Слайд 2Припуск на обработку -
Это слой металла, подлежащий удалению с поверхности заготовки
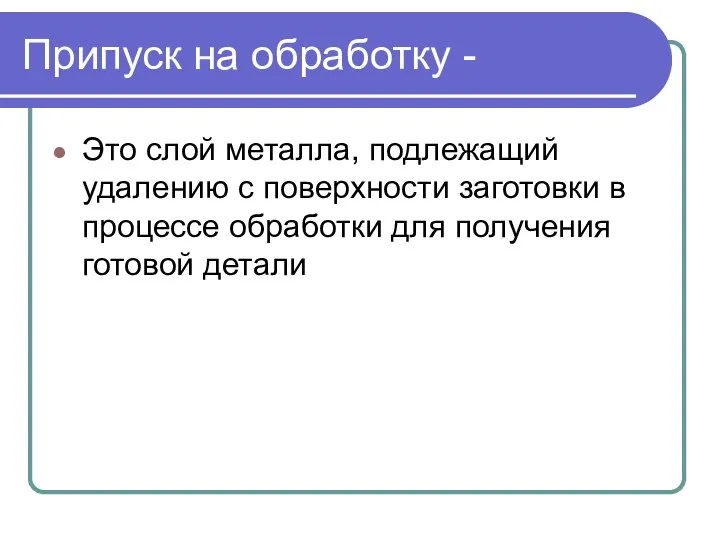
в процессе обработки для получения готовой детали
Слайд 3Размер припуска
Определяют разностью между размером заготовки и размером детали по рабочему чертежу;
Припуск
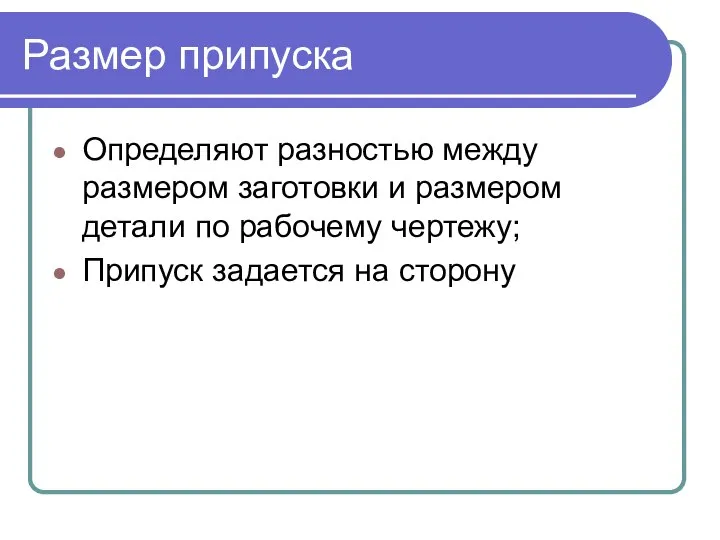
задается на сторону
Слайд 4Припуски подразделяют на
ОБЩИЕ, т.е. удаляемые в течение всего процесса обработки данной поверхности
МЕЖОПЕРАЦИОННЫЕ,
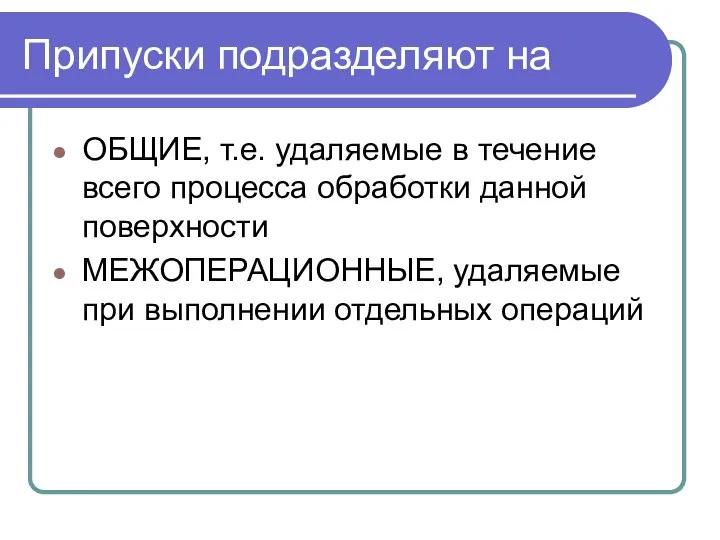
удаляемые при выполнении отдельных операций
Слайд 5Общий припуск на обработку
Равен сумме межоперационных припусков по всем техгологическим операциям –
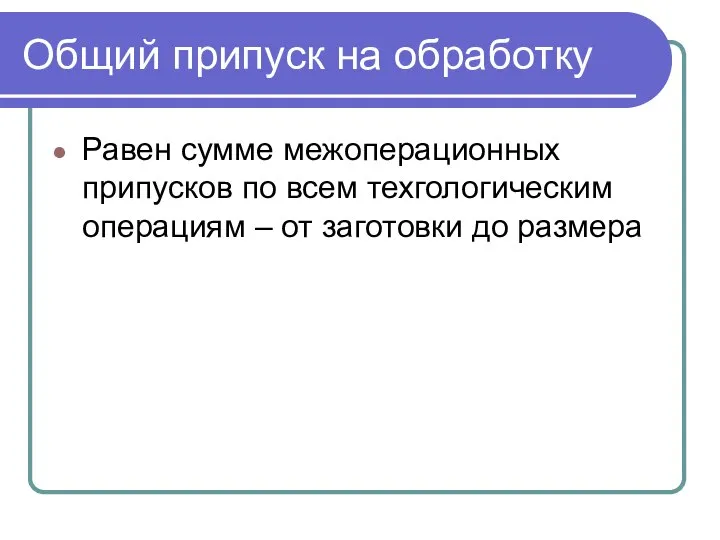
от заготовки до размера
Слайд 7Межоперационный припуск:
Равен сумме припусков, отведенных на черновой, получистовой и чистовой проходы на
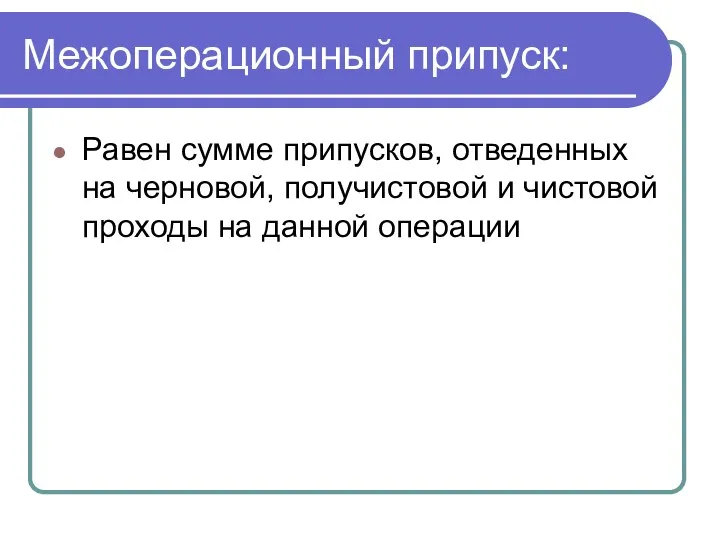
данной операции
Слайд 9При обработке поверхности вращения (внешних и внутренних) операционный припуск определяется:
2Z=δ+2(R+T)+2(ε+ρ)
При обработке плоских
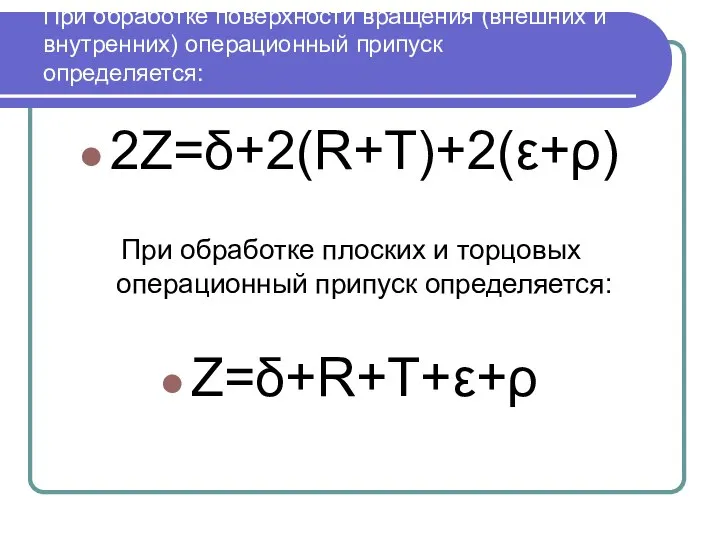
и торцовых операционный припуск определяется:
Z=δ+R+T+ε+ρ
Слайд 10
Где:
δ - допуск на размер;
R – высота микронеровностей;
T – глубина дефектного слоя;
ε
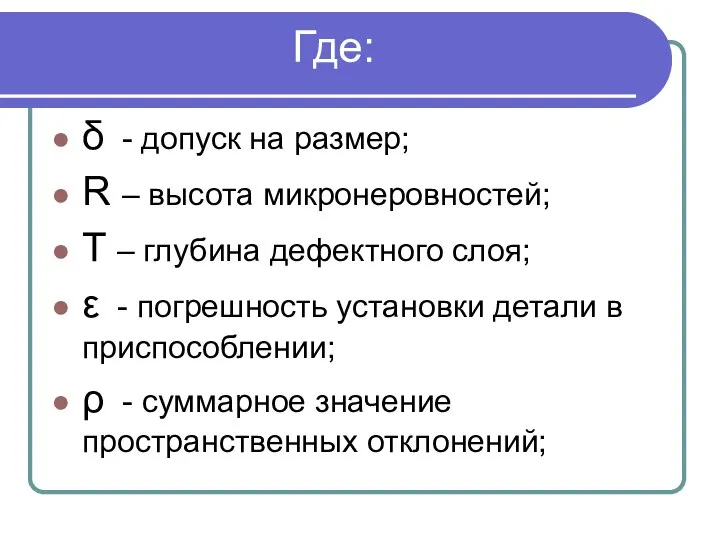
- погрешность установки детали в приспособлении;
ρ - суммарное значение пространственных отклонений;
Слайд 11δ, R, T, ρ - это дефекты, оставшиеся на поверхности детали от
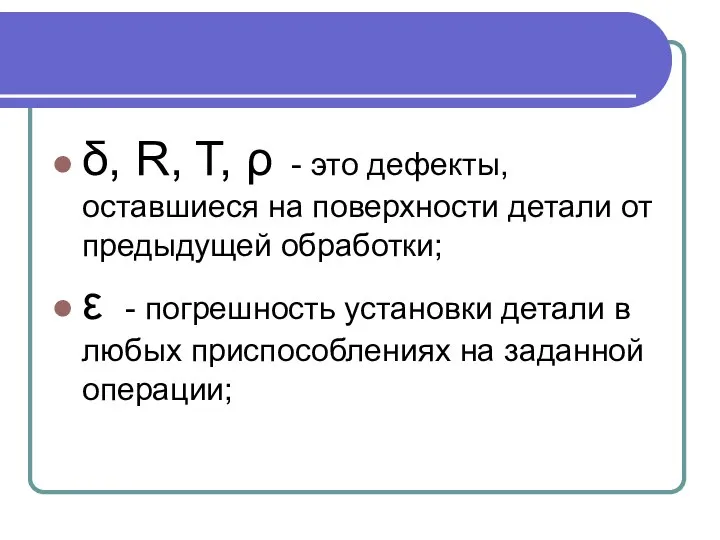
предыдущей обработки;
ε - погрешность установки детали в любых приспособлениях на заданной операции;
Слайд 12Два метода определения припусков:
Аналитический (расчетный);
Статистический (табличный);
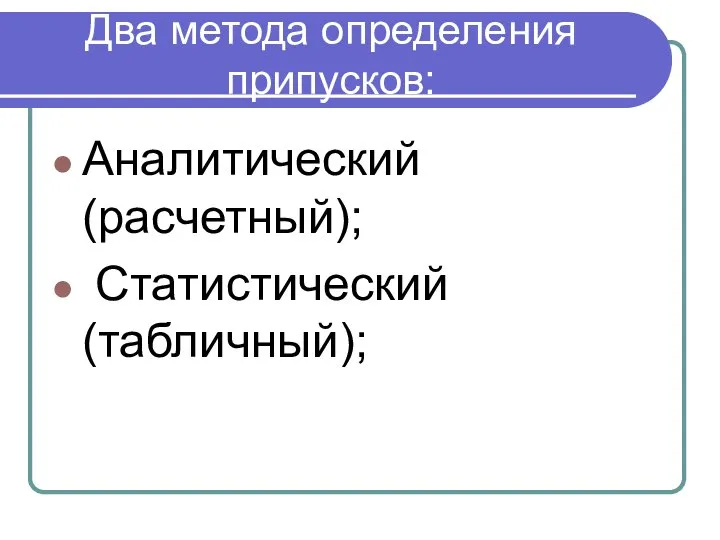
Слайд 15Определение технологичности:
1.Определение коэффициента точности:
Кт = 1- 1/ Аср;
Аср.= ΣAn/n = 7+8+9+10+3х12/7=10
Кт =
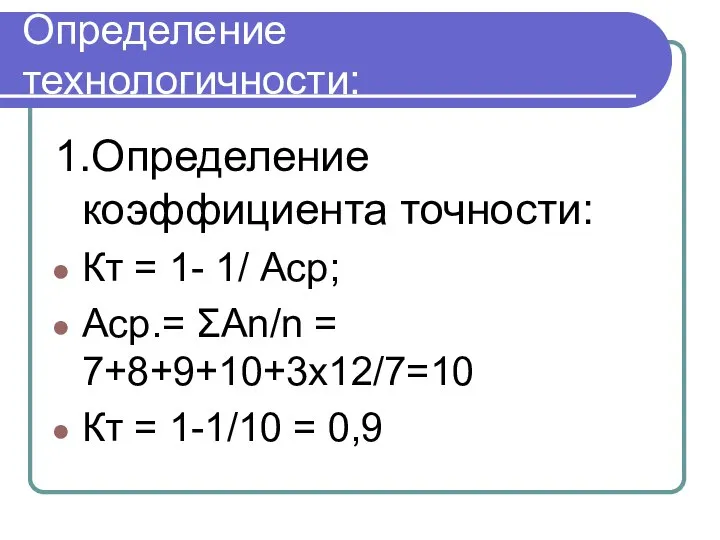
1-1/10 = 0,9
Слайд 162. Определение коэффициента шероховатости:
Кш = 1- 1/ Бср;
Бср.= ΣБn / n =
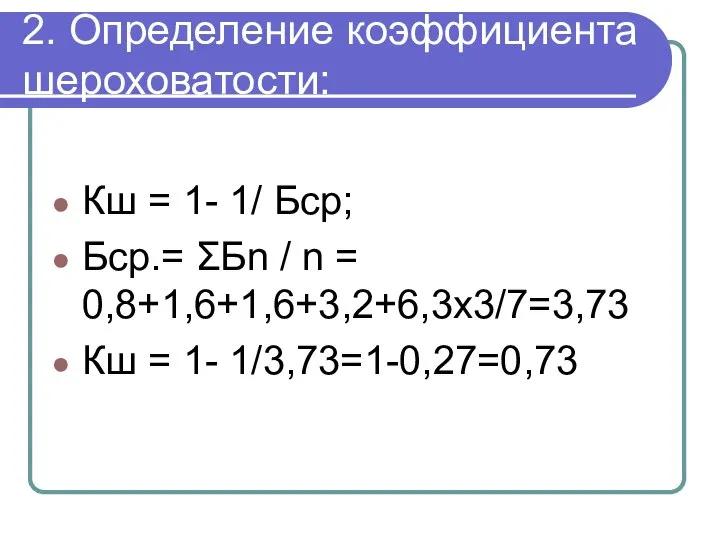
0,8+1,6+1,6+3,2+6,3х3/7=3,73
Кш = 1- 1/3,73=1-0,27=0,73
Слайд 17Т.к. Кт= 0,9 > 0,8;
а Кш=0,73 > 0,16
- деталь технологична и
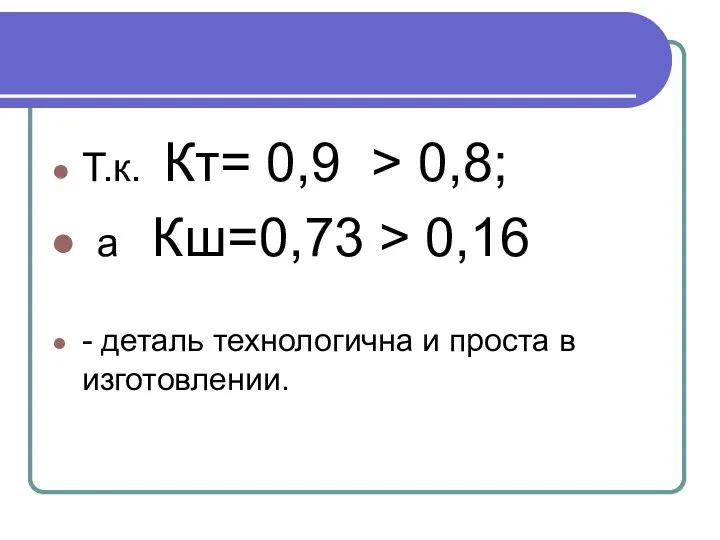
проста в изготовлении.
Слайд 18
Статистический метод определения припусков:
Пример:
Необходимо назначить припуски на обработку Ø35 h8 (-0,039),
Шероховатость
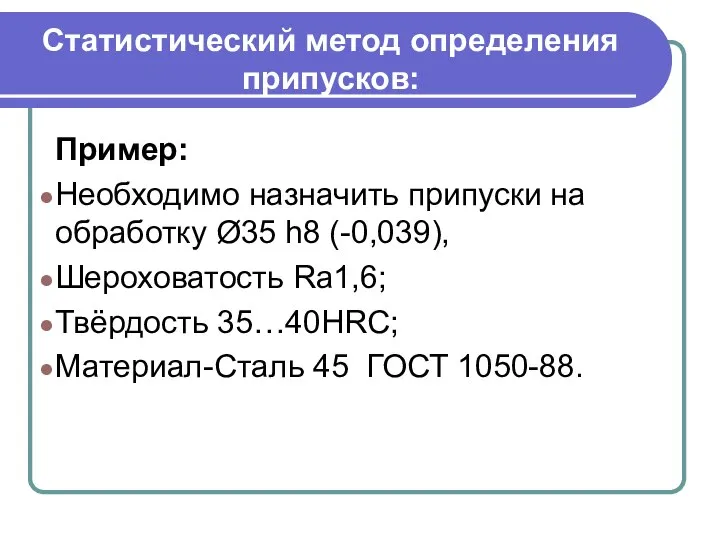
Ra1,6;
Твёрдость 35…40HRC;
Материал-Сталь 45 ГОСТ 1050-88.
Слайд 19Составляем План обработки поверхностиØ35 h8 (-0,039),
1. Заготовительная
2. Токарная(черновая)
3. Токарная (чистовая)
4. Термическая
5.
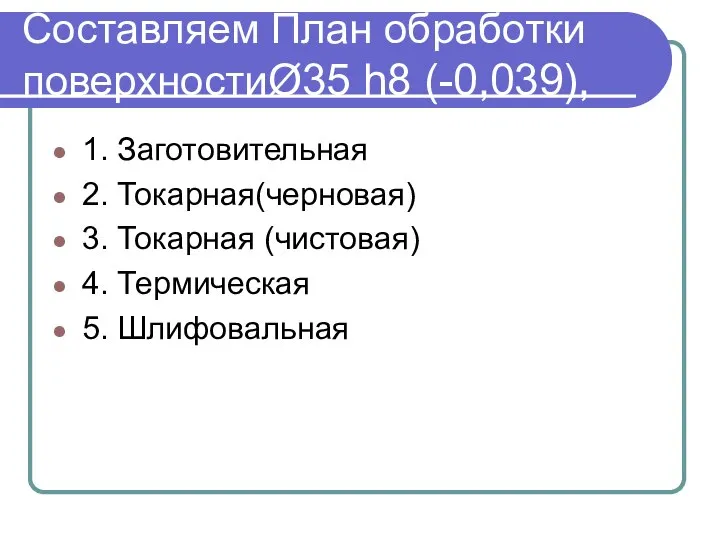
Шлифовальная