Слайд 22
Основные элементы коленчатого вала
1. Коренная шейка – опора вала, лежащая в коренном
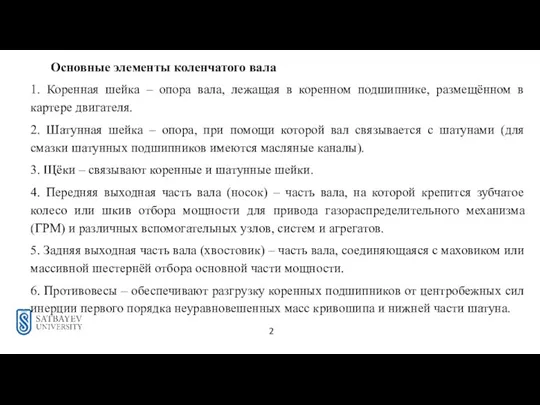
подшипнике, размещённом в картере двигателя.
2. Шатунная шейка – опора, при помощи которой вал связывается с шатунами (для смазки шатунных подшипников имеются масляные каналы).
3. Щёки – связывают коренные и шатунные шейки.
4. Передняя выходная часть вала (носок) – часть вала, на которой крепится зубчатое колесо или шкив отбора мощности для привода газораспределительного механизма (ГРМ) и различных вспомогательных узлов, систем и агрегатов.
5. Задняя выходная часть вала (хвостовик) – часть вала, соединяющаяся с маховиком или массивной шестернёй отбора основной части мощности.
6. Противовесы – обеспечивают разгрузку коренных подшипников от центробежных сил инерции первого порядка неуравновешенных масс кривошипа и нижней части шатуна.
Слайд 33
Общий вид коленчатого вала с маховиком:
1 – шатунная шейка, 2 – щека,
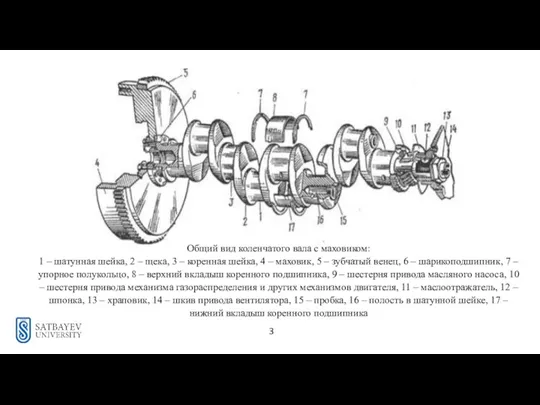
3 – коренная шейка, 4 – маховик, 5 – зубчатый венец, 6 – шарикоподшипник, 7 – упорное полукольцо, 8 – верхний вкладыш коренного подшипника, 9 – шестерня привода масляного насоса, 10 – шестерня привода механизма газораспределения и других механизмов двигателя, 11 – маслоотражатель, 12 – шпонка, 13 – храповик, 14 – шкив привода вентилятора, 15 – пробка, 16 – полость в шатунной шейке, 17 – нижний вкладыш коренного подшипника
Слайд 44
Коленчатый вал двигателя Евро-2 КамАЗ-740
Упрочнение коленчатого вала производится азотированием на глубину
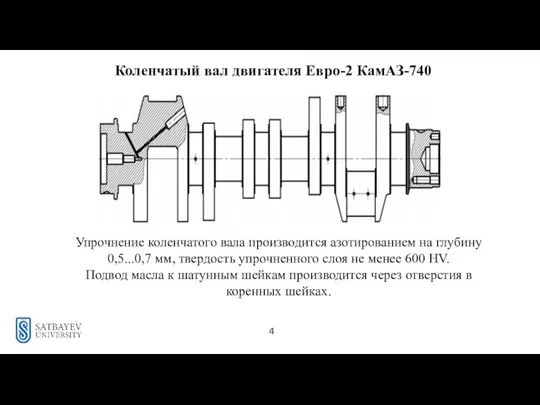
0,5...0,7 мм, твердость упрочненного слоя не менее 600 HV.
Подвод масла к шатунным шейкам производится через отверстия в коренных шейках.
Слайд 55
Износ и дефекты коленчатого вала
Основные дефекты коленчатых валов [30]:
1. Изгиб
![5 Износ и дефекты коленчатого вала Основные дефекты коленчатых валов [30]: 1.](/_ipx/f_webp&q_80&fit_contain&s_1440x1080/imagesDir/jpg/1033350/slide-4.jpg)
вала;
2. Износ посадочных мест и шпоночных канавок под шестерню или шкив вала;
3. Повреждение или износ резьбы под храповик;
4. Износ отверстий или резьбы во фланце для крепления маховика;
5. Износ шеек и т. д.
Слайд 6Износ и дефекты коленчатого вала
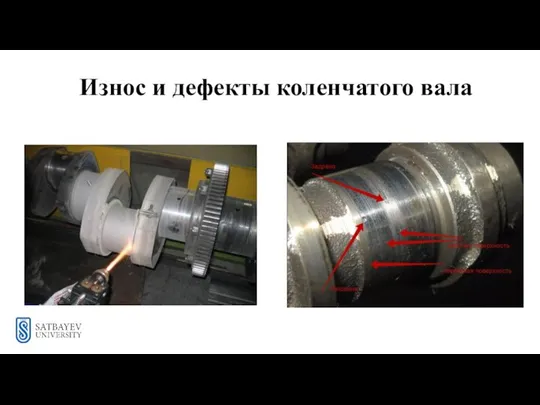
Слайд 7Износ и дефекты коленчатого вала
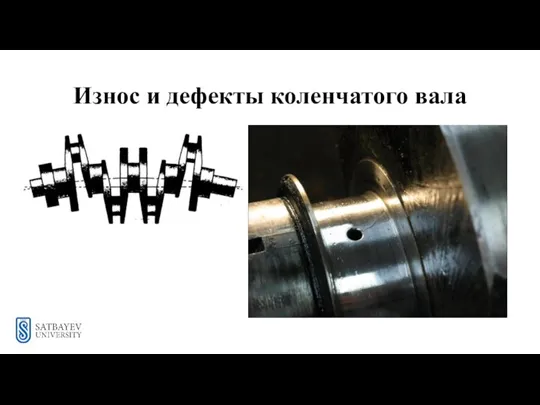
Слайд 86
Выбор заготовки
Существуют три пути выбора заготовки:
1. Грубая заготовка – конфигурация
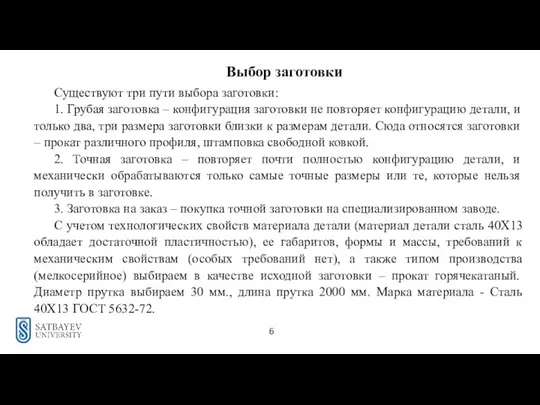
заготовки не повторяет конфигурацию детали, и только два, три размера заготовки близки к размерам детали. Сюда относятся заготовки – прокат различного профиля, штамповка свободной ковкой.
2. Точная заготовка – повторяет почти полностью конфигурацию детали, и механически обрабатываются только самые точные размеры или те, которые нельзя получить в заготовке.
3. Заготовка на заказ – покупка точной заготовки на специализированном заводе.
С учетом технологических свойств материала детали (материал детали сталь 40X13 обладает достаточной пластичностью), ее габаритов, формы и массы, требований к механическим свойствам (особых требований нет), а также типом производства (мелкосерийное) выбираем в качестве исходной заготовки – прокат горячекатаный. Диаметр прутка выбираем 30 мм., длина прутка 2000 мм. Марка материала - Сталь 40X13 ГОСТ 5632-72.
Слайд 97
Выбор оборудования и технологической оснастки
1. Соответствие основных размеров станка габаритным размерам
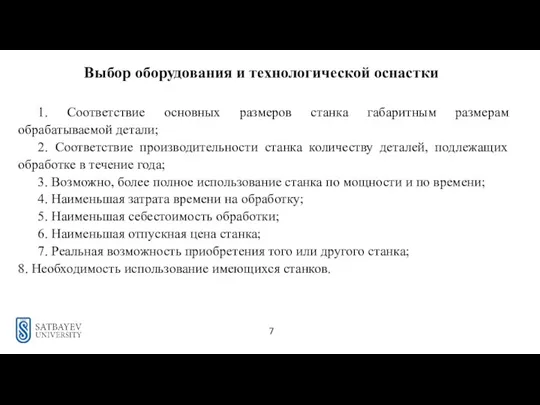
обрабатываемой детали;
2. Соответствие производительности станка количеству деталей, подлежащих обработке в течение года;
3. Возможно, более полное использование станка по мощности и по времени;
4. Наименьшая затрата времени на обработку;
5. Наименьшая себестоимость обработки;
6. Наименьшая отпускная цена станка;
7. Реальная возможность приобретения того или другого станка;
8. Необходимость использование имеющихся станков.
Слайд 1210
Расчет конструкторских размеров

Слайд 1311
Расчет режимов резания
Выбор величин элементов резания и параметров инструмента для точения
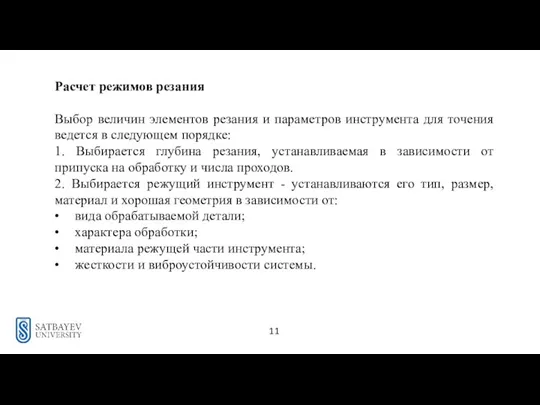
ведется в следующем порядке:
1. Выбирается глубина резания, устанавливаемая в зависимости от припуска на обработку и числа проходов.
2. Выбирается режущий инструмент - устанавливаются его тип, размер, материал и хорошая геометрия в зависимости от:
• вида обрабатываемой детали;
• характера обработки;
• материала режущей части инструмента;
• жесткости и виброустойчивости системы.