между массой чашки с остатком и массой пустой чашки.
Слайд 39Определение зернового состава минеральной части смеси после экстрагирования
Проведение испытания и обработка результатов
Определение зернового состава минеральной части смеси после экстрагирования
Проведение испытания и обработка результатов
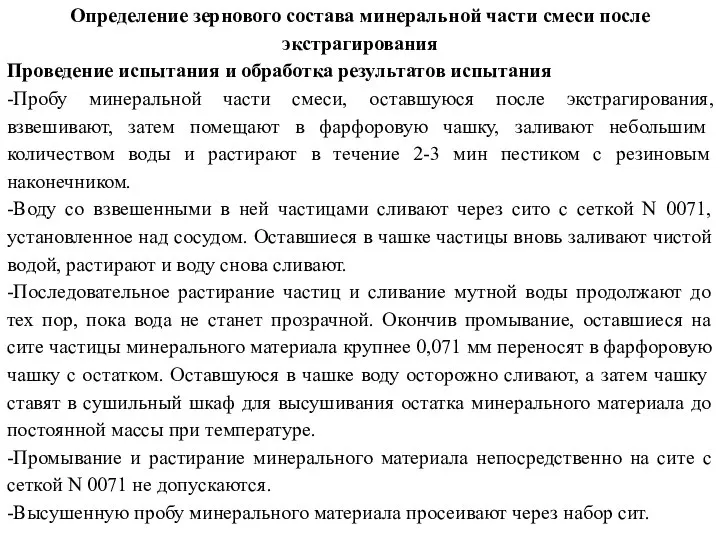
-Пробу минеральной части смеси, оставшуюся после экстрагирования, взвешивают, затем помещают в фарфоровую чашку, заливают небольшим количеством воды и растирают в течение 2-3 мин пестиком с резиновым наконечником.
-Воду со взвешенными в ней частицами сливают через сито с сеткой N 0071, установленное над сосудом. Оставшиеся в чашке частицы вновь заливают чистой водой, растирают и воду снова сливают.
-Последовательное растирание частиц и сливание мутной воды продолжают до тех пор, пока вода не станет прозрачной. Окончив промывание, оставшиеся на сите частицы минерального материала крупнее 0,071 мм переносят в фарфоровую чашку с остатком. Оставшуюся в чашке воду осторожно сливают, а затем чашку ставят в сушильный шкаф для высушивания остатка минерального материала до постоянной массы при температуре.
-Промывание и растирание минерального материала непосредственно на сите с сеткой N 0071 не допускаются.
-Высушенную пробу минерального материала просеивают через набор сит.
Слайд 40-Перед окончанием просеивания для проверки каждое сито вручную интенсивно встряхивают в течение
-Перед окончанием просеивания для проверки каждое сито вручную интенсивно встряхивают в течение
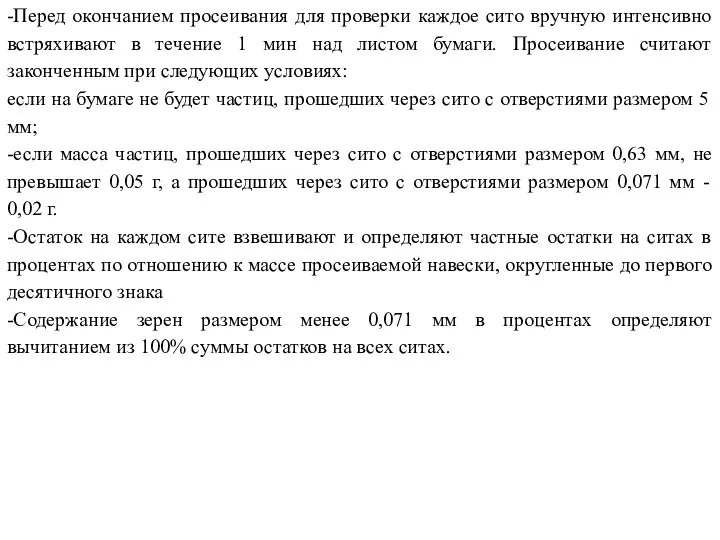
если на бумаге не будет частиц, прошедших через сито с отверстиями размером 5 мм;
-если масса частиц, прошедших через сито с отверстиями размером 0,63 мм, не превышает 0,05 г, а прошедших через сито с отверстиями размером 0,071 мм - 0,02 г.
-Остаток на каждом сите взвешивают и определяют частные остатки на ситах в процентах по отношению к массе просеиваемой навески, округленные до первого десятичного знака
-Содержание зерен размером менее 0,071 мм в процентах определяют вычитанием из 100% суммы остатков на всех ситах.
Слайд 43-Порядок проведения испытания
-Химический стакан заполняют на 2/3 объема дистиллированной водой, устанавливают на
-Порядок проведения испытания
-Химический стакан заполняют на 2/3 объема дистиллированной водой, устанавливают на
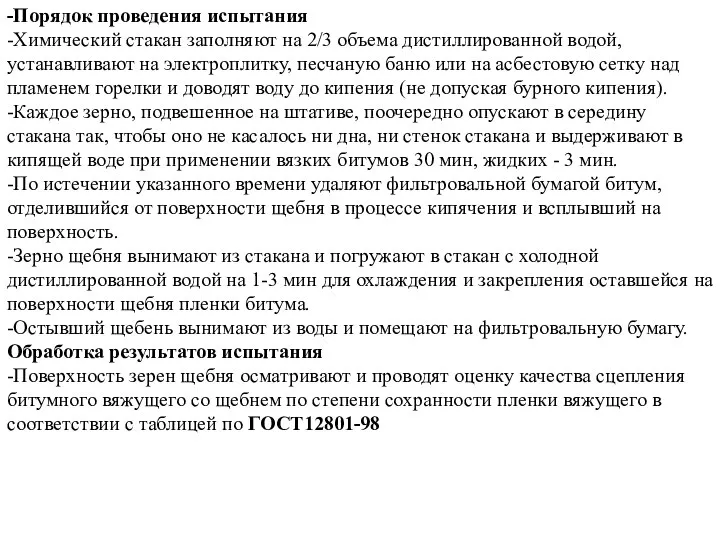
-Каждое зерно, подвешенное на штативе, поочередно опускают в середину стакана так, чтобы оно не касалось ни дна, ни стенок стакана и выдерживают в кипящей воде при применении вязких битумов 30 мин, жидких - 3 мин.
-По истечении указанного времени удаляют фильтровальной бумагой битум, отделившийся от поверхности щебня в процессе кипячения и всплывший на поверхность.
-Зерно щебня вынимают из стакана и погружают в стакан с холодной дистиллированной водой на 1-3 мин для охлаждения и закрепления оставшейся на поверхности щебня пленки битума.
-Остывший щебень вынимают из воды и помещают на фильтровальную бумагу.
Обработка результатов испытания
-Поверхность зерен щебня осматривают и проводят оценку качества сцепления битумного вяжущего со щебнем по степени сохранности пленки вяжущего в соответствии с таблицей по ГОСТ12801-98
Слайд 44Битумы нефтяные дорожные
Битумы нефтяные дорожные
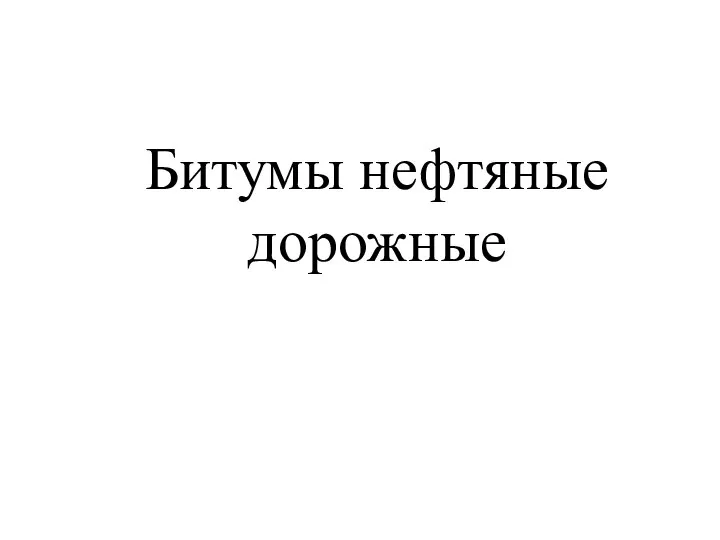
Слайд 45-Вязкие нефтяные дорожные битумы изготовляют окислением продуктов прямой перегонки нефти и селективного
-Вязкие нефтяные дорожные битумы изготовляют окислением продуктов прямой перегонки нефти и селективного
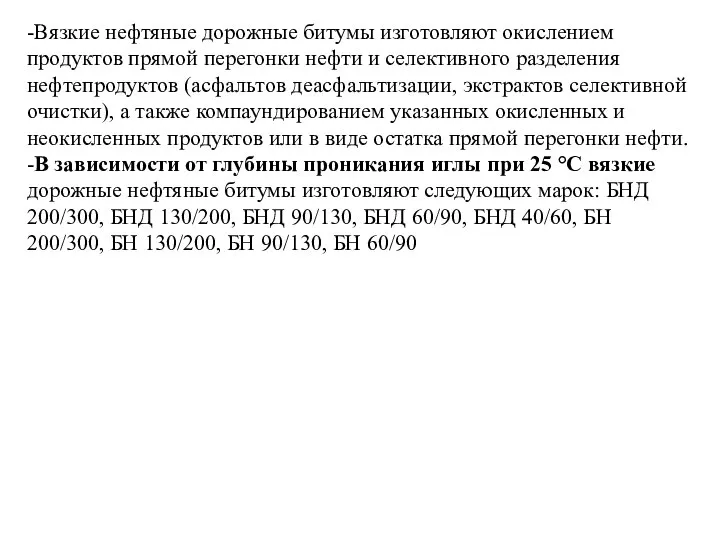
-В зависимости от глубины проникания иглы при 25 °С вязкие дорожные нефтяные битумы изготовляют следующих марок: БНД 200/300, БНД 130/200, БНД 90/130, БНД 60/90, БНД 40/60, БН 200/300, БН 130/200, БН 90/130, БН 60/90
Слайд 46- Обезвоженный и расплавленный до подвижного состояния битум процеживают через металлическое сито
- Обезвоженный и расплавленный до подвижного состояния битум процеживают через металлическое сито
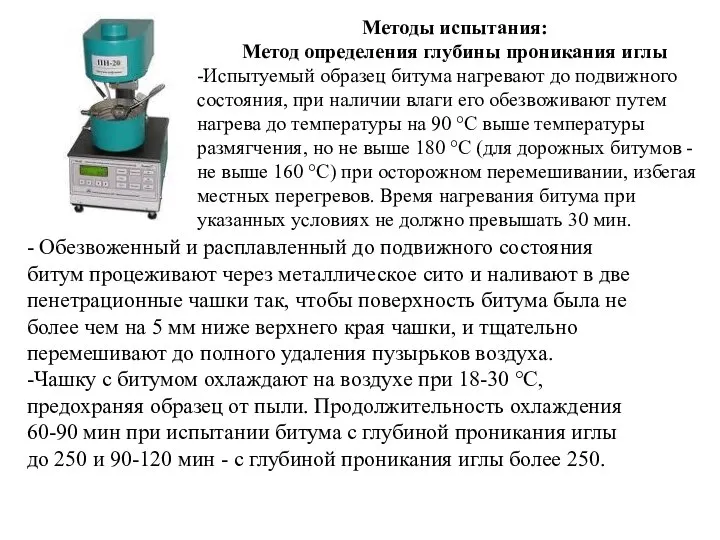
-Чашку с битумом охлаждают на воздухе при 18-30 °С, предохраняя образец от пыли. Продолжительность охлаждения 60-90 мин при испытании битума с глубиной проникания иглы до 250 и 90-120 мин - с глубиной проникания иглы более 250.
Методы испытания:
Метод определения глубины проникания иглы
-Испытуемый образец битума нагревают до подвижного состояния, при наличии влаги его обезвоживают путем нагрева до температуры на 90 °С выше температуры размягчения, но не выше 180 °С (для дорожных битумов - не выше 160 °С) при осторожном перемешивании, избегая местных перегревов. Время нагревания битума при указанных условиях не должно превышать 30 мин.
Слайд 47-Затем чашки с битумом помещают в баню для термостатирования при заданной температуре
-Затем чашки с битумом помещают в баню для термостатирования при заданной температуре
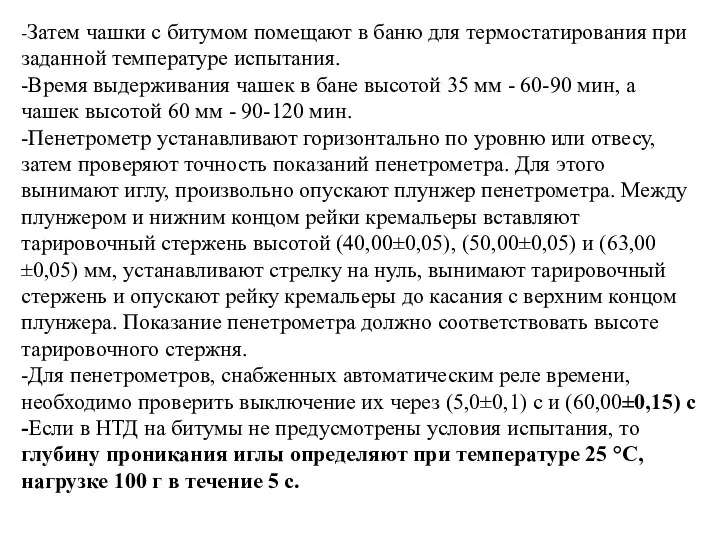
-Время выдерживания чашек в бане высотой 35 мм - 60-90 мин, а чашек высотой 60 мм - 90-120 мин.
-Пенетрометр устанавливают горизонтально по уровню или отвесу, затем проверяют точность показаний пенетрометра. Для этого вынимают иглу, произвольно опускают плунжер пенетрометра. Между плунжером и нижним концом рейки кремальеры вставляют тарировочный стержень высотой (40,00±0,05), (50,00±0,05) и (63,00±0,05) мм, устанавливают стрелку на нуль, вынимают тарировочный стержень и опускают рейку кремальеры до касания с верхним концом плунжера. Показание пенетрометра должно соответствовать высоте тарировочного стержня.
-Для пенетрометров, снабженных автоматическим реле времени, необходимо проверить выключение их через (5,0±0,1) с и (60,00±0,15) с -Если в НТД на битумы не предусмотрены условия испытания, то глубину проникания иглы определяют при температуре 25 °С, нагрузке 100 г в течение 5 с.
Слайд 48-По истечении заданного времени выдерживания чашку с образцом битума вынимают из бани
-По истечении заданного времени выдерживания чашку с образцом битума вынимают из бани
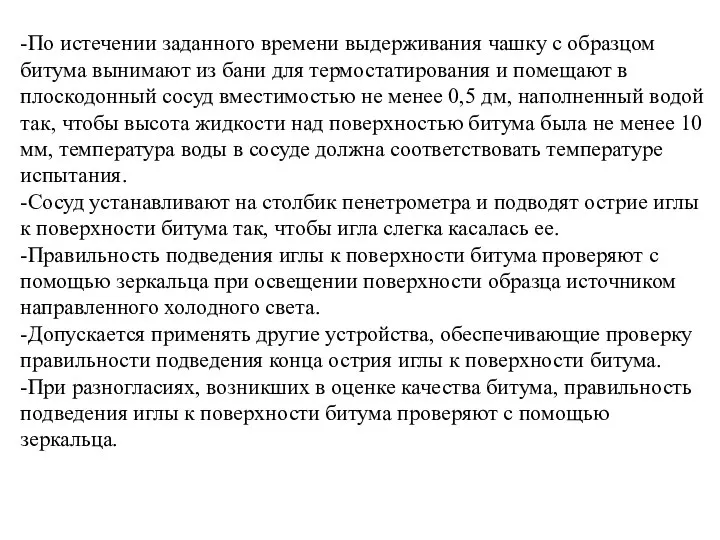
-Сосуд устанавливают на столбик пенетрометра и подводят острие иглы к поверхности битума так, чтобы игла слегка касалась ее.
-Правильность подведения иглы к поверхности битума проверяют с помощью зеркальца при освещении поверхности образца источником направленного холодного света.
-Допускается применять другие устройства, обеспечивающие проверку правильности подведения конца острия иглы к поверхности битума.
-При разногласиях, возникших в оценке качества битума, правильность подведения иглы к поверхности битума проверяют с помощью зеркальца.
Слайд 49-Доводят кремальеру до верхней площадки плунжера, несущего иглу, и устанавливают стрелку на
-Доводят кремальеру до верхней площадки плунжера, несущего иглу, и устанавливают стрелку на
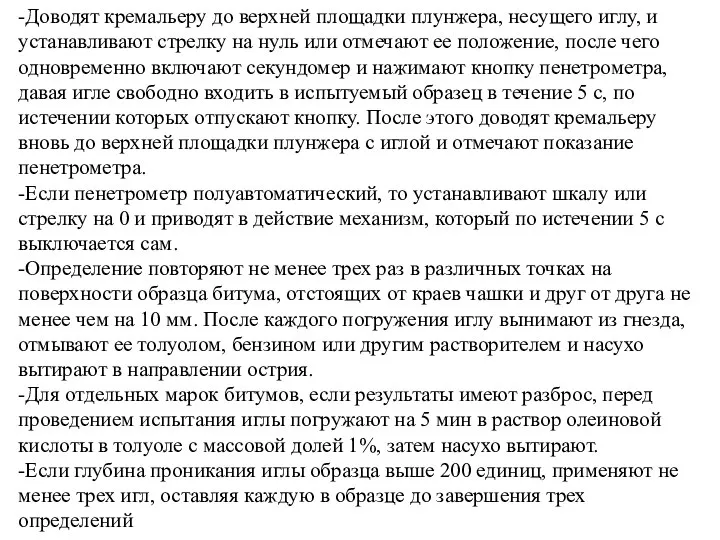
-Если пенетрометр полуавтоматический, то устанавливают шкалу или стрелку на 0 и приводят в действие механизм, который по истечении 5 с выключается сам.
-Определение повторяют не менее трех раз в различных точках на поверхности образца битума, отстоящих от краев чашки и друг от друга не менее чем на 10 мм. После каждого погружения иглу вынимают из гнезда, отмывают ее толуолом, бензином или другим растворителем и насухо вытирают в направлении острия.
-Для отдельных марок битумов, если результаты имеют разброс, перед проведением испытания иглы погружают на 5 мин в раствор олеиновой кислоты в толуоле с массовой долей 1%, затем насухо вытирают.
-Если глубина проникания иглы образца выше 200 единиц, применяют не менее трех игл, оставляя каждую в образце до завершения трех определений
Слайд 50Метод определения температуры размягчения по кольцу и шару
-Битум наливают с некоторым избытком
Метод определения температуры размягчения по кольцу и шару
-Битум наливают с некоторым избытком
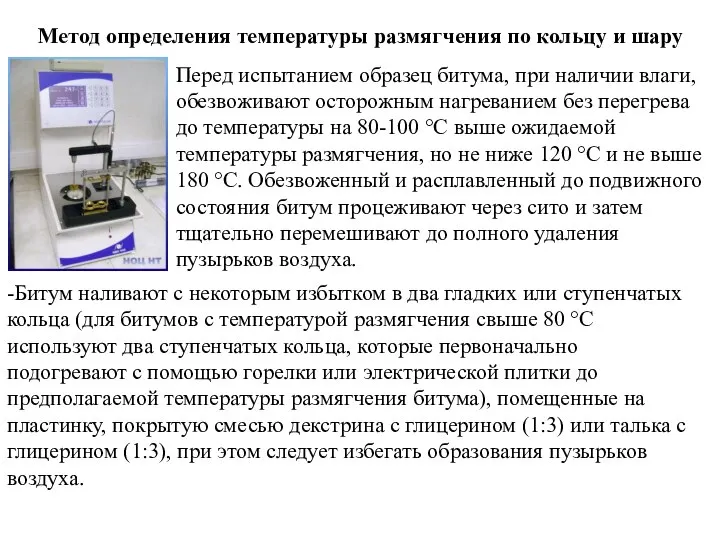
Перед испытанием образец битума, при наличии влаги, обезвоживают осторожным нагреванием без перегрева до температуры на 80-100 °С выше ожидаемой температуры размягчения, но не ниже 120 °С и не выше 180 °С. Обезвоженный и расплавленный до подвижного состояния битум процеживают через сито и затем тщательно перемешивают до полного удаления пузырьков воздуха.
Слайд 51 -После охлаждения колец с битумом на воздухе в течение 30 мин
-После охлаждения колец с битумом на воздухе в течение 30 мин
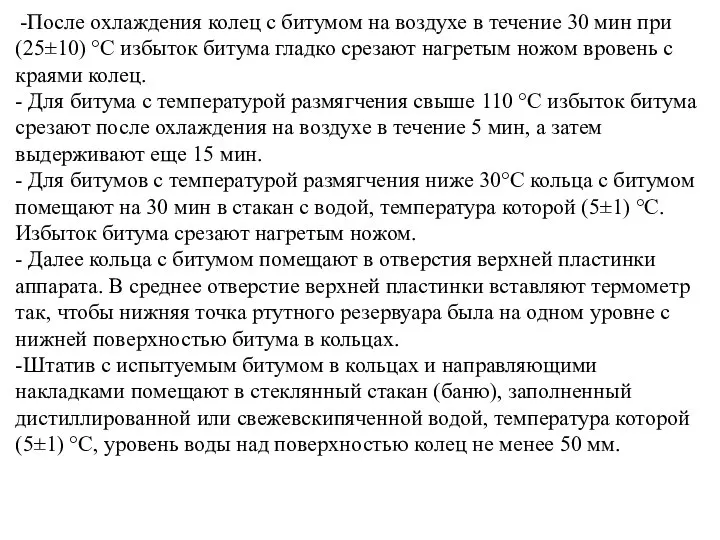
- Для битума с температурой размягчения свыше 110 °С избыток битума срезают после охлаждения на воздухе в течение 5 мин, а затем выдерживают еще 15 мин.
- Для битумов с температурой размягчения ниже 30°С кольца с битумом помещают на 30 мин в стакан с водой, температура которой (5±1) °С. Избыток битума срезают нагретым ножом.
- Далее кольца с битумом помещают в отверстия верхней пластинки аппарата. В среднее отверстие верхней пластинки вставляют термометр так, чтобы нижняя точка ртутного резервуара была на одном уровне с нижней поверхностью битума в кольцах.
-Штатив с испытуемым битумом в кольцах и направляющими накладками помещают в стеклянный стакан (баню), заполненный дистиллированной или свежевскипяченной водой, температура которой (5±1) °С, уровень воды над поверхностью колец не менее 50 мм.
Слайд 52-По истечении 15 мин штатив вынимают из бани, на каждое кольцо в
-По истечении 15 мин штатив вынимают из бани, на каждое кольцо в
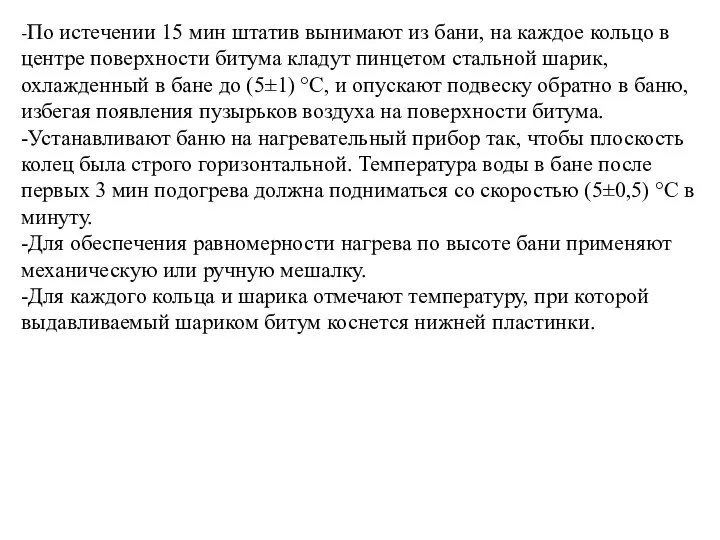
-Устанавливают баню на нагревательный прибор так, чтобы плоскость колец была строго горизонтальной. Температура воды в бане после первых 3 мин подогрева должна подниматься со скоростью (5±0,5) °С в минуту.
-Для обеспечения равномерности нагрева по высоте бани применяют механическую или ручную мешалку.
-Для каждого кольца и шарика отмечают температуру, при которой выдавливаемый шариком битум коснется нижней пластинки.
Слайд 53Метод определения растяжимости
-Перед испытанием битум при наличии влаги обезвоживают осторожным нагреванием без
Метод определения растяжимости
-Перед испытанием битум при наличии влаги обезвоживают осторожным нагреванием без
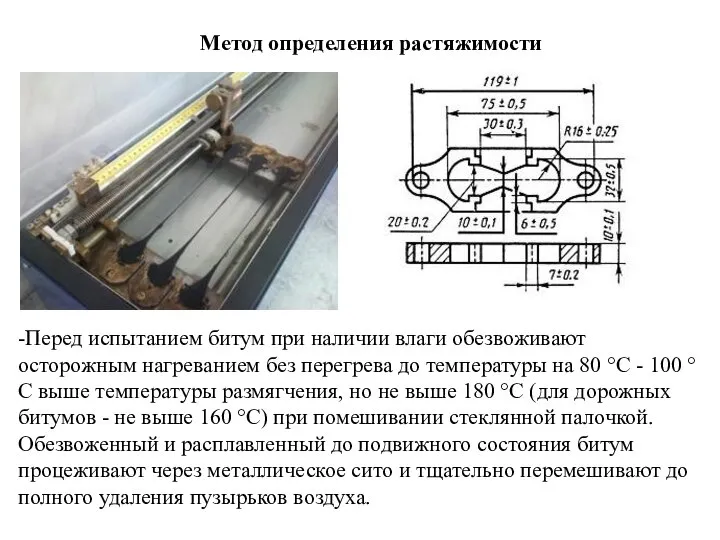
Слайд 54 -Полированную металлическую или стеклянную пластинку и внутренние боковые стенки вкладышей "восьмерки"
-Полированную металлическую или стеклянную пластинку и внутренние боковые стенки вкладышей "восьмерки"
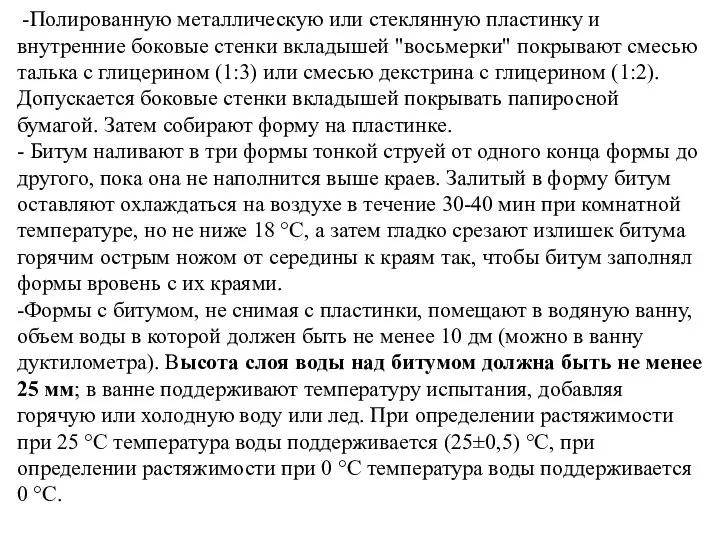
- Битум наливают в три формы тонкой струей от одного конца формы до другого, пока она не наполнится выше краев. Залитый в форму битум оставляют охлаждаться на воздухе в течение 30-40 мин при комнатной температуре, но не ниже 18 °С, а затем гладко срезают излишек битума горячим острым ножом от середины к краям так, чтобы битум заполнял формы вровень с их краями.
-Формы с битумом, не снимая с пластинки, помещают в водяную ванну, объем воды в которой должен быть не менее 10 дм (можно в ванну дуктилометра). Высота слоя воды над битумом должна быть не менее 25 мм; в ванне поддерживают температуру испытания, добавляя горячую или холодную воду или лед. При определении растяжимости при 25 °С температура воды поддерживается (25±0,5) °С, при определении растяжимости при 0 °С температура воды поддерживается 0 °C.
Слайд 55 -По истечении 1 ч формы с битумом вынимают из воды, снимают
-По истечении 1 ч формы с битумом вынимают из воды, снимают
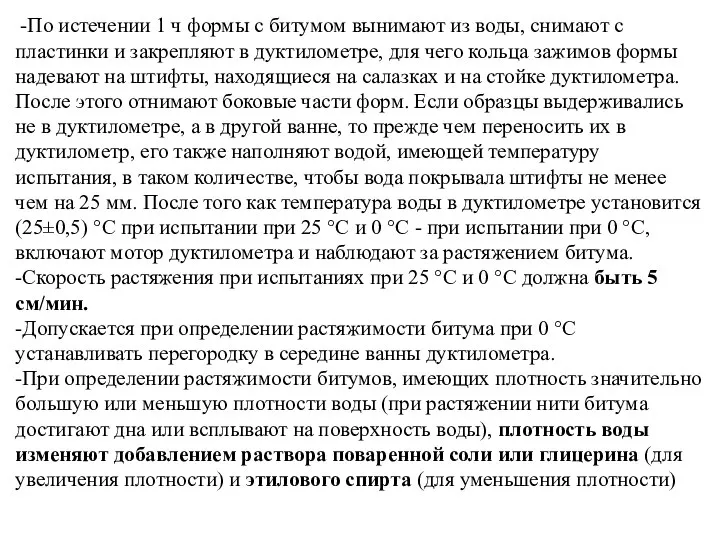
-Скорость растяжения при испытаниях при 25 °С и 0 °С должна быть 5 см/мин.
-Допускается при определении растяжимости битума при 0 °С устанавливать перегородку в середине ванны дуктилометра.
-При определении растяжимости битумов, имеющих плотность значительно большую или меньшую плотности воды (при растяжении нити битума достигают дна или всплывают на поверхность воды), плотность воды изменяют добавлением раствора поваренной соли или глицерина (для увеличения плотности) и этилового спирта (для уменьшения плотности)
Слайд 56Метод определения температуры вспышки
и воспламенения в открытом тигле
-Перед каждым испытанием тигель
Метод определения температуры вспышки
и воспламенения в открытом тигле
-Перед каждым испытанием тигель
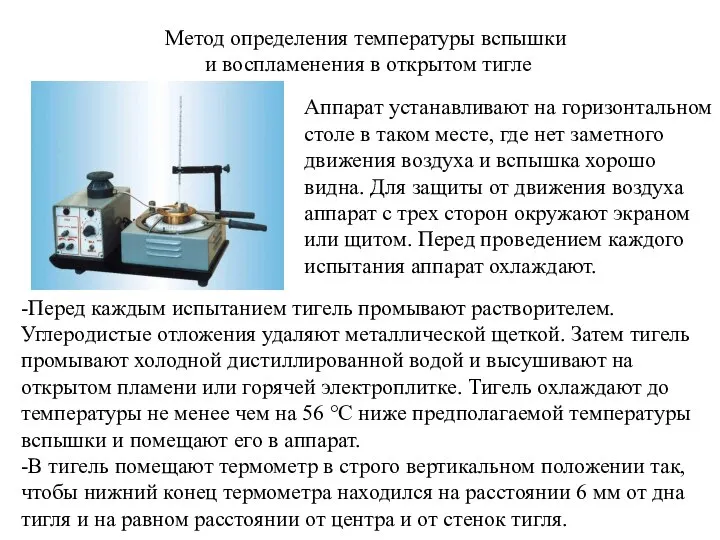
-В тигель помещают термометр в строго вертикальном положении так, чтобы нижний конец термометра находился на расстоянии 6 мм от дна тигля и на равном расстоянии от центра и от стенок тигля.
Аппарат устанавливают на горизонтальном столе в таком месте, где нет заметного движения воздуха и вспышка хорошо видна. Для защиты от движения воздуха аппарат с трех сторон окружают экраном или щитом. Перед проведением каждого испытания аппарат охлаждают.
Слайд 57 Проведение испытания
-Тигель заполняют нефтепродуктом так, чтобы верхний мениск точно совпадал с
Проведение испытания
-Тигель заполняют нефтепродуктом так, чтобы верхний мениск точно совпадал с
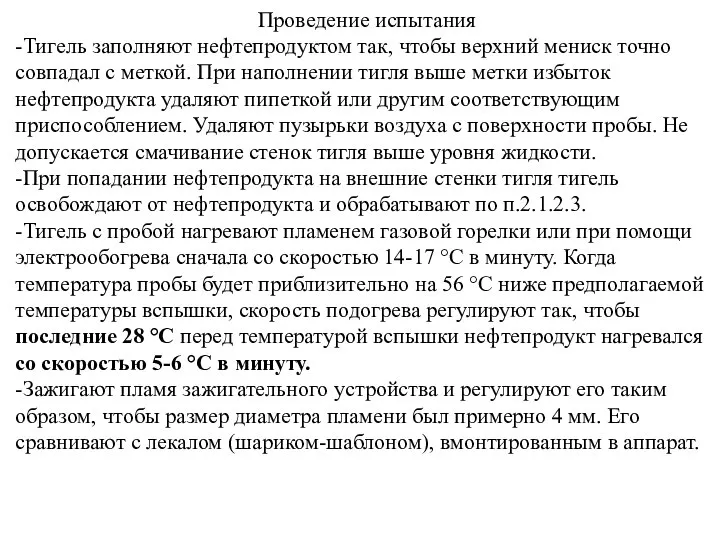
-При попадании нефтепродукта на внешние стенки тигля тигель освобождают от нефтепродукта и обрабатывают по п.2.1.2.3.
-Тигель с пробой нагревают пламенем газовой горелки или при помощи электрообогрева сначала со скоростью 14-17 °С в минуту. Когда температура пробы будет приблизительно на 56 °С ниже предполагаемой температуры вспышки, скорость подогрева регулируют так, чтобы последние 28 °С перед температурой вспышки нефтепродукт нагревался со скоростью 5-6 °С в минуту.
-Зажигают пламя зажигательного устройства и регулируют его таким образом, чтобы размер диаметра пламени был примерно 4 мм. Его сравнивают с лекалом (шариком-шаблоном), вмонтированным в аппарат.
Слайд 58-Начиная с температуры не менее чем на 28 °С ниже температуры вспышки,
-Начиная с температуры не менее чем на 28 °С ниже температуры вспышки,
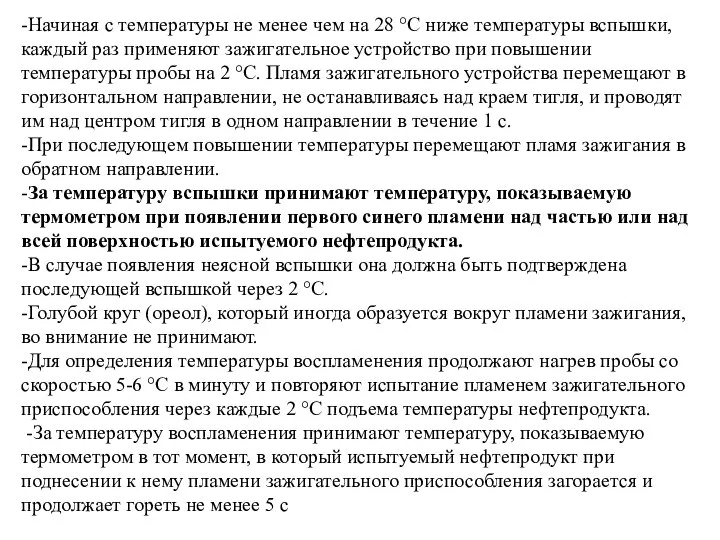
-При последующем повышении температуры перемещают пламя зажигания в обратном направлении.
-За температуру вспышки принимают температуру, показываемую термометром при появлении первого синего пламени над частью или над всей поверхностью испытуемого нефтепродукта.
-В случае появления неясной вспышки она должна быть подтверждена последующей вспышкой через 2 °С.
-Голубой круг (ореол), который иногда образуется вокруг пламени зажигания, во внимание не принимают.
-Для определения температуры воспламенения продолжают нагрев пробы со скоростью 5-6 °С в минуту и повторяют испытание пламенем зажигательного приспособления через каждые 2 °С подъема температуры нефтепродукта.
-За температуру воспламенения принимают температуру, показываемую термометром в тот момент, в который испытуемый нефтепродукт при поднесении к нему пламени зажигательного приспособления загорается и продолжает гореть не менее 5 с
Слайд 59Метод определения изменения массы после прогрева
-Перед испытанием пробу битума при необходимости обезвоживают
Метод определения изменения массы после прогрева
-Перед испытанием пробу битума при необходимости обезвоживают
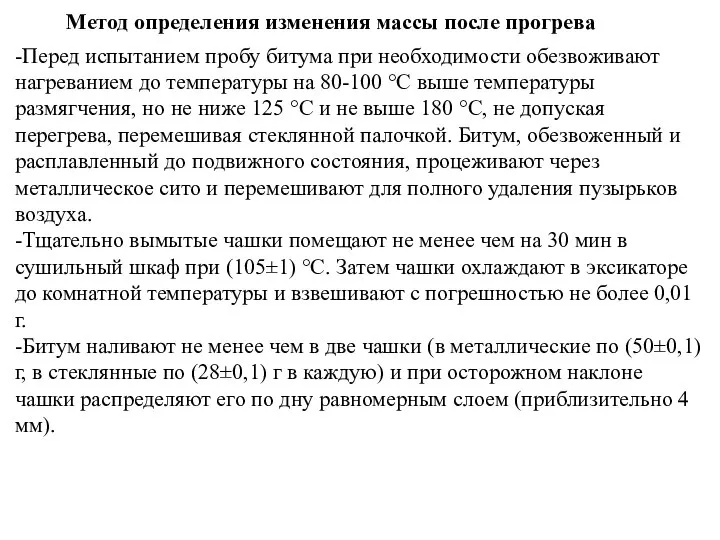
-Тщательно вымытые чашки помещают не менее чем на 30 мин в сушильный шкаф при (105±1) °С. Затем чашки охлаждают в эксикаторе до комнатной температуры и взвешивают с погрешностью не более 0,01 г.
-Битум наливают не менее чем в две чашки (в металлические по (50±0,1) г, в стеклянные по (28±0,1) г в каждую) и при осторожном наклоне чашки распределяют его по дну равномерным слоем (приблизительно 4 мм).
Слайд 60-После охлаждения битума до комнатной температуры в эксикаторе пробы взвешивают с погрешностью
-После охлаждения битума до комнатной температуры в эксикаторе пробы взвешивают с погрешностью
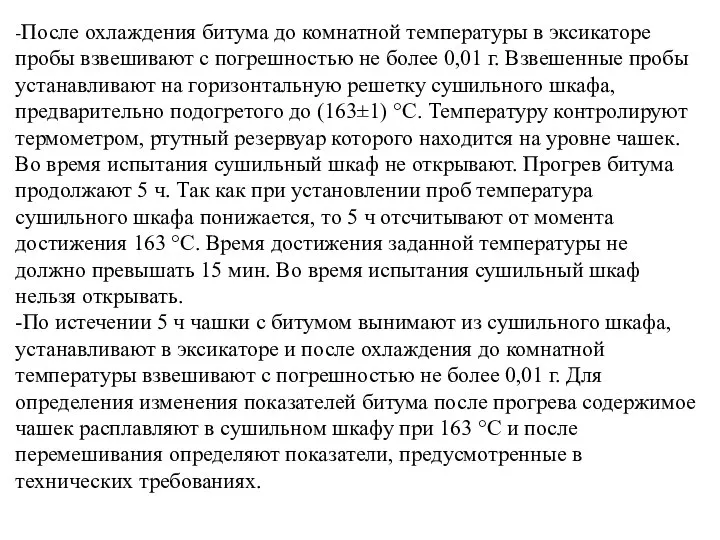
-По истечении 5 ч чашки с битумом вынимают из сушильного шкафа, устанавливают в эксикаторе и после охлаждения до комнатной температуры взвешивают с погрешностью не более 0,01 г. Для определения изменения показателей битума после прогрева содержимое чашек расплавляют в сушильном шкафу при 163 °С и после перемешивания определяют показатели, предусмотренные в технических требованиях.
Слайд 61По физико-химическим показателям битумы должны соответствовать требованиям и нормам
По физико-химическим показателям битумы должны соответствовать требованиям и нормам
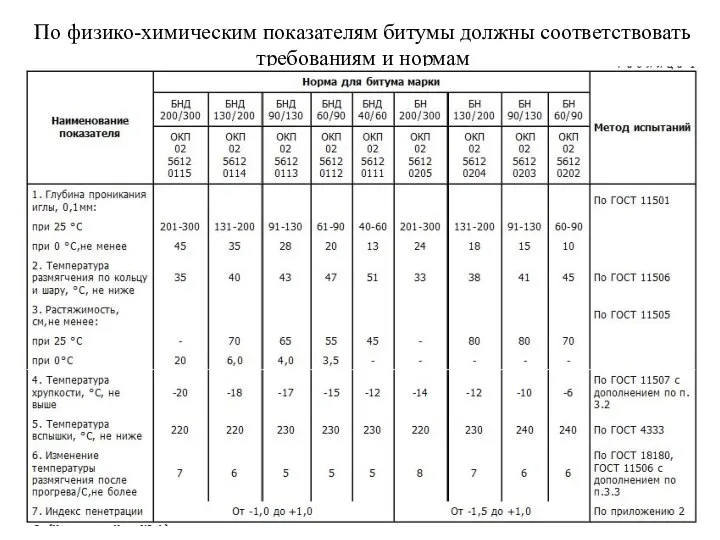
Слайд 62СХЕМА ЛАБОРАТОРНОГО КОНТРОЛЯ КАЧЕСТВА
БИТУМЫ НЕФТЯНЫЕ, ПБВ
СХЕМА ЛАБОРАТОРНОГО КОНТРОЛЯ КАЧЕСТВА
БИТУМЫ НЕФТЯНЫЕ, ПБВ
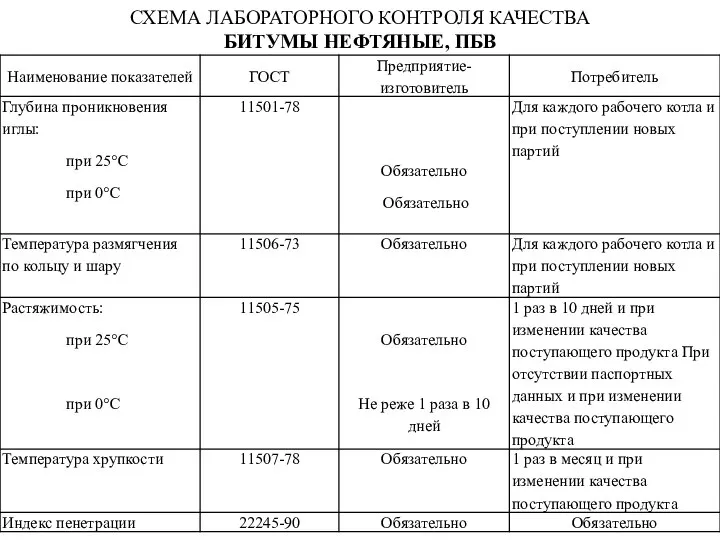
Слайд 64Приготовление бетонной смеси
-должно обеспечивать требуемый объем вовлеченного воздуха с учетом продолжительности
Приготовление бетонной смеси
-должно обеспечивать требуемый объем вовлеченного воздуха с учетом продолжительности
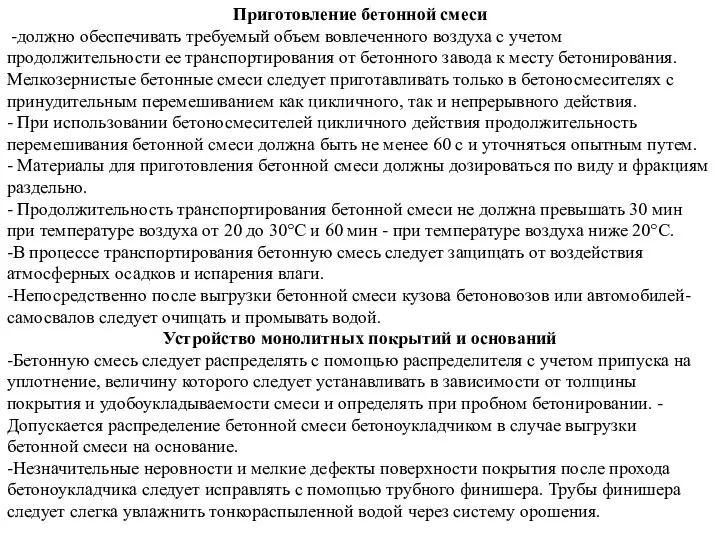
Мелкозернистые бетонные смеси следует приготавливать только в бетоносмесителях с принудительным перемешиванием как цикличного, так и непрерывного действия.
- При использовании бетоносмесителей цикличного действия продолжительность перемешивания бетонной смеси должна быть не менее 60 с и уточняться опытным путем.
- Материалы для приготовления бетонной смеси должны дозироваться по виду и фракциям раздельно.
- Продолжительность транспортирования бетонной смеси не должна превышать 30 мин при температуре воздуха от 20 до 30°С и 60 мин - при температуре воздуха ниже 20°С.
-В процессе транспортирования бетонную смесь следует защищать от воздействия атмосферных осадков и испарения влаги.
-Непосредственно после выгрузки бетонной смеси кузова бетоновозов или автомобилей-самосвалов следует очищать и промывать водой.
Устройство монолитных покрытий и оснований
-Бетонную смесь следует распределять с помощью распределителя с учетом припуска на уплотнение, величину которого следует устанавливать в зависимости от толщины покрытия и удобоукладываемости смеси и определять при пробном бетонировании. -Допускается распределение бетонной смеси бетоноукладчиком в случае выгрузки бетонной смеси на основание.
-Незначительные неровности и мелкие дефекты поверхности покрытия после прохода бетоноукладчика следует исправлять с помощью трубного финишера. Трубы финишера следует слегка увлажнить тонкораспыленной водой через систему орошения.
Слайд 65-Организация работ по устройству двухслойного покрытия должна обеспечивать ритмичную укладку смеси и
-Организация работ по устройству двухслойного покрытия должна обеспечивать ритмичную укладку смеси и
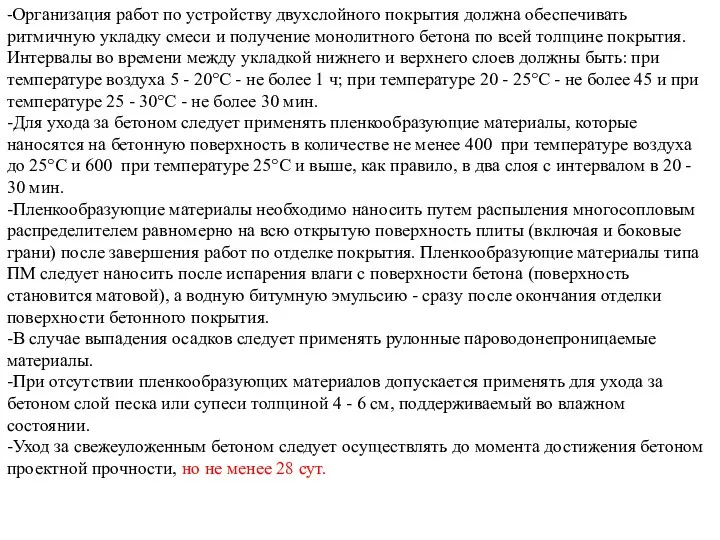
Интервалы во времени между укладкой нижнего и верхнего слоев должны быть: при температуре воздуха 5 - 20°С - не более 1 ч; при температуре 20 - 25°С - не более 45 и при температуре 25 - 30°С - не более 30 мин.
-Для ухода за бетоном следует применять пленкообразующие материалы, которые наносятся на бетонную поверхность в количестве не менее 400 при температуре воздуха до 25°С и 600 при температуре 25°С и выше, как правило, в два слоя с интервалом в 20 - 30 мин.
-Пленкообразующие материалы необходимо наносить путем распыления многосопловым распределителем равномерно на всю открытую поверхность плиты (включая и боковые грани) после завершения работ по отделке покрытия. Пленкообразующие материалы типа ПМ следует наносить после испарения влаги с поверхности бетона (поверхность становится матовой), а водную битумную эмульсию - сразу после окончания отделки поверхности бетонного покрытия.
-В случае выпадения осадков следует применять рулонные пароводонепроницаемые материалы.
-При отсутствии пленкообразующих материалов допускается применять для ухода за бетоном слой песка или супеси толщиной 4 - 6 см, поддерживаемый во влажном состоянии.
-Уход за свежеуложенным бетоном следует осуществлять до момента достижения бетоном проектной прочности, но не менее 28 сут.
Слайд 66-При максимальной суточной температуре воздуха 25°С и выше темные пленкообразующие материалы после
-При максимальной суточной температуре воздуха 25°С и выше темные пленкообразующие материалы после
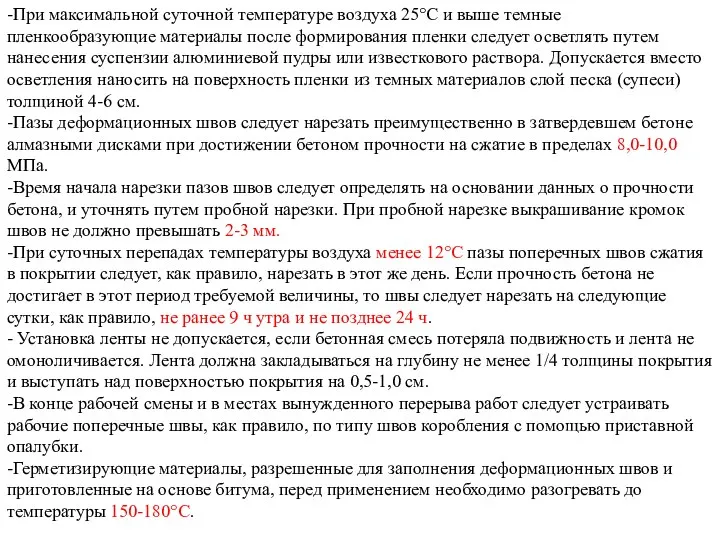
-Пазы деформационных швов следует нарезать преимущественно в затвердевшем бетоне алмазными дисками при достижении бетоном прочности на сжатие в пределах 8,0-10,0 МПа.
-Время начала нарезки пазов швов следует определять на основании данных о прочности бетона, и уточнять путем пробной нарезки. При пробной нарезке выкрашивание кромок швов не должно превышать 2-3 мм.
-При суточных перепадах температуры воздуха менее 12°С пазы поперечных швов сжатия в покрытии следует, как правило, нарезать в этот же день. Если прочность бетона не достигает в этот период требуемой величины, то швы следует нарезать на следующие сутки, как правило, не ранее 9 ч утра и не позднее 24 ч.
- Установка ленты не допускается, если бетонная смесь потеряла подвижность и лента не омоноличивается. Лента должна закладываться на глубину не менее 1/4 толщины покрытия и выступать над поверхностью покрытия на 0,5-1,0 см.
-В конце рабочей смены и в местах вынужденного перерыва работ следует устраивать рабочие поперечные швы, как правило, по типу швов коробления с помощью приставной опалубки.
-Герметизирующие материалы, разрешенные для заполнения деформационных швов и приготовленные на основе битума, перед применением необходимо разогревать до температуры 150-180°С.
Слайд 67Контроль качества работ
-При приготовлении цементобетонной смеси следует контролировать:
постоянно - соблюдение технологических режимов
Контроль качества работ
-При приготовлении цементобетонной смеси следует контролировать:
постоянно - соблюдение технологических режимов
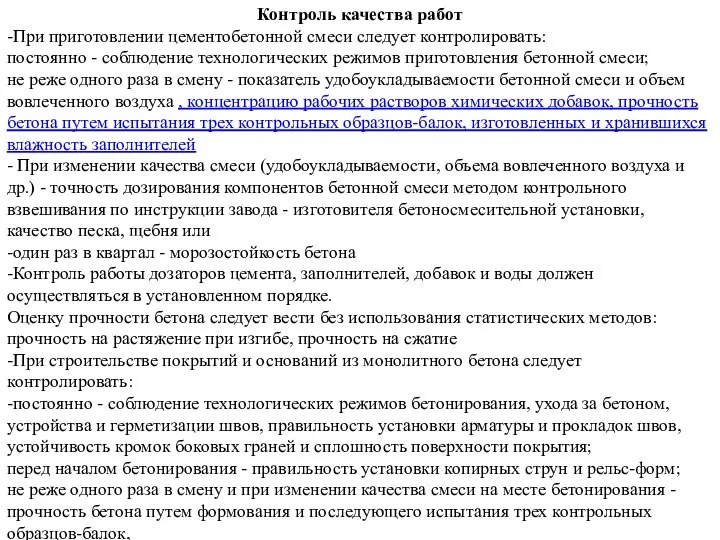
не реже одного раза в смену - показатель удобоукладываемости бетонной смеси и объем вовлеченного воздуха , концентрацию рабочих растворов химических добавок, прочность бетона путем испытания трех контрольных образцов-балок, изготовленных и хранившихся влажность заполнителей
- При изменении качества смеси (удобоукладываемости, объема вовлеченного воздуха и др.) - точность дозирования компонентов бетонной смеси методом контрольного взвешивания по инструкции завода - изготовителя бетоносмесительной установки, качество песка, щебня или
-один раз в квартал - морозостойкость бетона
-Контроль работы дозаторов цемента, заполнителей, добавок и воды должен осуществляться в установленном порядке.
Оценку прочности бетона следует вести без использования статистических методов: прочность на растяжение при изгибе, прочность на сжатие
-При строительстве покрытий и оснований из монолитного бетона следует контролировать:
-постоянно - соблюдение технологических режимов бетонирования, ухода за бетоном, устройства и герметизации швов, правильность установки арматуры и прокладок швов, устойчивость кромок боковых граней и сплошность поверхности покрытия;
перед началом бетонирования - правильность установки копирных струн и рельс-форм;
не реже одного раза в смену и при изменении качества смеси на месте бетонирования - прочность бетона путем формования и последующего испытания трех контрольных образцов-балок,
Слайд 68удобоукладываемость и объем вовлеченного воздуха, а также качество работ по уходу за
удобоукладываемость и объем вовлеченного воздуха, а также качество работ по уходу за
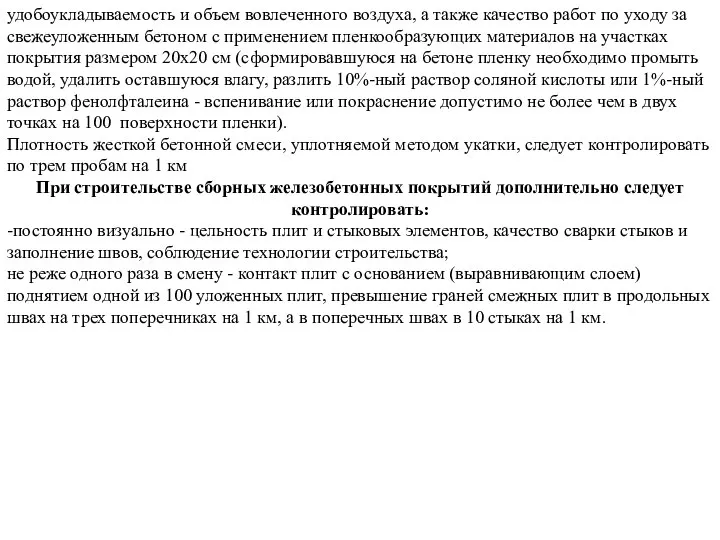
Плотность жесткой бетонной смеси, уплотняемой методом укатки, следует контролировать по трем пробам на 1 км
При строительстве сборных железобетонных покрытий дополнительно следует контролировать:
-постоянно визуально - цельность плит и стыковых элементов, качество сварки стыков и заполнение швов, соблюдение технологии строительства;
не реже одного раза в смену - контакт плит с основанием (выравнивающим слоем) поднятием одной из 100 уложенных плит, превышение граней смежных плит в продольных швах на трех поперечниках на 1 км, а в поперечных швах в 10 стыках на 1 км.
Слайд 69 Бетон - искусственный каменный материал, получаемый из рационально подобранной смеси вяжущего вещества
Бетон - искусственный каменный материал, получаемый из рационально подобранной смеси вяжущего вещества
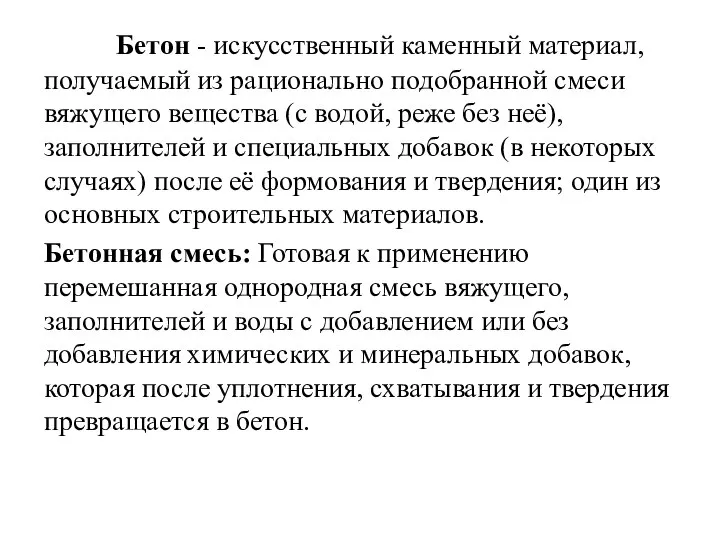
Бетонная смесь: Готовая к применению перемешанная однородная смесь вяжущего, заполнителей и воды с добавлением или без добавления химических и минеральных добавок, которая после уплотнения, схватывания и твердения превращается в бетон.
Слайд 70 Классификация бетонов
Бетоны классифицируются по следующим признакам:
- основное назначение;
- стойкость к видам
Классификация бетонов Бетоны классифицируются по следующим признакам: - основное назначение; - стойкость к видам
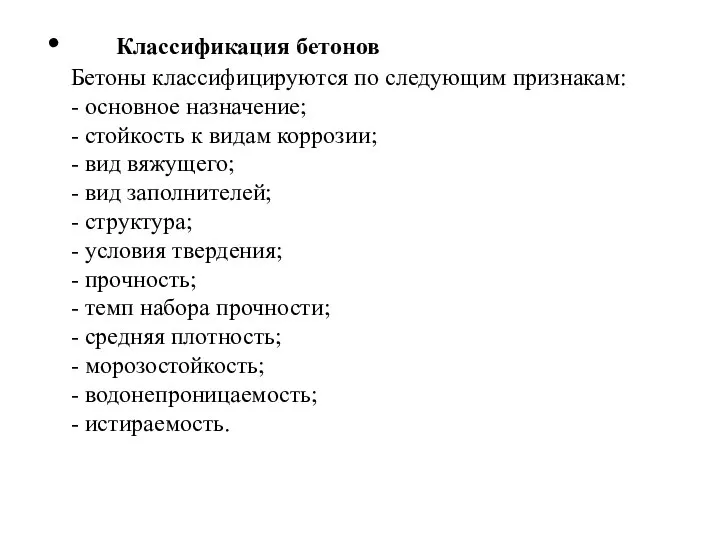
Слайд 71В зависимости от основного назначения бетоны подразделяют на:
- конструкционные;
- специальные (например, теплоизоляционные,
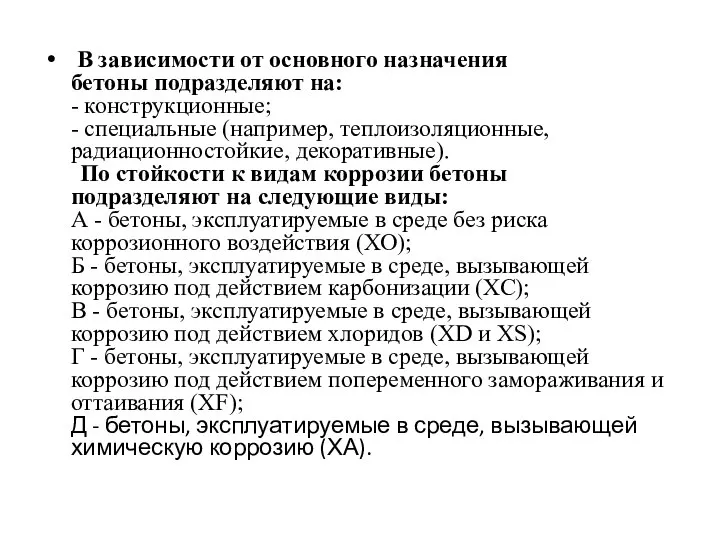
Слайд 72По виду вяжущего бетоны подразделяют на:
- цементные;
- известковые;
- шлаковые;
- гипсовые;
- специальные (например,
По виду вяжущего бетоны подразделяют на: - цементные; - известковые; - шлаковые; - гипсовые; - специальные (например,
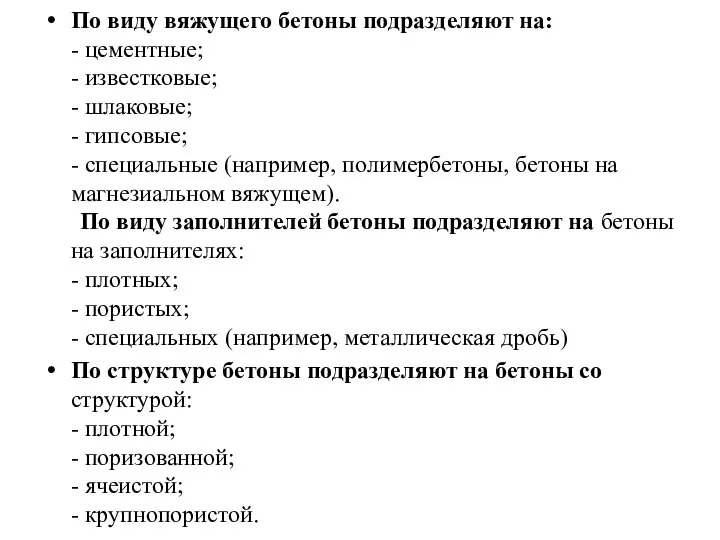
По структуре бетоны подразделяют на бетоны со структурой: - плотной; - поризованной; - ячеистой; - крупнопористой.
Слайд 73По условиям твердения бетоны подразделяют на твердеющие:
- в естественных условиях;
- в условиях
По условиям твердения бетоны подразделяют на твердеющие: - в естественных условиях; - в условиях
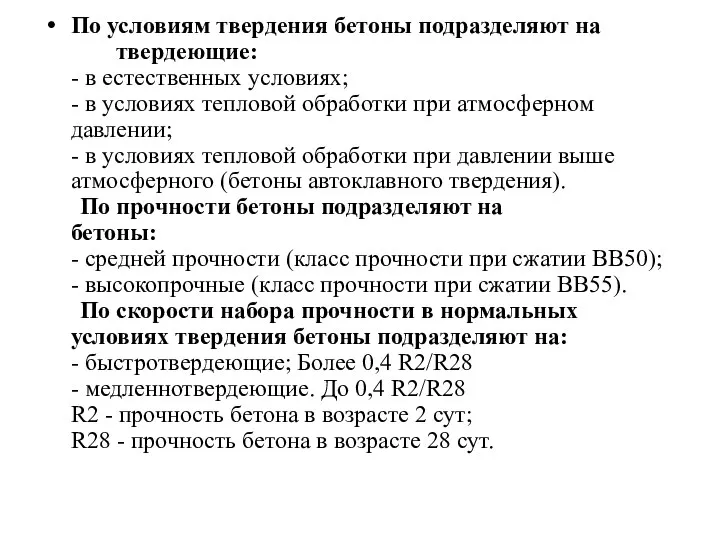
Слайд 74По средней плотности бетоны подразделяют на:
- особо легкие (марки по средней плотности
По средней плотности бетоны подразделяют на: - особо легкие (марки по средней плотности
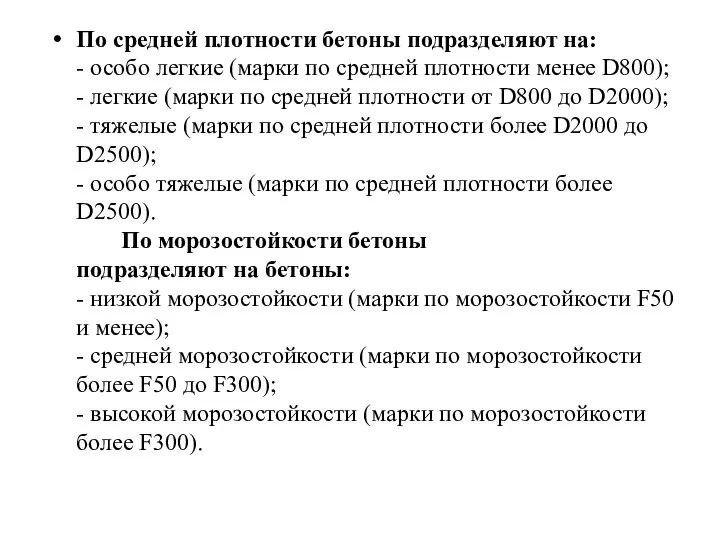
Слайд 75 По водонепроницаемости бетоны подразделяют на бетоны:
- низкой водонепроницаемости (марки по водонепроницаемости
По водонепроницаемости бетоны подразделяют на бетоны: - низкой водонепроницаемости (марки по водонепроницаемости
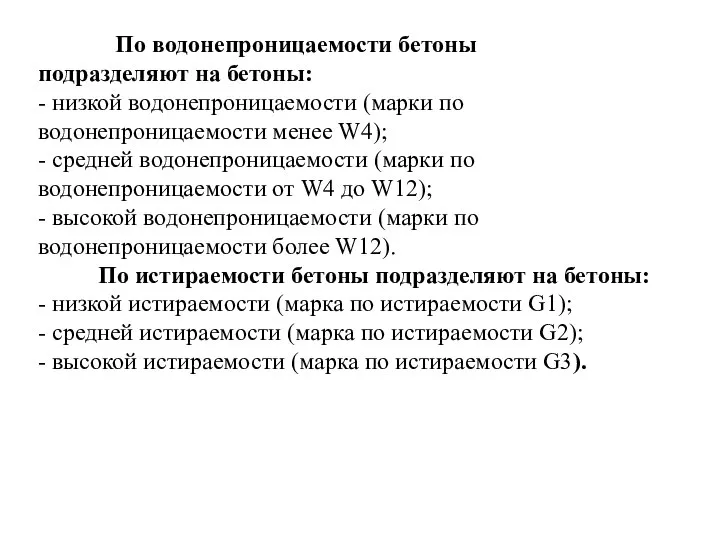
Слайд 76СМЕСИ БЕТОННЫЕ
Классификация
По типу бетона бетонные смеси подразделяют на:
- бетонные
СМЕСИ БЕТОННЫЕ
Классификация
По типу бетона бетонные смеси подразделяют на:
- бетонные
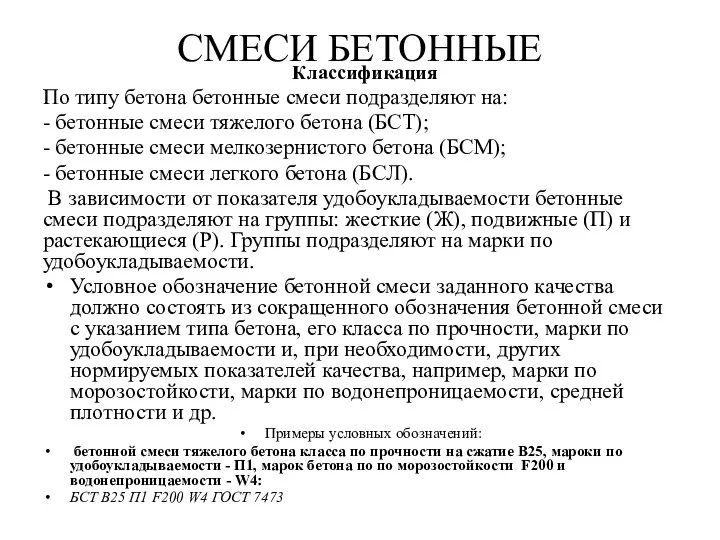
- бетонные смеси мелкозернистого бетона (БСМ);
- бетонные смеси легкого бетона (БСЛ).
В зависимости от показателя удобоукладываемости бетонные смеси подразделяют на группы: жесткие (Ж), подвижные (П) и растекающиеся (Р). Группы подразделяют на марки по удобоукладываемости.
Условное обозначение бетонной смеси заданного качества должно состоять из сокращенного обозначения бетонной смеси с указанием типа бетона, его класса по прочности, марки по удобоукладываемости и, при необходимости, других нормируемых показателей качества, например, марки по морозостойкости, марки по водонепроницаемости, средней плотности и др.
Примеры условных обозначений:
бетонной смеси тяжелого бетона класса по прочности на сжатие В25, мароки по удобоукладываемости - П1, марок бетона по по морозостойкости F200 и водонепроницаемости - W4:
БСТ В25 П1 F200 W4 ГОСТ 7473
Слайд 77Бетонные смеси характеризуют следующими технологическими показателями качества:
— удобоукладываемость;
— средняя плотность;
Бетонные смеси характеризуют следующими технологическими показателями качества:
— удобоукладываемость;
— средняя плотность;
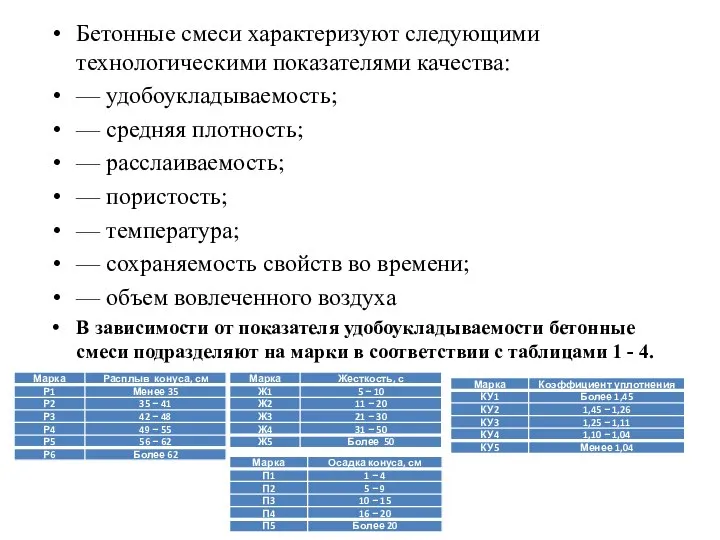
— расслаиваемость;
— пористость;
— температура;
— сохраняемость свойств во времени;
— объем вовлеченного воздуха
В зависимости от показателя удобоукладываемости бетонные смеси подразделяют на марки в соответствии с таблицами 1 - 4.
Слайд 78Допустимые отклонения заданных значений удобоукладываемости
Допустимые отклонения заданных значений удобоукладываемости
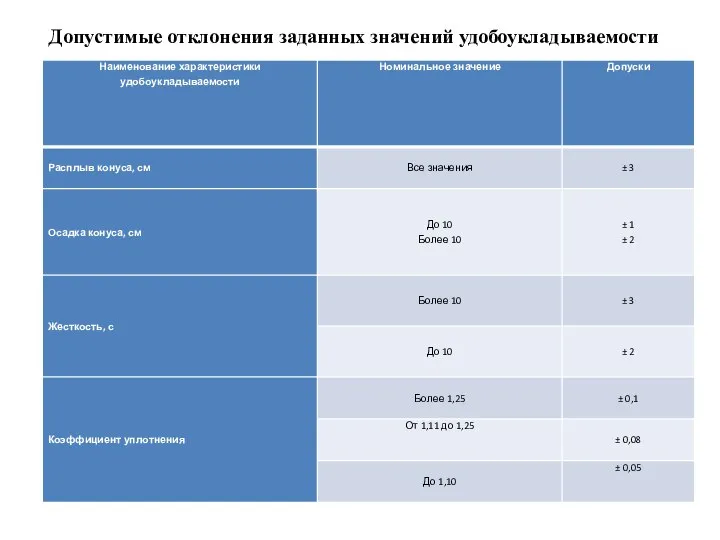
Слайд 79При поставке бетонной смеси допустимое отклонение заданных значений показателей: средней плотности, расслаиваемости,
При поставке бетонной смеси допустимое отклонение заданных значений показателей: средней плотности, расслаиваемости,
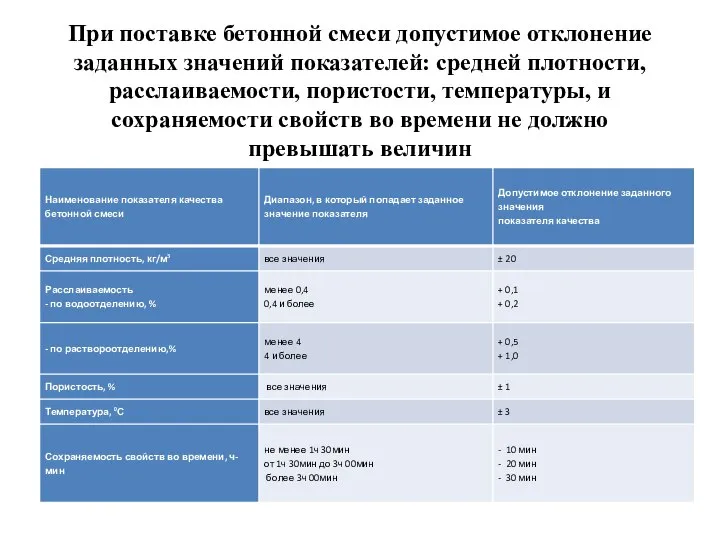
Слайд 80Бетонные смеси должны быть приняты по качеству и количеству техническим контролем производителя.
Бетонные смеси должны быть приняты по качеству и количеству техническим контролем производителя.
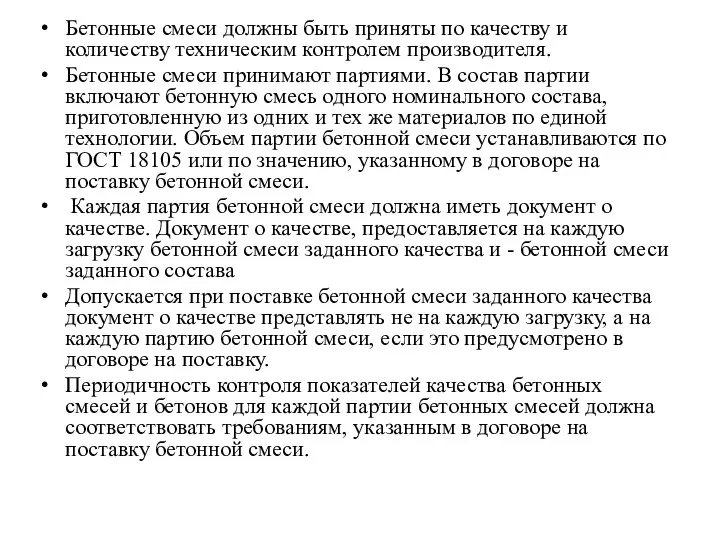
Бетонные смеси принимают партиями. В состав партии включают бетонную смесь одного номинального состава, приготовленную из одних и тех же материалов по единой технологии. Объем партии бетонной смеси устанавливаются по ГОСТ 18105 или по значению, указанному в договоре на поставку бетонной смеси.
Каждая партия бетонной смеси должна иметь документ о качестве. Документ о качестве, предоставляется на каждую загрузку бетонной смеси заданного качества и - бетонной смеси заданного состава
Допускается при поставке бетонной смеси заданного качества документ о качестве представлять не на каждую загрузку, а на каждую партию бетонной смеси, если это предусмотрено в договоре на поставку.
Периодичность контроля показателей качества бетонных смесей и бетонов для каждой партии бетонных смесей должна соответствовать требованиям, указанным в договоре на поставку бетонной смеси.
Слайд 81Заданные технологические показатели качества бетонной смеси производят у производителя через 15 мин
Заданные технологические показатели качества бетонной смеси производят у производителя через 15 мин
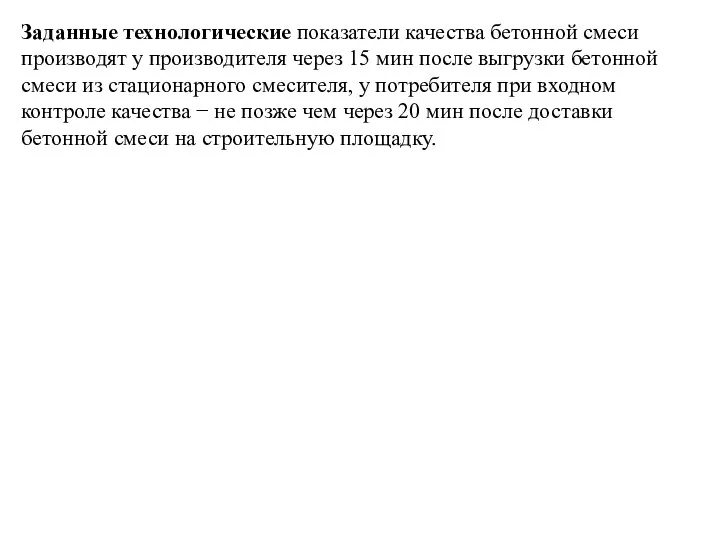
Слайд 82МЕТОДЫ КОНТРОЛЯ
Пробы бетонной смеси для испытания при производственном контроле следует отбирать:
-
МЕТОДЫ КОНТРОЛЯ
Пробы бетонной смеси для испытания при производственном контроле следует отбирать:
-
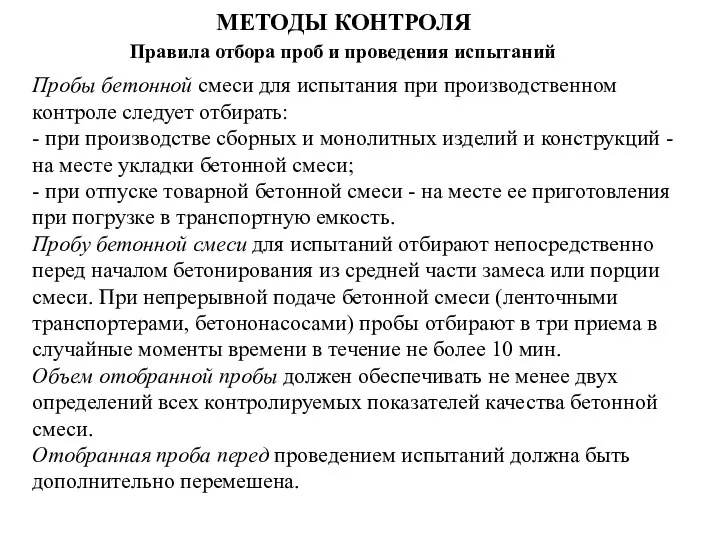
- при отпуске товарной бетонной смеси - на месте ее приготовления при погрузке в транспортную емкость.
Пробу бетонной смеси для испытаний отбирают непосредственно перед началом бетонирования из средней части замеса или порции смеси. При непрерывной подаче бетонной смеси (ленточными транспортерами, бетононасосами) пробы отбирают в три приема в случайные моменты времени в течение не более 10 мин.
Объем отобранной пробы должен обеспечивать не менее двух определений всех контролируемых показателей качества бетонной смеси.
Отобранная проба перед проведением испытаний должна быть дополнительно перемешена.
Правила отбора проб и проведения испытаний
Слайд 83Бетонные смеси, содержащие воздухововлекающие, газообразующие и пенообразующие добавки, а также предварительно разогретые
Бетонные смеси, содержащие воздухововлекающие, газообразующие и пенообразующие добавки, а также предварительно разогретые
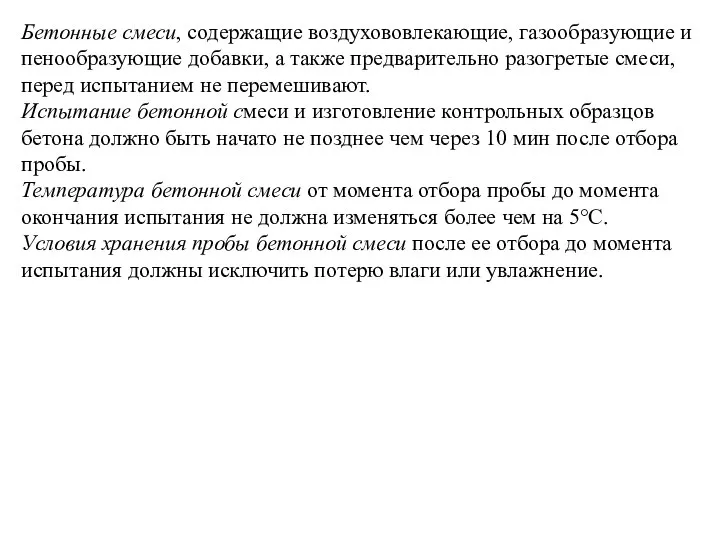
Испытание бетонной смеси и изготовление контрольных образцов бетона должно быть начато не позднее чем через 10 мин после отбора пробы.
Температура бетонной смеси от момента отбора пробы до момента окончания испытания не должна изменяться более чем на 5°C.
Условия хранения пробы бетонной смеси после ее отбора до момента испытания должны исключить потерю влаги или увлажнение.
Слайд 84Определение удобоукладываемости бетонной смеси
Удобоукладываемость бетонной смеси оценивают показателями подвижности или жесткости.
Определение подвижности
Определение удобоукладываемости бетонной смеси
Удобоукладываемость бетонной смеси оценивают показателями подвижности или жесткости.
Определение подвижности
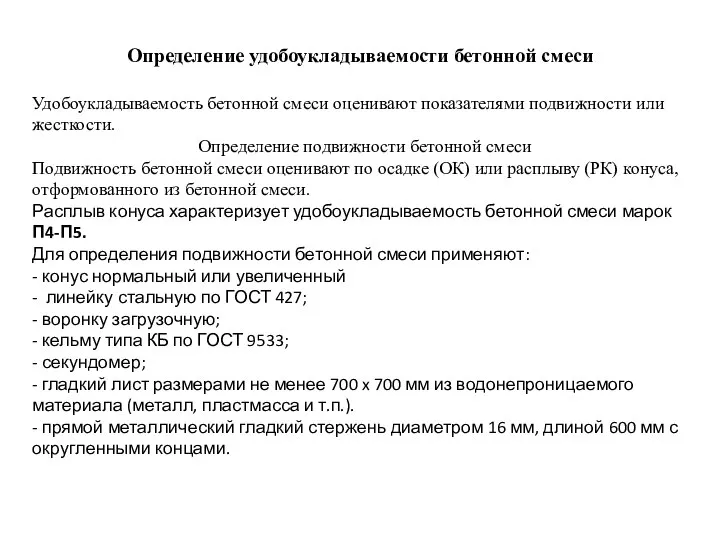
Подвижность бетонной смеси оценивают по осадке (ОК) или расплыву (РК) конуса, отформованного из бетонной смеси.
Расплыв конуса характеризует удобоукладываемость бетонной смеси марок П4-П5.
Для определения подвижности бетонной смеси применяют:
- конус нормальный или увеличенный
- линейку стальную по ГОСТ 427;
- воронку загрузочную;
- кельму типа КБ по ГОСТ 9533;
- секундомер;
- гладкий лист размерами не менее 700 x 700 мм из водонепроницаемого материала (металл, пластмасса и т.п.).
- прямой металлический гладкий стержень диаметром 16 мм, длиной 600 мм с округленными концами.
Слайд 85Конус для определения подвижности бетона
Конус для определения подвижности бетона
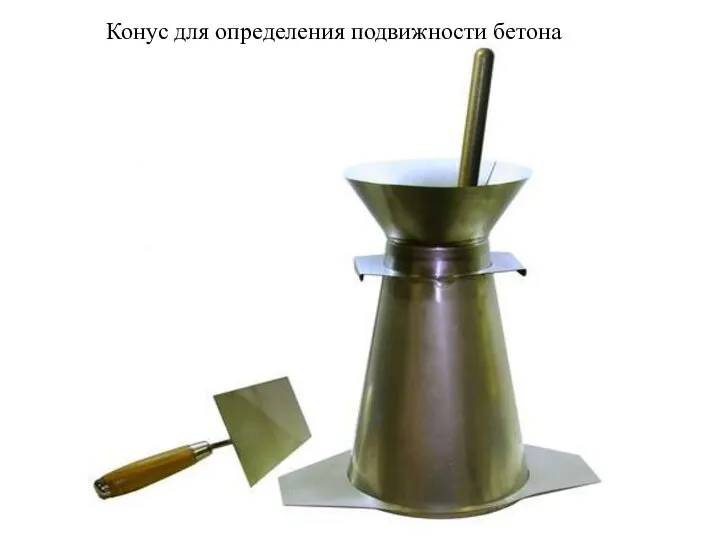
Слайд 86Для определения подвижности бетонной смеси с зернами заполнителя наибольшей крупностью до 40
Для определения подвижности бетонной смеси с зернами заполнителя наибольшей крупностью до 40
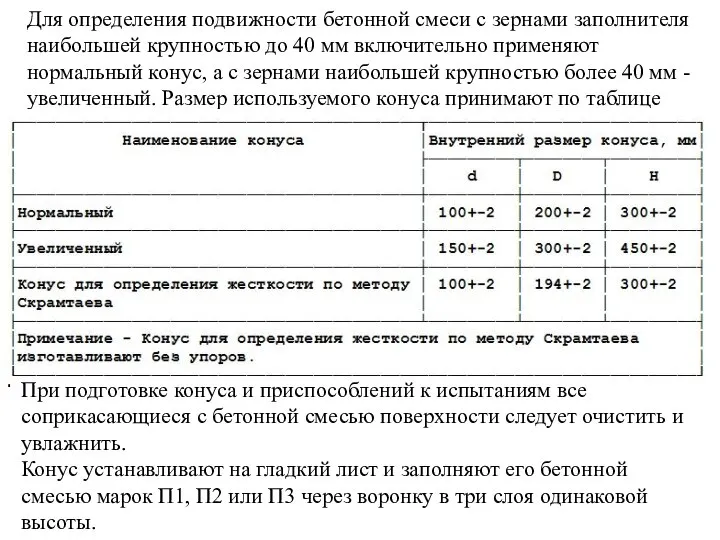
При подготовке конуса и приспособлений к испытаниям все соприкасающиеся с бетонной смесью поверхности следует очистить и увлажнить.
Конус устанавливают на гладкий лист и заполняют его бетонной смесью марок П1, П2 или П3 через воронку в три слоя одинаковой высоты.
Слайд 87Каждый слой на его высоту уплотняют штыкованием металлическим стержнем: в нормальном конусе
Каждый слой на его высоту уплотняют штыкованием металлическим стержнем: в нормальном конусе
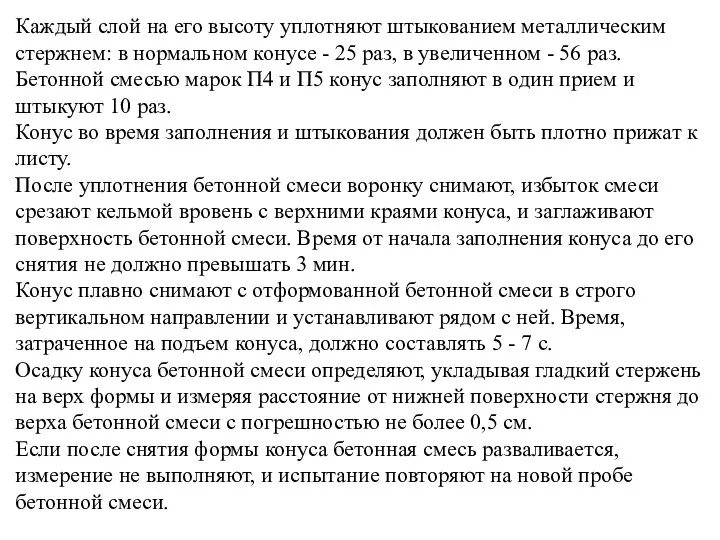
Бетонной смесью марок П4 и П5 конус заполняют в один прием и штыкуют 10 раз.
Конус во время заполнения и штыкования должен быть плотно прижат к листу.
После уплотнения бетонной смеси воронку снимают, избыток смеси срезают кельмой вровень с верхними краями конуса, и заглаживают поверхность бетонной смеси. Время от начала заполнения конуса до его снятия не должно превышать 3 мин.
Конус плавно снимают с отформованной бетонной смеси в строго вертикальном направлении и устанавливают рядом с ней. Время, затраченное на подъем конуса, должно составлять 5 - 7 с.
Осадку конуса бетонной смеси определяют, укладывая гладкий стержень на верх формы и измеряя расстояние от нижней поверхности стержня до верха бетонной смеси с погрешностью не более 0,5 см.
Если после снятия формы конуса бетонная смесь разваливается, измерение не выполняют, и испытание повторяют на новой пробе бетонной смеси.
Слайд 88Осадку конуса бетонной смеси, определенную в увеличенном конусе, приводят к осадке нормального
Осадку конуса бетонной смеси, определенную в увеличенном конусе, приводят к осадке нормального
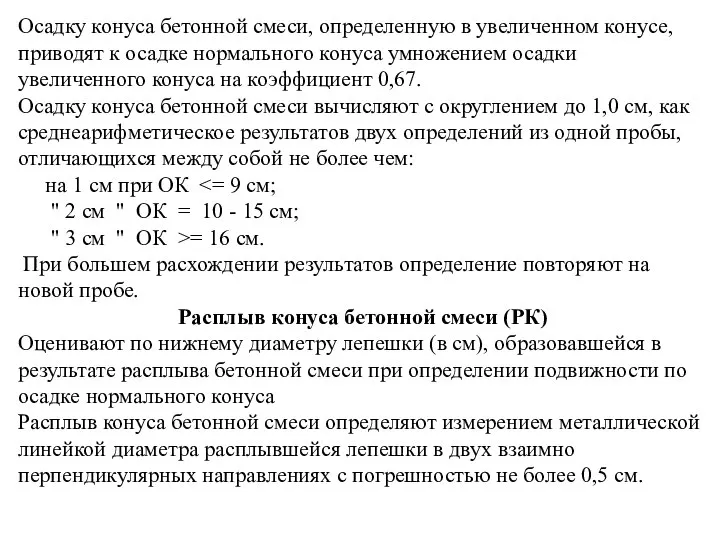
Осадку конуса бетонной смеси вычисляют с округлением до 1,0 см, как среднеарифметическое результатов двух определений из одной пробы, отличающихся между собой не более чем:
на 1 см при ОК <= 9 см;
" 2 см " ОК = 10 - 15 см;
" 3 см " ОК >= 16 см.
При большем расхождении результатов определение повторяют на новой пробе.
Расплыв конуса бетонной смеси (РК)
Оценивают по нижнему диаметру лепешки (в см), образовавшейся в результате расплыва бетонной смеси при определении подвижности по осадке нормального конуса
Расплыв конуса бетонной смеси определяют измерением металлической линейкой диаметра расплывшейся лепешки в двух взаимно перпендикулярных направлениях с погрешностью не более 0,5 см.
Слайд 89Правила обработки результатов испытаний
Осадку и расплыв конуса бетонной смеси определяют дважды. Общее
Правила обработки результатов испытаний
Осадку и расплыв конуса бетонной смеси определяют дважды. Общее
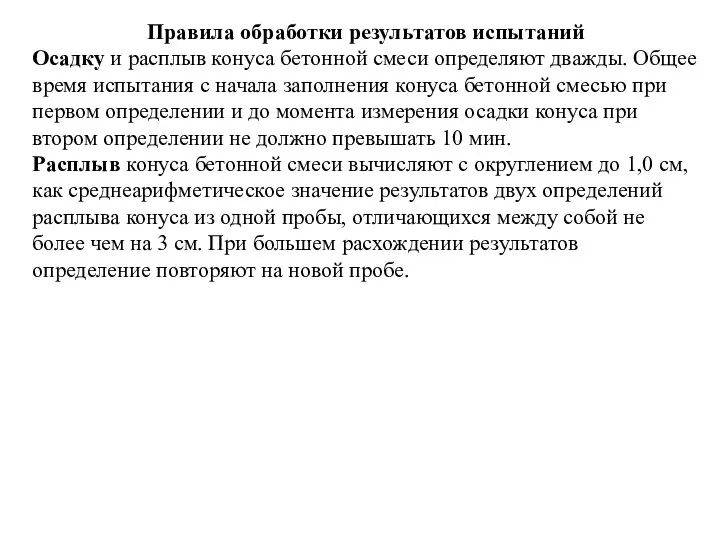
Расплыв конуса бетонной смеси вычисляют с округлением до 1,0 см, как среднеарифметическое значение результатов двух определений расплыва конуса из одной пробы, отличающихся между собой не более чем на 3 см. При большем расхождении результатов определение повторяют на новой пробе.
Слайд 90Определение жесткости бетонной смеси
Жесткость бетонной смеси характеризуют временем вибрации в секундах, необходимым
Определение жесткости бетонной смеси
Жесткость бетонной смеси характеризуют временем вибрации в секундах, необходимым
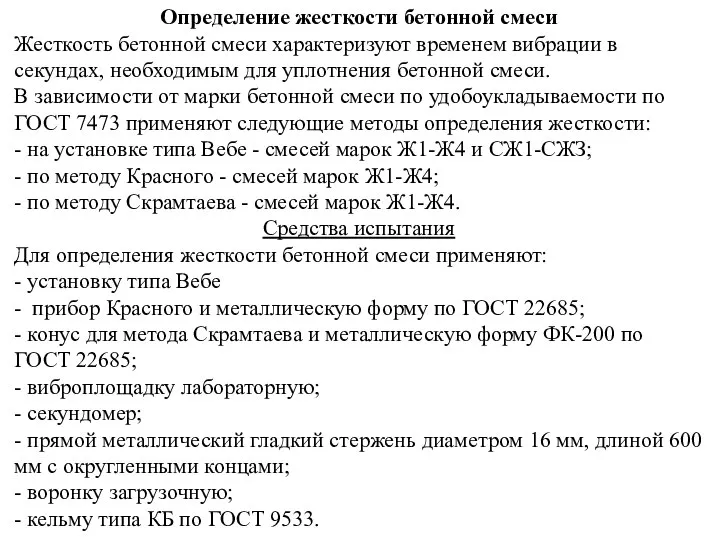
В зависимости от марки бетонной смеси по удобоукладываемости по ГОСТ 7473 применяют следующие методы определения жесткости:
- на установке типа Вебе - смесей марок Ж1-Ж4 и СЖ1-СЖЗ;
- по методу Красного - смесей марок Ж1-Ж4;
- по методу Скрамтаева - смесей марок Ж1-Ж4.
Средства испытания
Для определения жесткости бетонной смеси применяют:
- установку типа Вебе
- прибор Красного и металлическую форму по ГОСТ 22685;
- конус для метода Скрамтаева и металлическую форму ФК-200 по ГОСТ 22685;
- виброплощадку лабораторную;
- секундомер;
- прямой металлический гладкий стержень диаметром 16 мм, длиной 600 мм с округленными концами;
- воронку загрузочную;
- кельму типа КБ по ГОСТ 9533.
Слайд 91Установку типа Вебе
Прибор Красного
Конус Скрамтаева
Установку типа Вебе
Прибор Красного
Конус Скрамтаева
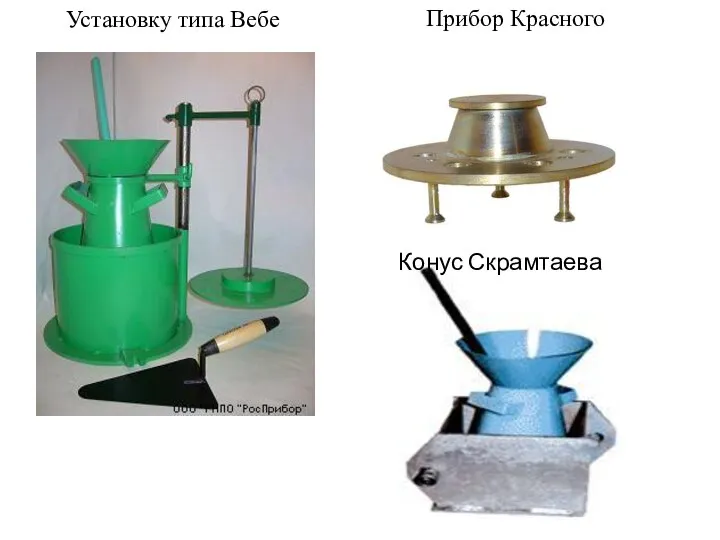
Слайд 92Определение жесткости бетонной смеси на установке типа Вебе
Установку собирают и закрепляют на
Определение жесткости бетонной смеси на установке типа Вебе
Установку собирают и закрепляют на
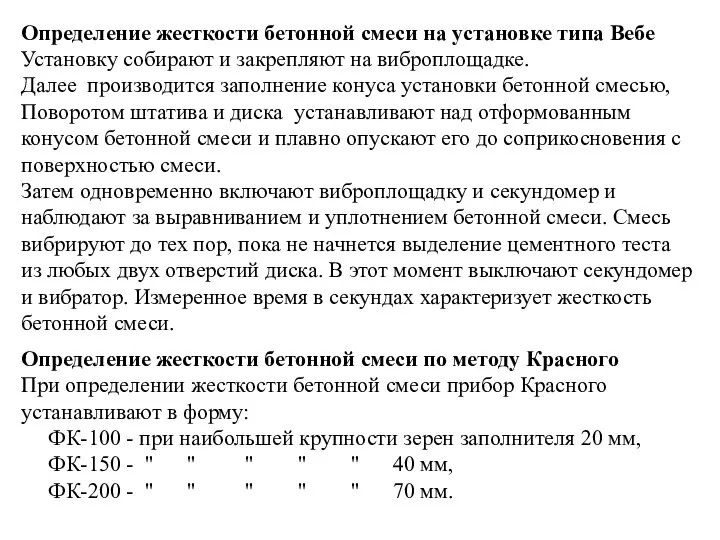
Далее производится заполнение конуса установки бетонной смесью, Поворотом штатива и диска устанавливают над отформованным конусом бетонной смеси и плавно опускают его до соприкосновения с поверхностью смеси.
Затем одновременно включают виброплощадку и секундомер и наблюдают за выравниванием и уплотнением бетонной смеси. Смесь вибрируют до тех пор, пока не начнется выделение цементного теста из любых двух отверстий диска. В этот момент выключают секундомер и вибратор. Измеренное время в секундах характеризует жесткость бетонной смеси.
Определение жесткости бетонной смеси по методу Красного
При определении жесткости бетонной смеси прибор Красного устанавливают в форму:
ФК-100 - при наибольшей крупности зерен заполнителя 20 мм,
ФК-150 - " " " " " 40 мм,
ФК-200 - " " " " " 70 мм.
Слайд 93Возможно применение цилиндрических форм ФЦ диаметром, соответствующим размеру ребра формы куба.
Установленную на
Возможно применение цилиндрических форм ФЦ диаметром, соответствующим размеру ребра формы куба.
Установленную на
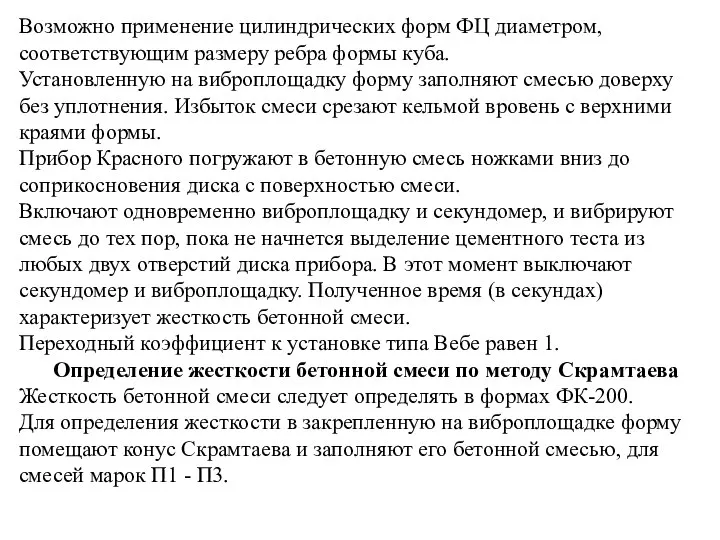
Прибор Красного погружают в бетонную смесь ножками вниз до соприкосновения диска с поверхностью смеси.
Включают одновременно виброплощадку и секундомер, и вибрируют смесь до тех пор, пока не начнется выделение цементного теста из любых двух отверстий диска прибора. В этот момент выключают секундомер и виброплощадку. Полученное время (в секундах) характеризует жесткость бетонной смеси.
Переходный коэффициент к установке типа Вебе равен 1.
Определение жесткости бетонной смеси по методу Скрамтаева
Жесткость бетонной смеси следует определять в формах ФК-200.
Для определения жесткости в закрепленную на виброплощадке форму помещают конус Скрамтаева и заполняют его бетонной смесью, для смесей марок П1 - П3.
Слайд 94Затем конус осторожно снимают, и включают одновременно виброплощадку и секундомер. Вибрирование осуществляют
Затем конус осторожно снимают, и включают одновременно виброплощадку и секундомер. Вибрирование осуществляют

Время (в секундах), необходимое для выравнивания поверхности бетонной смеси в форме, характеризует жесткость смеси.
Переходный коэффициент от метода Скрамтаева к методу определения жесткости на установке типа Вебе принимают равным 0,7.
Жесткость бетонной смеси определяют дважды. Общее время испытания с начала заполнения формы при первом определении и до окончания вибрирования при втором определении не должно превышать 10 мин.
Жесткость бетонной смеси вычисляют с округлением до 1 с, как среднеарифметическое значение результатов двух определений жесткости из одной пробы смеси, отличающихся между собой не более чем на 20% среднего значения. При большем расхождении результатов определение повторяют на новой пробе.
Слайд 95Определение средней плотности бетонной смеси
Среднюю плотность бетонной смеси характеризуют отношением массы уплотненной
Определение средней плотности бетонной смеси
Среднюю плотность бетонной смеси характеризуют отношением массы уплотненной
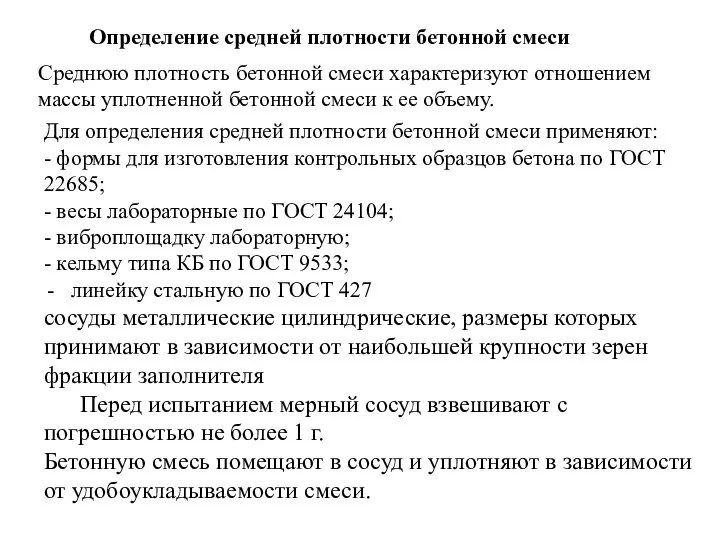
Для определения средней плотности бетонной смеси применяют:
- формы для изготовления контрольных образцов бетона по ГОСТ 22685;
- весы лабораторные по ГОСТ 24104;
- виброплощадку лабораторную;
- кельму типа КБ по ГОСТ 9533;
линейку стальную по ГОСТ 427
сосуды металлические цилиндрические, размеры которых принимают в зависимости от наибольшей крупности зерен фракции заполнителя
Перед испытанием мерный сосуд взвешивают с погрешностью не более 1 г.
Бетонную смесь помещают в сосуд и уплотняют в зависимости от удобоукладываемости смеси.
Слайд 96После уплотнения избыток смеси срезают стальной линейкой, и поверхность тщательно выравнивают вровень
После уплотнения избыток смеси срезают стальной линейкой, и поверхность тщательно выравнивают вровень
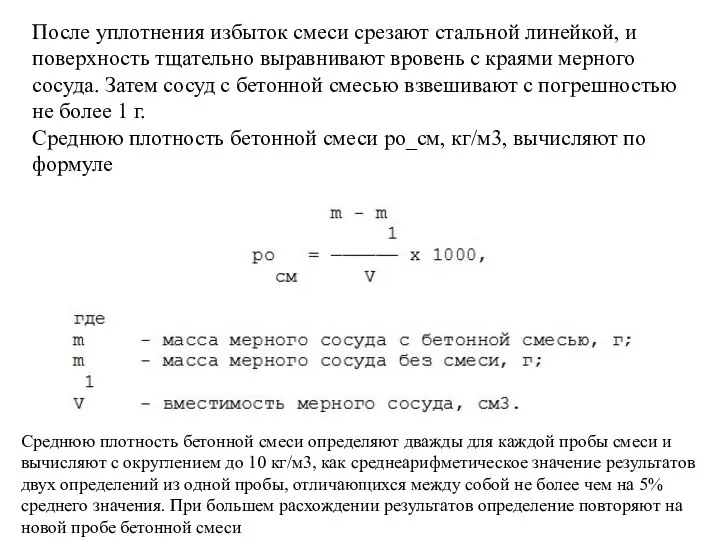
Среднюю плотность бетонной смеси ро_см, кг/м3, вычисляют по формуле
Среднюю плотность бетонной смеси определяют дважды для каждой пробы смеси и вычисляют с округлением до 10 кг/м3, как среднеарифметическое значение результатов двух определений из одной пробы, отличающихся между собой не более чем на 5% среднего значения. При большем расхождении результатов определение повторяют на новой пробе бетонной смеси
Слайд 97 Определение пористости бетонной смеси
Пористость бетонной смеси оценивают следующими показателями: объемом воздуха
Определение пористости бетонной смеси
Пористость бетонной смеси оценивают следующими показателями: объемом воздуха
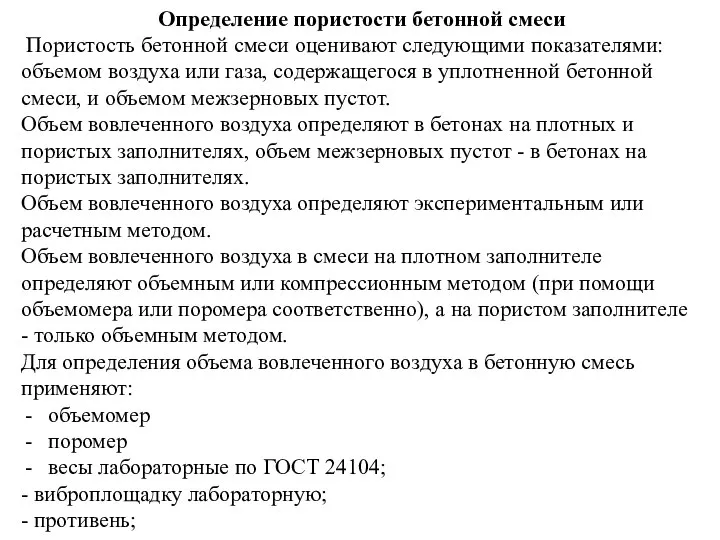
Объем вовлеченного воздуха определяют в бетонах на плотных и пористых заполнителях, объем межзерновых пустот - в бетонах на пористых заполнителях.
Объем вовлеченного воздуха определяют экспериментальным или расчетным методом.
Объем вовлеченного воздуха в смеси на плотном заполнителе определяют объемным или компрессионным методом (при помощи объемомера или поромера соответственно), а на пористом заполнителе - только объемным методом.
Для определения объема вовлеченного воздуха в бетонную смесь применяют:
объемомер
поромер
весы лабораторные по ГОСТ 24104;
- виброплощадку лабораторную;
- противень;
Слайд 98- кельму типа КБ по ГОСТ 9533;
- посуду мерную стеклянную по ГОСТ
- кельму типа КБ по ГОСТ 9533;
- посуду мерную стеклянную по ГОСТ
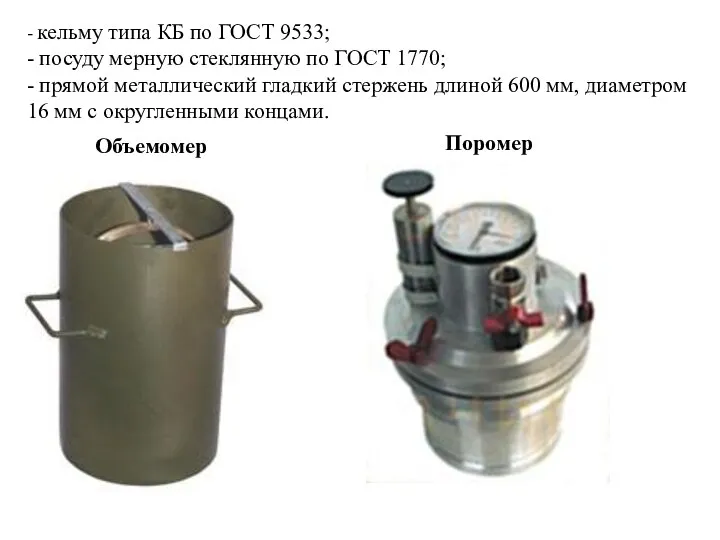
- прямой металлический гладкий стержень длиной 600 мм, диаметром 16 мм с округленными концами.
Объемомер
Поромер
Слайд 99Объемный метод определения объема вовлеченного воздуха
Навеску бетонной смеси помещают в сосуд объемомера
Объемный метод определения объема вовлеченного воздуха
Навеску бетонной смеси помещают в сосуд объемомера
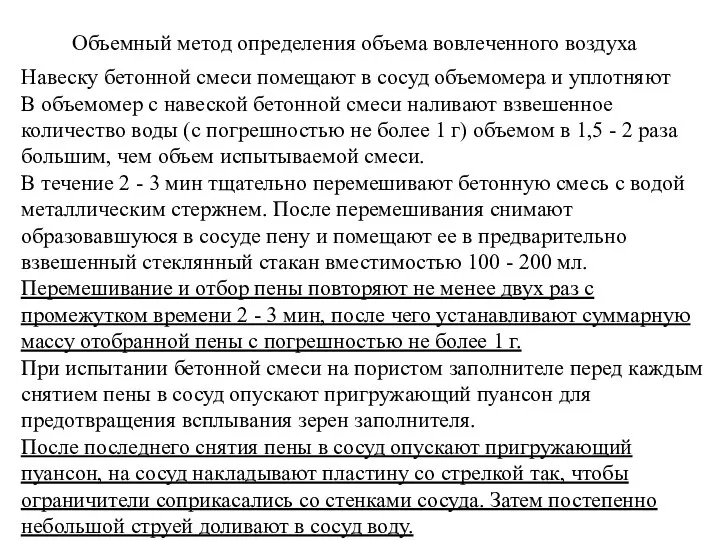
В объемомер с навеской бетонной смеси наливают взвешенное количество воды (с погрешностью не более 1 г) объемом в 1,5 - 2 раза большим, чем объем испытываемой смеси.
В течение 2 - 3 мин тщательно перемешивают бетонную смесь с водой металлическим стержнем. После перемешивания снимают образовавшуюся в сосуде пену и помещают ее в предварительно взвешенный стеклянный стакан вместимостью 100 - 200 мл.
Перемешивание и отбор пены повторяют не менее двух раз с промежутком времени 2 - 3 мин, после чего устанавливают суммарную массу отобранной пены с погрешностью не более 1 г.
При испытании бетонной смеси на пористом заполнителе перед каждым снятием пены в сосуд опускают пригружающий пуансон для предотвращения всплывания зерен заполнителя.
После последнего снятия пены в сосуд опускают пригружающий пуансон, на сосуд накладывают пластину со стрелкой так, чтобы ограничители соприкасались со стенками сосуда. Затем постепенно небольшой струей доливают в сосуд воду.
Слайд 100После этого взвешиванием определяют суммарную массу всей налитой в сосуд воды с
После этого взвешиванием определяют суммарную массу всей налитой в сосуд воды с
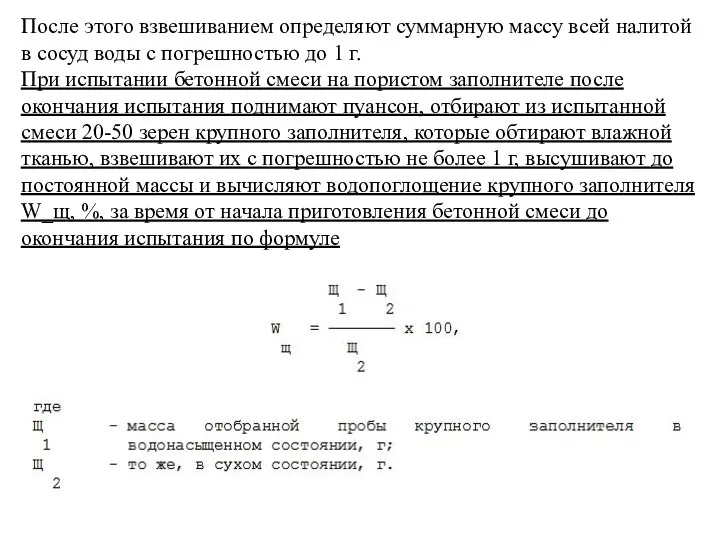
При испытании бетонной смеси на пористом заполнителе после окончания испытания поднимают пуансон, отбирают из испытанной смеси 20-50 зерен крупного заполнителя, которые обтирают влажной тканью, взвешивают их с погрешностью не более 1 г, высушивают до постоянной массы и вычисляют водопоглощение крупного заполнителя W_щ, %, за время от начала приготовления бетонной смеси до окончания испытания по формуле
Слайд 101Пористость бетонной смеси V_в, %, вычисляют с округлением до 0,1% по формуле
Пористость бетонной смеси V_в, %, вычисляют с округлением до 0,1% по формуле
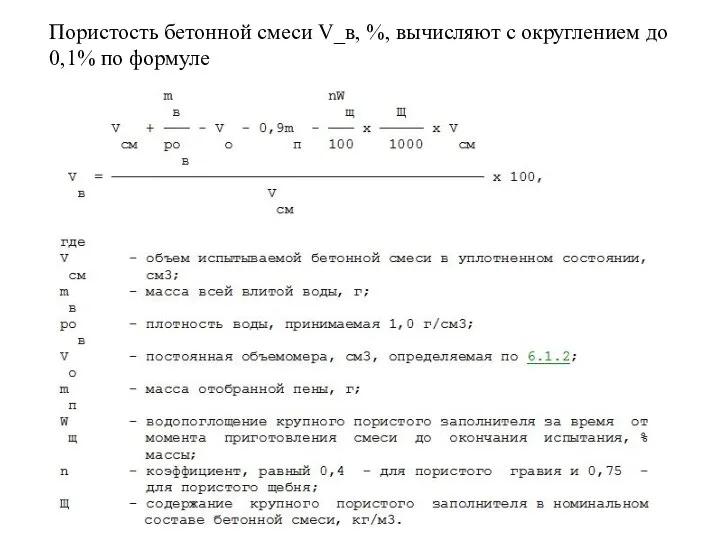
Слайд 102Компрессионный метод определения объема вовлеченного воздуха
Бетонную смесь укладывают в чашу поромера и
Компрессионный метод определения объема вовлеченного воздуха
Бетонную смесь укладывают в чашу поромера и
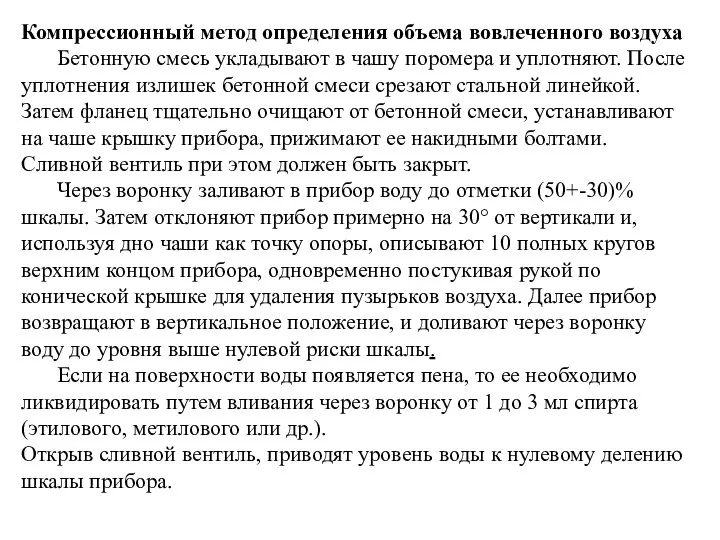
Через воронку заливают в прибор воду до отметки (50+-30)% шкалы. Затем отклоняют прибор примерно на 30° от вертикали и, используя дно чаши как точку опоры, описывают 10 полных кругов верхним концом прибора, одновременно постукивая рукой по конической крышке для удаления пузырьков воздуха. Далее прибор возвращают в вертикальное положение, и доливают через воронку воду до уровня выше нулевой риски шкалы.
Если на поверхности воды появляется пена, то ее необходимо ликвидировать путем вливания через воронку от 1 до 3 мл спирта (этилового, метилового или др.).
Открыв сливной вентиль, приводят уровень воды к нулевому делению шкалы прибора.
Слайд 103 Закрывают входной и сливной вентили и насосом поднимают давление в приборе до
Закрывают входной и сливной вентили и насосом поднимают давление в приборе до
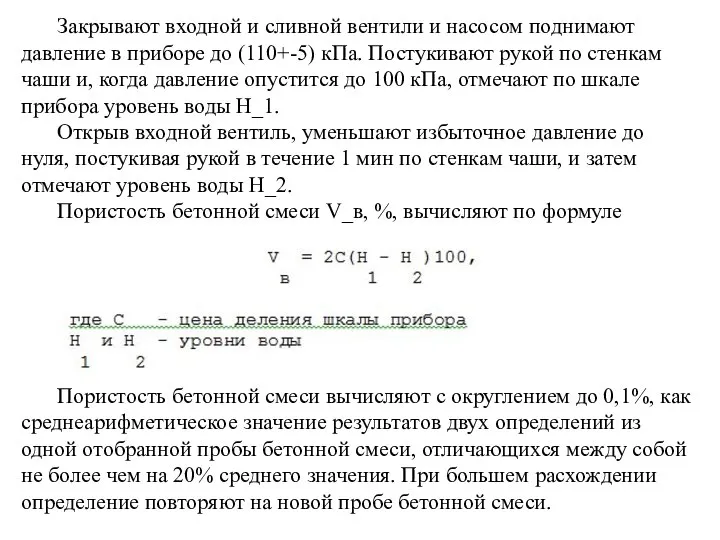
Открыв входной вентиль, уменьшают избыточное давление до нуля, постукивая рукой в течение 1 мин по стенкам чаши, и затем отмечают уровень воды H_2.
Пористость бетонной смеси V_в, %, вычисляют по формуле
Пористость бетонной смеси вычисляют с округлением до 0,1%, как среднеарифметическое значение результатов двух определений из одной отобранной пробы бетонной смеси, отличающихся между собой не более чем на 20% среднего значения. При большем расхождении определение повторяют на новой пробе бетонной смеси.
Слайд 104Показатели качества бетона
Методы определения прочности по контрольным образцам
Определение прочности бетона состоит в
Показатели качества бетона
Методы определения прочности по контрольным образцам
Определение прочности бетона состоит в
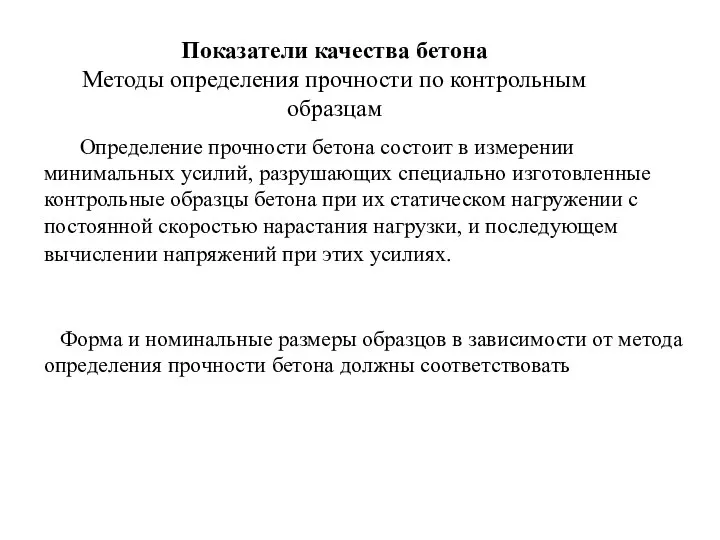
Форма и номинальные размеры образцов в зависимости от метода определения прочности бетона должны соответствовать
Слайд 106Наибольший номинальный размер зерен заполнителя
Наибольший номинальный размер зерен заполнителя
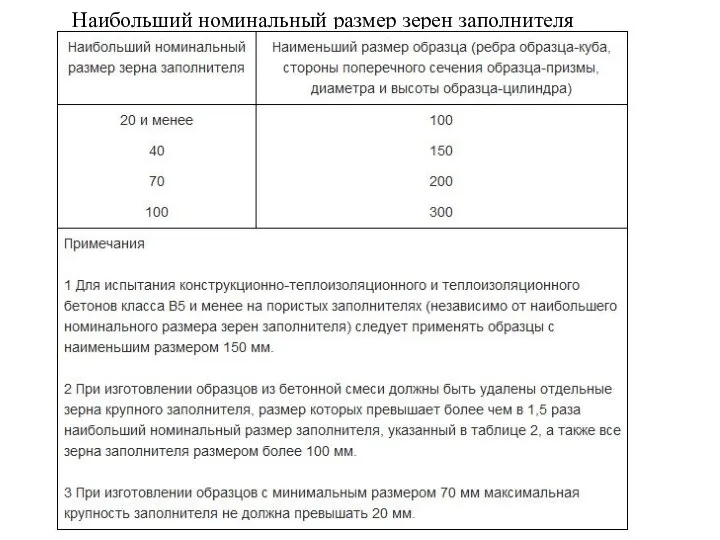
Слайд 107Отбор проб бетонной смеси и изготовление контрольных образцов
Объем пробы бетонной смеси должен
Отбор проб бетонной смеси и изготовление контрольных образцов
Объем пробы бетонной смеси должен
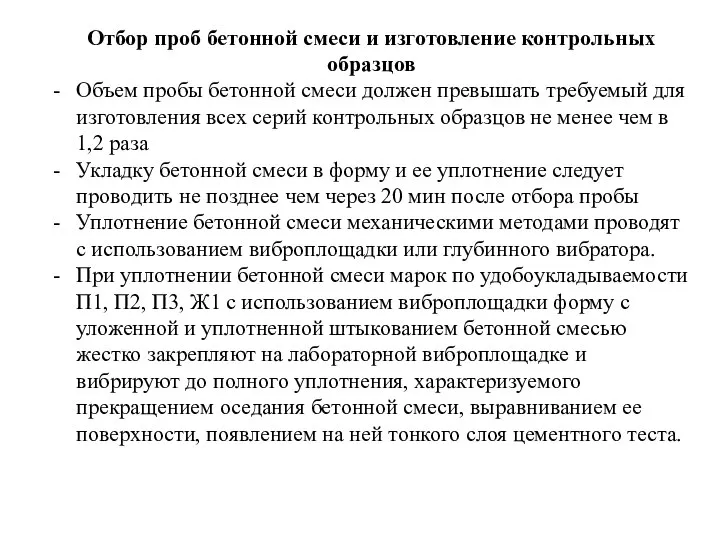
Укладку бетонной смеси в форму и ее уплотнение следует проводить не позднее чем через 20 мин после отбора пробы
Уплотнение бетонной смеси механическими методами проводят с использованием виброплощадки или глубинного вибратора.
При уплотнении бетонной смеси марок по удобоукладываемости П1, П2, П3, Ж1 с использованием виброплощадки форму с уложенной и уплотненной штыкованием бетонной смесью жестко закрепляют на лабораторной виброплощадке и вибрируют до полного уплотнения, характеризуемого прекращением оседания бетонной смеси, выравниванием ее поверхности, появлением на ней тонкого слоя цементного теста.
Слайд 108При уплотнении бетонной смеси марок по удобоукладываемости Ж2, Ж3, Ж4, Ж5 с
При уплотнении бетонной смеси марок по удобоукладываемости Ж2, Ж3, Ж4, Ж5 с
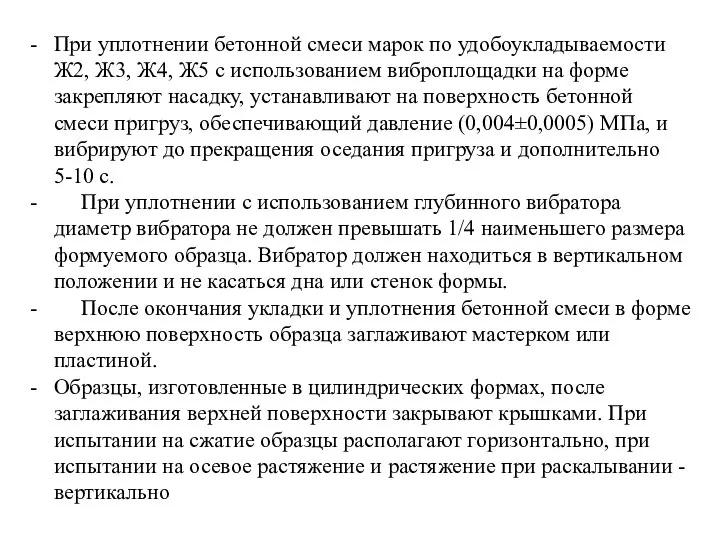
При уплотнении с использованием глубинного вибратора диаметр вибратора не должен превышать 1/4 наименьшего размера формуемого образца. Вибратор должен находиться в вертикальном положении и не касаться дна или стенок формы.
После окончания укладки и уплотнения бетонной смеси в форме верхнюю поверхность образца заглаживают мастерком или пластиной.
Образцы, изготовленные в цилиндрических формах, после заглаживания верхней поверхности закрывают крышками. При испытании на сжатие образцы располагают горизонтально, при испытании на осевое растяжение и растяжение при раскалывании - вертикально
Слайд 109Твердение, хранение и транспортирование образцов
Образцы, предназначенные для твердения в нормальных условиях, после
Твердение, хранение и транспортирование образцов
Образцы, предназначенные для твердения в нормальных условиях, после
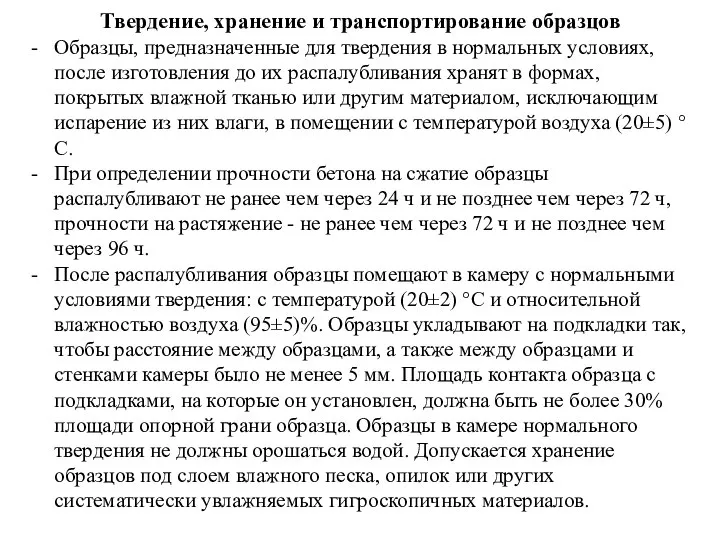
При определении прочности бетона на сжатие образцы распалубливают не ранее чем через 24 ч и не позднее чем через 72 ч, прочности на растяжение - не ранее чем через 72 ч и не позднее чем через 96 ч.
После распалубливания образцы помещают в камеру с нормальными условиями твердения: с температурой (20±2) °С и относительной влажностью воздуха (95±5)%. Образцы укладывают на подкладки так, чтобы расстояние между образцами, а также между образцами и стенками камеры было не менее 5 мм. Площадь контакта образца с подкладками, на которые он установлен, должна быть не более 30% площади опорной грани образца. Образцы в камере нормального твердения не должны орошаться водой. Допускается хранение образцов под слоем влажного песка, опилок или других систематически увлажняемых гигроскопичных материалов.
Слайд 110- При транспортировании образцов необходимо предохранять их от повреждений, изменения влажности и
- При транспортировании образцов необходимо предохранять их от повреждений, изменения влажности и
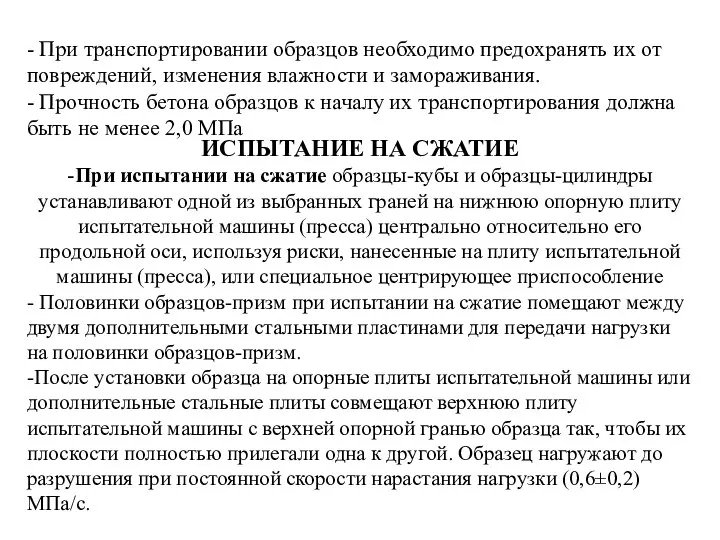
- Прочность бетона образцов к началу их транспортирования должна быть не менее 2,0 МПа
ИСПЫТАНИЕ НА СЖАТИЕ
-При испытании на сжатие образцы-кубы и образцы-цилиндры устанавливают одной из выбранных граней на нижнюю опорную плиту испытательной машины (пресса) центрально относительно его продольной оси, используя риски, нанесенные на плиту испытательной машины (пресса), или специальное центрирующее приспособление
- Половинки образцов-призм при испытании на сжатие помещают между двумя дополнительными стальными пластинами для передачи нагрузки на половинки образцов-призм.
-После установки образца на опорные плиты испытательной машины или дополнительные стальные плиты совмещают верхнюю плиту испытательной машины с верхней опорной гранью образца так, чтобы их плоскости полностью прилегали одна к другой. Образец нагружают до разрушения при постоянной скорости нарастания нагрузки (0,6±0,2) МПа/с.
Слайд 111-В случае разрушения образца по одной из неудовлетворительных схем, результат не учитывают,
-В случае разрушения образца по одной из неудовлетворительных схем, результат не учитывают,
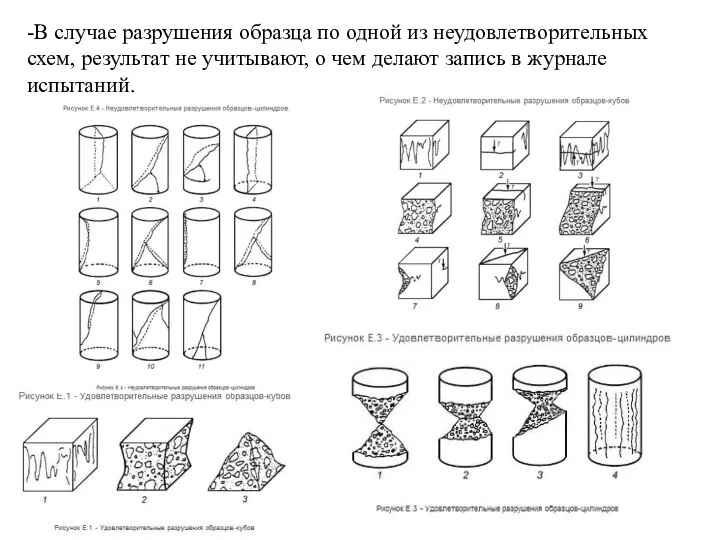
Слайд 112 Испытание на растяжение при изгибе
- Образец-призму устанавливают в испытательную машину и
Испытание на растяжение при изгибе
- Образец-призму устанавливают в испытательную машину и
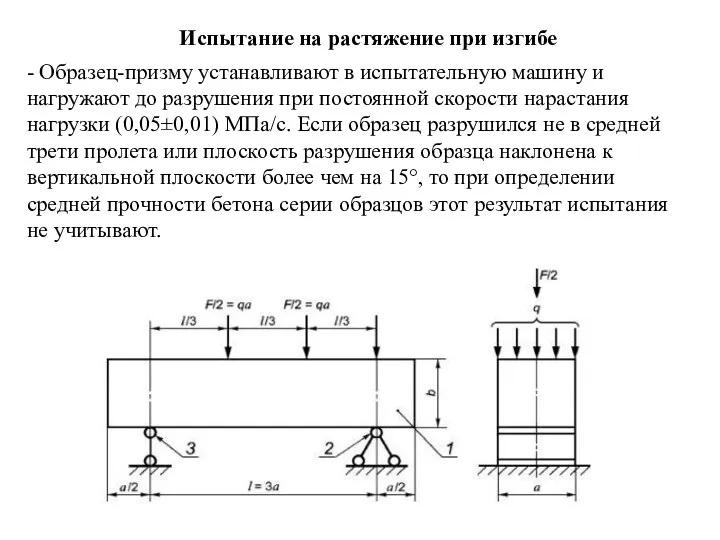
Слайд 1131 - образец; 2 - шар; 3 - опорная подушка; 4 -
1 - образец; 2 - шар; 3 - опорная подушка; 4 -
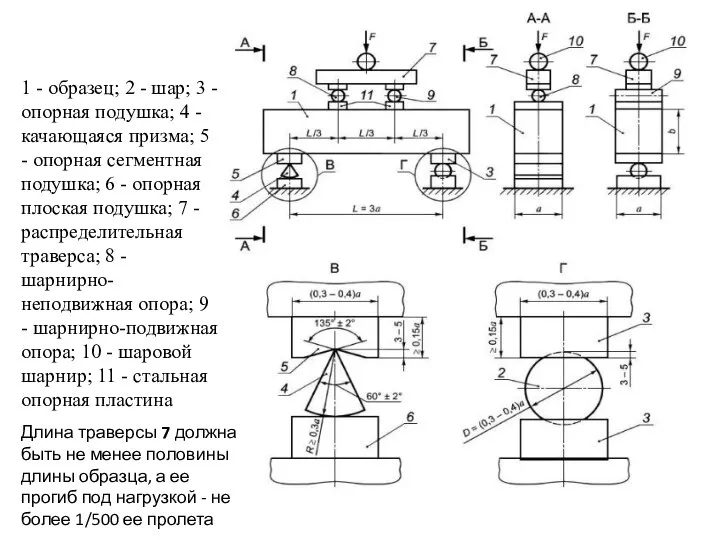
Длина траверсы 7 должна быть не менее половины длины образца, а ее прогиб под нагрузкой - не более 1/500 ее пролета
Слайд 114ИСПЫТАНИЯ НА РАСТЯЖЕНИЕ ПРИ РАСКАЛЫВАНИИ
Схемы испытания на растяжение при раскалывании
ИСПЫТАНИЯ НА РАСТЯЖЕНИЕ ПРИ РАСКАЛЫВАНИИ
Схемы испытания на растяжение при раскалывании
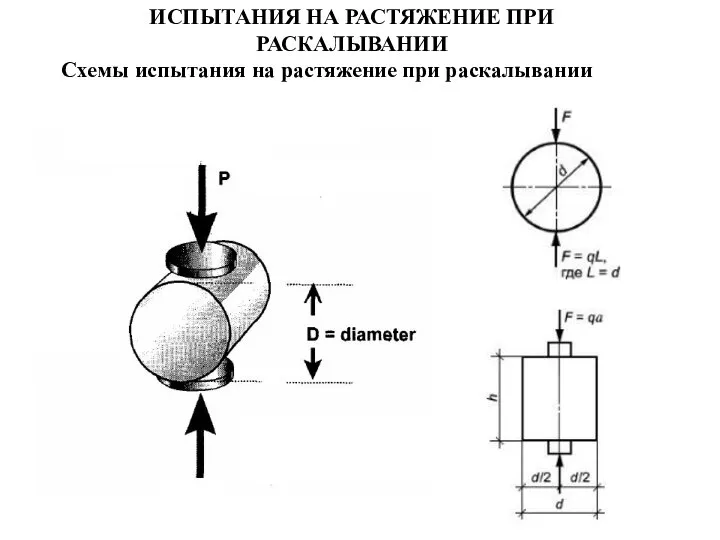
Слайд 115-Образец устанавливают на плиту испытательной машины
-С помощью держателя или временных опор проверяют,
-Образец устанавливают на плиту испытательной машины
-С помощью держателя или временных опор проверяют,
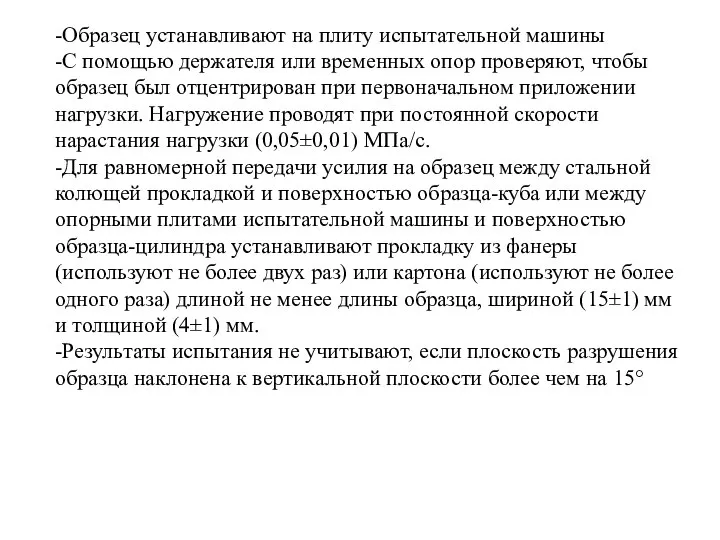
-Для равномерной передачи усилия на образец между стальной колющей прокладкой и поверхностью образца-куба или между опорными плитами испытательной машины и поверхностью образца-цилиндра устанавливают прокладку из фанеры (используют не более двух раз) или картона (используют не более одного раза) длиной не менее длины образца, шириной (15±1) мм и толщиной (4±1) мм.
-Результаты испытания не учитывают, если плоскость разрушения образца наклонена к вертикальной плоскости более чем на 15°
Слайд 116Испытание на осевое растяжение
-Образец закрепляют в разрывной машине по одной из схем,
Испытание на осевое растяжение
-Образец закрепляют в разрывной машине по одной из схем,
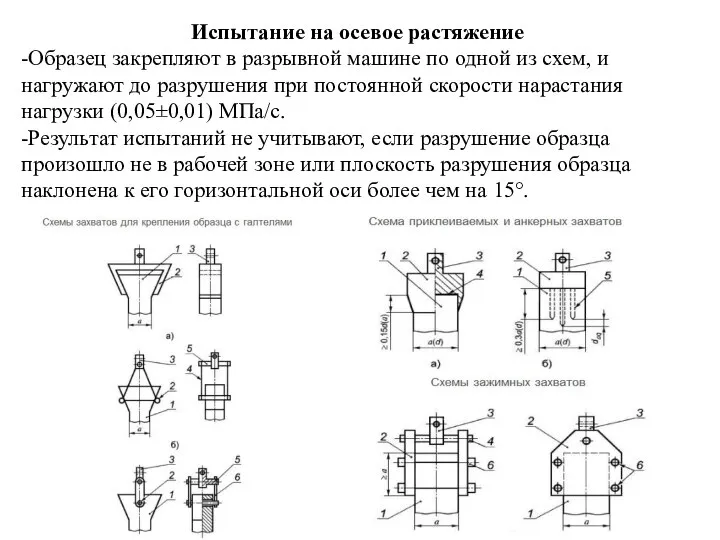
-Результат испытаний не учитывают, если разрушение образца произошло не в рабочей зоне или плоскость разрушения образца наклонена к его горизонтальной оси более чем на 15°.
Слайд 117ОПРЕДЕЛЕНИЯ МОРОЗОСТОЙКОСТИ
ОПРЕДЕЛЕНИЯ МОРОЗОСТОЙКОСТИ
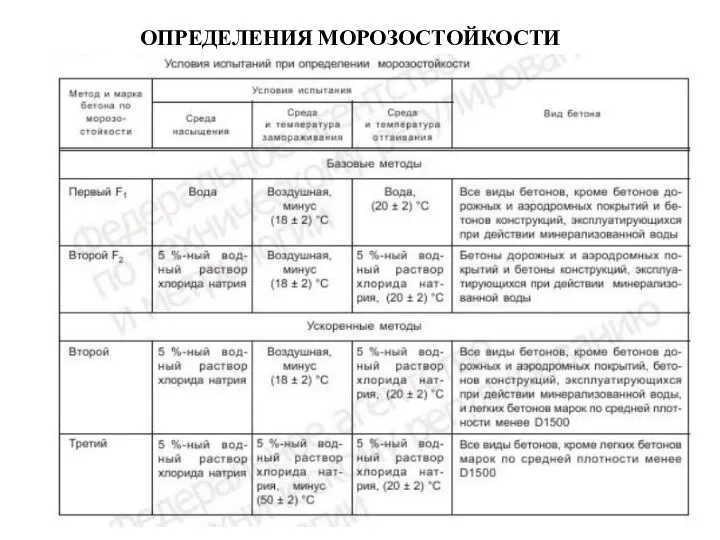
Слайд 118-Морозостойкость бетона определяют в проектном возрасте (после итоговых испытаний), установленном в нормативно-технической
-Морозостойкость бетона определяют в проектном возрасте (после итоговых испытаний), установленном в нормативно-технической
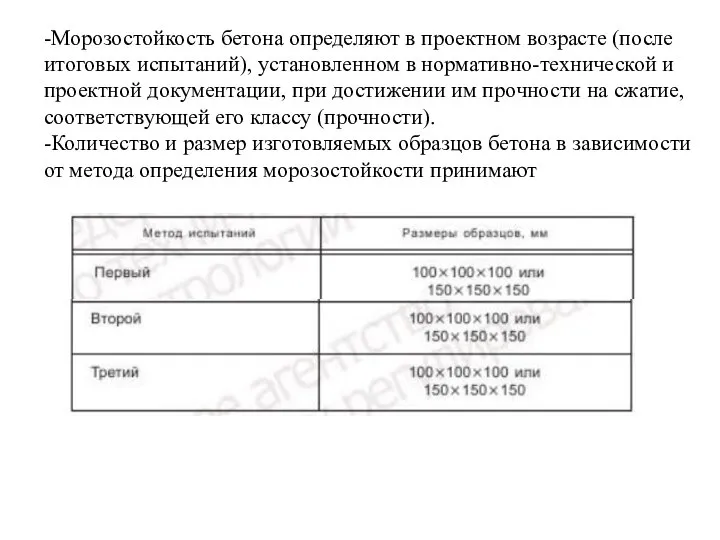
-Количество и размер изготовляемых образцов бетона в зависимости от метода определения морозостойкости принимают
Слайд 119-Образцы для испытания должны быть без внешних дефектов, средняя плотность которых не
-Образцы для испытания должны быть без внешних дефектов, средняя плотность которых не
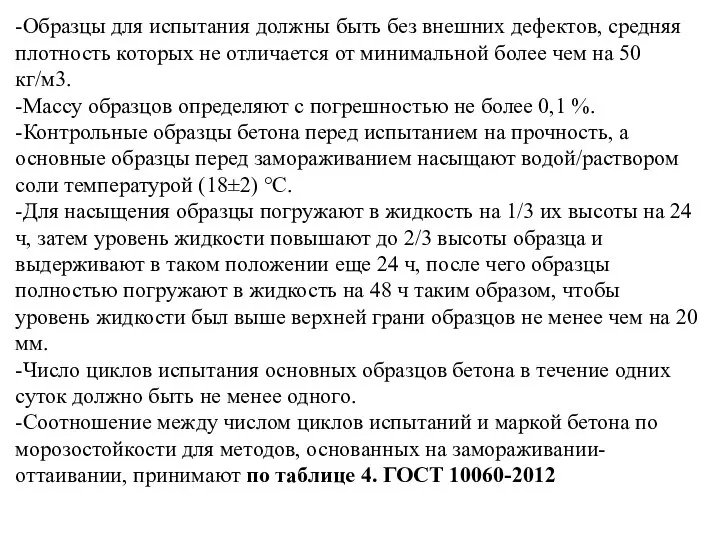
-Массу образцов определяют с погрешностью не более 0,1 %.
-Контрольные образцы бетона перед испытанием на прочность, а основные образцы перед замораживанием насыщают водой/раствором соли температурой (18±2) °С.
-Для насыщения образцы погружают в жидкость на 1/3 их высоты на 24 ч, затем уровень жидкости повышают до 2/3 высоты образца и выдерживают в таком положении еще 24 ч, после чего образцы полностью погружают в жидкость на 48 ч таким образом, чтобы уровень жидкости был выше верхней грани образцов не менее чем на 20 мм.
-Число циклов испытания основных образцов бетона в течение одних суток должно быть не менее одного.
-Соотношение между числом циклов испытаний и маркой бетона по морозостойкости для методов, основанных на замораживании-оттаивании, принимают по таблице 4. ГОСТ 10060-2012
Слайд 120Соотношение между числом циклов испытаний и маркой бетона
Соотношение между числом циклов испытаний и маркой бетона
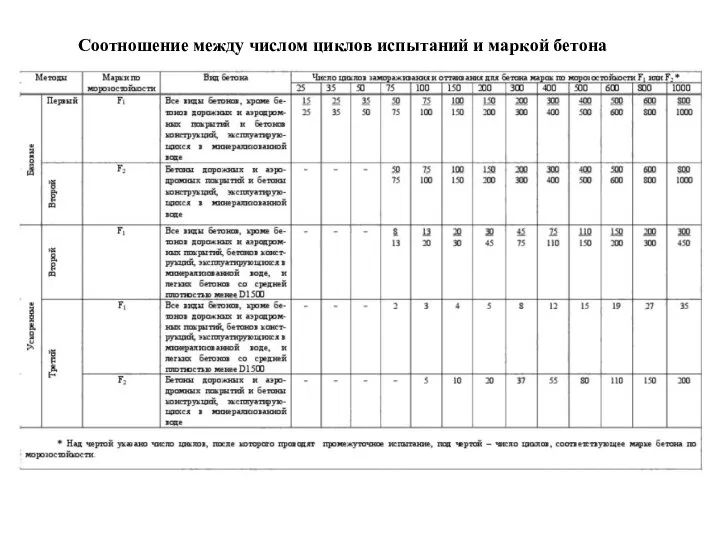
Слайд 121- В промежуточный срок испытания контролируют состояние образцов: появление трещин, отколов, шелушение
- В промежуточный срок испытания контролируют состояние образцов: появление трещин, отколов, шелушение
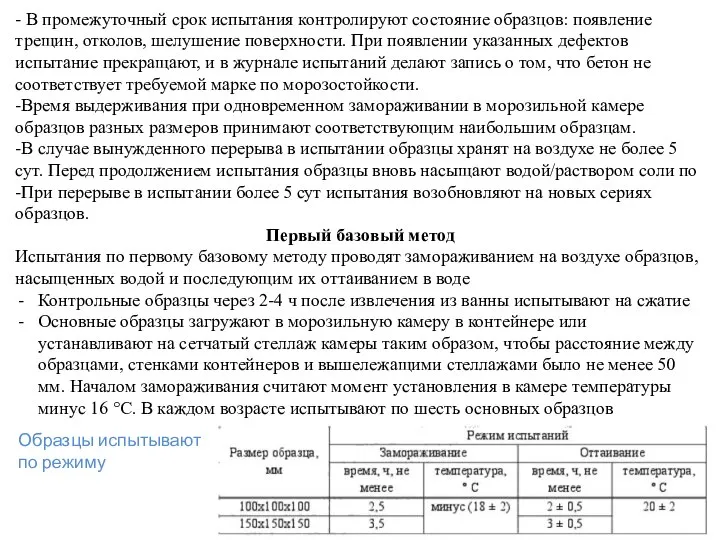
-Время выдерживания при одновременном замораживании в морозильной камере образцов разных размеров принимают соответствующим наибольшим образцам.
-В случае вынужденного перерыва в испытании образцы хранят на воздухе не более 5 сут. Перед продолжением испытания образцы вновь насыщают водой/раствором соли по -При перерыве в испытании более 5 сут испытания возобновляют на новых сериях образцов.
Первый базовый метод
Испытания по первому базовому методу проводят замораживанием на воздухе образцов, насыщенных водой и последующим их оттаиванием в воде
Контрольные образцы через 2-4 ч после извлечения из ванны испытывают на сжатие
Основные образцы загружают в морозильную камеру в контейнере или устанавливают на сетчатый стеллаж камеры таким образом, чтобы расстояние между образцами, стенками контейнеров и вышележащими стеллажами было не менее 50 мм. Началом замораживания считают момент установления в камере температуры минус 16 °С. В каждом возрасте испытывают по шесть основных образцов
Образцы испытывают по режиму
Слайд 122-Образцы после замораживания оттаивают в ванне с водой при температуре (18±2) °С.
-Температуру
-Образцы после замораживания оттаивают в ванне с водой при температуре (18±2) °С.
-Температуру
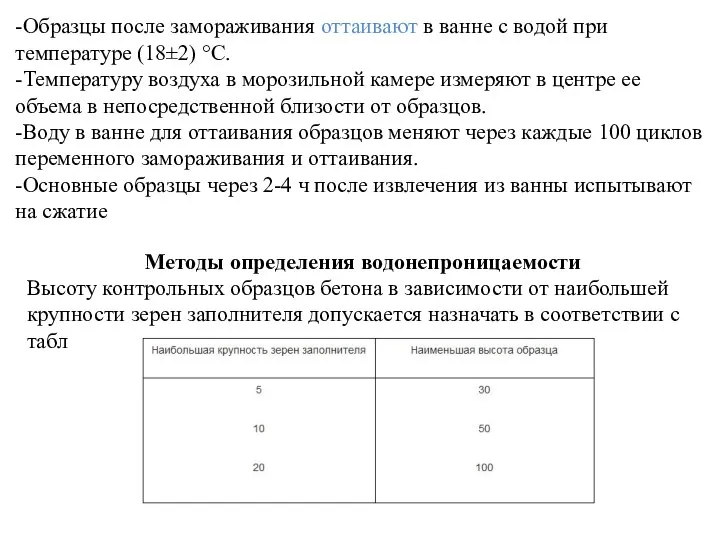
-Воду в ванне для оттаивания образцов меняют через каждые 100 циклов переменного замораживания и оттаивания.
-Основные образцы через 2-4 ч после извлечения из ванны испытывают на сжатие
Методы определения водонепроницаемости
Высоту контрольных образцов бетона в зависимости от наибольшей крупности зерен заполнителя допускается назначать в соответствии с табл
Слайд 123Схемы крепления и герметизации образцов бетона в обоймах
1 - образец бетона; 2
Схемы крепления и герметизации образцов бетона в обоймах
1 - образец бетона; 2
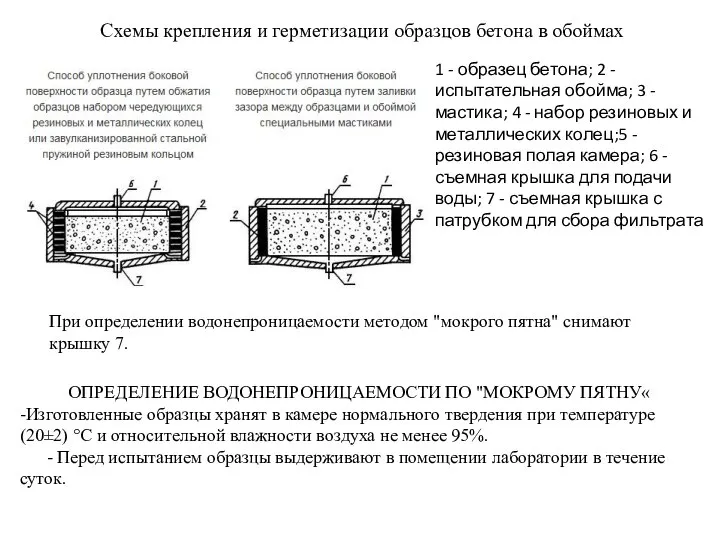
При определении водонепроницаемости методом "мокрого пятна" снимают крышку 7.
ОПРЕДЕЛЕНИЕ ВОДОНЕПРОНИЦАЕМОСТИ ПО "МОКРОМУ ПЯТНУ«
-Изготовленные образцы хранят в камере нормального твердения при температуре (20±2) °С и относительной влажности воздуха не менее 95%.
- Перед испытанием образцы выдерживают в помещении лаборатории в течение суток.
Слайд 124Проведение испытания
-Образцы в обойме устанавливают в гнезда установки для испытания и надежно
Проведение испытания
-Образцы в обойме устанавливают в гнезда установки для испытания и надежно
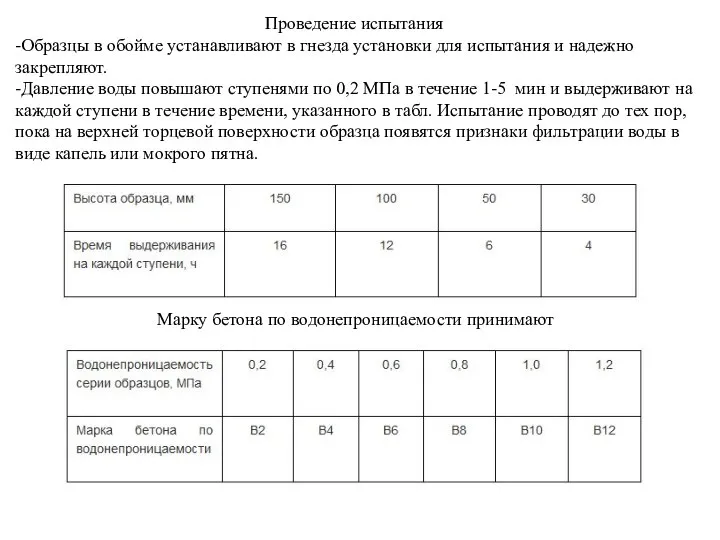
-Давление воды повышают ступенями по 0,2 МПа в течение 1-5 мин и выдерживают на каждой ступени в течение времени, указанного в табл. Испытание проводят до тех пор, пока на верхней торцевой поверхности образца появятся признаки фильтрации воды в виде капель или мокрого пятна.
Марку бетона по водонепроницаемости принимают
Слайд 125Пределение истираемости бетона на установках типа "круг истирания"
-Испытание бетона на круге истирания
Пределение истираемости бетона на установках типа "круг истирания"
-Испытание бетона на круге истирания
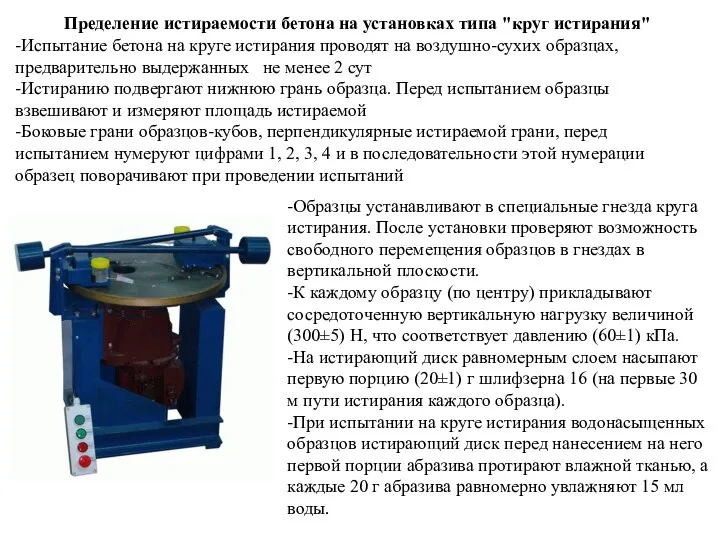
-Истиранию подвергают нижнюю грань образца. Перед испытанием образцы взвешивают и измеряют площадь истираемой
-Боковые грани образцов-кубов, перпендикулярные истираемой грани, перед испытанием нумеруют цифрами 1, 2, 3, 4 и в последовательности этой нумерации образец поворачивают при проведении испытаний
-Образцы устанавливают в специальные гнезда круга истирания. После установки проверяют возможность свободного перемещения образцов в гнездах в вертикальной плоскости.
-К каждому образцу (по центру) прикладывают сосредоточенную вертикальную нагрузку величиной (300±5) Н, что соответствует давлению (60±1) кПа.
-На истирающий диск равномерным слоем насыпают первую порцию (20±1) г шлифзерна 16 (на первые 30 м пути истирания каждого образца).
-При испытании на круге истирания водонасыщенных образцов истирающий диск перед нанесением на него первой порции абразива протирают влажной тканью, а каждые 20 г абразива равномерно увлажняют 15 мл воды.
Слайд 126-После установки образца (образцов) и нанесения на истирающий диск абразива включают привод
-После установки образца (образцов) и нанесения на истирающий диск абразива включают привод
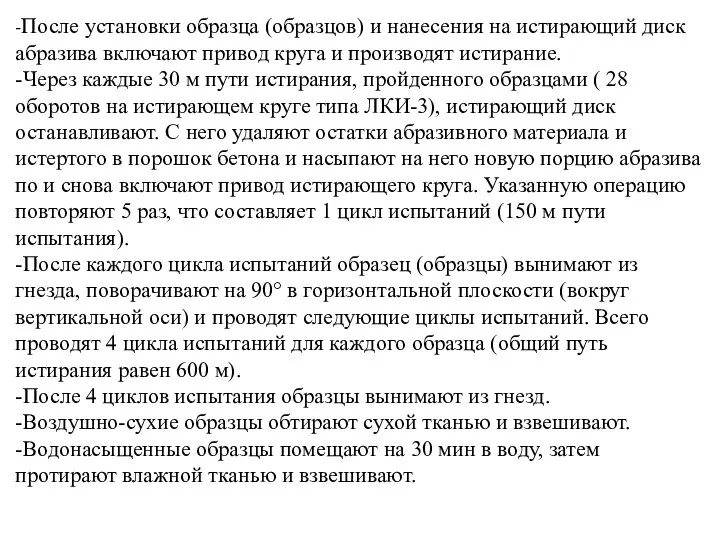
-Через каждые 30 м пути истирания, пройденного образцами ( 28 оборотов на истирающем круге типа ЛКИ-3), истирающий диск останавливают. С него удаляют остатки абразивного материала и истертого в порошок бетона и насыпают на него новую порцию абразива по и снова включают привод истирающего круга. Указанную операцию повторяют 5 раз, что составляет 1 цикл испытаний (150 м пути испытания).
-После каждого цикла испытаний образец (образцы) вынимают из гнезда, поворачивают на 90° в горизонтальной плоскости (вокруг вертикальной оси) и проводят следующие циклы испытаний. Всего проводят 4 цикла испытаний для каждого образца (общий путь истирания равен 600 м).
-После 4 циклов испытания образцы вынимают из гнезд.
-Воздушно-сухие образцы обтирают сухой тканью и взвешивают.
-Водонасыщенные образцы помещают на 30 мин в воду, затем протирают влажной тканью и взвешивают.
Слайд 127СХЕМА ЛАБОРАТОРНОГО КОНТРОЛЯ КАЧЕСТВА
БЕТОННЫЕ СМЕСИ И БЕТОН
СХЕМА ЛАБОРАТОРНОГО КОНТРОЛЯ КАЧЕСТВА
БЕТОННЫЕ СМЕСИ И БЕТОН
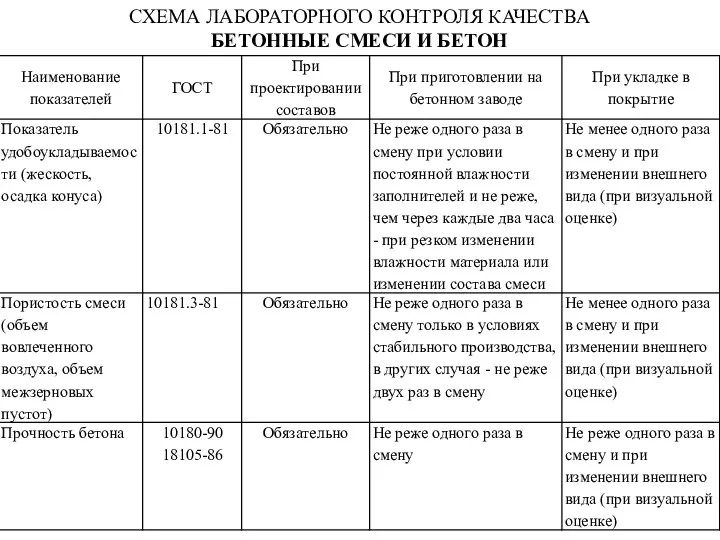
Слайд 129Повторное использование материалов
-С целью экономии средств, сегодня нередко прибегают к восстановлению
Повторное использование материалов
-С целью экономии средств, сегодня нередко прибегают к восстановлению
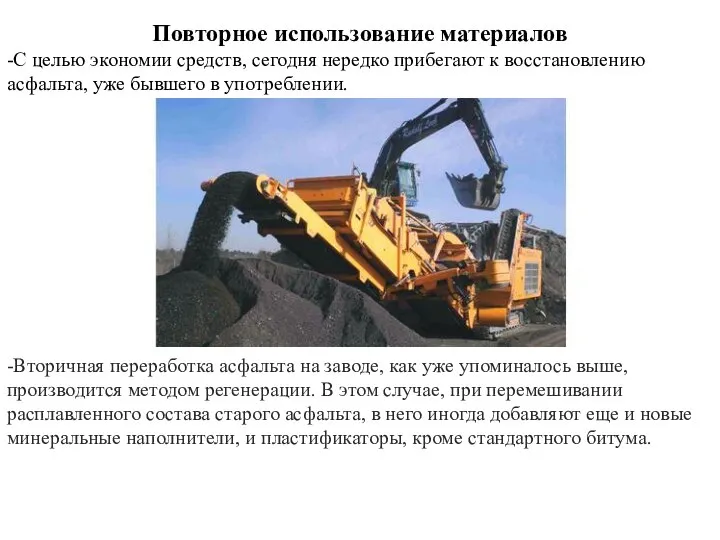
-Вторичная переработка асфальта на заводе, как уже упоминалось выше, производится методом регенерации. В этом случае, при перемешивании расплавленного состава старого асфальта, в него иногда добавляют еще и новые минеральные наполнители, и пластификаторы, кроме стандартного битума.
Слайд 130Холодный ресайклинг состоит в фрезеровании старого дорожного покрытия, последующем смешении асфальтовой крошки или
Холодный ресайклинг состоит в фрезеровании старого дорожного покрытия, последующем смешении асфальтовой крошки или
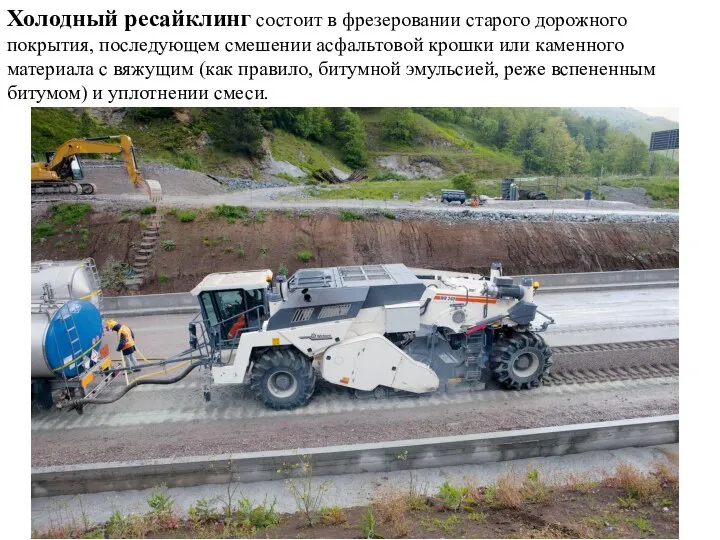
Слайд 131-Холодный ресайклинг как способ ремонта дорожной одежды имеет ряд очевидных преимуществ. Исключена
-Холодный ресайклинг как способ ремонта дорожной одежды имеет ряд очевидных преимуществ. Исключена

Слайд 132Горячее ремиксирование асфальтобетона
Горячее ремиксирование асфальтобетона
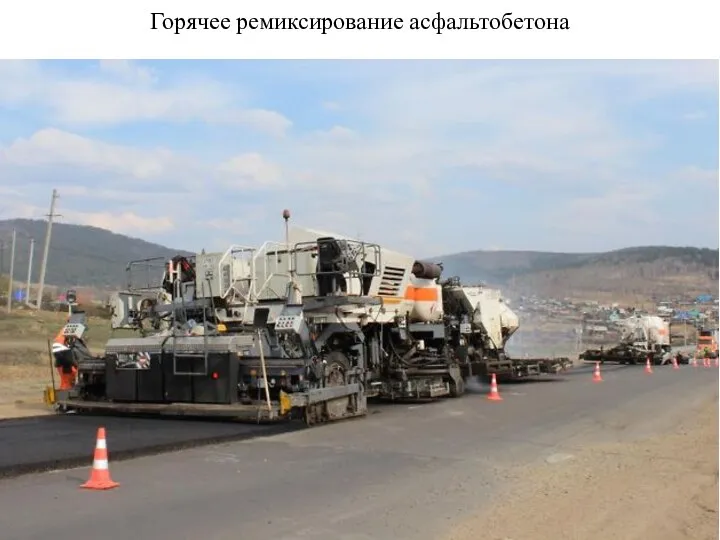