Содержание
- 2. Технический процесс брикетирования отходов деревообработки Исходные данные Необходимо переработать отходы, возникающие в результате деятельности предприятия по
- 3. Подготовка сырья В зависимости от используемого оборудования в результате распиловки выход деловой древесины составляет порядка 40%,
- 4. Измельчение горбыля и прочих крупных древесных и агро-отходов Для измельчения горбыля и крупных древесных и агро-отходов
- 5. Измельчение мелких древесных и агро-отходов Для измельчения мелких древесных и агро-отходов (крупные древесные отходы, переработанные щепорезом,
- 6. Сушка отходов После дробления молотковой дробилкой отходы имеют естественную влажность 35%-50%. Для нормальной работы пресса-экструдера нужно
- 7. Брикетирование Для брикетирования уже измельченных и просушенных отходов используются: пресс-экструдеры серии SBM, производительностью до 350кг/ч. Брикеты
- 8. Производительность линий брикетирования Производительность небольшой линии брикетирования можно менять за счет количества установленных пресс-экструдеров: Линия брикетирования
- 9. Требования к персоналу для обслуживания линии производительностью 700кг/ч Необходимое количество рабочих для непрерывной работы Для непрерывной
- 10. Расчет стоимости оборудования для комплекса с производительностью до 700 кг/ч: ИТОГО стоимость комплекса = 1 850
- 11. Дополнительные затраты для запуска линии производительностью до 700 кг/ч Необходимые условия для установки линии: площадь помещения
- 12. Окупаемость проекта (Модель 1) Модель1. Пессимистичный расчет окупаемости проекта при работе комплекса 22 часа в сутки
- 13. Окупаемость проекта (Модель 2) Модель 2. Пессимистичный расчет окупаемости проекта при работе комплекса 8 часов в
- 14. Гарантийные обязательства, доставка, монтаж, сроки На все оборудование, за исключением расходных материалов и запасных частей, предоставляется
- 15. Евродрова стандарта Pini-Kay и NESTRO Топливные брикеты из древесных и агро-отходов являются популярным и самым экономичным
- 16. Евродрова стандарта Pini-Kay и NESTRO Высокая продолжительность горения Это означает, что по сравнению с обычными дровами,
- 18. Скачать презентацию
Слайд 2Технический процесс брикетирования отходов деревообработки
Исходные данные
Необходимо переработать отходы, возникающие в результате деятельности
Технический процесс брикетирования отходов деревообработки
Исходные данные
Необходимо переработать отходы, возникающие в результате деятельности
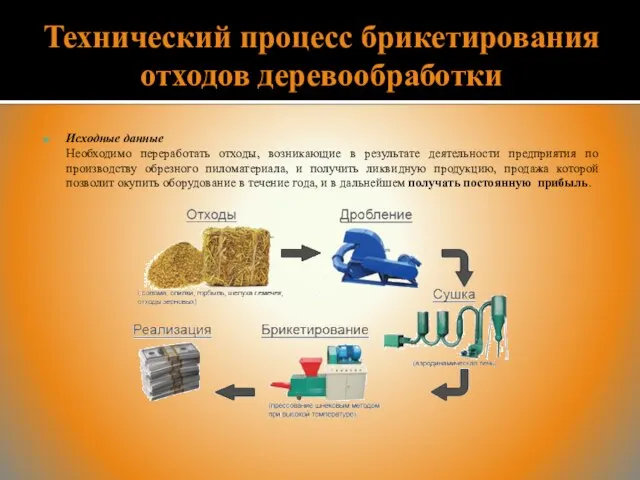
Слайд 3Подготовка сырья
В зависимости от используемого оборудования в результате распиловки выход деловой древесины
Подготовка сырья
В зависимости от используемого оборудования в результате распиловки выход деловой древесины
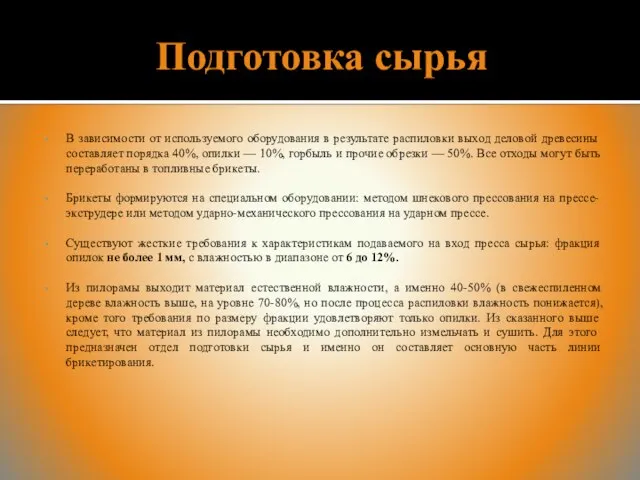
Брикеты формируются на специальном оборудовании: методом шнекового прессования на прессе-экструдере или методом ударно-механического прессования на ударном прессе.
Существуют жесткие требования к характеристикам подаваемого на вход пресса сырья: фракция опилок не более 1 мм, с влажностью в диапазоне от 6 до 12%.
Из пилорамы выходит материал естественной влажности, а именно 40-50% (в свежеспиленном дереве влажность выше, на уровне 70-80%, но после процесса распиловки влажность понижается), кроме того требования по размеру фракции удовлетворяют только опилки. Из сказанного выше следует, что материал из пилорамы необходимо дополнительно измельчать и сушить. Для этого предназначен отдел подготовки сырья и именно он составляет основную часть линии брикетирования.
Слайд 4Измельчение горбыля и прочих крупных древесных и агро-отходов
Для измельчения горбыля и крупных
Измельчение горбыля и прочих крупных древесных и агро-отходов
Для измельчения горбыля и крупных
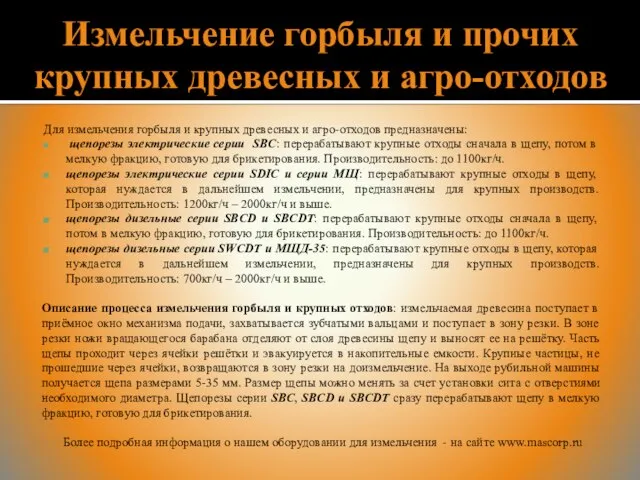
щепорезы электрические серии SBC: перерабатывают крупные отходы сначала в щепу, потом в мелкую фракцию, готовую для брикетирования. Производительность: до 1100кг/ч.
щепорезы электрические серии SDIC и серии МЩ: перерабатывают крупные отходы в щепу, которая нуждается в дальнейшем измельчении, предназначены для крупных производств. Производительность: 1200кг/ч – 2000кг/ч и выше.
щепорезы дизельные серии SBCD и SBCDT: перерабатывают крупные отходы сначала в щепу, потом в мелкую фракцию, готовую для брикетирования. Производительность: до 1100кг/ч.
щепорезы дизельные серии SWCDT и МЩД-35: перерабатывают крупные отходы в щепу, которая нуждается в дальнейшем измельчении, предназначены для крупных производств. Производительность: 700кг/ч – 2000кг/ч и выше.
Описание процесса измельчения горбыля и крупных отходов: измельчаемая древесина поступает в приёмное окно механизма подачи, захватывается зубчатыми вальцами и поступает в зону резки. В зоне резки ножи вращающегося барабана отделяют от слоя древесины щепу и выносят ее на решётку. Часть щепы проходит через ячейки решётки и эвакуируется в накопительные емкости. Крупные частицы, не прошедшие через ячейки, возвращаются в зону резки на доизмельчение. На выходе рубильной машины получается щепа размерами 5-35 мм. Размер щепы можно менять за счет установки сита с отверстиями необходимого диаметра. Щепорезы серии SBC, SBCD и SBCDT сразу перерабатывают щепу в мелкую фракцию, готовую для брикетирования.
Более подробная информация о нашем оборудовании для измельчения - на сайте www.mascorp.ru
Слайд 5Измельчение мелких древесных и агро-отходов
Для измельчения мелких древесных и агро-отходов (крупные древесные
Измельчение мелких древесных и агро-отходов
Для измельчения мелких древесных и агро-отходов (крупные древесные

Щепа поступает в установку через бункер-накопитель и размалывается под действием крутящегося барабана на скорости 1500 об/мин до фракции 0.1мм – 1мм.
Подробная техническая информация и стоимость оборудования - на сайте www.mascorp.ru
Слайд 6Сушка отходов
После дробления молотковой дробилкой отходы имеют естественную влажность 35%-50%.
Для нормальной
Сушка отходов
После дробления молотковой дробилкой отходы имеют естественную влажность 35%-50%.
Для нормальной
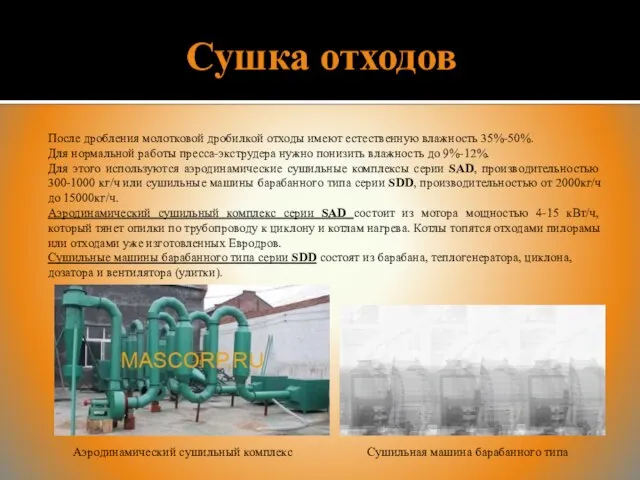
Для этого используются аэродинамические сушильные комплексы серии SAD, производительностью 300-1000 кг/ч или сушильные машины барабанного типа серии SDD, производительностью от 2000кг/ч до 15000кг/ч.
Аэродинамический сушильный комплекс серии SAD состоит из мотора мощностью 4-15 кВт/ч, который тянет опилки по трубопроводу к циклону и котлам нагрева. Котлы топятся отходами пилорамы или отходами уже изготовленных Евродров.
Сушильные машины барабанного типа серии SDD состоят из барабана, теплогенератора, циклона, дозатора и вентилятора (улитки).
Аэродинамический сушильный комплекс Сушильная машина барабанного типа
Слайд 7Брикетирование
Для брикетирования уже измельченных и просушенных отходов используются:
пресс-экструдеры серии SBM, производительностью
Брикетирование
Для брикетирования уже измельченных и просушенных отходов используются:
пресс-экструдеры серии SBM, производительностью
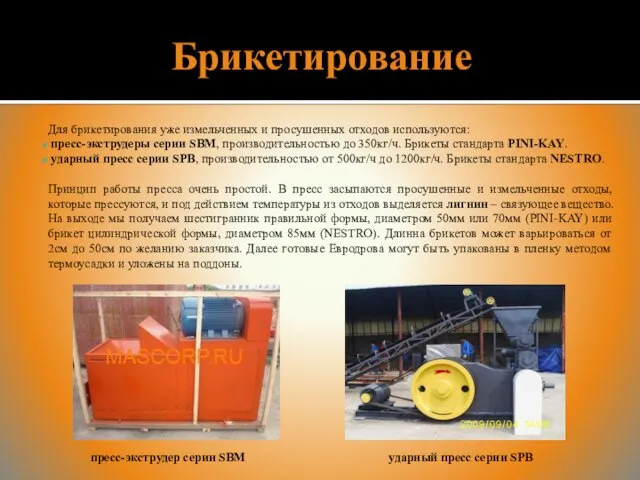
ударный пресс серии SPB, производительностью от 500кг/ч до 1200кг/ч. Брикеты стандарта NESTRO.
Принцип работы пресса очень простой. В пресс засыпаются просушенные и измельченные отходы, которые прессуются, и под действием температуры из отходов выделяется лигнин – связующее вещество. На выходе мы получаем шестигранник правильной формы, диаметром 50мм или 70мм (PINI-KAY) или брикет цилиндрической формы, диаметром 85мм (NESTRO). Длинна брикетов может варьироваться от 2см до 50см по желанию заказчика. Далее готовые Евродрова могут быть упакованы в пленку методом термоусадки и уложены на поддоны.
пресс-экструдер серии SBM ударный пресс серии SPB
Слайд 8Производительность линий брикетирования
Производительность небольшой линии брикетирования можно менять за счет количества установленных
Производительность линий брикетирования
Производительность небольшой линии брикетирования можно менять за счет количества установленных
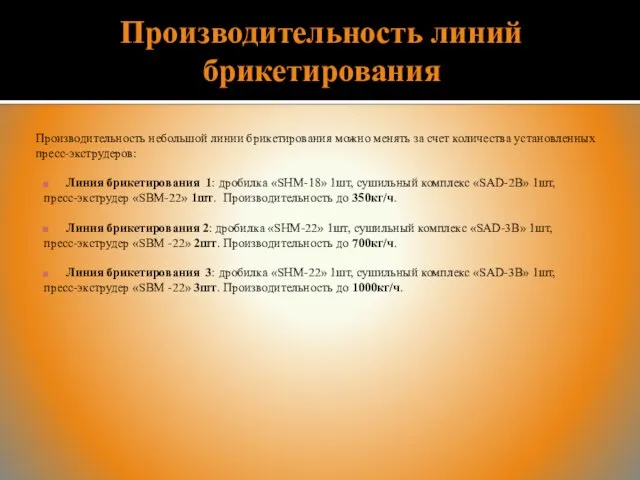
Линия брикетирования 1: дробилка «SHM-18» 1шт, сушильный комплекс «SAD-2B» 1шт,
пресс-экструдер «SBM-22» 1шт. Производительность до 350кг/ч.
Линия брикетирования 2: дробилка «SHM-22» 1шт, сушильный комплекс «SAD-3B» 1шт,
пресс-экструдер «SBM -22» 2шт. Производительность до 700кг/ч.
Линия брикетирования 3: дробилка «SHM-22» 1шт, сушильный комплекс «SAD-3B» 1шт,
пресс-экструдер «SBM -22» 3шт. Производительность до 1000кг/ч.
Слайд 9Требования к персоналу для обслуживания линии производительностью 700кг/ч
Необходимое количество рабочих для непрерывной
Требования к персоналу для обслуживания линии производительностью 700кг/ч
Необходимое количество рабочих для непрерывной
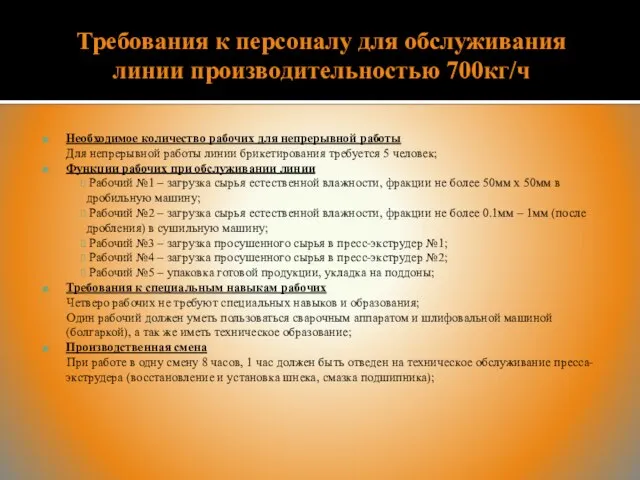
Для непрерывной работы линии брикетирования требуется 5 человек;
Функции рабочих при обслуживании линии
Рабочий №1 – загрузка сырья естественной влажности, фракции не более 50мм х 50мм в дробильную машину;
Рабочий №2 – загрузка сырья естественной влажности, фракции не более 0.1мм – 1мм (после дробления) в сушильную машину;
Рабочий №3 – загрузка просушенного сырья в пресс-экструдер №1;
Рабочий №4 – загрузка просушенного сырья в пресс-экструдер №2;
Рабочий №5 – упаковка готовой продукции, укладка на поддоны;
Требования к специальным навыкам рабочих
Четверо рабочих не требуют специальных навыков и образования;
Один рабочий должен уметь пользоваться сварочным аппаратом и шлифовальной машиной (болгаркой), а так же иметь техническое образование;
Производственная смена
При работе в одну смену 8 часов, 1 час должен быть отведен на техническое обслуживание пресса-экструдера (восстановление и установка шнека, смазка подшипника);
Слайд 10Расчет стоимости оборудования для комплекса с производительностью до 700 кг/ч:
ИТОГО стоимость
Расчет стоимости оборудования для комплекса с производительностью до 700 кг/ч:
ИТОГО стоимость
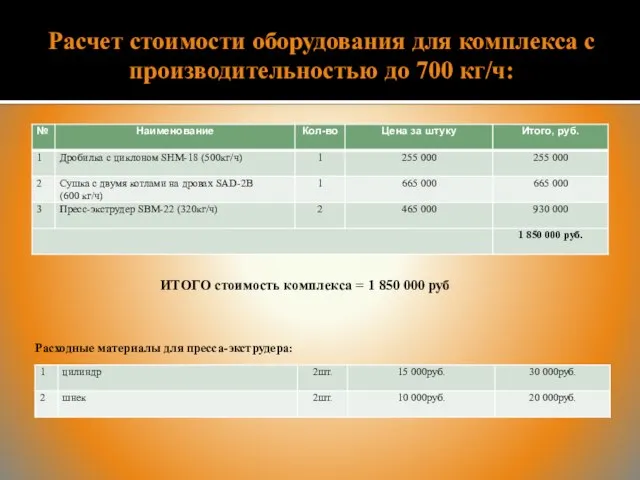
Расходные материалы для пресса-экструдера:
Слайд 11Дополнительные затраты для запуска линии производительностью до 700 кг/ч
Необходимые условия для установки
Дополнительные затраты для запуска линии производительностью до 700 кг/ч
Необходимые условия для установки
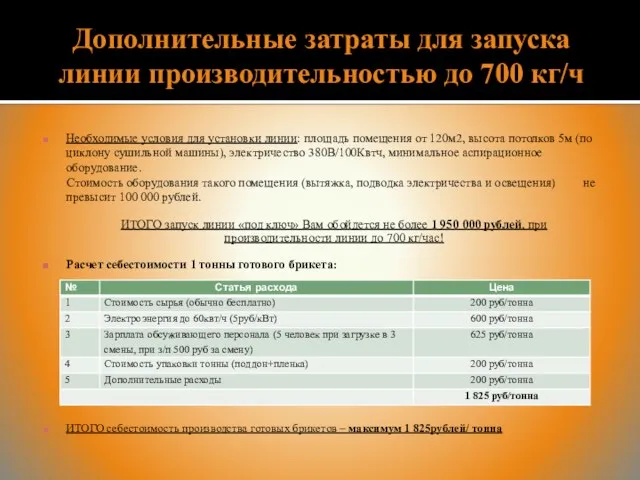
Стоимость оборудования такого помещения (вытяжка, подводка электричества и освещения) не превысит 100 000 рублей.
ИТОГО запуск линии «под ключ» Вам обойдется не более 1 950 000 рублей, при производительности линии до 700 кг/час!
Расчет себестоимости 1 тонны готового брикета:
ИТОГО себестоимость производства готовых брикетов – максимум 1 825рублей/ тонна
Слайд 12Окупаемость проекта (Модель 1)
Модель1.
Пессимистичный расчет окупаемости проекта при работе комплекса 22
Окупаемость проекта (Модель 1)
Модель1.
Пессимистичный расчет окупаемости проекта при работе комплекса 22
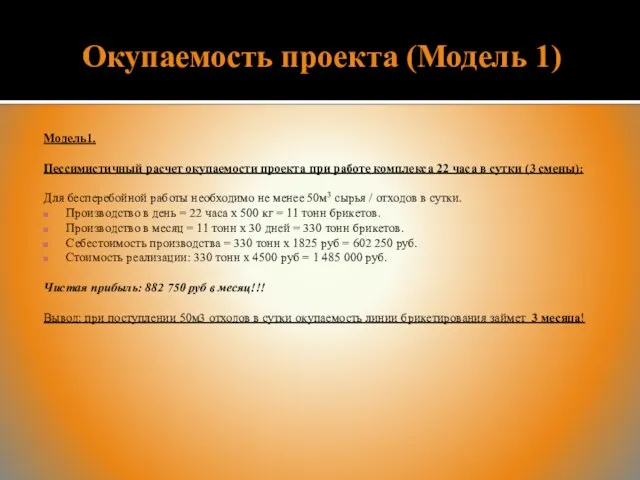
Для бесперебойной работы необходимо не менее 50м3 сырья / отходов в сутки.
Производство в день = 22 часа х 500 кг = 11 тонн брикетов.
Производство в месяц = 11 тонн х 30 дней = 330 тонн брикетов.
Себестоимость производства = 330 тонн х 1825 руб = 602 250 руб.
Стоимость реализации: 330 тонн х 4500 руб = 1 485 000 руб.
Чистая прибыль: 882 750 руб в месяц!!!
Вывод: при поступлении 50м3 отходов в сутки окупаемость линии брикетирования займет 3 месяца!
Слайд 13Окупаемость проекта (Модель 2)
Модель 2.
Пессимистичный расчет окупаемости проекта при работе комплекса
Окупаемость проекта (Модель 2)
Модель 2.
Пессимистичный расчет окупаемости проекта при работе комплекса
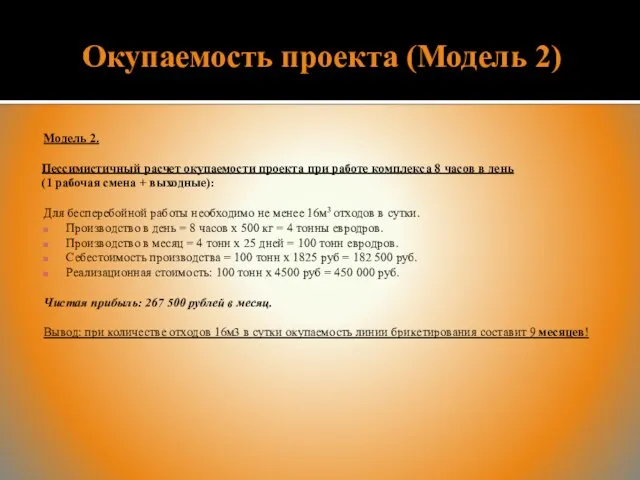
(1 рабочая смена + выходные):
Для бесперебойной работы необходимо не менее 16м3 отходов в сутки.
Производство в день = 8 часов х 500 кг = 4 тонны евродров.
Производство в месяц = 4 тонн х 25 дней = 100 тонн евродров.
Себестоимость производства = 100 тонн х 1825 руб = 182 500 руб.
Реализационная стоимость: 100 тонн х 4500 руб = 450 000 руб.
Чистая прибыль: 267 500 рублей в месяц.
Вывод: при количестве отходов 16м3 в сутки окупаемость линии брикетирования составит 9 месяцев!
Слайд 14Гарантийные обязательства, доставка, монтаж, сроки
На все оборудование, за исключением расходных материалов и
Гарантийные обязательства, доставка, монтаж, сроки
На все оборудование, за исключением расходных материалов и
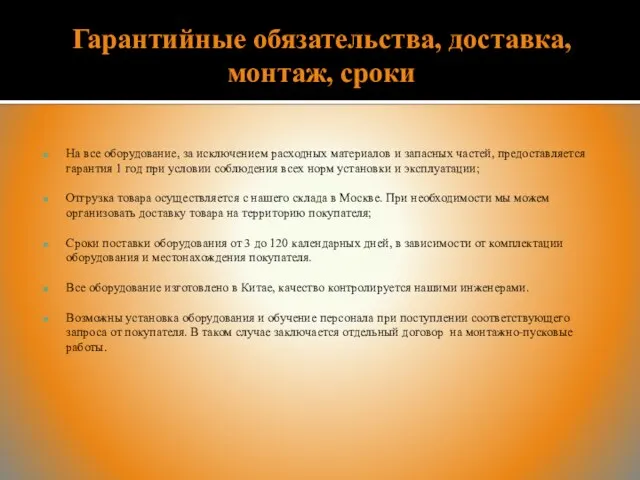
Отгрузка товара осуществляется с нашего склада в Москве. При необходимости мы можем организовать доставку товара на территорию покупателя;
Сроки поставки оборудования от 3 до 120 календарных дней, в зависимости от комплектации оборудования и местонахождения покупателя.
Все оборудование изготовлено в Китае, качество контролируется нашими инженерами.
Возможны установка оборудования и обучение персонала при поступлении соответствующего запроса от покупателя. В таком случае заключается отдельный договор на монтажно-пусковые работы.
Слайд 15Евродрова стандарта Pini-Kay и NESTRO
Топливные брикеты из древесных и агро-отходов являются популярным
Евродрова стандарта Pini-Kay и NESTRO
Топливные брикеты из древесных и агро-отходов являются популярным
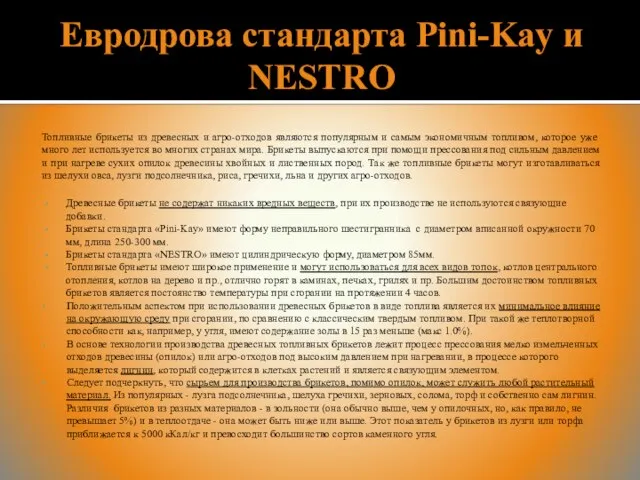
Древесные брикеты не содержат никаких вредных веществ, при их производстве не используются связующие добавки.
Брикеты стандарта «Pini-Kay» имеют форму неправильного шестигранника с диаметром вписанной окружности 70 мм, длина 250-300 мм.
Брикеты стандарта «NESTRO» имеют цилиндрическую форму, диаметром 85мм.
Топливные брикеты имеют широкое применение и могут использоваться для всех видов топок, котлов центрального отопления, котлов на дерево и пр., отлично горят в каминах, печках, грилях и пр. Большим достоинством топливных брикетов является постоянство температуры при сгорании на протяжении 4 часов.
Положительным аспектом при использовании древесных брикетов в виде топлива является их минимальное влияние на окружающую среду при сгорании, по сравнению с классическим твердым топливом. При такой же теплотворной способности как, например, у угля, имеют содержание золы в 15 раз меньше (макс 1.0%).
В основе технологии производства древесных топливных брикетов лежит процесс прессования мелко измельченных отходов древесины (опилок) или агро-отходов под высоким давлением при нагревании, в процессе которого выделяется лигнин, который содержится в клетках растений и является связующим элементом.
Следует подчеркнуть, что сырьем для производства брикетов, помимо опилок, может служить любой растительный материал. Из популярных - лузга подсолнечника, шелуха гречихи, зерновых, солома, торф и собственно сам лигнин. Различия брикетов из разных материалов - в зольности (она обычно выше, чем у опилочных, но, как правило, не превышает 5%) и в теплоотдаче - она может быть ниже или выше. Этот показатель у брикетов из лузги или торфа приближается к 5000 кКал/кг и превосходит большинство сортов каменного угля.
Слайд 16Евродрова стандарта Pini-Kay и NESTRO
Высокая продолжительность горения
Это означает, что по сравнению
Евродрова стандарта Pini-Kay и NESTRO
Высокая продолжительность горения
Это означает, что по сравнению
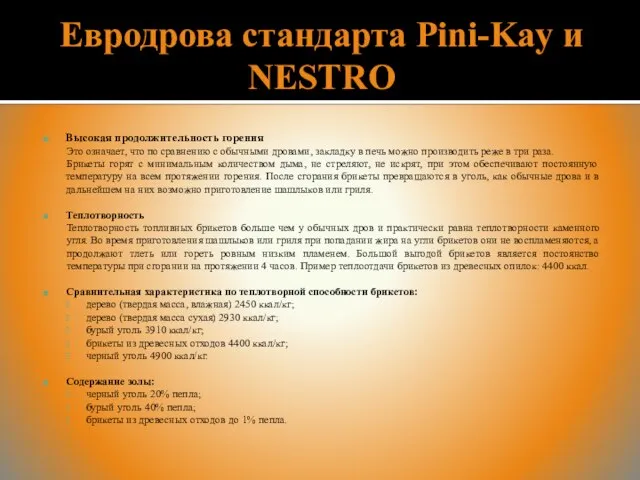
Брикеты горят с минимальным количеством дыма, не стреляют, не искрят, при этом обеспечивают постоянную температуру на всем протяжении горения. После сгорания брикеты превращаются в уголь, как обычные дрова и в дальнейшем на них возможно приготовление шашлыков или гриля.
Теплотворность
Теплотворность топливных брикетов больше чем у обычных дров и практически равна теплотворности каменного угля. Во время приготовления шашлыков или гриля при попадании жира на угли брикетов они не воспламеняются, а продолжают тлеть или гореть ровным низким пламенем. Большой выгодой брикетов является постоянство температуры при сгорании на протяжении 4 часов. Пример теплоотдачи брикетов из древесных опилок: 4400 ккал.
Сравнительная характеристика по теплотворной способности брикетов:
дерево (твердая масса, влажная) 2450 ккал/кг;
дерево (твердая масса сухая) 2930 ккал/кг;
бурый уголь 3910 ккал/кг;
брикеты из древесных отходов 4400 ккал/кг;
черный уголь 4900 ккал/кг.
Cодержание золы:
черный уголь 20% пепла;
бурый уголь 40% пепла;
брикеты из древесных отходов до 1% пепла.