Содержание
- 2. 1. Introduction to standard costs Standard costs are carefully predetermined costs that are used as performance
- 3. 2. Benefits of standard costs The most important benefits of standard costs are: 1. Planning in
- 4. 2. Performance evaluation. Standard costs serve as targets in the application of management by exception to
- 5. 3. Recordkeeping cost savings. Standard costs can be used for inventory valuation with cost savings in
- 6. 4. Managerial decision making. Standard cost information is available on a timely basis for managerial decision
- 7. 5. Cost awareness. Standard costs make employees more aware of costs and their impact on the
- 8. 3. Limitations of standard costs The limitations of standard costs should be understood so they can
- 9. 4. Use of direct costing Direct costing (also called variable costing) is an alternative inventory valuation
- 10. Three major steps are involved in the application of variable costing: 1. All costs - manufacturing,
- 11. 5. Benefits of direct costing The major benefits of variable costing are: 1. Direct costing forces
- 12. 6. Limitations of direct costing The main limitations are: 1. The separation of many cost behavior
- 13. 7. Process costing method Process costing method are used by firms with repetitive production. A process
- 14. When multiple processing centers are used, the relationships between the centers must be clearly defined to
- 15. The control document used in a process costing system is called a cost of production report.
- 16. 8. Job order costing method Managers need reliable product cost information for such actions as setting
- 17. A job order cost sheet is the control document in a job order costing system and
- 19. Скачать презентацию
Слайд 2 1. Introduction to standard costs
Standard costs are carefully predetermined costs
1. Introduction to standard costs
Standard costs are carefully predetermined costs
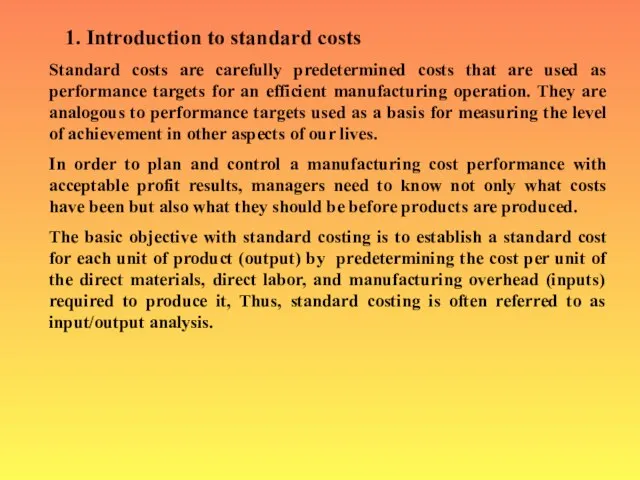
In order to plan and control a manufacturing cost performance with acceptable profit results, managers need to know not only what costs have been but also what they should be before products are produced.
The basic objective with standard costing is to establish a standard cost for each unit of product (output) by predetermining the cost per unit of the direct materials, direct labor, and manufacturing overhead (inputs) required to produce it, Thus, standard costing is often referred to as input/output analysis.
Слайд 32. Benefits of standard costs
The most important benefits of standard costs
2. Benefits of standard costs
The most important benefits of standard costs
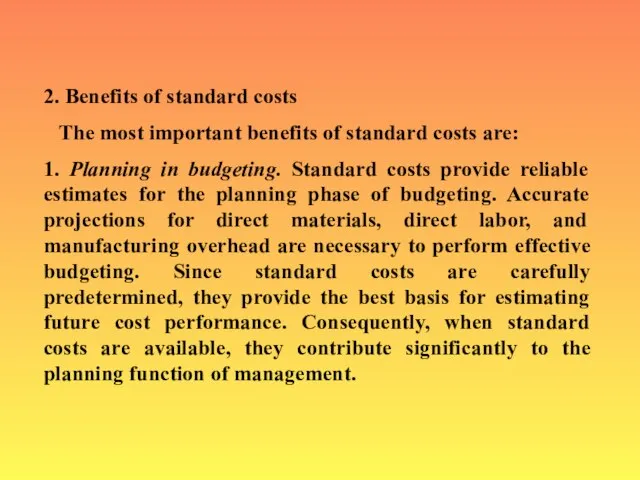
1. Planning in budgeting. Standard costs provide reliable estimates for the planning phase of budgeting. Accurate projections for direct materials, direct labor, and manufacturing overhead are necessary to perform effective budgeting. Since standard costs are carefully predetermined, they provide the best basis for estimating future cost performance. Consequently, when standard costs are available, they contribute significantly to the planning function of management.
Слайд 42. Performance evaluation. Standard costs serve as targets in the application of
2. Performance evaluation. Standard costs serve as targets in the application of
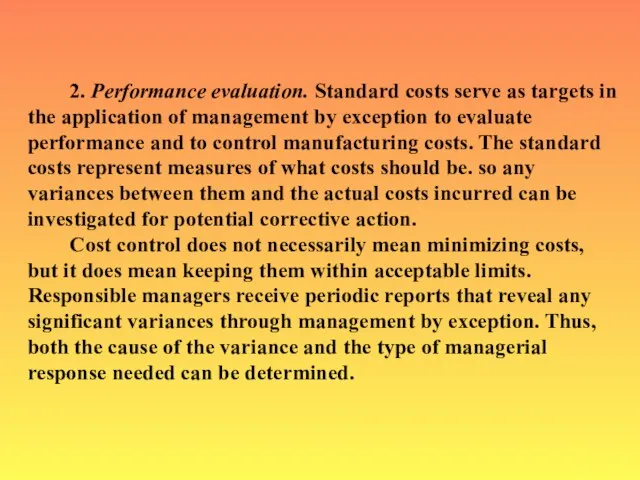
Cost control does not necessarily mean minimizing costs, but it does mean keeping them within acceptable limits. Responsible managers receive periodic reports that reveal any significant variances through management by exception. Thus, both the cause of the variance and the type of managerial response needed can be determined.
Слайд 53. Recordkeeping cost savings. Standard costs can be used for inventory valuation
3. Recordkeeping cost savings. Standard costs can be used for inventory valuation

Слайд 64. Managerial decision making. Standard cost information is available on a timely
4. Managerial decision making. Standard cost information is available on a timely
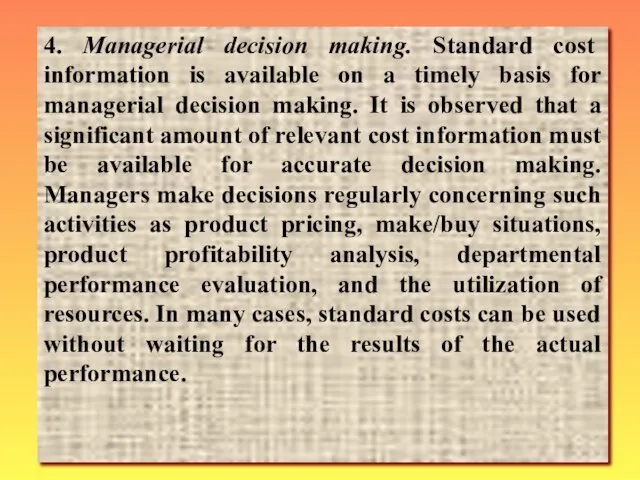
Слайд 75. Cost awareness. Standard costs make employees more aware of costs and
5. Cost awareness. Standard costs make employees more aware of costs and
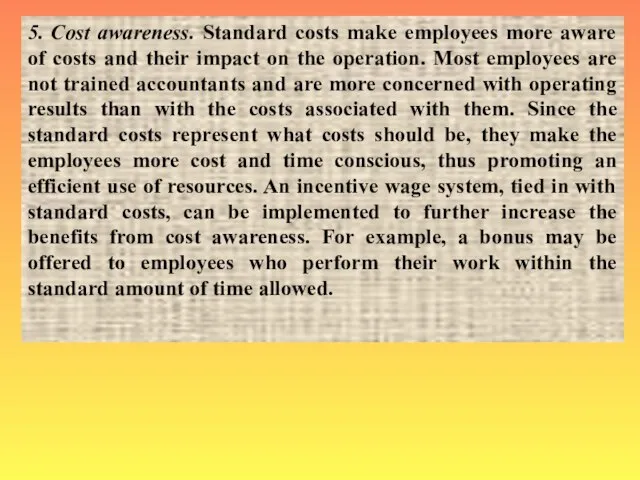
Слайд 83. Limitations of standard costs
The limitations of standard costs should be
3. Limitations of standard costs
The limitations of standard costs should be
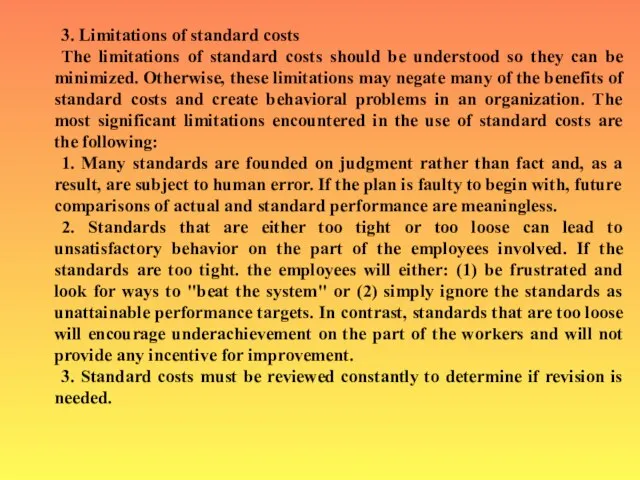
1. Many standards are founded on judgment rather than fact and, as a result, are subject to human error. If the plan is faulty to begin with, future comparisons of actual and standard performance are meaningless.
2. Standards that are either too tight or too loose can lead to unsatisfactory behavior on the part of the employees involved. If the standards are too tight. the employees will either: (1) be frustrated and look for ways to "beat the system" or (2) simply ignore the standards as unattainable performance targets. In contrast, standards that are too loose will encourage underachievement on the part of the workers and will not provide any incentive for improvement.
3. Standard costs must be reviewed constantly to determine if revision is needed.
Слайд 94. Use of direct costing
Direct costing (also called variable costing) is
4. Use of direct costing
Direct costing (also called variable costing) is
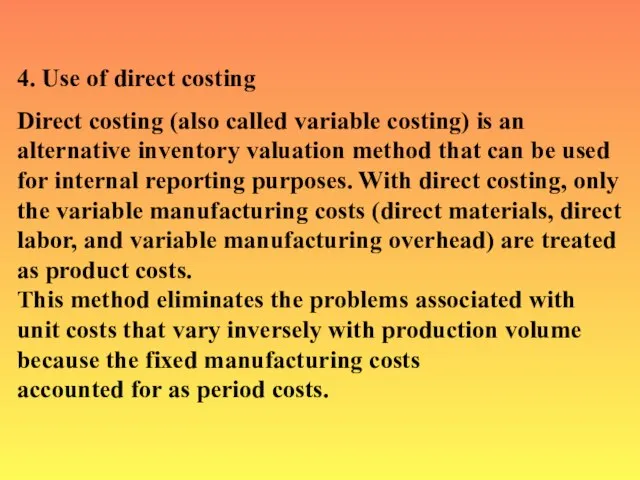
Слайд 10Three major steps are involved in the application of variable costing:
1. All
Three major steps are involved in the application of variable costing:
1. All
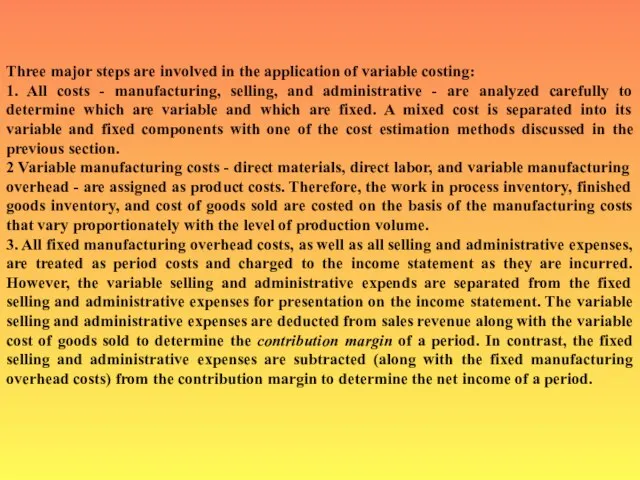
2 Variable manufacturing costs - direct materials, direct labor, and variable manufacturing overhead - are assigned as product costs. Therefore, the work in process inventory, finished goods inventory, and cost of goods sold are costed on the basis of the manufacturing costs that vary proportionately with the level of production volume.
3. All fixed manufacturing overhead costs, as well as all selling and administrative expenses, are treated as period costs and charged to the income statement as they are incurred. However, the variable selling and administrative expends are separated from the fixed selling and administrative expenses for presentation on the income statement. The variable selling and administrative expenses are deducted from sales revenue along with the variable cost of goods sold to determine the contribution margin of a period. In contrast, the fixed selling and administrative expenses are subtracted (along with the fixed manufacturing overhead costs) from the contribution margin to determine the net income of a period.
Слайд 115. Benefits of direct costing
The major benefits of variable costing are:
5. Benefits of direct costing
The major benefits of variable costing are:
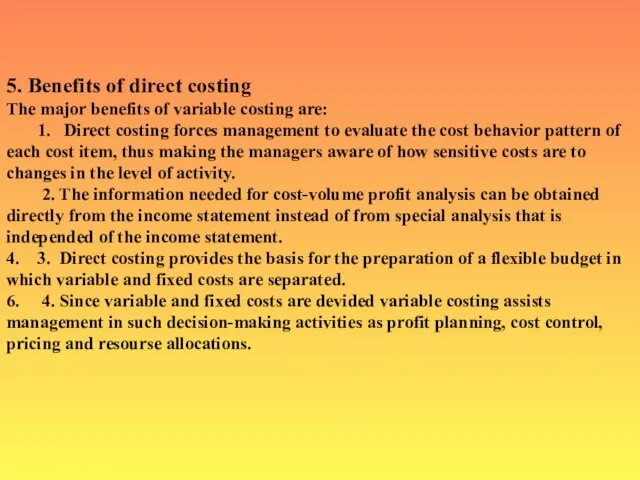
2. The information needed for cost-volume profit analysis can be obtained directly from the income statement instead of from special analysis that is independed of the income statement.
4. 3. Direct costing provides the basis for the preparation of a flexible budget in which variable and fixed costs are separated.
6. 4. Since variable and fixed costs are devided variable costing assists management in such decision-making activities as profit planning, cost control, pricing and resourse allocations.
Слайд 126. Limitations of direct costing
The main limitations are:
1. The separation of
6. Limitations of direct costing
The main limitations are:
1. The separation of
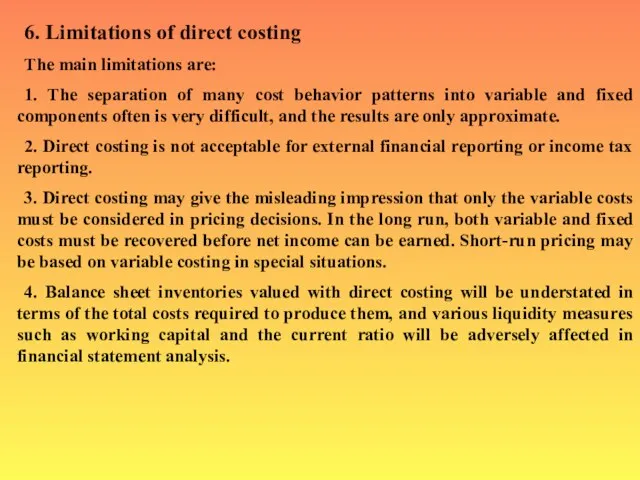
2. Direct costing is not acceptable for external financial reporting or income tax reporting.
3. Direct costing may give the misleading impression that only the variable costs must be considered in pricing decisions. In the long run, both variable and fixed costs must be recovered before net income can be earned. Short-run pricing may be based on variable costing in special situations.
4. Balance sheet inventories valued with direct costing will be understated in terms of the total costs required to produce them, and various liquidity measures such as working capital and the current ratio will be adversely affected in financial statement analysis.
Слайд 13 7. Process costing method
Process costing method are used by firms
7. Process costing method
Process costing method are used by firms
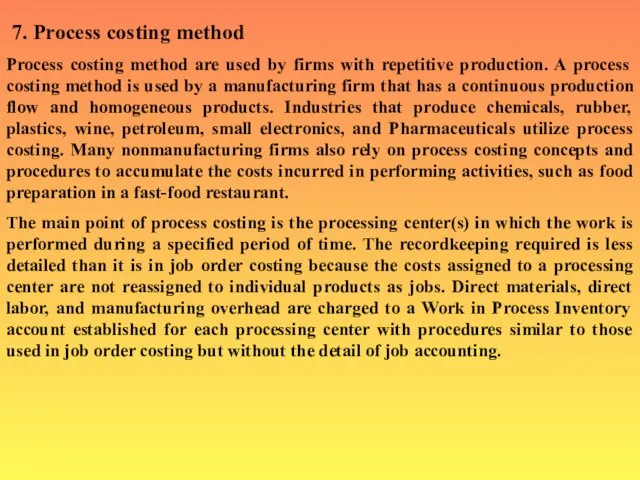
The main point of process costing is the processing center(s) in which the work is performed during a specified period of time. The recordkeeping required is less detailed than it is in job order costing because the costs assigned to a processing center are not reassigned to individual products as jobs. Direct materials, direct labor, and manufacturing overhead are charged to a Work in Process Inventory account established for each processing center with procedures similar to those used in job order costing but without the detail of job accounting.
Слайд 14When multiple processing centers are used, the relationships between the centers must
When multiple processing centers are used, the relationships between the centers must
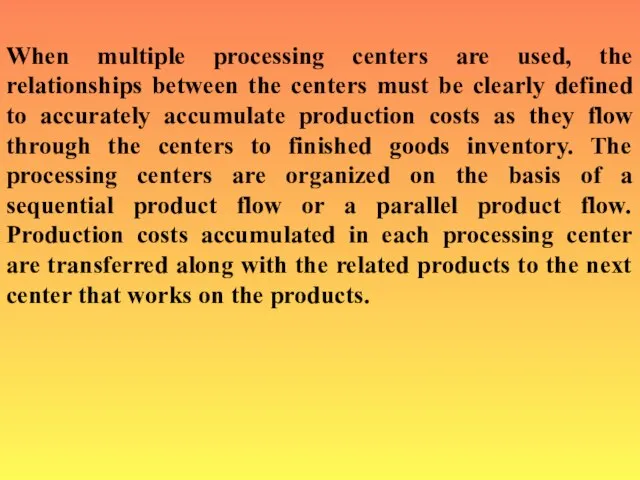
Слайд 15The control document used in a process costing system is called a
The control document used in a process costing system is called a
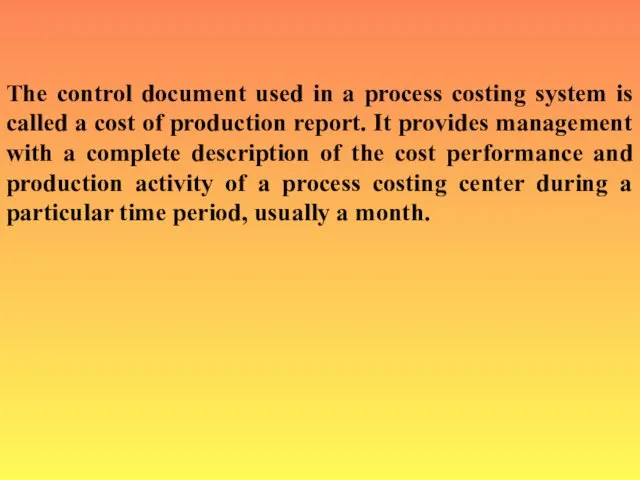
Слайд 168. Job order costing method
Managers need reliable product cost information for
8. Job order costing method
Managers need reliable product cost information for
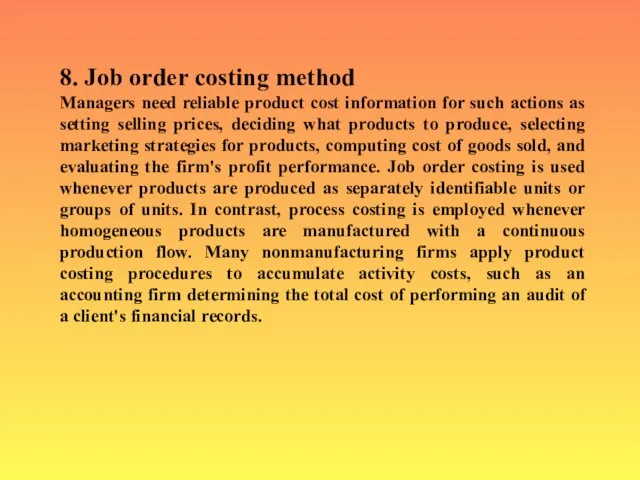
Слайд 17A job order cost sheet is the control document in a job
A job order cost sheet is the control document in a job
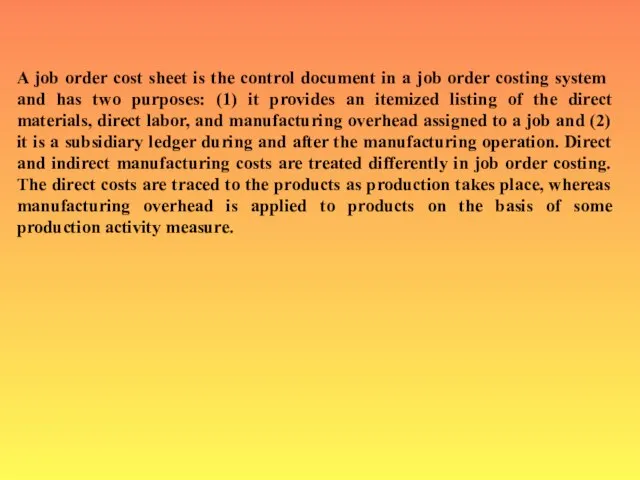