Содержание
- 2. Виробництво інфузійних розчинів (включаючи ЦЗЛ та ВТК) Номенклатура Пускова потужність - 5 млн. фл. / рік
- 3. Серійне виробництво розчинів для інфузій Терміни проведення будівництва
- 4. Контроль у процесі виробництва Вихідна сировина, матеріали, напівпродукти Стадія 1. Підготовка сировини Ваги Стадія 2. Підготовка
- 5. Контроль у процесі виробництва Вихідна сировина, матеріали, напівпродукти Стадія 1. Підготовка сировини Ваги Стадія 2. Підготовка
- 6. Контроль у процесі виробництва Вихідна сировина, матеріали, напівпродукти Стадія 1. Підготовка сировини Ваги Стадія 2. Підготовка
- 7. Контроль у процесі виробництва Вихідна сировина, матеріали, напівпродукти Стадія 1. Підготовка сировини Ваги Стадія 2. Підготовка
- 8. Контроль у процесі виробництва Вихідна сировина, матеріали, напівпродукти Стадія 1. Підготовка сировини Ваги Стадія 2. Підготовка
- 9. Контроль у процесі виробництва Вихідна сировина, матеріали, напівпродукти Стадія 1. Підготовка сировини Ваги Стадія 2. Підготовка
- 10. Річна програма виробництва Річна потужність - 5 млн. фл. / рік (з розрахунку на флакони по
- 11. Розрахунок та вибір основного та допоміжного обладнання Розрахунок ємнісного обладнання. З урахування коефіцієнту заповнення φ необхідно
- 12. Розрахунок кількості основного та допоміжного обладнання Або N=Qріч/(q ∙ Fн), де N – кількість одиниць обладнання;
- 13. 3. Стерилізаційний тунель Nр= n/mτ = 13334 /(3000 ∙ 8) = 0,55 – достатньо одного тунелю.
- 14. 7. Автомат для пакування флаконів у пачки Nр= n/mτ = 13 334 /(5000 ∙ 8) =
- 15. Розрахунки витрат води, пари, електроенергії та стислого повітря Витрати води та пари Всередньому при приготуванні р-ну
- 16. Витрати електроенергії Розрахунок споживання електроенергії для виробництва однієї серії проводиться за формулою: N = Ni ∙
- 17. Вимоги до обладнання Продуктивність Потужність - 5 млн. / рік з розрахунку 100 мл Передбачити збільшення
- 18. Перелік обладнання
- 19. Перелік обладнання
- 20. Ваги Виробник: Техноваги (Україна) Моделі: платформні ТВ1 промислові ТВ-31-4. - Підсилена конструкція ваги та GMP-дизайн; -
- 21. Лінія для мийки флаконів Виробник: Bosch (Німеччина) Модель: RRN 2020 Об’єм: 100-500 мл Продуктивність – 2000-5000
- 22. Стерилізаційний тунель Виробник: Neri S.p.A. (Італія) Продуктивність – до 3000 фл. / год., потужність – 32
- 23. Установка багатоступеневої дистиляції Виробник: STERIS Life Sciences Модель: Finn-Aqua Продуктивність: 500-750 л/год Виробник: F&L (США) Модель:
- 24. Реактори для виробництва інфузійних розчинів Виробник: LabPHARMA (Чехія) Швидкість:100-150 об/хв (6 кВт) Об’єм: 5000-8000л Продуктивність: до
- 25. Фільтри для рідин Матриця градуйованою щільності картріджних фільтрів дозволяє обернути в один картридж носій з двома
- 26. Машина для наповнення і закупорювання флаконів Виробник: ROTA (Німеччина) Продуктивність – 2-5 тис. фл / год
- 27. Автоклави Виробник: FEDEGARI (Італія) Модель: 1495 ЛТР FOF 3/4 з полірованої нержавіючої сталі Продуктивність – 3200
- 28. Машина для етикетування Виробник: Marchesini (Італія) Модель: Neri RL 500 Продуктивність – 2500-6000 фл./год. (залежно від
- 30. Скачать презентацию
Слайд 2Виробництво інфузійних розчинів
(включаючи ЦЗЛ та ВТК)
Номенклатура
Пускова потужність - 5 млн. фл.
Виробництво інфузійних розчинів
(включаючи ЦЗЛ та ВТК)
Номенклатура
Пускова потужність - 5 млн. фл.
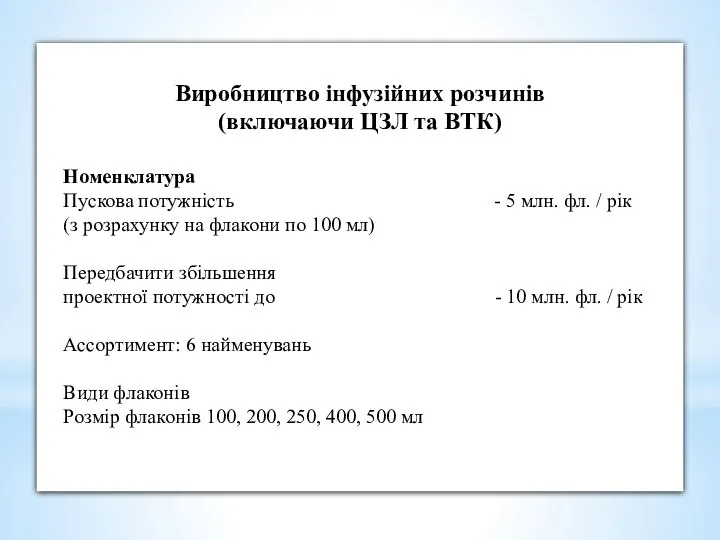
(з розрахунку на флакони по 100 мл)
Передбачити збільшення
проектної потужності до - 10 млн. фл. / рік
Ассортимент: 6 найменувань
Види флаконів
Розмір флаконів 100, 200, 250, 400, 500 мл
Слайд 3Серійне виробництво розчинів для інфузій
Терміни проведення будівництва
Серійне виробництво розчинів для інфузій
Терміни проведення будівництва
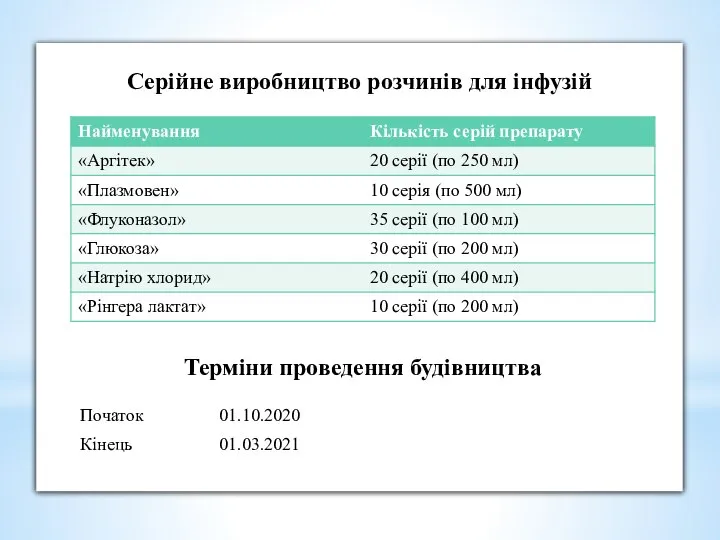
Слайд 4Контроль у процесі виробництва
Вихідна сировина, матеріали, напівпродукти
Стадія 1. Підготовка сировини
Ваги
Стадія 2. Підготовка
Контроль у процесі виробництва
Вихідна сировина, матеріали, напівпродукти
Стадія 1. Підготовка сировини
Ваги
Стадія 2. Підготовка
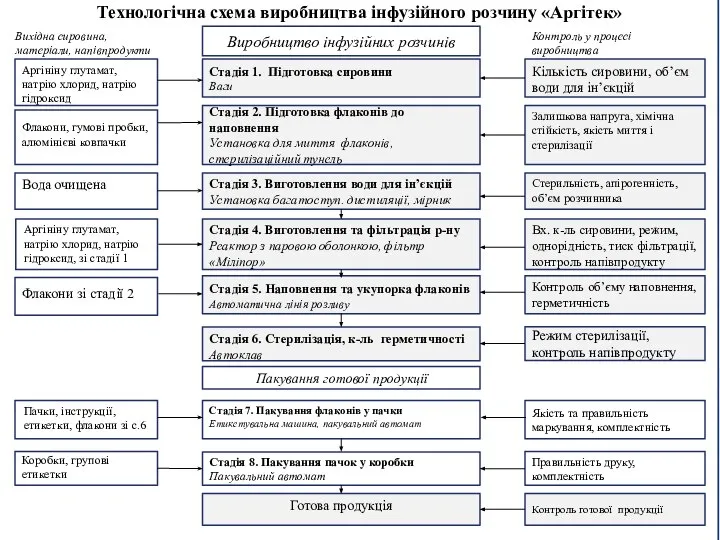
Установка для миття флаконів, стерилізаційний тунель
Кількість сировини, об’єм води для ін’єкцій
Залишкова напруга, хімічна стійкість, якість миття і стерилізації
Аргініну глутамат, натрію хлорид, натрію гідроксид
Стадія 3. Виготовлення води для ін’єкцій
Установка багатоступ. дистиляції, мірник
Флакони, гумові пробки, алюмінієві ковпачки
Стерильність, апірогенність, об’єм розчинника
Стадія 4. Виготовлення та фільтрація р-ну
Реактор з паровою оболонкою, фільтр «Міліпор»
Вх. к-ль сировини, режим, однорідність, тиск фільтрації, контроль напівпродукту
Вода очищена
Стадія 5. Наповнення та укупорка флаконів
Автоматична лінія розливу
Контроль об’єму наповнення, герметичність
Флакони зі стадії 2
Стадія 7. Пакування флаконів у пачки
Етикетувальна машина, пакувальний автомат
Пачки, інструкції, етикетки, флакони зі с.6
Якість та правильність маркування, комплектність
Стадія 8. Пакування пачок у коробки
Пакувальний автомат
Коробки, групові етикетки
Правильність друку, комплектність
Готова продукція
Контроль готової продукції
Стадія 6. Стерилізація, к-ль герметичності
Автоклав
Режим стерилізації, контроль напівпродукту
Технологічна схема виробництва інфузійного розчину «Аргітек»
Виробництво інфузійних розчинів
Аргініну глутамат, натрію хлорид, натрію гідроксид, зі стадії 1
Пакування готової продукції
Слайд 5Контроль у процесі виробництва
Вихідна сировина, матеріали, напівпродукти
Стадія 1. Підготовка сировини
Ваги
Стадія 2. Підготовка
Контроль у процесі виробництва
Вихідна сировина, матеріали, напівпродукти
Стадія 1. Підготовка сировини
Ваги
Стадія 2. Підготовка
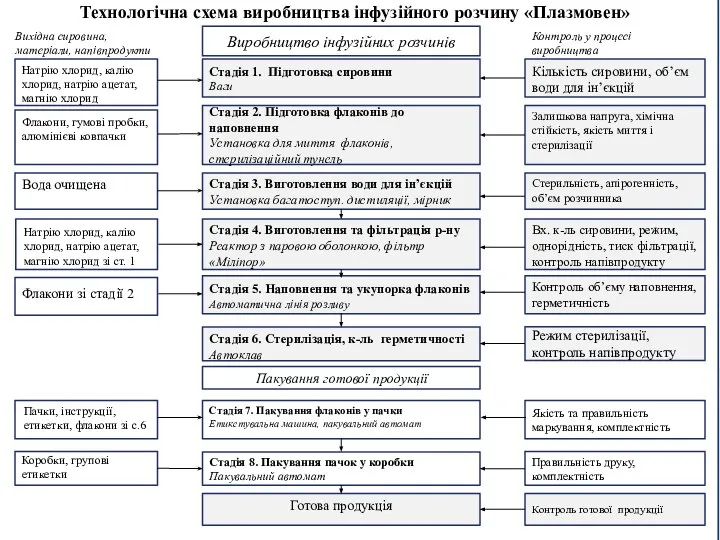
Установка для миття флаконів, стерилізаційний тунель
Кількість сировини, об’єм води для ін’єкцій
Залишкова напруга, хімічна стійкість, якість миття і стерилізації
Натрію хлорид, калію хлорид, натрію ацетат, магнію хлорид
Стадія 3. Виготовлення води для ін’єкцій
Установка багатоступ. дистиляції, мірник
Флакони, гумові пробки, алюмінієві ковпачки
Стерильність, апірогенність, об’єм розчинника
Стадія 4. Виготовлення та фільтрація р-ну
Реактор з паровою оболонкою, фільтр «Міліпор»
Вх. к-ль сировини, режим, однорідність, тиск фільтрації, контроль напівпродукту
Вода очищена
Стадія 5. Наповнення та укупорка флаконів
Автоматична лінія розливу
Контроль об’єму наповнення, герметичність
Флакони зі стадії 2
Стадія 7. Пакування флаконів у пачки
Етикетувальна машина, пакувальний автомат
Пачки, інструкції, етикетки, флакони зі с.6
Якість та правильність маркування, комплектність
Стадія 8. Пакування пачок у коробки
Пакувальний автомат
Коробки, групові етикетки
Правильність друку, комплектність
Готова продукція
Контроль готової продукції
Стадія 6. Стерилізація, к-ль герметичності
Автоклав
Режим стерилізації, контроль напівпродукту
Технологічна схема виробництва інфузійного розчину «Плазмовен»
Виробництво інфузійних розчинів
Натрію хлорид, калію хлорид, натрію ацетат, магнію хлорид зі ст. 1
Пакування готової продукції
Слайд 6Контроль у процесі виробництва
Вихідна сировина, матеріали, напівпродукти
Стадія 1. Підготовка сировини
Ваги
Стадія 2. Підготовка
Контроль у процесі виробництва
Вихідна сировина, матеріали, напівпродукти
Стадія 1. Підготовка сировини
Ваги
Стадія 2. Підготовка
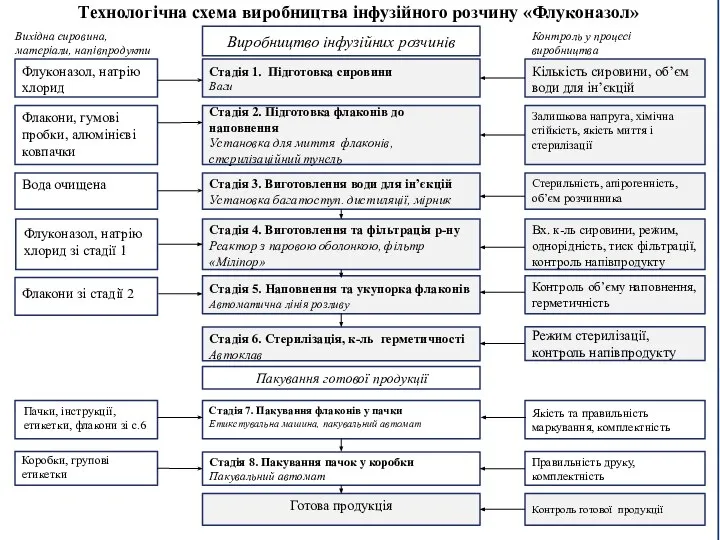
Установка для миття флаконів, стерилізаційний тунель
Кількість сировини, об’єм води для ін’єкцій
Залишкова напруга, хімічна стійкість, якість миття і стерилізації
Флуконазол, натрію хлорид
Стадія 3. Виготовлення води для ін’єкцій
Установка багатоступ. дистиляції, мірник
Флакони, гумові пробки, алюмінієві ковпачки
Стерильність, апірогенність, об’єм розчинника
Стадія 4. Виготовлення та фільтрація р-ну
Реактор з паровою оболонкою, фільтр «Міліпор»
Вх. к-ль сировини, режим, однорідність, тиск фільтрації, контроль напівпродукту
Вода очищена
Стадія 5. Наповнення та укупорка флаконів
Автоматична лінія розливу
Контроль об’єму наповнення, герметичність
Флакони зі стадії 2
Стадія 7. Пакування флаконів у пачки
Етикетувальна машина, пакувальний автомат
Пачки, інструкції, етикетки, флакони зі с.6
Якість та правильність маркування, комплектність
Стадія 8. Пакування пачок у коробки
Пакувальний автомат
Коробки, групові етикетки
Правильність друку, комплектність
Готова продукція
Контроль готової продукції
Стадія 6. Стерилізація, к-ль герметичності
Автоклав
Режим стерилізації, контроль напівпродукту
Технологічна схема виробництва інфузійного розчину «Флуконазол»
Виробництво інфузійних розчинів
Флуконазол, натрію хлорид зі стадії 1
Пакування готової продукції
Слайд 7Контроль у процесі виробництва
Вихідна сировина, матеріали, напівпродукти
Стадія 1. Підготовка сировини
Ваги
Стадія 2. Підготовка
Контроль у процесі виробництва
Вихідна сировина, матеріали, напівпродукти
Стадія 1. Підготовка сировини
Ваги
Стадія 2. Підготовка
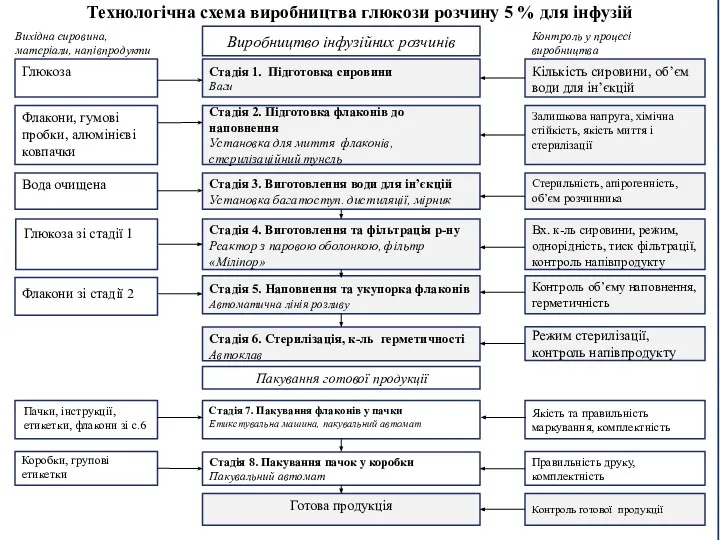
Установка для миття флаконів, стерилізаційний тунель
Кількість сировини, об’єм води для ін’єкцій
Залишкова напруга, хімічна стійкість, якість миття і стерилізації
Глюкоза
Стадія 3. Виготовлення води для ін’єкцій
Установка багатоступ. дистиляції, мірник
Флакони, гумові пробки, алюмінієві ковпачки
Стерильність, апірогенність, об’єм розчинника
Стадія 4. Виготовлення та фільтрація р-ну
Реактор з паровою оболонкою, фільтр «Міліпор»
Вх. к-ль сировини, режим, однорідність, тиск фільтрації, контроль напівпродукту
Вода очищена
Стадія 5. Наповнення та укупорка флаконів
Автоматична лінія розливу
Контроль об’єму наповнення, герметичність
Флакони зі стадії 2
Стадія 7. Пакування флаконів у пачки
Етикетувальна машина, пакувальний автомат
Пачки, інструкції, етикетки, флакони зі с.6
Якість та правильність маркування, комплектність
Стадія 8. Пакування пачок у коробки
Пакувальний автомат
Коробки, групові етикетки
Правильність друку, комплектність
Готова продукція
Контроль готової продукції
Стадія 6. Стерилізація, к-ль герметичності
Автоклав
Режим стерилізації, контроль напівпродукту
Технологічна схема виробництва глюкози розчину 5 % для інфузій
Виробництво інфузійних розчинів
Глюкоза зі стадії 1
Пакування готової продукції
Слайд 8Контроль у процесі виробництва
Вихідна сировина, матеріали, напівпродукти
Стадія 1. Підготовка сировини
Ваги
Стадія 2. Підготовка
Контроль у процесі виробництва
Вихідна сировина, матеріали, напівпродукти
Стадія 1. Підготовка сировини
Ваги
Стадія 2. Підготовка
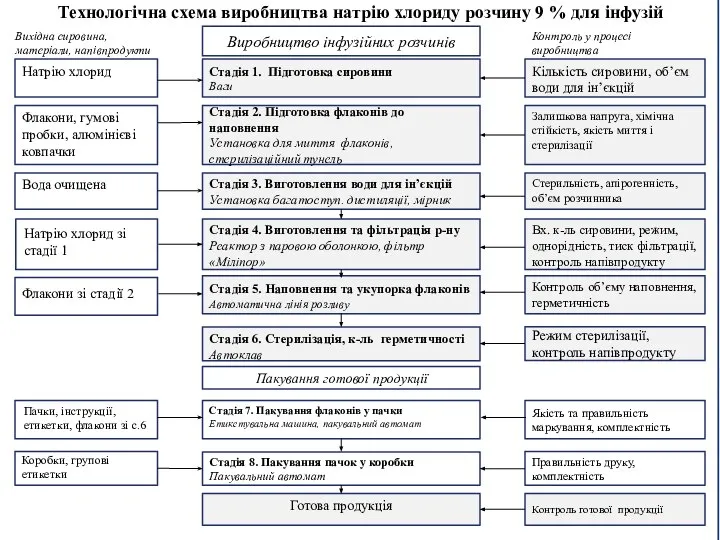
Установка для миття флаконів, стерилізаційний тунель
Кількість сировини, об’єм води для ін’єкцій
Залишкова напруга, хімічна стійкість, якість миття і стерилізації
Натрію хлорид
Стадія 3. Виготовлення води для ін’єкцій
Установка багатоступ. дистиляції, мірник
Флакони, гумові пробки, алюмінієві ковпачки
Стерильність, апірогенність, об’єм розчинника
Стадія 4. Виготовлення та фільтрація р-ну
Реактор з паровою оболонкою, фільтр «Міліпор»
Вх. к-ль сировини, режим, однорідність, тиск фільтрації, контроль напівпродукту
Вода очищена
Стадія 5. Наповнення та укупорка флаконів
Автоматична лінія розливу
Контроль об’єму наповнення, герметичність
Флакони зі стадії 2
Стадія 7. Пакування флаконів у пачки
Етикетувальна машина, пакувальний автомат
Пачки, інструкції, етикетки, флакони зі с.6
Якість та правильність маркування, комплектність
Стадія 8. Пакування пачок у коробки
Пакувальний автомат
Коробки, групові етикетки
Правильність друку, комплектність
Готова продукція
Контроль готової продукції
Стадія 6. Стерилізація, к-ль герметичності
Автоклав
Режим стерилізації, контроль напівпродукту
Технологічна схема виробництва натрію хлориду розчину 9 % для інфузій
Виробництво інфузійних розчинів
Натрію хлорид зі стадії 1
Пакування готової продукції
Слайд 9Контроль у процесі виробництва
Вихідна сировина, матеріали, напівпродукти
Стадія 1. Підготовка сировини
Ваги
Стадія 2. Підготовка
Контроль у процесі виробництва
Вихідна сировина, матеріали, напівпродукти
Стадія 1. Підготовка сировини
Ваги
Стадія 2. Підготовка
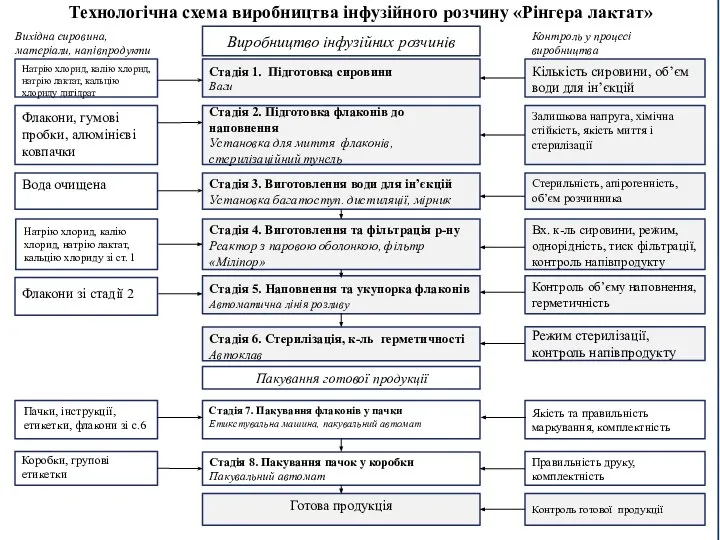
Установка для миття флаконів, стерилізаційний тунель
Кількість сировини, об’єм води для ін’єкцій
Залишкова напруга, хімічна стійкість, якість миття і стерилізації
Натрію хлорид, калію хлорид, натрію лактат, кальцію хлориду дигідрат
Стадія 3. Виготовлення води для ін’єкцій
Установка багатоступ. дистиляції, мірник
Флакони, гумові пробки, алюмінієві ковпачки
Стерильність, апірогенність, об’єм розчинника
Стадія 4. Виготовлення та фільтрація р-ну
Реактор з паровою оболонкою, фільтр «Міліпор»
Вх. к-ль сировини, режим, однорідність, тиск фільтрації, контроль напівпродукту
Вода очищена
Стадія 5. Наповнення та укупорка флаконів
Автоматична лінія розливу
Контроль об’єму наповнення, герметичність
Флакони зі стадії 2
Стадія 7. Пакування флаконів у пачки
Етикетувальна машина, пакувальний автомат
Пачки, інструкції, етикетки, флакони зі с.6
Якість та правильність маркування, комплектність
Стадія 8. Пакування пачок у коробки
Пакувальний автомат
Коробки, групові етикетки
Правильність друку, комплектність
Готова продукція
Контроль готової продукції
Стадія 6. Стерилізація, к-ль герметичності
Автоклав
Режим стерилізації, контроль напівпродукту
Технологічна схема виробництва інфузійного розчину «Рінгера лактат»
Виробництво інфузійних розчинів
Натрію хлорид, калію хлорид, натрію лактат, кальцію хлориду зі ст. 1
Пакування готової продукції
Слайд 10
Річна програма виробництва
Річна потужність - 5 млн. фл. / рік (з розрахунку
Річна програма виробництва
Річна потужність - 5 млн. фл. / рік (з розрахунку
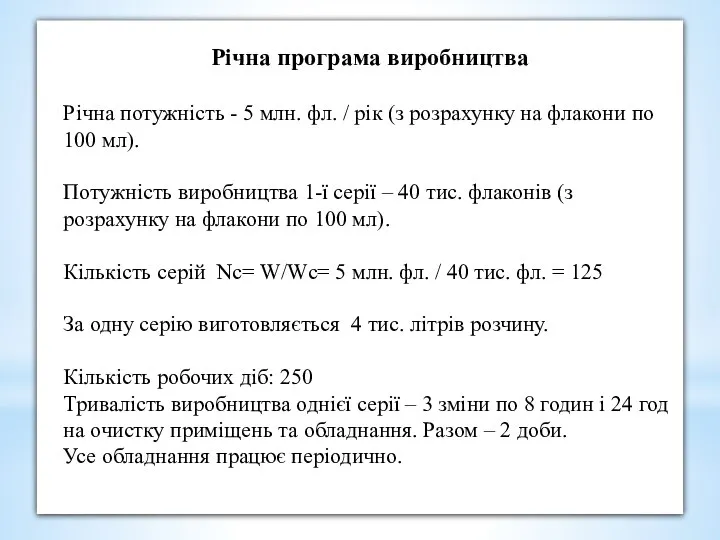
Потужність виробництва 1-ї серії – 40 тис. флаконів (з розрахунку на флакони по 100 мл).
Кількість серій Nс= W/Wc= 5 млн. фл. / 40 тис. фл. = 125
За одну серію виготовляється 4 тис. літрів розчину.
Кількість робочих діб: 250
Тривалість виробництва однієї серії – 3 зміни по 8 годин і 24 год на очистку приміщень та обладнання. Разом – 2 доби.
Усе обладнання працює періодично.
Слайд 11
Розрахунок та вибір основного та допоміжного обладнання
Розрахунок ємнісного обладнання.
З урахування коефіцієнту
Розрахунок та вибір основного та допоміжного обладнання
Розрахунок ємнісного обладнання.
З урахування коефіцієнту
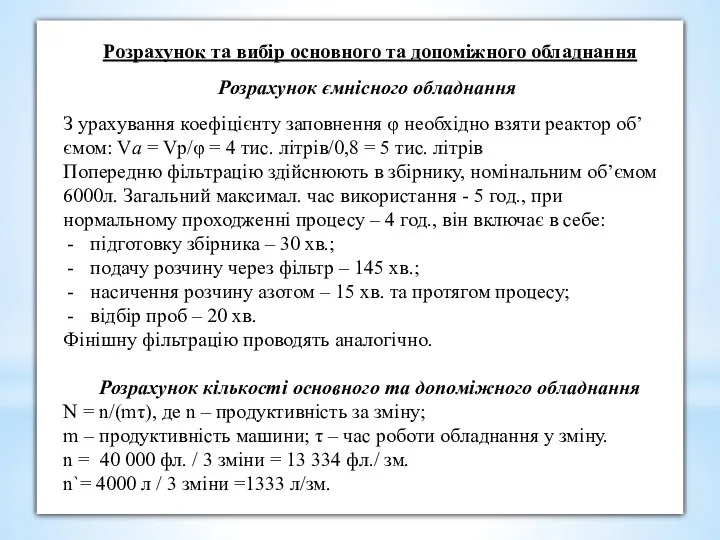
Попередню фільтрацію здійснюють в збірнику, номінальним об’ємом 6000л. Загальний максимал. час використання - 5 год., при нормальному проходженні процесу – 4 год., він включає в себе:
підготовку збірника – 30 хв.;
подачу розчину через фільтр – 145 хв.;
насичення розчину азотом – 15 хв. та протягом процесу;
відбір проб – 20 хв.
Фінішну фільтрацію проводять аналогічно.
Розрахунок кількості основного та допоміжного обладнання
N = n/(mτ), де n – продуктивність за зміну;
m – продуктивність машини; τ – час роботи обладнання у зміну.
n = 40 000 фл. / 3 зміни = 13 334 фл./ зм.
n`= 4000 л / 3 зміни =1333 л/зм.
Слайд 12
Розрахунок кількості основного та допоміжного обладнання
Або N=Qріч/(q ∙ Fн), де N –
Розрахунок кількості основного та допоміжного обладнання
Або N=Qріч/(q ∙ Fн), де N –
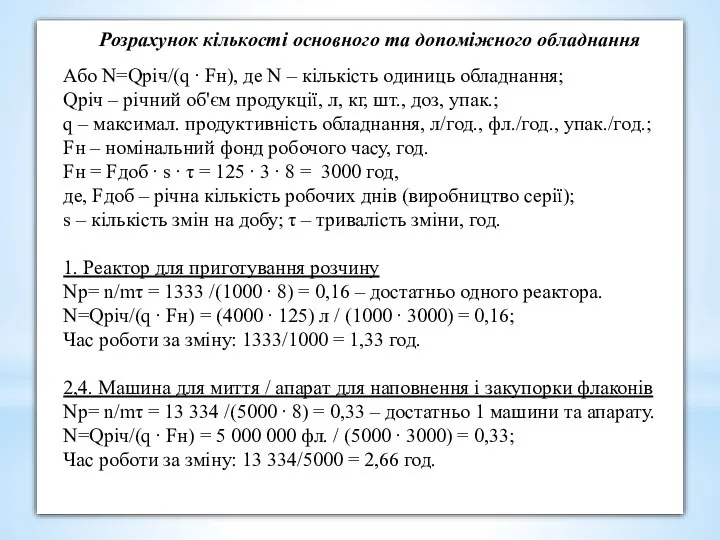
Qріч – річний об'єм продукції, л, кг, шт., доз, упак.;
q – максимал. продуктивність обладнання, л/год., фл./год., упак./год.;
Fн – номінальний фонд робочого часу, год.
Fн = Fдоб ∙ ѕ ∙ τ = 125 ∙ 3 ∙ 8 = 3000 год,
де, Fдоб – річна кількість робочих днів (виробництво серії);
ѕ – кількість змін на добу; τ – тривалість зміни, год.
1. Реактор для приготування розчину
Nр= n/mτ = 1333 /(1000 ∙ 8) = 0,16 – достатньо одного реактора.
N=Qріч/(q ∙ Fн) = (4000 ∙ 125) л / (1000 ∙ 3000) = 0,16;
Час роботи за зміну: 1333/1000 = 1,33 год.
2,4. Машина для миття / апарат для наповнення і закупорки флаконів
Nр= n/mτ = 13 334 /(5000 ∙ 8) = 0,33 – достатньо 1 машини та апарату.
N=Qріч/(q ∙ Fн) = 5 000 000 фл. / (5000 ∙ 3000) = 0,33;
Час роботи за зміну: 13 334/5000 = 2,66 год.
Слайд 13
3. Стерилізаційний тунель
Nр= n/mτ = 13334 /(3000 ∙ 8) = 0,55 –
3. Стерилізаційний тунель
Nр= n/mτ = 13334 /(3000 ∙ 8) = 0,55 –
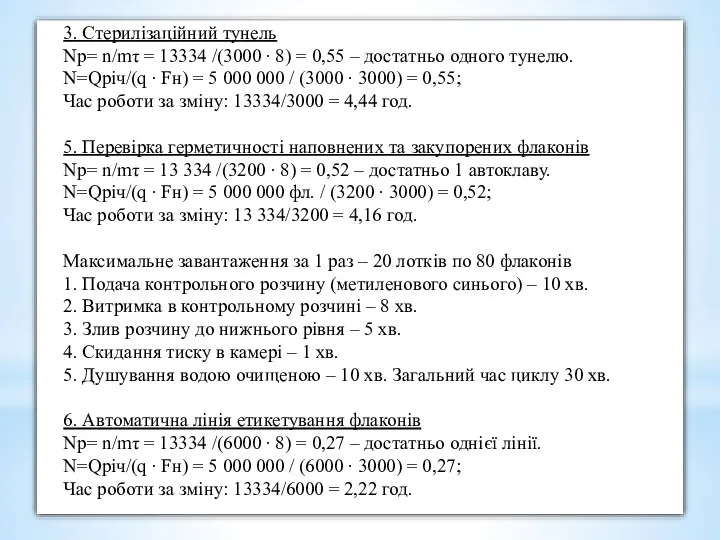
N=Qріч/(q ∙ Fн) = 5 000 000 / (3000 ∙ 3000) = 0,55;
Час роботи за зміну: 13334/3000 = 4,44 год.
5. Перевірка герметичності наповнених та закупорених флаконів
Nр= n/mτ = 13 334 /(3200 ∙ 8) = 0,52 – достатньо 1 автоклаву.
N=Qріч/(q ∙ Fн) = 5 000 000 фл. / (3200 ∙ 3000) = 0,52;
Час роботи за зміну: 13 334/3200 = 4,16 год.
Максимальне завантаження за 1 раз – 20 лотків по 80 флаконів
1. Подача контрольного розчину (метиленового синього) – 10 хв.
2. Витримка в контрольному розчині – 8 хв.
3. Злив розчину до нижнього рівня – 5 хв.
4. Скидання тиску в камері – 1 хв.
5. Душування водою очищеною – 10 хв. Загальний час циклу 30 хв.
6. Автоматична лінія етикетування флаконів
Nр= n/mτ = 13334 /(6000 ∙ 8) = 0,27 – достатньо однієї лінії.
N=Qріч/(q ∙ Fн) = 5 000 000 / (6000 ∙ 3000) = 0,27;
Час роботи за зміну: 13334/6000 = 2,22 год.
Слайд 14
7. Автомат для пакування флаконів у пачки
Nр= n/mτ = 13 334 /(5000
7. Автомат для пакування флаконів у пачки
Nр= n/mτ = 13 334 /(5000
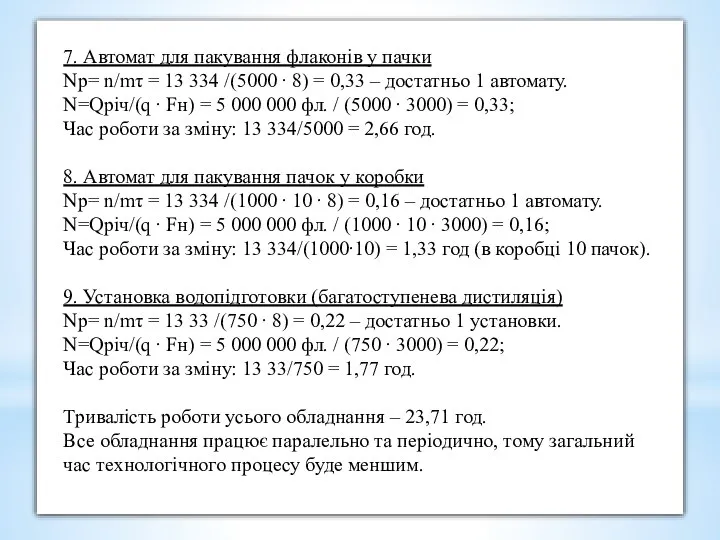
N=Qріч/(q ∙ Fн) = 5 000 000 фл. / (5000 ∙ 3000) = 0,33;
Час роботи за зміну: 13 334/5000 = 2,66 год.
8. Автомат для пакування пачок у коробки
Nр= n/mτ = 13 334 /(1000 ∙ 10 ∙ 8) = 0,16 – достатньо 1 автомату.
N=Qріч/(q ∙ Fн) = 5 000 000 фл. / (1000 ∙ 10 ∙ 3000) = 0,16;
Час роботи за зміну: 13 334/(1000∙10) = 1,33 год (в коробці 10 пачок).
9. Установка водопідготовки (багатоступенева дистиляція)
Nр= n/mτ = 13 33 /(750 ∙ 8) = 0,22 – достатньо 1 установки.
N=Qріч/(q ∙ Fн) = 5 000 000 фл. / (750 ∙ 3000) = 0,22;
Час роботи за зміну: 13 33/750 = 1,77 год.
Тривалість роботи усього обладнання – 23,71 год.
Все обладнання працює паралельно та періодично, тому загальний
час технологічного процесу буде меншим.
Слайд 15
Розрахунки витрат води, пари, електроенергії та стислого повітря
Витрати води та пари
Всередньому
Розрахунки витрат води, пари, електроенергії та стислого повітря
Витрати води та пари
Всередньому
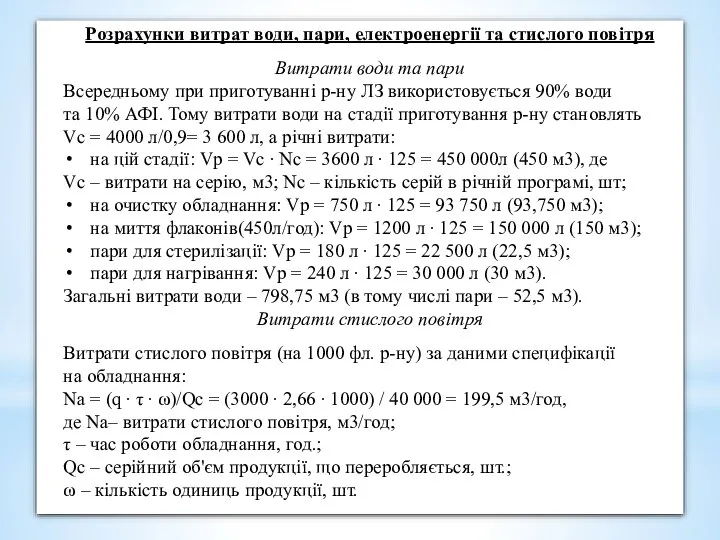
та 10% АФІ. Тому витрати води на стадії приготування р-ну становлять
Vc = 4000 л/0,9= 3 600 л, а річні витрати:
на цій стадії: Vp = Vc ∙ Nc = 3600 л ∙ 125 = 450 000л (450 м3), де
Vс – витрати на серію, м3; Nс – кількість серій в річній програмі, шт;
на очистку обладнання: Vр = 750 л ∙ 125 = 93 750 л (93,750 м3);
на миття флаконів(450л/год): Vр = 1200 л ∙ 125 = 150 000 л (150 м3);
пари для стерилізації: Vр = 180 л ∙ 125 = 22 500 л (22,5 м3);
пари для нагрівання: Vр = 240 л ∙ 125 = 30 000 л (30 м3).
Загальні витрати води – 798,75 м3 (в тому числі пари – 52,5 м3).
Витрати стислого повітря
Витрати стислого повітря (на 1000 фл. р-ну) за даними специфікації
на обладнання:
Nа = (q ∙ τ ∙ ω)/Qc = (3000 ∙ 2,66 ∙ 1000) / 40 000 = 199,5 м3/год,
де Nа– витрати стислого повітря, м3/год;
τ – час роботи обладнання, год.;
Qс – серійний об'єм продукції, що переробляється, шт.;
ω – кількість одиниць продукції, шт.
Слайд 16
Витрати електроенергії
Розрахунок споживання електроенергії для виробництва однієї серії проводиться за формулою: N
Витрати електроенергії
Розрахунок споживання електроенергії для виробництва однієї серії проводиться за формулою: N
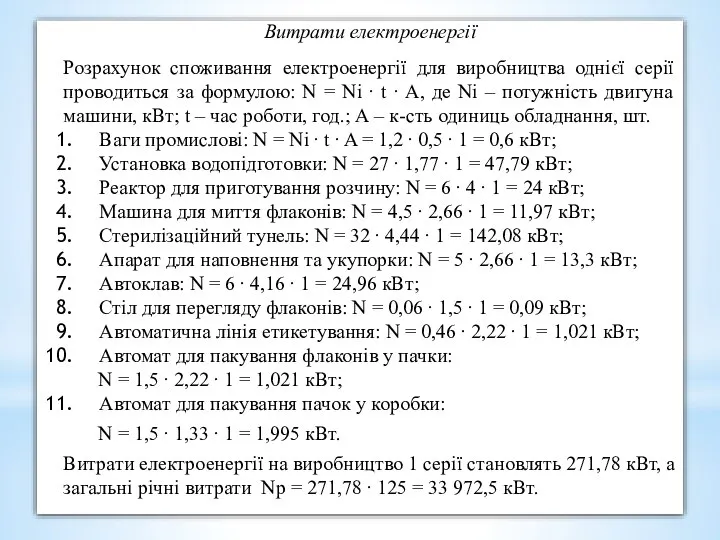
Ваги промислові: N = Ni ∙ t ∙ A = 1,2 ∙ 0,5 ∙ 1 = 0,6 кВт;
Установка водопідготовки: N = 27 ∙ 1,77 ∙ 1 = 47,79 кВт;
Реактор для приготування розчину: N = 6 ∙ 4 ∙ 1 = 24 кВт;
Машина для миття флаконів: N = 4,5 ∙ 2,66 ∙ 1 = 11,97 кВт;
Стерилізаційний тунель: N = 32 ∙ 4,44 ∙ 1 = 142,08 кВт;
Апарат для наповнення та укупорки: N = 5 ∙ 2,66 ∙ 1 = 13,3 кВт;
Автоклав: N = 6 ∙ 4,16 ∙ 1 = 24,96 кВт;
Стіл для перегляду флаконів: N = 0,06 ∙ 1,5 ∙ 1 = 0,09 кВт;
Автоматична лінія етикетування: N = 0,46 ∙ 2,22 ∙ 1 = 1,021 кВт;
Автомат для пакування флаконів у пачки:
N = 1,5 ∙ 2,22 ∙ 1 = 1,021 кВт;
Автомат для пакування пачок у коробки:
N = 1,5 ∙ 1,33 ∙ 1 = 1,995 кВт.
Витрати електроенергії на виробництво 1 серії становлять 271,78 кВт, а загальні річні витрати Np = 271,78 ∙ 125 = 33 972,5 кВт.
Слайд 17Вимоги до обладнання
Продуктивність
Потужність - 5 млн. / рік з розрахунку 100 мл
Передбачити
Вимоги до обладнання
Продуктивність
Потужність - 5 млн. / рік з розрахунку 100 мл
Передбачити

Слайд 18Перелік обладнання
Перелік обладнання
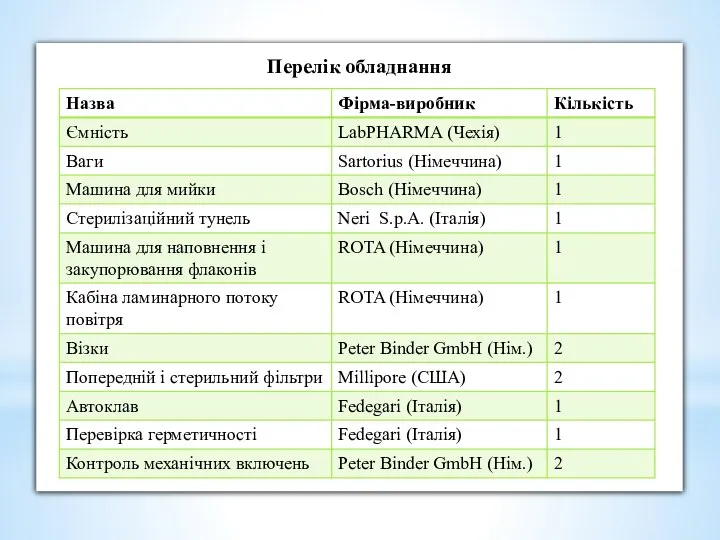
Слайд 19Перелік обладнання
Перелік обладнання
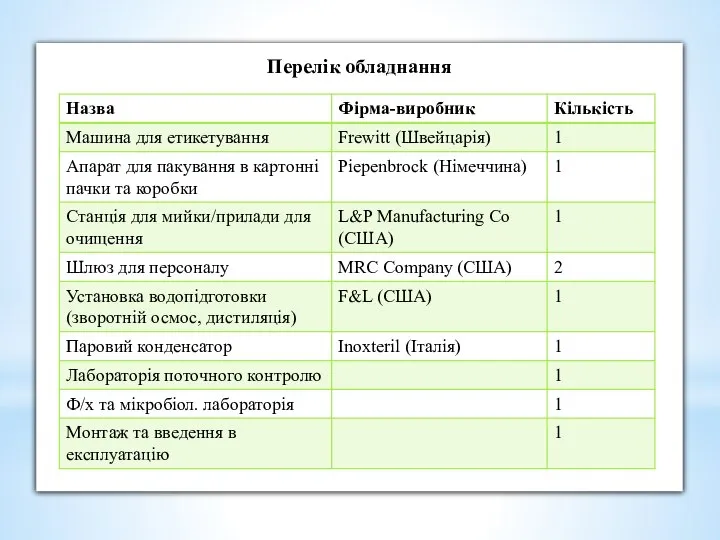
Слайд 20Ваги
Виробник: Техноваги (Україна)
Моделі:
платформні ТВ1
промислові ТВ-31-4.
- Підсилена конструкція ваги та GMP-дизайн;
-
Ваги
Виробник: Техноваги (Україна)
Моделі:
платформні ТВ1
промислові ТВ-31-4.
- Підсилена конструкція ваги та GMP-дизайн; -
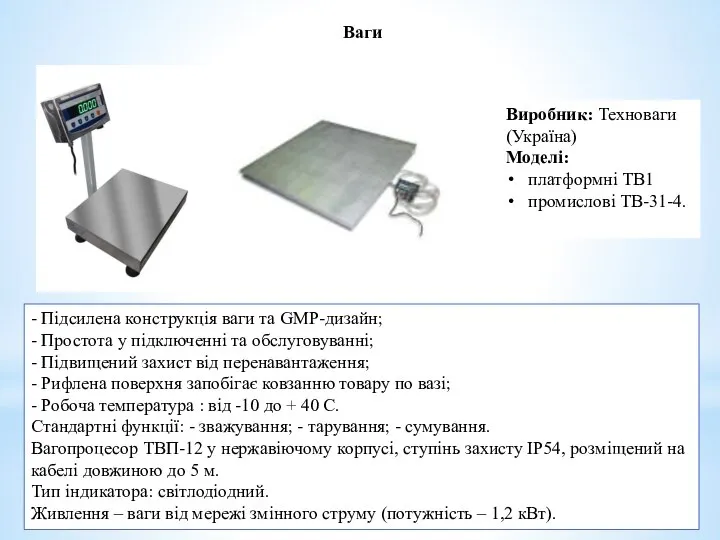
Слайд 21Лінія для мийки флаконів
Виробник: Bosch (Німеччина)
Модель: RRN 2020
Об’єм: 100-500 мл
Продуктивність – 2000-5000
Лінія для мийки флаконів
Виробник: Bosch (Німеччина)
Модель: RRN 2020
Об’єм: 100-500 мл
Продуктивність – 2000-5000
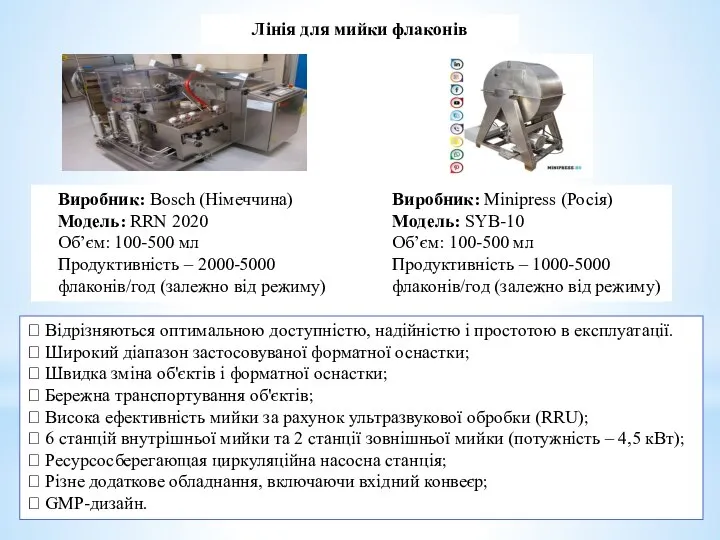
Відрізняються оптимальною доступністю, надійністю і простотою в експлуатації.
Широкий діапазон застосовуваної форматної оснастки;
Швидка зміна об'єктів і форматної оснастки;
Бережна транспортування об'єктів;
Висока ефективність мийки за рахунок ультразвукової обробки (RRU);
6 станцій внутрішньої мийки та 2 станції зовнішньої мийки (потужність – 4,5 кВт);
Ресурсосберегающая циркуляційна насосна станція;
Різне додаткове обладнання, включаючи вхідний конвеєр;
GMP-дизайн.
Виробник: Minipress (Росія)
Модель: SYB-10
Об’єм: 100-500 мл
Продуктивність – 1000-5000 флаконів/год (залежно від режиму)
Слайд 22Стерилізаційний тунель
Виробник: Neri S.p.A. (Італія)
Продуктивність – до 3000 фл. / год., потужність
Стерилізаційний тунель
Виробник: Neri S.p.A. (Італія)
Продуктивність – до 3000 фл. / год., потужність
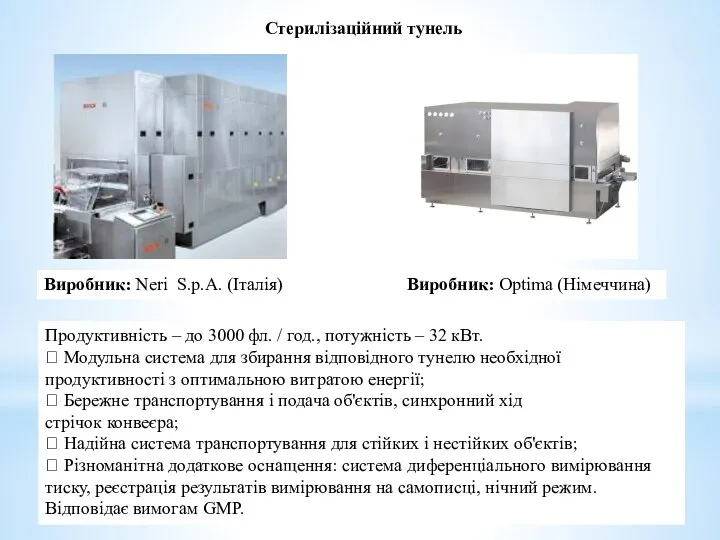
Модульна система для збирання відповідного тунелю необхідної
продуктивності з оптимальною витратою енергії;
Бережне транспортування і подача об'єктів, синхронний хід
стрічок конвеєра;
Надійна система транспортування для стійких і нестійких об'єктів;
Різноманітна додаткове оснащення: система диференціального вимірювання тиску, реєстрація результатів вимірювання на самописці, нічний режим.
Відповідає вимогам GMP.
Виробник: Optima (Німеччина)
Слайд 23Установка багатоступеневої дистиляції
Виробник: STERIS Life Sciences
Модель: Finn-Aqua
Продуктивність: 500-750 л/год
Виробник: F&L (США)
Модель:
Установка багатоступеневої дистиляції
Виробник: STERIS Life Sciences
Модель: Finn-Aqua
Продуктивність: 500-750 л/год
Виробник: F&L (США)
Модель:
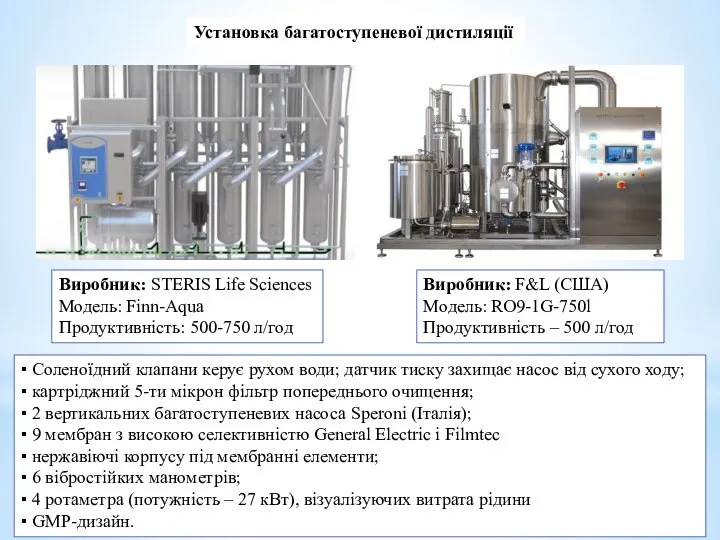
Продуктивність – 500 л/год
▪ Соленоїдний клапани керує рухом води; датчик тиску захищає насос від сухого ходу;
▪ картріджний 5-ти мікрон фільтр попереднього очищення;
▪ 2 вертикальних багатоступеневих насоса Speroni (Італія);
▪ 9 мембран з високою селективністю General Electric і Filmtec
▪ нержавіючі корпусу під мембранні елементи;
▪ 6 вібростійких манометрів;
▪ 4 ротаметра (потужність – 27 кВт), візуалізуючих витрата рідини
▪ GMP-дизайн.
Слайд 24Реактори для виробництва інфузійних розчинів
Виробник: LabPHARMA (Чехія)
Швидкість:100-150 об/хв (6 кВт)
Об’єм: 5000-8000л
Продуктивність: до
Реактори для виробництва інфузійних розчинів
Виробник: LabPHARMA (Чехія)
Швидкість:100-150 об/хв (6 кВт)
Об’єм: 5000-8000л
Продуктивність: до
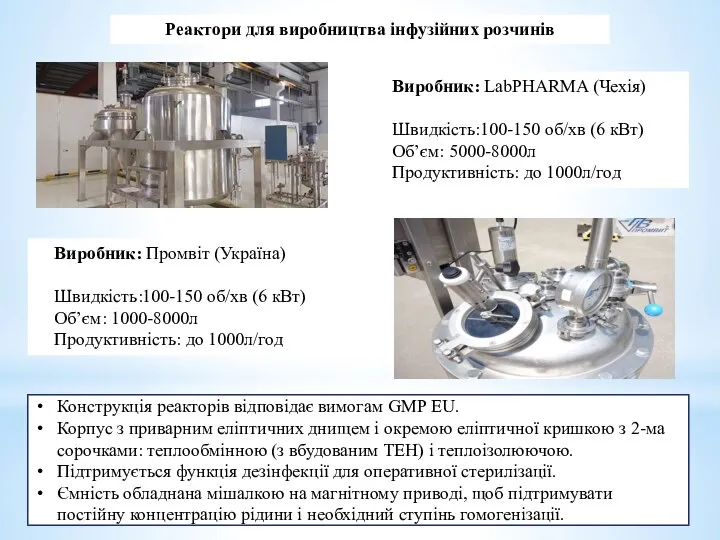
Виробник: Промвіт (Україна)
Швидкість:100-150 об/хв (6 кВт)
Об’єм: 1000-8000л
Продуктивність: до 1000л/год
Конструкція реакторів відповідає вимогам GMP EU.
Корпус з приварним еліптичних днищем і окремою еліптичної кришкою з 2-ма сорочками: теплообмінною (з вбудованим ТЕН) і теплоізолюючою.
Підтримується функція дезінфекції для оперативної стерилізації.
Ємність обладнана мішалкою на магнітному приводі, щоб підтримувати постійну концентрацію рідини і необхідний ступінь гомогенізації.
Слайд 25Фільтри для рідин
Матриця градуйованою щільності картріджних фільтрів дозволяє обернути в один картридж
Фільтри для рідин
Матриця градуйованою щільності картріджних фільтрів дозволяє обернути в один картридж
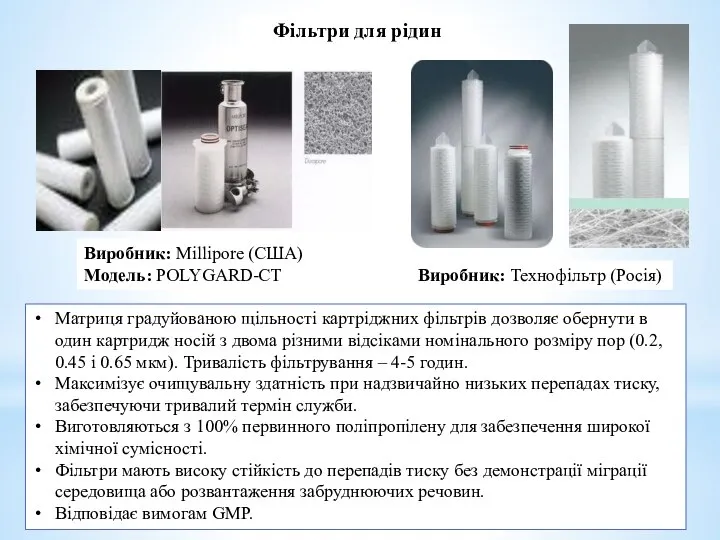
Максимізує очищувальну здатність при надзвичайно низьких перепадах тиску, забезпечуючи тривалий термін служби.
Виготовляються з 100% первинного поліпропілену для забезпечення широкої хімічної сумісності.
Фільтри мають високу стійкість до перепадів тиску без демонстрації міграції середовища або розвантаження забруднюючих речовин.
Відповідає вимогам GMP.
Виробник: Millipore (США)
Модель: POLYGARD-CT
Виробник: Технофільтр (Росія)
Слайд 26Машина для наповнення і закупорювання флаконів
Виробник: ROTA (Німеччина)
Продуктивність – 2-5 тис. фл
Машина для наповнення і закупорювання флаконів
Виробник: ROTA (Німеччина)
Продуктивність – 2-5 тис. фл
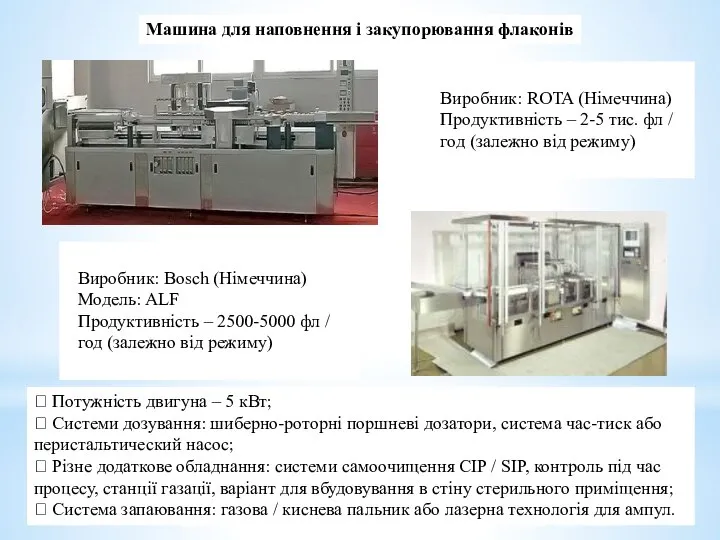
Потужність двигуна – 5 кВт;
Системи дозування: шиберно-роторні поршневі дозатори, система час-тиск або перистальтический насос;
Різне додаткове обладнання: системи самоочищення CIP / SIP, контроль під час процесу, станції газації, варіант для вбудовування в стіну стерильного приміщення;
Система запаювання: газова / киснева пальник або лазерна технологія для ампул.
Виробник: Bosch (Німеччина)
Модель: ALF
Продуктивність – 2500-5000 фл / год (залежно від режиму)
Слайд 27Автоклави
Виробник: FEDEGARI (Італія)
Модель: 1495 ЛТР FOF 3/4 з полірованої нержавіючої сталі
Продуктивність –
Автоклави
Виробник: FEDEGARI (Італія)
Модель: 1495 ЛТР FOF 3/4 з полірованої нержавіючої сталі
Продуктивність –
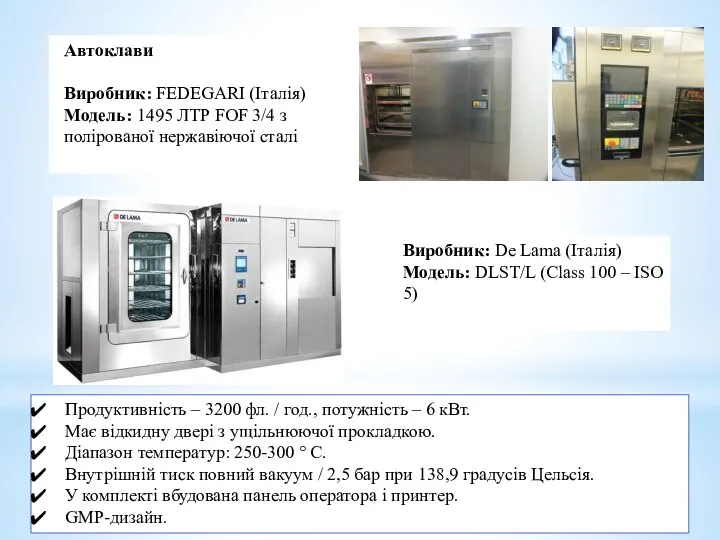
Має відкидну двері з ущільнюючої прокладкою.
Діапазон температур: 250-300 ° C.
Внутрішній тиск повний вакуум / 2,5 бар при 138,9 градусів Цельсія.
У комплекті вбудована панель оператора і принтер.
GMP-дизайн.
Виробник: De Lama (Італія)
Модель: DLST/L (Class 100 – ISO 5)
Слайд 28Машина для етикетування
Виробник: Marchesini (Італія)
Модель: Neri RL 500
Продуктивність – 2500-6000 фл./год. (залежно
Машина для етикетування
Виробник: Marchesini (Італія)
Модель: Neri RL 500
Продуктивність – 2500-6000 фл./год. (залежно
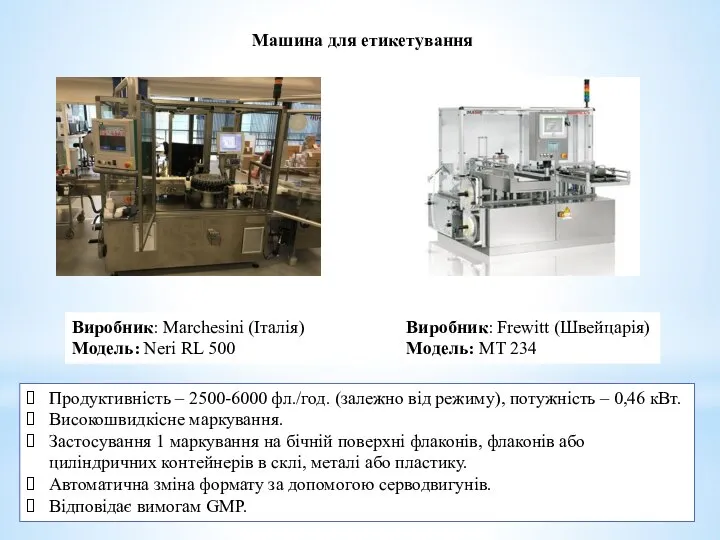
Високошвидкісне маркування.
Застосування 1 маркування на бічній поверхні флаконів, флаконів або циліндричних контейнерів в склі, металі або пластику.
Автоматична зміна формату за допомогою серводвигунів.
Відповідає вимогам GMP.
Виробник: Frewitt (Швейцарія)
Модель: МТ 234